Reduce product lost with FILLPro™ dust reduction kit
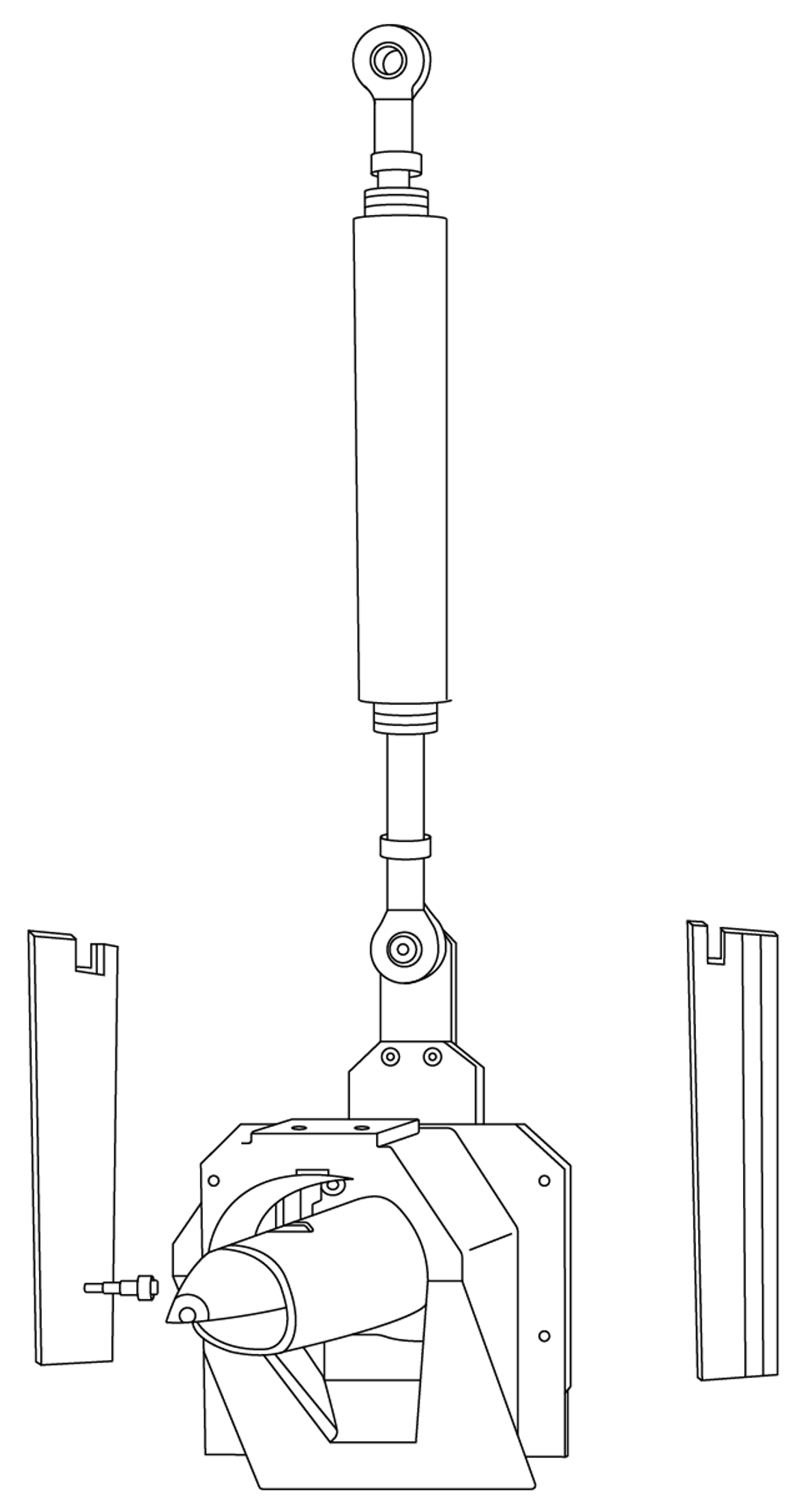
What we offer
Reduce dust in your bagging area
Dust in the bagging area is product that’s not making it out to customers. The FILLPro™ dust reduction kit for GIROMAT® EVO rotary packers enables you to capture that dust and return it to your process. Plus, additional features prevent clogging in the pipe, helping reduce wear and tear and eliminate bottlenecks. These improvements work together to enable materials to pass through the filling pipe without clogging, and to travel into the bag with significantly less dust emissions. Any product expelled during the final part of the filling process is returned to the packer body and re-utilized, dramatically reducing waste and dust generation in the packing area.
What does dust cost your business?
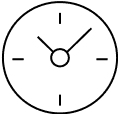
Lost Profits - Valuable product is split on the floor
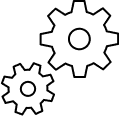
Wear and tear of machinery and components
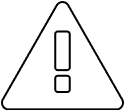
Health and safety risk for manpower
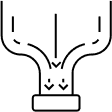
Maintenance requirements reduce productivity
Let's talk about improvements
Let's talk about real improvements that matter to your bottom line. The FILLPro™ dust reduction kit delivers measurable enhancements to your existing GIROMAT® EVO rotary packer. Each component is engineered with premium materials and designed for seamless integration, ensuring optimal performance from day one. The upgrade maintains compatibility with your current system while significantly improving operational efficiency through advanced dust control and anti-clogging features. When considering long-term value, both the initial investment and ongoing maintenance costs are optimized to provide maximum return on investment, with spare parts pricing structured to maintain consistency with your existing equipment.
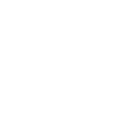
Increase of filling cycle availability
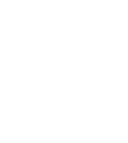
Reduction of dust loss during filling cycle
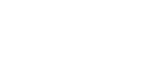
Elimination of clogging
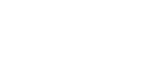
Reduction of downtime
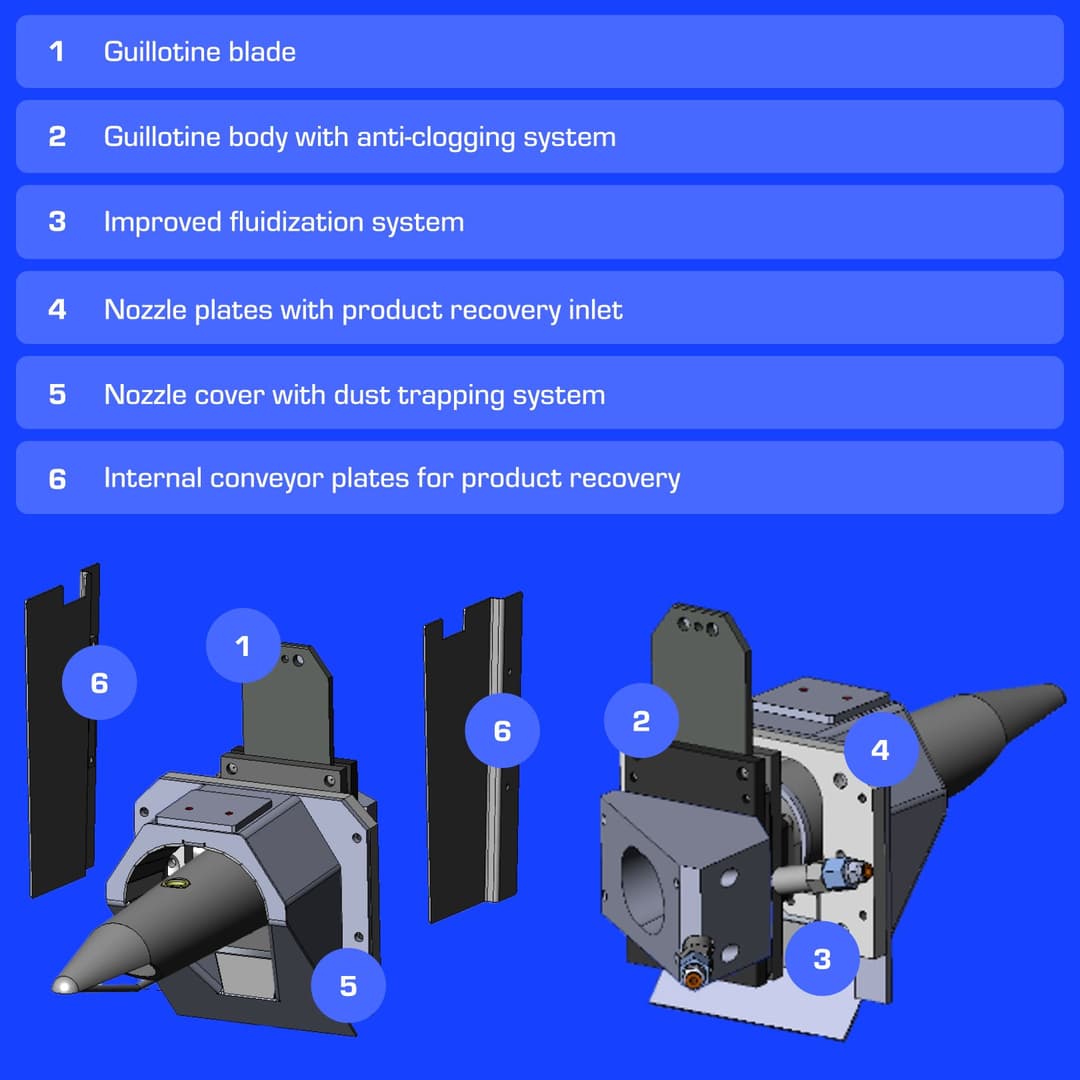

1. New guillotine shape with optimized fine-flow passage
The new guillotine shape optimizes the flow’s kinetic energy to: → Increase product flow → Reduce the need for compressed air injection, so less dust is generated → Reduce blockages

2. New Anti-Cloging System
→ Tighter surface tolerances give less space for product to infiltrate, which reduces wear and dust generation → All the holes for screws have been moved to the lateral borders, to prevent dust and particles from getting stuck and causing clogging and scratching → New material for plates: hardened full-penetration steel, the same of the guillotine blade, to improve smoothness and scratch resistance

3. Improved fluidization system
The air jet trajectory has been improved to better operate on the fine-flow passage and dramatically reduce guillotine wear. → New lateral fluidization pipe, plugged directly onto the plate and tangential to the duct, to optimize the dust flow in the partial filling process.

4. New Nozzle plates with product recovery inlet
With the new design of the nozzle plates, discharged in the central area where there is the highest concentration of dust, any product expelled during the final part of the filling process is conveyed inside the packer body to be recovered, virtually eliminating waste from this process.

5. New Nozzle cover with dust trapping system
The nebulized product is trapped inside the new nozzle cover, which prevents it from spreading into the surrounding environment and easing its recovery inside the packer bin.

6. Internal Conveyor plates for dust recovery
The new internal conveyor plates to be installed on the sides of the new kit allow the dust recovered during the bag filling process to flow in the best possible way.
Key benefits
Increase filling cycle performance
Filling runs more smoothly, so you can achieve improved performance and reduced product loss
Reduce dust
Dust is recovered back into the process, so you’re not losing valuable product
Eliminate clogging
Designed to prevent blockages and clogging, enabling material to flow freely
Reduce downtime
With clogging eliminated and flow optimised, wear and tear is reduced and downtime is reduced
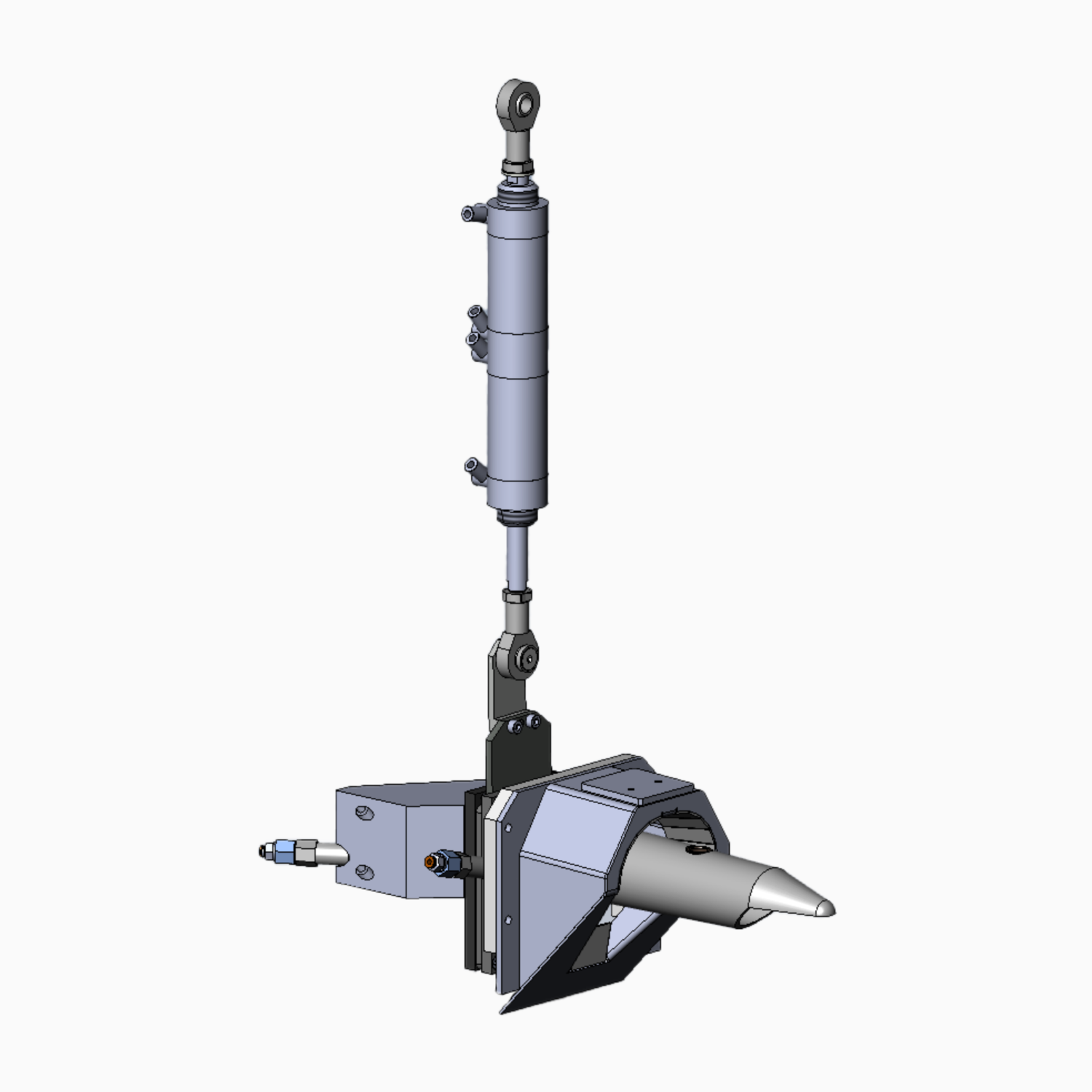
Features
Kit and compatibility
The complete FILLPro™ dust reduction kit includes: → Guillotine blade → Guillotine body with anti-clogging spring system → 3-position pneumatic cylinder → Joint between pump casing and guillotine with improved fluidization pipe → Front plate with product recovery inlet → Internal conveyor plates for product recovery → Conic nozzle based on customer bag valve size → Nozzle cover with dust trapping system The kit is suitable for GIROMAT® EVO generation rotary packers, with vertical axis impeller. Different sizes have been developed to fit different diameters of the exit conduit/nozzle/guillotine. The correct kit size will be selected based on the specific customer needs (i.e. bag and valve size).
Final results
Preliminary tests. The aim is to highlight differences in the front area of the spout. Fluidization is always switched on. The dust emission above the spout and on the bag saddle will be further reduced during next revisions of conveyor plates and nozzle cover.
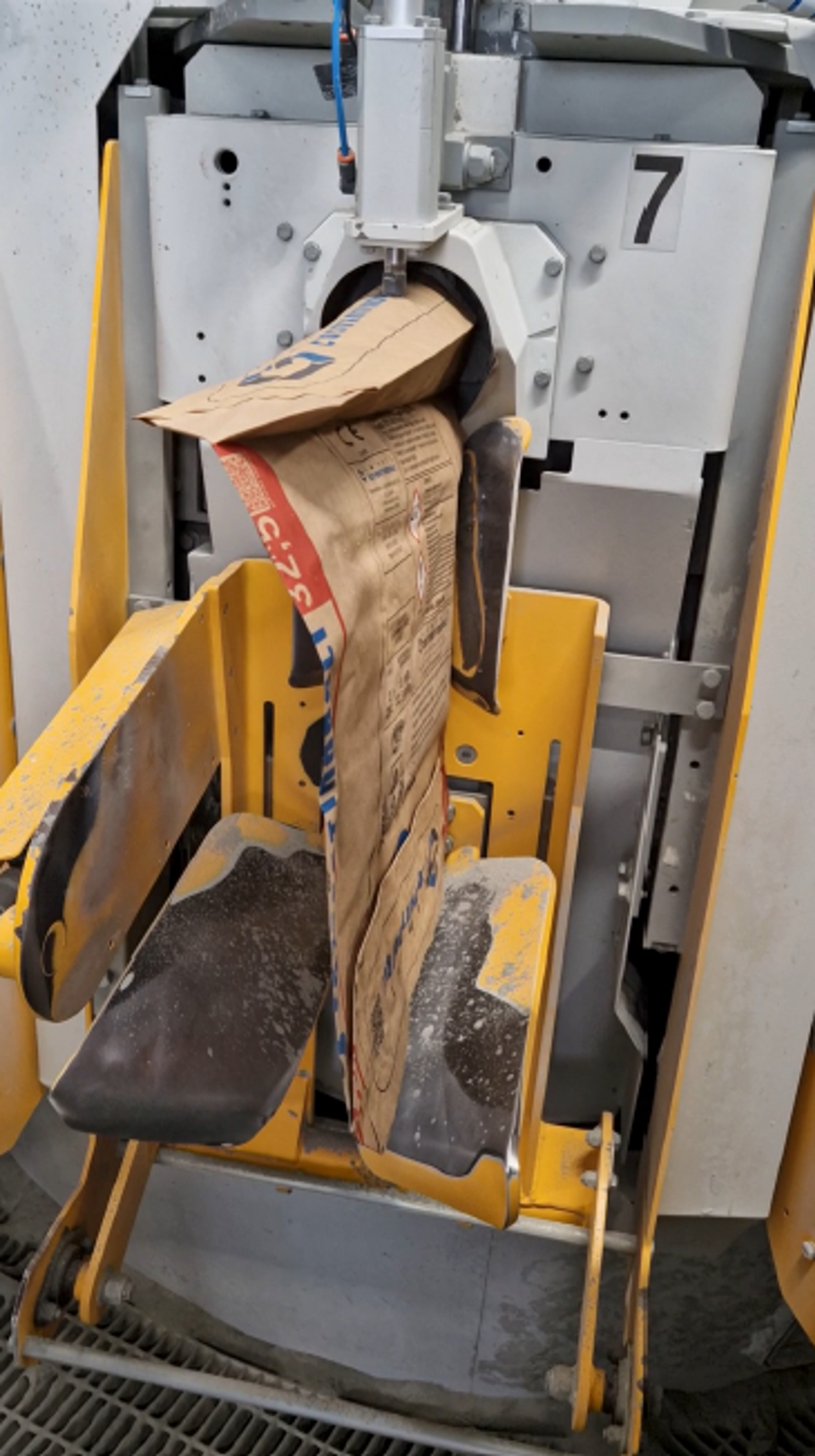
Without FILLPro™
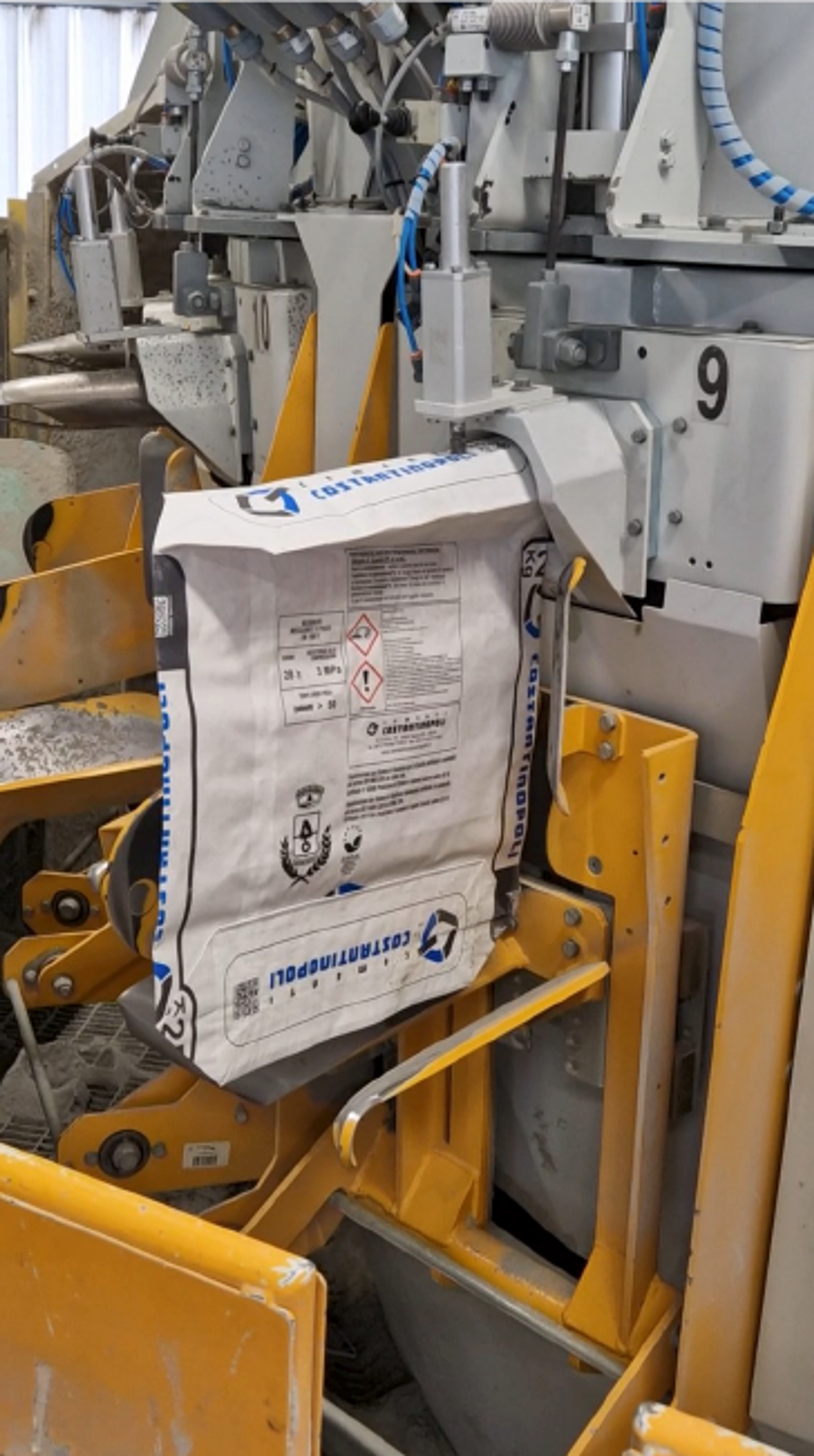
With FILLPro™
Pierluigi Varesini, Regional Sales Manager, Central America & Caribbean
Cleaner cement bagging is just an upgrade away
Upgrade your existing GIROMAT® EVO packer with our simple retrofit solution that instantly reduces dust and product loss. The FILLPro™ dust reduction kit delivers immediate improvements to your bagging operation while protecting both your equipment and personnel.