Our air-to-air heat exchanger offers you superior excess gas cooling
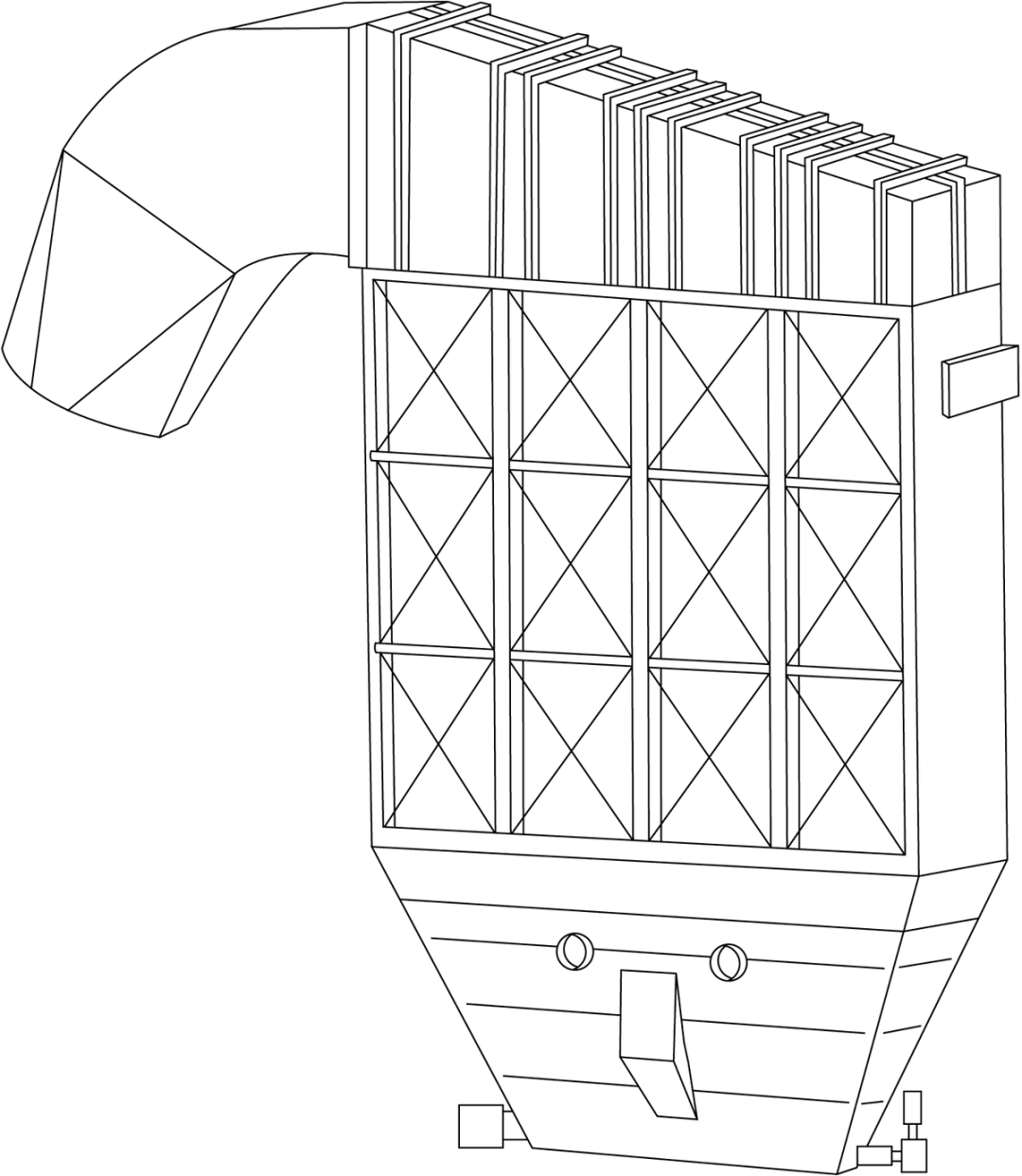
What we offer
A reliable air-to-air heat exchanger for effective excess gas cooling
Production of cement clinker produces a lot of hot, dust-laden excess gases. These hot gases need to be cooled quickly to reduce negative impacts on downstream equipment and to meet emission requirements. For efficient and reliable cement clinker excess air cooling, our air-to-air heat exchanger for gas cooling showcases smart technology with a modular design to fit your cooling needs.
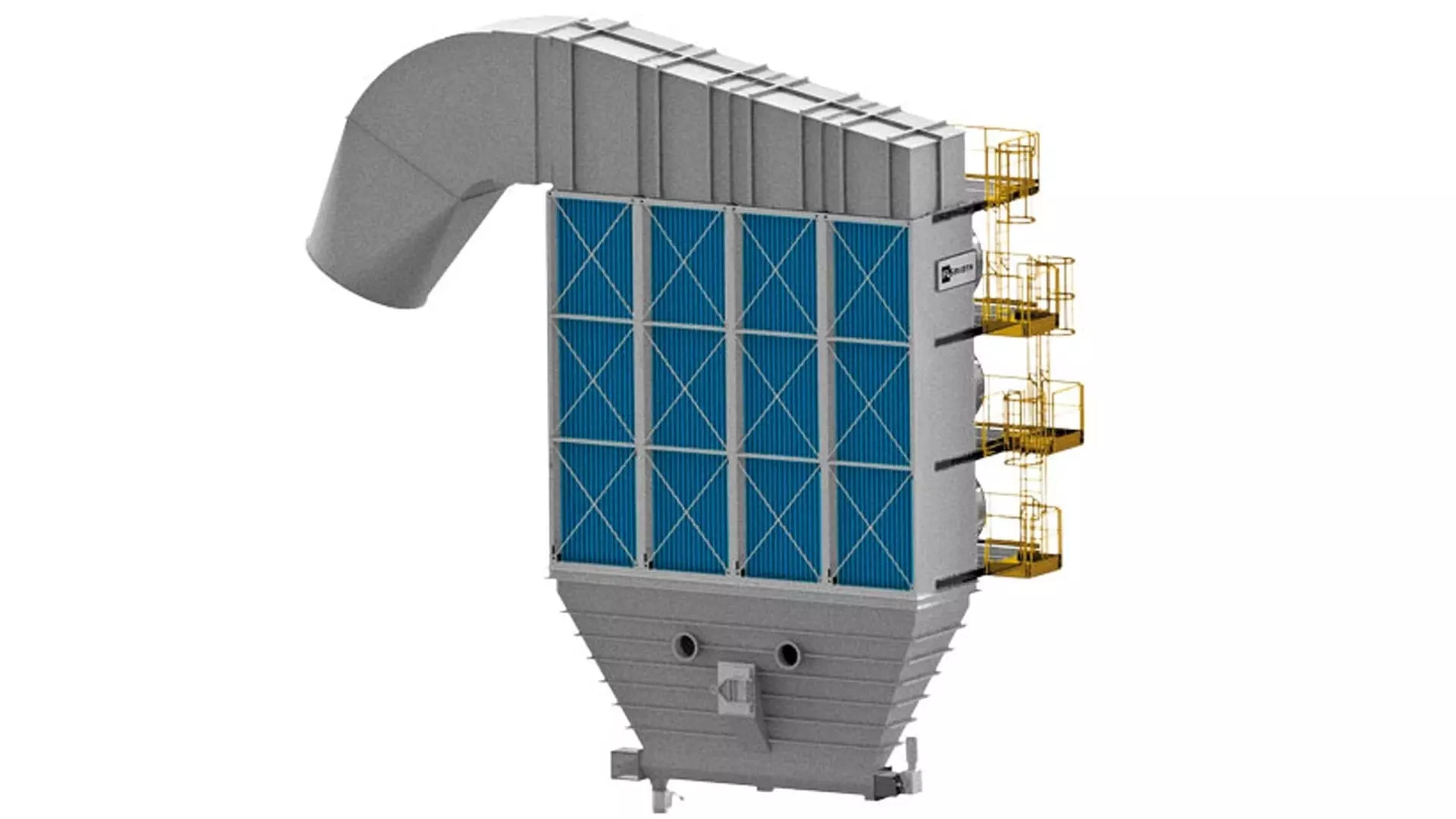
Efficient excess gas cooling
The underlying operating principles of the air-to-air heat exchanger for gas cooling involves the use of many fans and tubes. The excess gas from the clinker cooler is ventilated to the heat exchanger where it passes evenly through vertical parallel tubes. Cooling air is blown horizontally over the outer surface of the tubes by axial flow fans.
The upper fan row has full-speed cooling fans whereas the rest of the fan rows have a common frequency drive per row. The outlet temperature is controlled by changing the speed of the fans and the number of rows in operation. This method minimises power consumption.
It’s getting cool in here
The air-to-air heat exchanger handles cooling from 500°C to 120°C (or any range in between) with flexibility in the desired size for any kiln and cooler available in the market.
Our tough air-to-air heat exchanger comes with pre-assembled modules and fans for lower initial costs and total installation costs. Small axial fans are used to cool the hot excess gas, reducing operating costs due to decreased power consumption.
Designed to meet your needs
Depending on your gas cooling needs and the configuration of your production line, our highly-flexible air-to-air heat exchanger can be configured to allow gases to enter from either the side or the top. The surface area of the vertical tubes that carry the excess gas can be adjusted to provide optimum performance, depending on the desired temperature drop and the expected inlet gas flow. Modules can be added to accommodate increases in production.
Ease your maintenance
Years in the cement industry means we are well-acquainted with how heat exchangers wear over time. Easily replaceable wear parts at each tube inlet, where wear is known to occur, make maintenance of our air-to-air heat exchanger simple. In addition, each fan motor can be maintained while the air-to-air heat exchanger remains in operation, helping to reduce costly down-time.
Air-to-air heat exchanger excels in clinker cooler excess gas cooling
Modular design for fast installation and expansions
Our air-to-air heat exchanger modules and fans arrive to you, pre-assembled for your installation convenience. Additional modules are easily installed if you want to increase production.
Low power consumption for the cooling fans
The design decision to use small axial cooling fans results in lower power consumption, saving you on operational costs and reduced emissions.
Low initial costs and minimal maintenance demands
Our highly-optimised heat exchanger, with its modular design, is cost effective and reliable. The simple yet clever design of the air-to-air heat exchanger means we keep your maintenance costs down. By offering wear parts that are simple to replace, less time is spent on maintenance. Fan motors can be repaired or replaced while the air-to-air heat exchanger remains in operation, meaning no costly production shut-down.
Long lifetime of downstream filter bags
The air-to-air heat exchanger reduces excess gas temperature to the desired operating temperature of the downstream filter. This prevents filter bag damage, unstable kiln hood draft control and limited vent system capacity even during sudden flushes from the kiln. When extreme temperature fluctuations occur, two safety dampers introduce fresh air into the process, protecting the filter bags. More affordable bags with lower operating temperatures can be used, if desired.
Air-to-air heat exchanger designed to ease your gas cooling pains
The technology behind the heat exchanger’s design is referred to air-to-air heat exchange. This simply describes using forced air to cool the hot gases, or in this case, cooler excess gas in the tubes.
Small axial fans to reduce energy use
The number of fans is highly dependent on the number of modules you select for your air-to-air heat exchanger.
Easily replaceable wear parts
In heat exchangers, wear tends to occur around the tube inlets, due to the extreme heat and dust-laden gases. These wear parts are easy to replace as they are simply placed on top of the cooling tube like a cap. Fan motors can also be maintained while the air-to-air heat exchanger is still in operation.
Designed for easy transport and assembly
The air-to-air heat exchanger modules are assembled in the workshop and transported to site in standard containers. Each module consists of a bundle of carbon steel tubes and tube sheets, assembled within a structural frame. The tubes are shop-welded to upper and lower tube sheets, with intermediate tube sheets located between fan levels. The lower and intermediate tube sheets are welded to the frame, while the upper tube sheet floats to allow for tube expansion.
Another one bites the dust
The dust precipitated from the gas stream is collected in a bottom hopper and transported out by a screw conveyor. At the discharge of the screw conveyor, a flap valve minimises false air intake before passing the dust to the subsequent conveying system.