KilnLoq: A high temperature probe system built for difficult processes
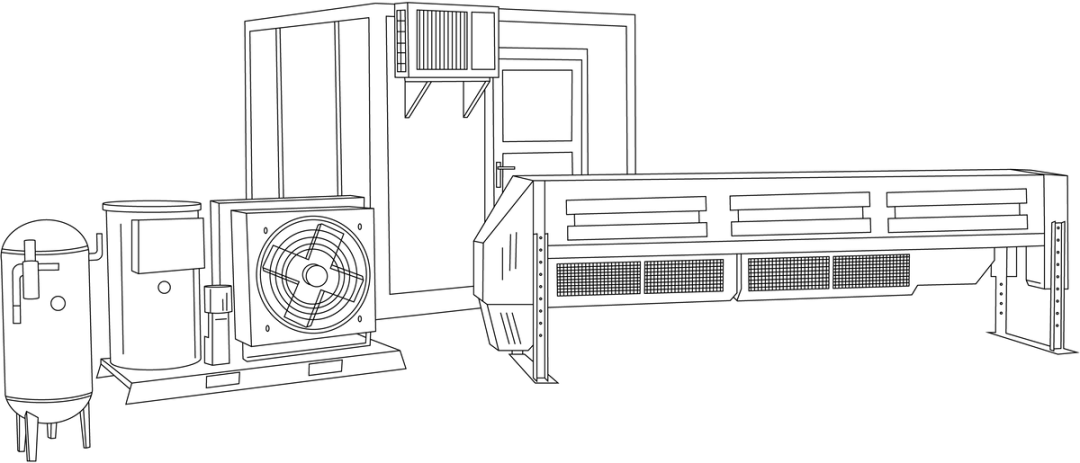
What we offer
A kiln inlet analyser system for real life kiln optimisation
Process conditions in the cement and minerals industries can be very harsh. Temperatures can reach up to 1400°C, and dust loads can be as high as 500-2000 g/m3. Strong and powerful equipment is required to operate in this kind of environment Handling the temperature and dust load, however, is a simple enough engineering task. All of our pyroprocess equipment is designed to handle these conditions. The real challenge comes when gas condenses in the raw material, which can happen if high concentrations of volatiles occur in the process. The result is sticky scaling on any surface exposed to the hot volatile-loaded gas – including the probe. Blockages can cause downtime of up to a couple of hours, during which you’re running your process blind. What’s the point of a gas analysis system that goes down when you need it the most? You need a better solution. One that recognises that unstable conditions occur and probes get blocked, but that hour-long outages are out of the question.
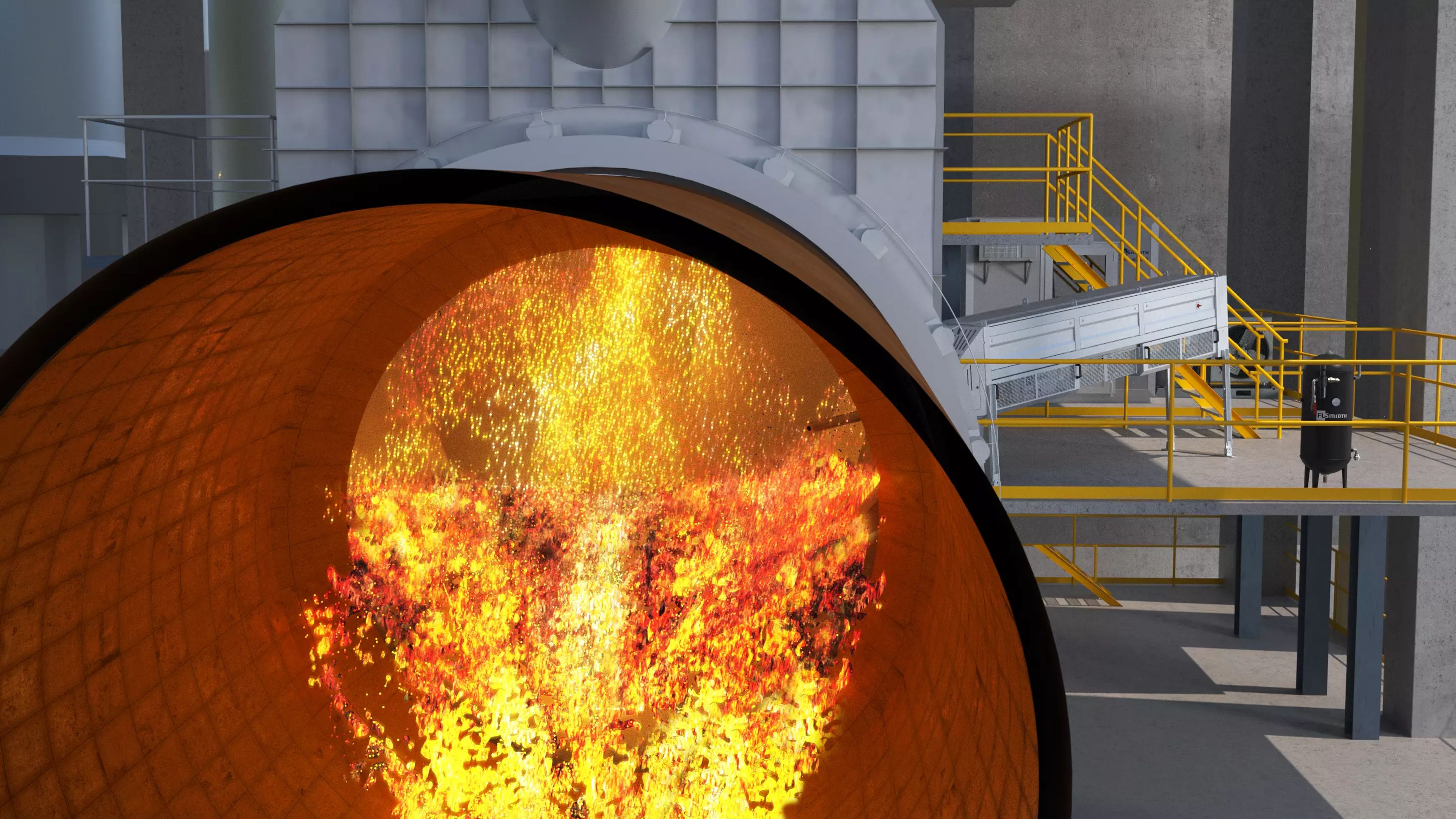
KilnLoq - Simple and powerful design
While exploring this problem, we came up with the simple and powerful design of the FLSmidth KilnLoq probe. It is robust and reliable. Perfectly suited to high-temperature, dust-laden conditions such as the kiln inlet or calciner exit. And it’s a solution that accepts that blockages happen, and deals with them immediately and effectively when they do. No long outtages. No expensive repair work. Just simple engineering.
We borrowed some ideas from the design of the air cannon to create the patented One-Pipe layout of the probe: one straight pipe with unmatched cleaning power. There are no mechanical plungers or rotating parts. There are no complex mechanical solutions. Just one straight pipe through the probe that can be cleaned and returned to operation in less than 3 minutes.
The result? Continuous gas analysis sampling that enables you to precisely monitor your process. Our kiln inlet analyser system measures critical gases in your kiln and enables you to react accordingly, to optimise your combustion process and reduce the occurrence of kiln stoppages.
Performance. Precision. A high temperature probe system that delivers.
Effective gas analysis has the potential to make all the difference to your operation. You can spot issues before they become problems, and deal with those problems before they become dangers. It’s a tool to improve operational safety as well as performance.
Kiln pyro control
Maintaining optimal levels of O2 removes the risk of explosion and prevents CO build-up
Kiln stop prevention
If O2, CO or SO2 build up in your kiln, there is a risk that production has to be stopped. Start-up can be challenging: throughput decreases and clinker quality may suffer. All this can be avoided with effective gas analysis.
Optimal fuel consumption
Gas analysis helps you control your O2 levels so that you can run your process according to market demand. Burn fuel fast for higher throughput or slow for more cost-efficient production.
Emission reduction
The more complete the combustion in the process, the less pollution your plant will produce. Gas analysis lets you regulate the O2 and CO at source, so you can optimise combustion and avoid expensive mitigation later in the process
Safety
f you are not in control of the levels of O2, CO and CH4 (methane) in your process, you are not in control of your pyro process – and that can have disastrous consequences.
Quality clinker
Gas analysis during production allows you to make fine adjustments to the process for the optimum clinker quality.
Control of volatiles
Detecting volatiles such as SO2 at source enables you to remove them from the process before expensive damage is caused.
A quick clean, and then back to work
Blockages in your gas analyser can prevent you from getting a reliable read. Gases condense, your probe surface gets scaled up, and before you know it you’ve lost two hours of measurements while the probe is manually cleaned. What was happening to your process during that time? You may never know.
We would love to tell you the KilnLoq gas analysis probe never gets blocked. But the reality is that all probes experience blockages. That is the nature of the high temperature, high dust environment we are dealing with. The KilnLoq probe system is built with an automatic cleaning process, which at most plants keeps the system running for a long time – but eventually it blocks and manual cleaning is required. Other probes with a more complicated design will take a long time to clean – time you can’t afford to lose. Our One-Pipe design is deliberately simple, enabling the KilnLoq probe to be cleaned and returned to use in less than 3 minutes. No other probe system on the market comes close for speed and ease of maintenance.
The patented One-Pipe design of the KilnLoq probe was inspired by the successful Air Blaster cleaning equipment. Just like an Air Blaster, One-Pipe has no bends, no kinks, no bulges: just a length of smooth, straight pipe. The probe runs the entire length of the pipe before connecting to a solenoid valve and an oversize air tank. Maintenance-friendly and capable of tackling any kiln inlet process, the air blaster-like design makes cleaning the probe quick and easy.
Simply effective kiln optimisation
Since its launch in 2003, the KilnLoq gas analyser system has become the preferred probe system for the cement industry. Typically used in kiln inlets and calciner exits, the KilnLoq probe is designed to withstand the harsh, high-temperature environment of your pyro process.
How it works
It’s simple. A sample of the gas is continuously drawn out from the process through a straight sample line into the conditioning system. There are no bends, obstacles or deposits to get in the way of your sample. The gas conditioning system removes all dust and dries the gas and any contaminating components. The gas is then delivered to the analysers with a fixed reference of dew point, flow, pressure and temperature in order to establish an analytical correlation with data taken at any other time. The entire sampling system is heated to 180˚C to avoid condensation. With data gathered from the KilnLoq sample, operators can adjust the process to correct unstable conditions swiftly and effectively. Furthermore, the KilnLoq system monitors potential scaling tendencies in the process and on the probe. This feature will support proactive measures by maintenance staff and operators and help keeping the process and probe system running without unnecessary production cuts.
KilnLoq One-Pipe - Automatic cleaning
The KilnLoq One-Pipe system has three cleaning systems that work in harmony to clean the sample path thoroughly from end to end. Firstly, the probe tip is cleaned to remove any deposits that could reduce the effectiveness of the main One-Pipe cleaning process. A jet of compressed air is then blasted through the entire length of the One-Pipe probe. At the same time, air is blown backward through the filter, lifting dust deposits off the filter filaments. This dust is swept up by the blasts of compressed air in the main body of the pipe and blown back into the kiln. This method keeps the probe clear for much longer than other solutions, but when the probe does inevitably block, as they all do, manual cleaning is easy. An access port at the end of the One-Pipe probe can be open in seconds, providing full access to the sample path’s entire length. You can clean out the entire length of the probe in a couple of minutes. And when the access port is open, the sample path can be visually inspected in seconds. This system is so effective that some of the first KilnLoq probe systems installed in 2003 are still operating with their original filters.