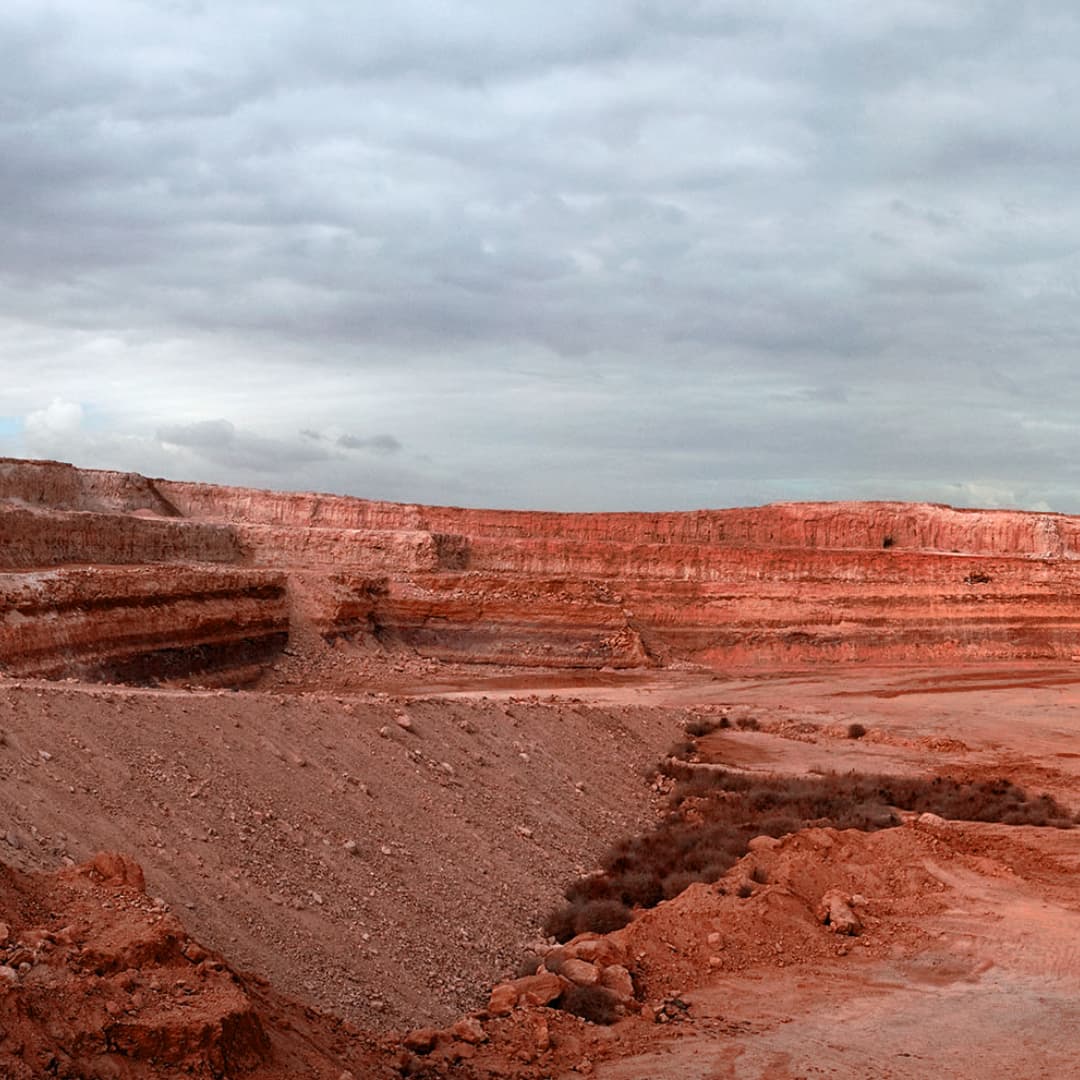
Calcined clay
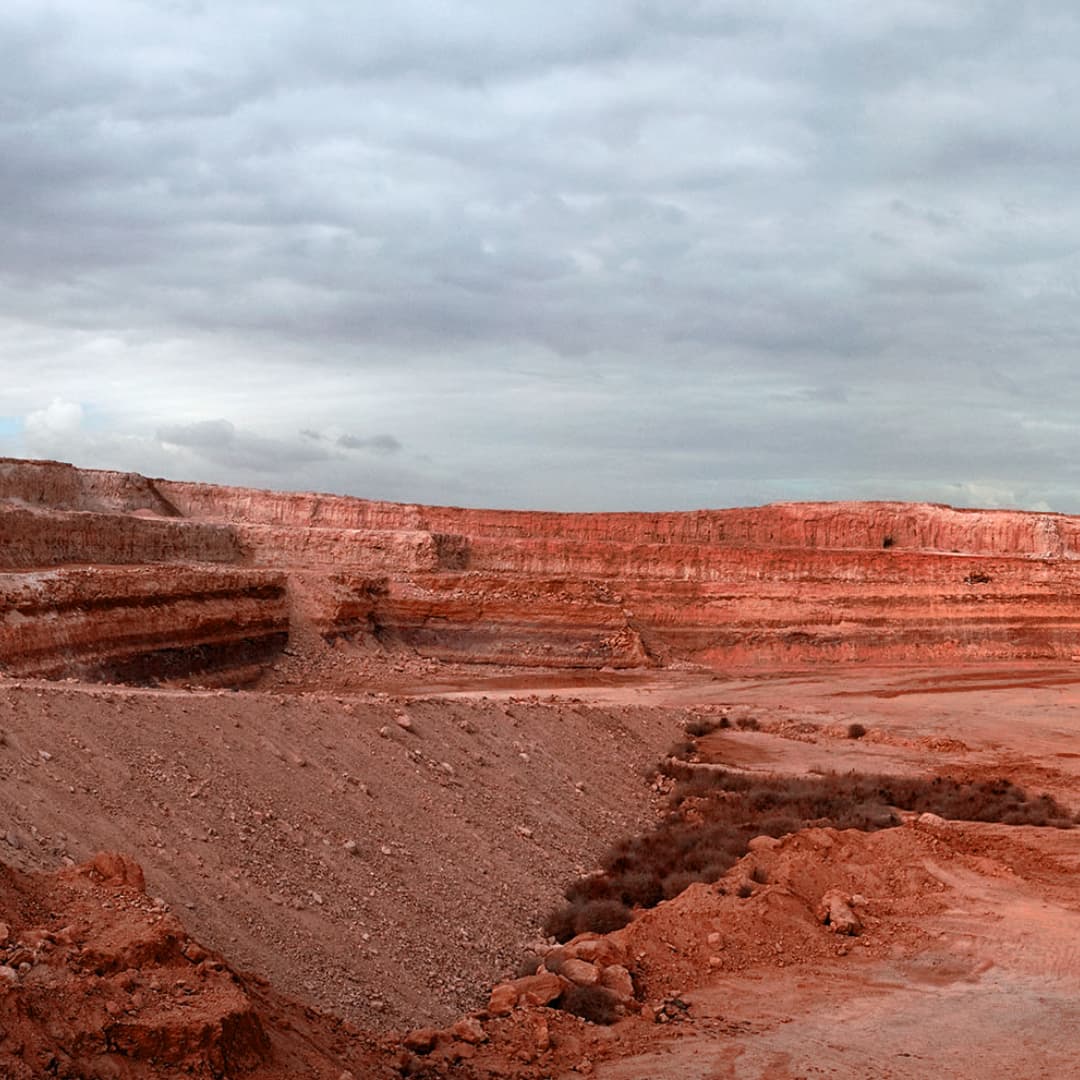
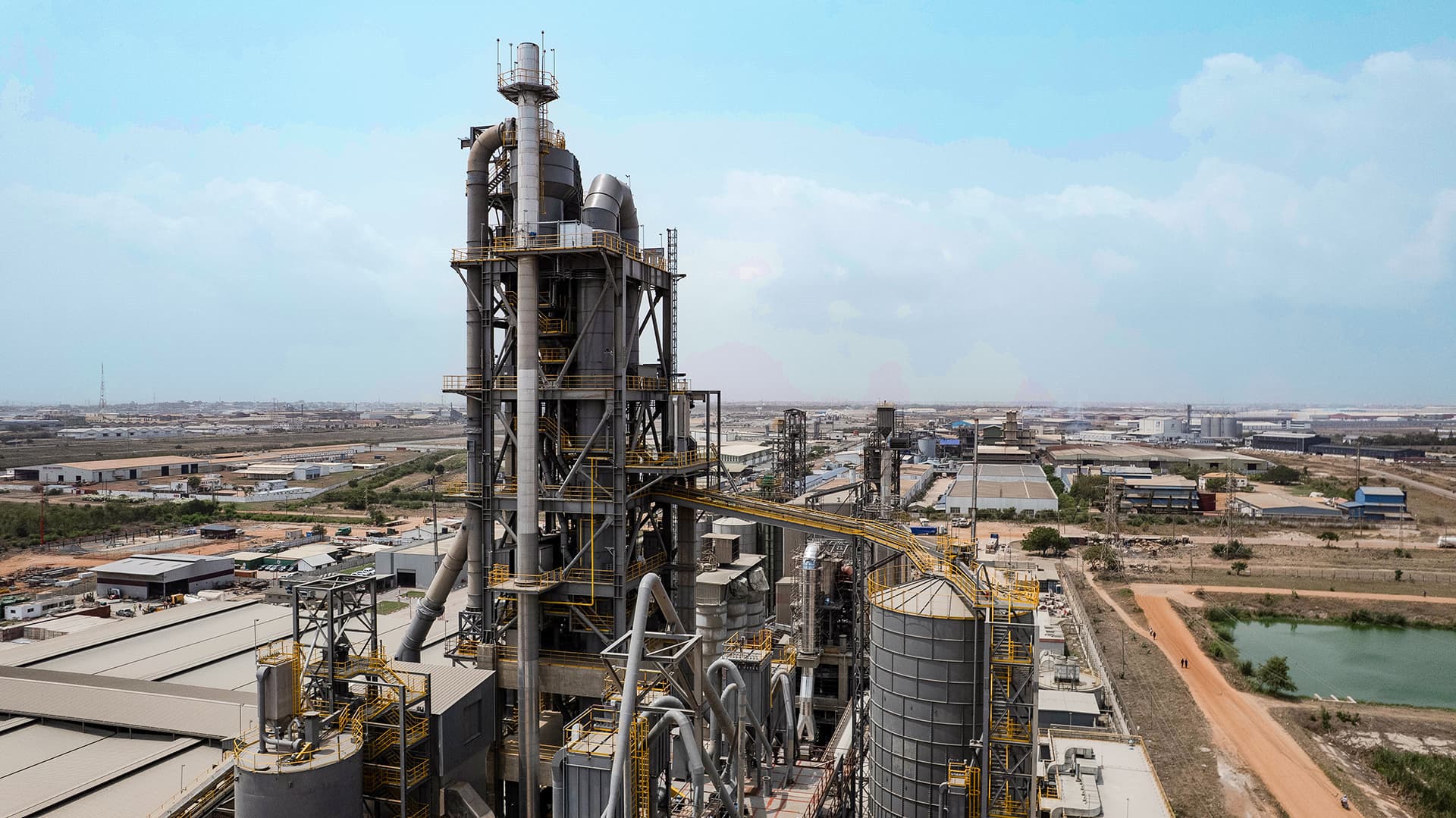
Our flash calciner system costs less to set up than a rotary kiln and is more energy efficient by approx. 20% as compared to a rotary kiln. Furthermore, it produces highly reactive clay that can be used as a clinker substitute in the range of 30 – 40%, resulting in a huge CO2 reduction for the finished cement product. In contrast, only 15 – 25% substitution can be achieved with product produced in a rotary kiln because the calcined clay is less reactive and therefore less suitable as a clinker substitute.

Colour control to obtain grey blended cement
By applying the right settings and conditions during activation and cooling, we have developed a unique, patent-pending process to achieve the standard grey cement colour in your clay. This ensures end users will be happy with the look of the product, as well as its performance.
FLEXIBLE, EFFICIENT FUEL CONSUMPTION
Our efficient calciner system minimizes fuel consumption, maximizing the recuperation of heat from the product.
ALTERNATIVE FUELS
Any fuel type typically used in a traditional clinker system - including waste fuels - can be fired in the calciner.
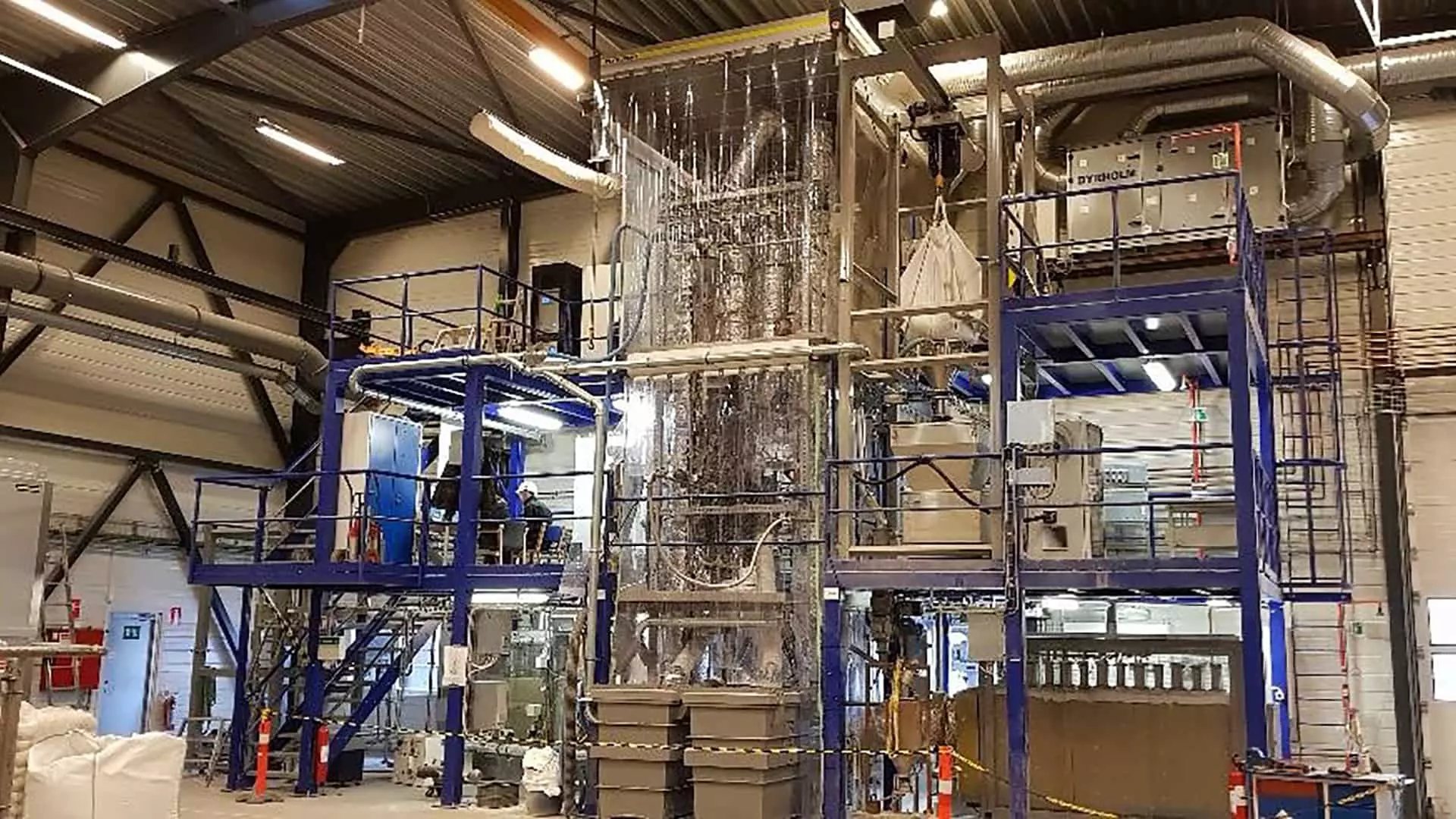
- Higher quality product due to more consistent activation •
- Higher mix percentage of calcined clay into blended cement •
- Lower fuel and maintenance costs •
- Greater fuel flexibility for burning waste fuels •
- Smaller footprint for a new system •
- Lower capital cost for a new system •
downloads
Brochures
Article reprint from ICR August 2023: Test before you invest
09.05.2024 |
3.41 MB |
English