At last: a hot/wet gas analysis system that excels in high sulphur conditions
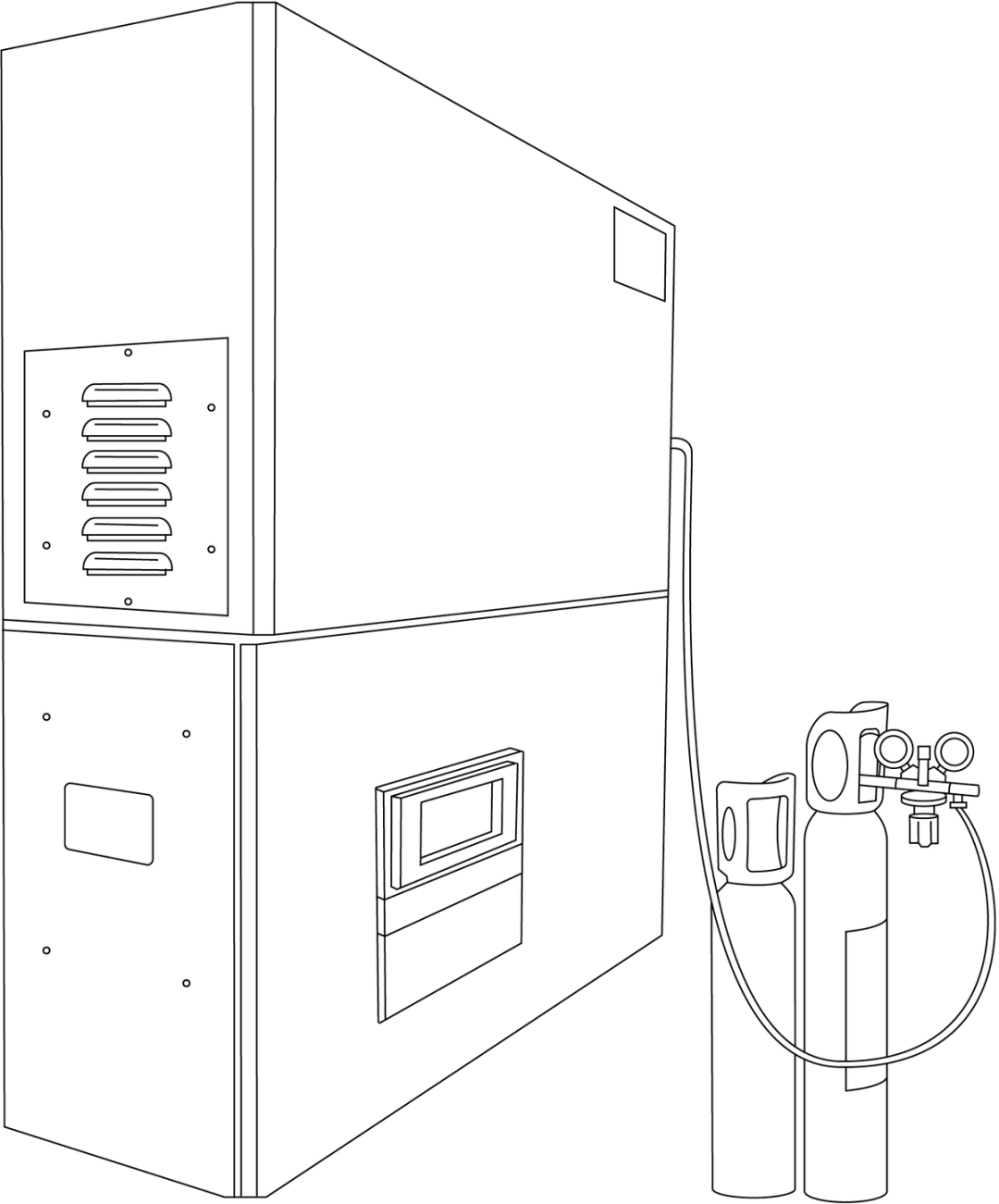
What we offer
Eliminating acid damage with the KilnLoq® HW Laser Gas Analysis System
Alternative fuels and raw materials with high sulphur content can damage your gas analysis system. Acid formation and corrosion can take your kiln inlet analyser out of operation altogether, leaving the kiln operator blind. Repairs are expensive and time consuming. And while you wait for your gas analysis system to be fixed, you can’t take the crucial measurements that can help you optimise the process and keep emissions in check.
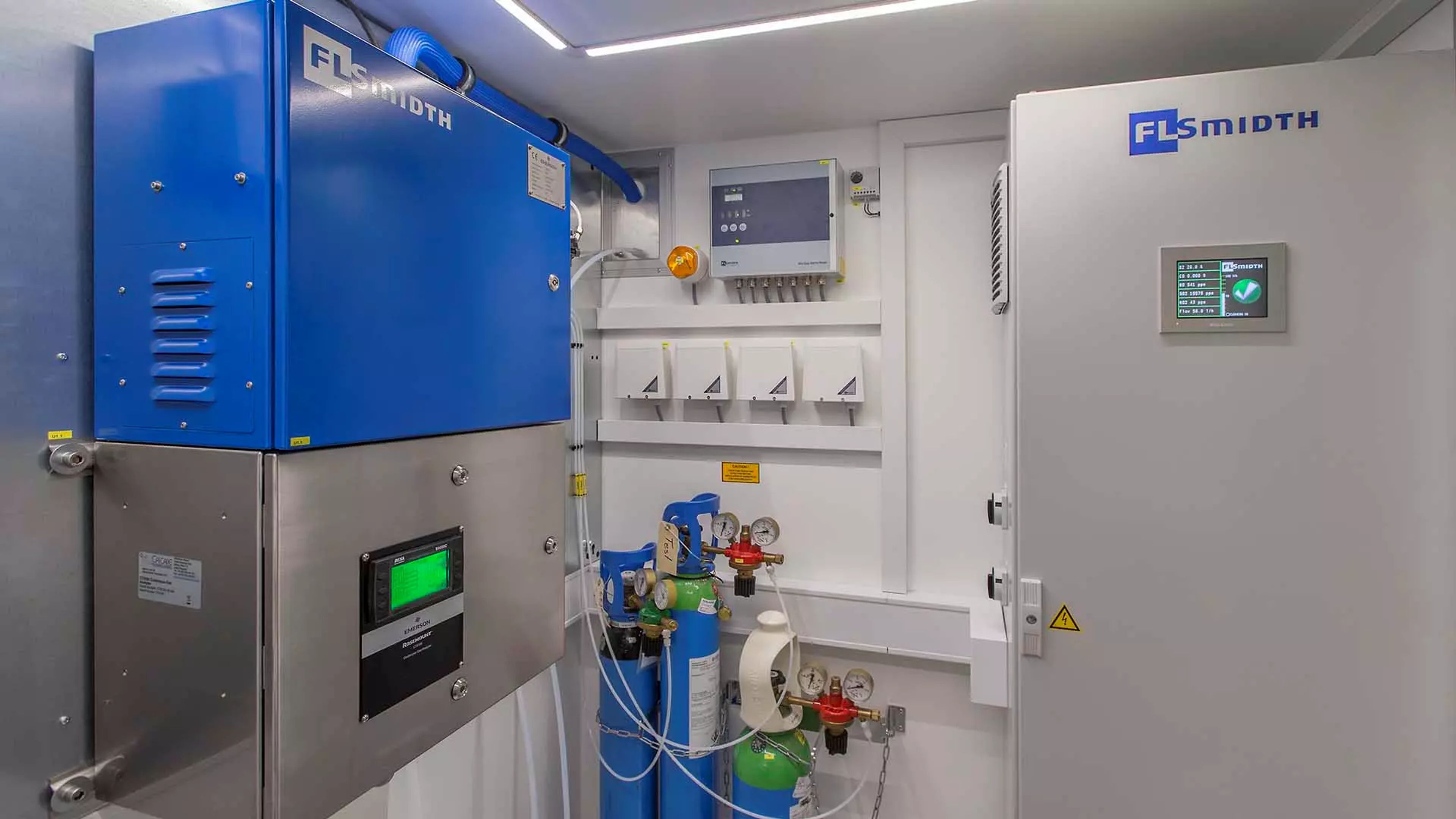
If your gas analysis solution can’t cope with your process, it’s not a solution. It’s a problem.
The KilnLoq® HW Laser Gas Analysis System is designed for these high sulphur conditions. It’s a state-of-the-art hot/wet gas analysis system based on laser technology that works in combination with our KilnLoq kiln inlet probe system. The temperature of all parts is kept at 180˚C – above the acid dew point – so that acid damage is entirely avoided. No expensive maintenance. No equipment downtime. No more prolonged data blackouts. Just fast, precise measurements. The KilnLoq® HW Laser System measures gases such as CO, NO, SO2, CO2, HCl and O2 at the kiln inlet. This insight enables kiln operators to optimise the air to fuel ratio for the best possible fuel consumption and clinker quality. This one-of-a-kind solution is designed for plants with high sulphur processes, whether because they are burning alternative fuels such as tyres and plastics, or because there is simply a high sulphur content in their raw materials. It’s also an ideal option for: Plants wishing to measure water-soluble components such as HCl and H2O; Plants experiencing high SO3 values that wish to measure SO2; and Plants that do not want to use H2O2 dosing due to safety and maintenance issues
The hot/wet solution
A hot/wet analysis system maintains a temperature above the sulfuric acid dewpoint so that the gas being measured is both hot and wet. Conventional gas analysis methods use a cold/dry system in which the gas being sampled is passed through a cooler and analysed in dry conditions at temperatures around 5˚C – a danger zone for acid formation. Hot/wet analysis is already widely used today, especially for CEMS (Continuous Emission Monitoring System) applications, mainly in the form of multicomponent FTIR analysers. However, these systems are commonly limited to lower measuring ranges than those required in process measurement, they’re typically complicated, and they’re high maintenance.
Proven laser technology
FLSmidth’s KilnLoq® HW Laser System is the only system of its kind. It utilises robust, low-maintenance Rosemount CT5100 laser technology, which has been around for over 20 years. During that time, this technology has successfully proven to offer reliability, a long lifetime and instant response time.
Hot/wet laser technology: A unique combination
The KilnLoq® HW Laser System is the only laser-based hot/wet analyser solution on the market;
The simplest hot/wet analyser solution with the least maintenance requirements and the most accurate hot/wet gas analysis solution available.
Hot/wet laser technology: A unique combination
The KilnLoq® HW Laser System is:
- The only laser-based hot/wet analyser solution on the market;
- The simplest hot/wet analyser solution with the least maintenance requirements and the most accurate hot/wet gas analysis solution available.
Fast, precise hot/wet gas analysis without the downtime
The KilnLoq® HW Laser Gas Analysis System for the kiln inlet uses Rosemount’s QCL/TDL technology with patented laser chirp technique. It expands gas analysis to both the near and mid-infrared range to enhance process insight, improve overall gas analysis sensitivity and selectivity, remove cross interference and increase response time. CO, NO, SO2, CO2, HCl and O2 can all be measured precisely in less than a microsecond. This technique provides significant benefits: It's accurate and fast; robust and reliable; compact; cost-effective; multiple measurements along same optical path.
High sulphur levels cause big problems
Burning alternative fuels such as tyres and plastics can introduce a lot of sulphur to your process. In some facilities, that sulphur is already present in the raw materials, even before introducing alternative fuels. Sulphur dioxide (SO2) can react with oxygen to produce sulphur trioxide (SO3), a dangerous chemical that reacts violently with water and produces highly corrosive sulfuric acid. Once you’ve got SO3 in your system, it’s hard to get rid of. Even ultra-low temperature coolers won’t eliminate water completely. The result? Extensive acid damage inside the gas analyser chamber and costly repairs that can’t usually be carried out onsite.
Hot/wet analysis eliminates acid damage
Where other analysers may succumb to extensive acid damage, the hot wet design of the KilnLoq® HW Laser System prevents condensation, keeping the gas analyser chamber free from acid formation and damage. Moreover, the KilnLoq® HW is very low-maintenance, benefitting from a simple design and a high degree of flexibility. Its modular layout enables laser modules to be easily replaced on site, ensuring minimum downtime, while the ability to fit six laser modules in total makes it possible to measure up to 12 parameters simultaneously.
Hot/wet technology compared to cold/dry
- Less consumption of wear/spare parts – expected saving over 5 years: EUR 8000.
- Savings on maintenance hours – reduced from 2 hours/week to 2 hours/month; expected saving over 5 years: 400 hours.
- Savings on man-hours for calibration due to less drift on analyser – reduced from once per week to once per year; expected saving over 5 years: 250 man-hours.
- Savings on repairs due to acid problems – expected savings over 5 years: EUR 35.000
Combining two reliable technologies: KilnLoq® Probe and Rosemount laser
Introduced in 2003, the KilnLoq® probe has proven to be the optimum solution for kiln inlet gas analysis with more than 300 references worldwide. While other products may have bends, obstacles or deposits that can get in the way of samples, the KilnLoq® probe uses the One Pipe system, which samples gas in a straight pipe. The process gas enters the filter housing through the centre of the pipe, where it passes through a coaxial filter for collection and analysis. The filter itself is built into a section of the One Pipe sample probe and the entire probe system is heated to 180°C, preventing the condensation of sulphuric acid.
Benefits of a One Pipe system
The unique One Pipe system features several benefits for cleaning, maintenance and inspection; Cleaning sequence setup is adaptable to process conditions; Probes stay clean for longer: The straight pipe means no bends or filters in the sample path to trap dust and the patented One Pipe design ensures much more powerful cleaning. Quick and easy maintenance and cleaning: Fully clean the sample pipe in less than 3 minutes – up to 40 times faster than any other systems on the market and no need to dismantle any machinery for cleaning or maintenance. Moreover, compressed air jets blast dust and residue out of the sample path in one go; Fast inspections: View the entire length of the probe’s sample path in seconds – the industry’s fastest visual check.
The QCL analyser: speed and precision
Backed by two decades of reliability, the low-maintenance Rosemount CT5100 Quantum Cascade laser analyser used in the KilnLoq® HW Laser System has proven dependability, longevity and instant response time. The design is straightforward and highly flexible. It can measure up to 12 parameters simultaneously, increasing efficiency, and allows easy on-site replacement of the laser modules, ensuring minimum downtime.