Cement laboratory automation has been a theme within the industry since the first blend control systems were commissioned back in the 1970s. The first automated laboratory followed some years later as cement plants sought to improve the consistency and quality of their analysis and thus their finished product. FLSmidth Cement has been a key player in these developments from the start, thanks to our QCX suite of solutions, which includes systems for automated sampling and transportation (QCX/AutoSampling™), automated sample preparation and analysis (QCX/RoboLab®), and chemical quality control (QCX/BlendExpert™).
A new trend is now emerging, however, that moves beyond automation. Cement plants increasingly want to know how their cement laboratory fits within their Industry 4.0 ambitions, with its embrace of machine learning and other AI-based technologies.
Perhaps counterintuitively, this requires us to go back to basics and look at the systems that underpin the automation solutions mentioned above. The reason for this is simple: data. Industry 4.0 solutions all need data. They are the base ingredient that allow AI systems to do what they do. And as a chef may only cook up the finest cuisine from the finest ingredients, the better the data, the better the AI outcomes will be.
Cement laboratories are, if nothing else, sources of data. The question then becomes: how do we best acquire the best-quality sample data from all analysers to ensure the availability of that data for the technologies of today and tomorrow? To answer this, we must look at the system responsible for collecting, organising, and tracking sample data. We call this the Production Laboratory Information Management System (Production LIMS) with QCX/Manager – the basis of our QCX suite – a leading example here.
We will dive into some of the key considerations for selecting a Production LIMS in the second part of this article. However, first we will look at the complexities of sample data.
WANT TO LEARN MORE?
Register to get full access to the whitepaper.
Sample data is not process data
There are two main points to be aware of when thinking about sample data. The first is how sample data are collected. The second deals with the nature of sample data itself.
Unlike process data – which are automatically collected by the vast number of sensors located throughout the cement-making process and sent to the control system – sample data can be collected in manyways (with varying risk of error), depending on the specific procedures in place at the cement plant in question.
At the top level, sample collection, transportation, preparation, and analysis are fully automated, e.g., via QCX/AutoSampling™ and QCX/RoboLab® systems. These deliver dependable, well-structured, and accurate data, but require higher initial investment. But even with a very high degree of laboratory automation, there will normally be laboratory procedures outside the automated lab, which involve a degree of manual intervention. An example here would be when the physical testing of cement involves a high degree of manual sample handling, as well as sample storage up to 28 days before testing, but equipment control and transfer of results remains automated.
At the lowest degree of automation, the entire process is manually operated, from sample handling and control of the equipment to manual entry of analysis data. This is labour intensive and there is a substantial risk of human error creeping into the system.
In an ideal world, all cement laboratories would be on the path to full automation, but we recognise this may not be practical in many instances. Cement plants will weigh up the benefits of fully automated laboratories against cost, and balance where it is acceptable to have a degree of manual operation. However – and this is key – whatever the level of automation, all data must be fed into a common LIMS if the effective use of AI technologies is to be supported.
The second point here concerns the nature of sample data compared to process data. The latter present a regular time series, with measurements typically taken at equal time intervals. In contrast, cement samples may not be sampled at equal time intervals, and there may be lengthy delays between sampling and analysis. Samples are divided into multiple preparations and provide complex analysis results. Sample data also typically cover a production timespan and an underlying tonnage. All this means it is far more important to record metadata for samples than for the process equivalent (more on which later).
Production LIMS and laboratory automation hosted in common software environment
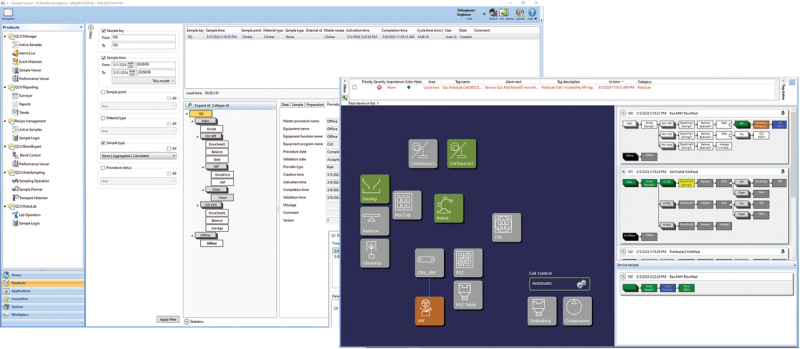
Production LIMS vs Overall LIMS
It is worth also taking a moment to consider types of LIMS. Within the wider context, different varieties of LIMS exist for different specialist applications, e.g., pharmaceutical laboratories, scientific laboratories, and commercial laboratories. But when it comes to cement plants specifically, there are two LIMS to be aware of.
1. The first is what we refer to as a Production LIMS, e.g., QCX/Manager: this is the basic laboratory management system on which laboratory automation systems are based and that receives data therefrom. Production LIMS specifically target the production laboratory environment, offering a set of LIMS features that are relevant to running a high number of standardised routine samples every day.
2. The second is an overall system, either in the form of an Overall LIMS (if managing laboratory data only) or a plant data management system (if combining process data and laboratory data). An example of the latter is FLSmidth Cement’s ECS/PlantDataManagement.
Typical cement plant software layout with process control system, Production LIMS, expert systems, and an overall plant data management system
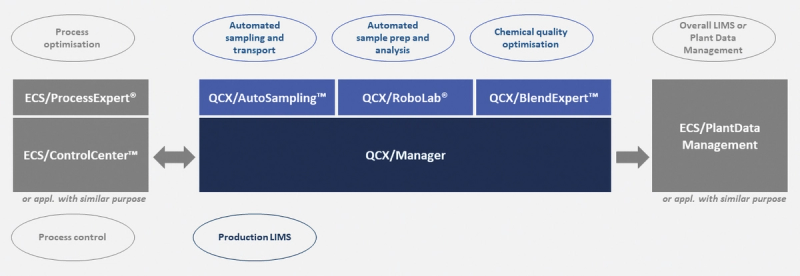
Cement plants often separate LIMS functionality between the Production LIMS and the Overall LIMS / plant data management system. This raises questions when it comes to system architecture. And that brings us to the second part of this article: what should a cement plant consider when selecting a Production LIMS?
Production LIMS selection checklist
Based on our discussions with clients, we have put together the following checklist of things to consider when planning and selecting a Production LIMS. The checklist focuses on supporting both automatic and manual sampling and analysis, as well as taking expected Industry 4.0 requirements into account.
- System architecture
- Metadata
- Sample data
- Sample data integrity
- User interfaces
- Export features
- Online analysers
- Equipment performance tracking
- Initial and maintenance costs
For brevity, we include a discussion of just three of these points (system architecture, metadata, and initial and maintenance costs) here.
System architecture
Cement plants that have invested in an automated laboratory will typically have a Production LIMS, which is responsible for recipe execution, equipment control, and the acquisition of analysis results. For smaller plants, this Production LIMS may be sufficient to cover all LIMS requirements, having all the features needed for day-to-day operations, such as a sample data viewer, as well as features for reporting and trending. However, larger plants typically only use the Production LIMS at the frontend, exporting sample data to an overall LIMS or a plant data management system. Such an overall system may be limited to a single plant or span several plants.
When there is a desire to acquire sample data from manually operated equipment, this triggers the question: should such equipment be connected to the Production LIMS or feed directly to the plant data management system? For routine samples, we suggest connecting to the Production LIMS, as the Production LIMS will likely already know about and have fully defined the sample in the sample database (as it is probably a subsample of a sample that was scheduled automatically). But whatever the decision, it is important to ensure every sample is unambiguously identified across both the Production LIMS and the plant data management system via a unique sample key.
Manually operated laboratory equipment connected to the Production LIMS
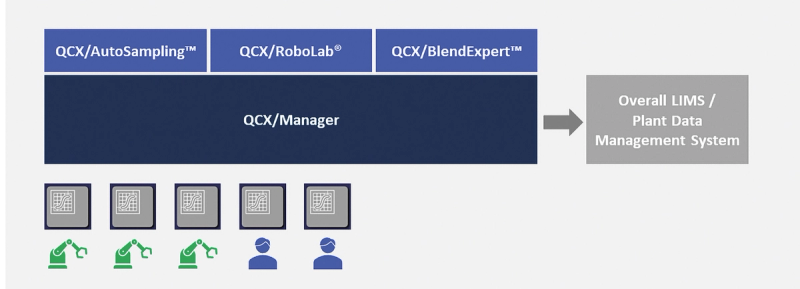
Manually operated laboratory equipment connected to the Overall LIMS or plant data management system
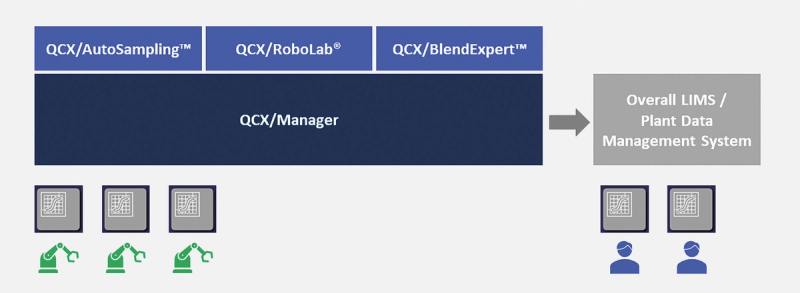
Finally, but crucially, sample data – together with their process data counterparts – must be a made available to optimisation software solutions via powerful export functionality and a well-considered data infrastructure. This is true regardless of whether the optimisation solutions are based on AI or other technologies, or whether they are well-established standard products or more experimental and site-specific trial systems.
Metadata
Metadata are basically data about data. When it comes to samples, important metadata will include when the sample was taken, the sample point, and the material type. But this is far from all. There are a vast amount of possible additional metadata that may be collected. For example: every analyser may provide valuable metadata, especially for systems the span several sites, including the instrument make, model, serial number, calibration date, and calibration text.
Such metadata are hugely valuable when it comes to managing sample data and are expected to gain even more significance with the implementation of AI solutions. Deciding how they are managed is thus a crucial factor when it comes to planning and implementing a Production LIMS. This should be able to handle metadata gracefully and make them available, alongside the sample data, through data export features.
Initial and maintenance costs
1. Initial cost: Is the system programmed-for-the-application or out-of-the-box and how does this impact the time required to get the system up and running?
2. Maintenance: Who can change configurations or add equipment: is it just the vendor or can the customer also do this? Is it possible to create communications scripts to interface to new equipment?
3. Software licenses: Many customers now prefer software subscriptions to owning the software outright (perpetual license). One reason for this is that software needs to be updated on a regular basis – partly to stay safe and secure, and partly to benefit from updates and new features. An alternative hybrid route, preferred by some, is a perpetual license backed by an ongoing software maintenance agreement.
Wrapping up
Production LIMS already play an important (if unsung) role in the frontend acquisition and storage of sample data at a cement plant. However, we expect this role to become increasingly important as the need for detailed and well-structured data grows to support AI advances. Careful planning and selection of the sample data infrastructure – considering the above considerations – is thus essential to ensuring your ability to support your Industry 4.0 goals.
Previously published in the July 2024 issue of International Cement Review