The most durable coal mill for grinding all types of raw coal
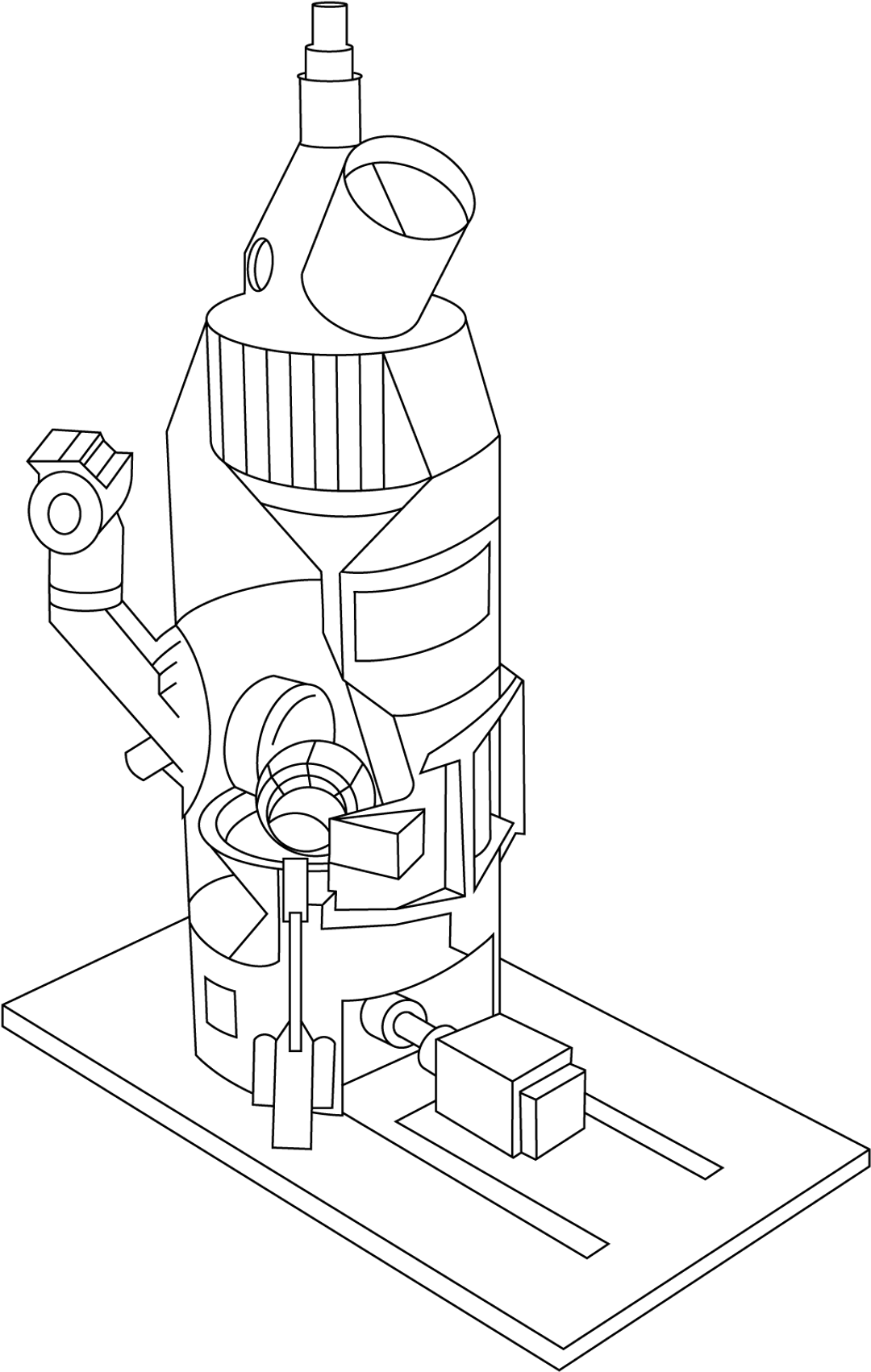
What we offer
A compact coal mill solution for grinding virtually any type of raw coal
Our ATOX® Coal Mill is a compact vertical roller mill that can grind almost any type of raw coal. The coal mill utilises compression and shear force generated between the large rollers and the rotating table to crush and grind raw coal, removing the need for a separate piece of equipment for crushing. The coal mill can also grind petroleum coke and anthracite down to a fineness below 5% +90 micromillimeters (mm) when coupled with a variable speed mill motor.
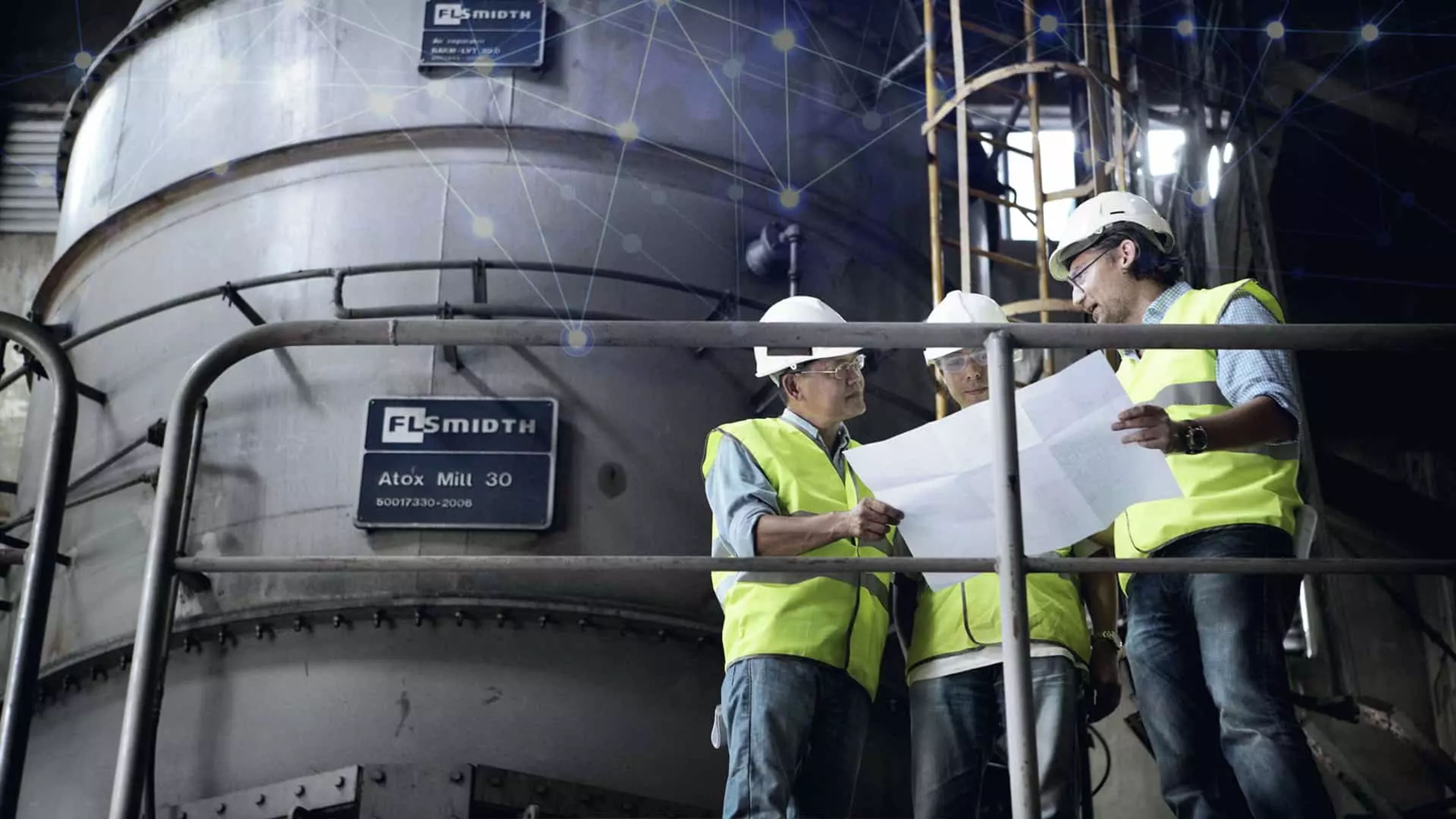
No sticky situations
The ATOX® Coal Mill can grind and dry raw coal with up to 25 percent moisture level. By adjusting the gas flow stream with the nozzle, you can deal with more ‘sticky’, high-moisture feed materials. There is an oversized nozzle ring and separator that is available to make this adjustment.
A fine operation
As the feed material is added to the mill, the moisture evaporates almost immediately. A continuous gas stream from the nozzle carries the finer particles to the separator, where they will be assessed for the specified fineness. For safety reasons, the coal mill is designed with no external recirculation of materials. Material is prevented from spilling over the edge of the dam ring as both the dam ring height and grinding pressure are adjustable.
The ATOX® Coal Mill’s efficient separator allows material that has reached the required fineness to leave the grinding mill and sends oversized material back for further grinding. The fineness is controlled by adjusting the rotor speed. The high efficiency of the separator is due to the rotor being equipped with an outer ring of louvre plates that are hardfaced for longevity.
The three relatively large diameter rollers enable the ATOX® Coal Mill to handle up to 200-millimetre feed lumps, reducing the use of energy and wear in the crusher.
Safety comes first
Our dynamic ATOX® Coal Mill can operate under inert and non-inert conditions. The determining factor being the exploding potential of the coal. Low to moderately-explosive coal types are safely ground under non-inert conditions where atmospheric air is used to maintain the system. As a safety precaution, inert conditions can be created by using kiln exit gases and recycled filter air.
Standing the test of time
Its compact design means the ATOX® Coal Mill has low installation costs. This vertical roller mill is easy to maintain, with easy-access doors designed for planned and unplanned maintenance, where parts like the rollers, can be serviced without having to remove them from the mill. The materials chosen for the ATOX® Coal Mill are highly durable – an important element when dealing with very large volumes of hard and abrasive material. The coal mill is able to stand the test of time, lasting longer than its predecessors.
No unexpected downtime
Unexpected downtime can cripple your operations. Our online condition monitoring services for ATOX mills help avoid unscheduled outages by picking up the earliest indications of failure. This not only enables you to act before the failure has the opportunity to cause widespread damage and disruption; it also gives you the chance to plan maintenance tasks at a time that suits you.
Our online condition monitoring services utilise a combination of plant data, AI-driven diagnostics software and the expertise of our 24/7 Global Remote Service Centre team to understand what’s going on in your mill, and what needs to be done to fix it. These recommendations are delivered via your account manager, for you to act on in the way that best suits your schedule.
Choose ATOX® Coal Mill for all your raw coal grinding needs
Handles all types of coal
The durable grinding mill can handle virtually any type of raw coal and has been designed to grind feed materials with varying moisture levels. The ATOX® Coal Mill handles feed materials with less than one percent moisture and up to 25 percent moisture, where abrasiveness and stickiness is not an issue for grinding.
Long-lasting durability
The materials used to produce the ATOX® Coal Mill’s segmented wear surfaces are durable and therefore, last longer. The reversal of liner segment option maximises use of these hard surfaces, making sure every surface is exploited while helping to address uneven wear at the same time.
High separation efficiency
The separator, with the highest mill capacity, ensures high separation efficiency through having a low bypass to reject. An efficient separator leads to a number of benefits including low specific power consumption for the mill motor, low vibrations, energy savings due to minimal pressure loss, and optimised airflow. Long-lasting durability is extended to the separator where the inside of the reject cone and outlet top section are faced with Densit®. The wear plates for the louvres are also hardfaced to maximise wear life.
Easy maintenance, simple and flexible operation
The ATOX® Coal Mill’s equipment is located at or above floor level for easy maintenance and cleaning. There are easy-access doors for inspection and maintenance of all of its parts, where roller replacement can occur while still inside the mill. For comprehensive maintenance, the large door is removable for crane access. Our coal mill offers the flexibility of non-inert and inert operation, depending on the exploding potential of your coal type. The tailored layout considers your coal grinding needs, ensuring simple and optimised operation. For example, the availability of heat sources to dry raw coal helps determine the final layout.
High flexibility with segmented liners
Liner segments can be reversed so that the wear, which normally occurs on the outer edge, can be spread evenly, making use of the entire segment surface. The coal mill’s liner segments can also be repeatedly hardfaced for maximal longevity.
Grinding raw coal with ease, using our ATOX® Coal Mill
Easy adjustment for desired amount
The dam ring is made up of stacked, bolted-on, segmented rings and is easily adjusted by adding or removing one or more segmented rings. The height of the dam ring determines the amount of raw coal on the grinding table.
Rollers help handle virtually any type of coal
The ATOX® Coal Mill’s large rollers can handle up to 200mm feed lumps, reducing the need for a separate crusher. Large rollers also help ensure a thick grinding bed for maximum uptime. The roller segments are reversible which ensures the highly durable materials are fully utilised. Our ATOX® Coal Mill can also be equipped with a water injection system to compensate for low water content in the raw coal.
Rotary feed sluice optimises mill operation
The heated rotary feed sluice ensures uniform flow of feed into the ATOX® Coal Mill for optimum mill operation including minimising power consumption. It is the right solution for a sticky feed material as hot gas from the mill inlet is guided through the rotor, preventing the sticky feed material from caking onto the rotor.
No separation anxieties
Located above the grinding rollers, the separator is very efficient because the rotor is equipped with an outer ring of louvre plates. The separator’s rotor runs inside a ring of guide vanes, which facilitate intake of the material entrained in the air from the mill into the rotor. The rotor rejects coarse particles, sending them back to the grinding table for further grinding. You can select the desired fineness by simply adjusting the rotor speed for the separator.
Segmentation of wear parts for longer life
Segmented wear parts for the grinding table and rollers allows us to use the most wear-resistant materials where they are needed the most. Segments of Hi-Chrome material are not only shock resistant, but also offer the option of reversing the liner segment, essentially doubling the life of the hardfaced layer. Further, the segments are suitable for repetitive hardfacing and for highly abrasive materials, Hi-Chrome segments with embedded ceramic inserts further increase the lifespan of the segments.
downloads
Brochures
First-time service agreements for new ATOX Milla and key ATOX Mill components
20.05.2024 |
263.11 KB |
English