The solution to achieve maximum substitution in your calciner fuel with a wide range of alternative fuels
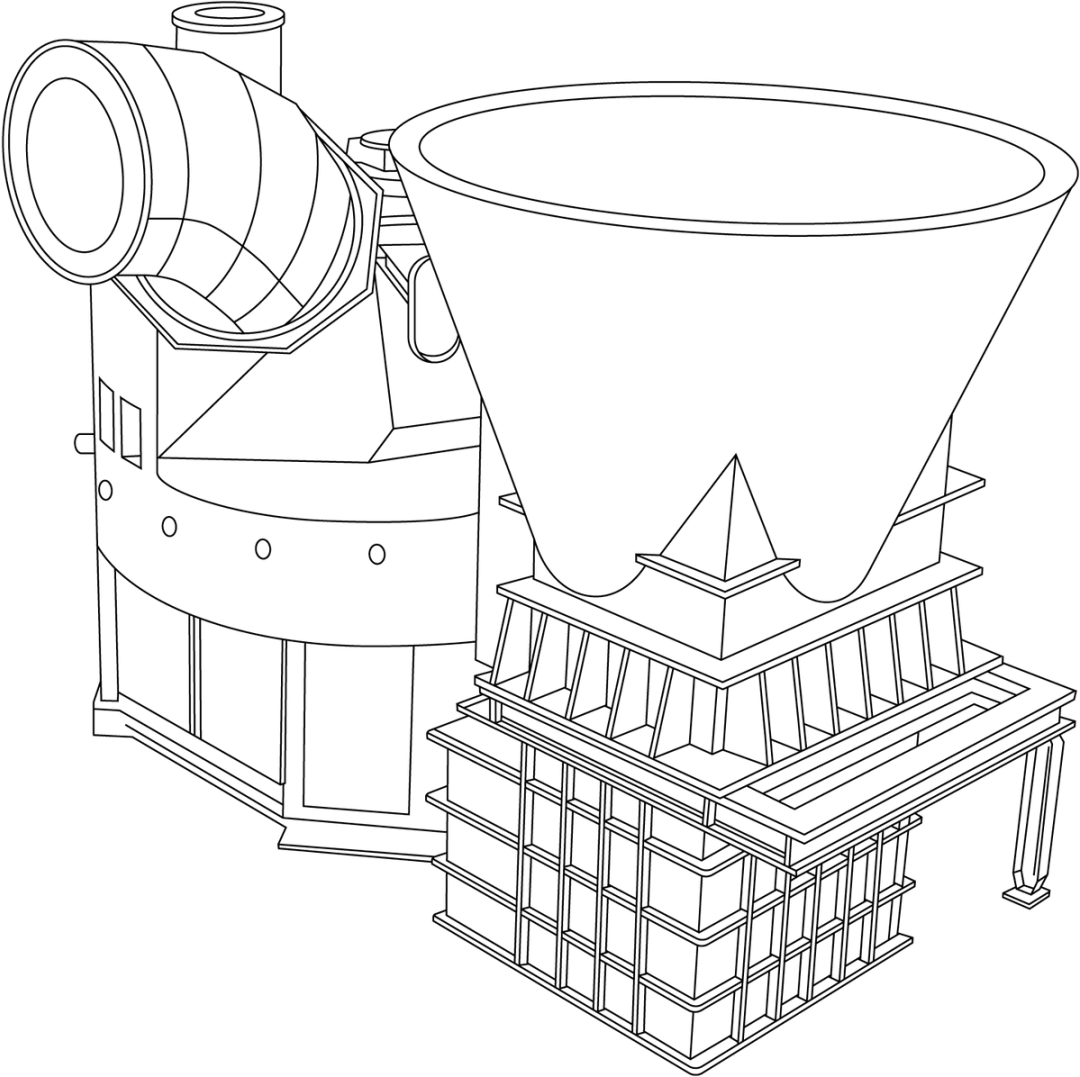
What we offer
Waste to energy and the freedom to choose lower-cost alternative fuels
From sludge and grains to whole truck tyres, our HOTDISC Reactor gives you the potential to burn a wide range of alternative fuels, without compromising on energy efficiency or kiln performance
Enjoy unsurpassed fuel flexibility and security
The HOTDISC alternative fuels solution can handle a wide variety of solid waste in sizes up to 1.2m – from sludge or grains to whole truck tyres. – without the need for expensive shredding of lumpy waste material or pre-drying. This makes the transition to alternative fuels much easier and more cost-effective, especially in regions that lack a developed waste processing industry. And because you are no longer tied into any single fuel supplier or supply chain, the HOTDISC improves your position on the fuel market.
Proven performance
The HOTDISC’s use of clinker cooler tertiary air and preheated raw meal, along with alternative fuel, ensures virtually 100% energy efficiency. The HOTDISC is designed to achieve a calciner substitution rate of 50% up to 80% of the calciner fuel, and potentially even higher. Results vary by the specific plant conditions and fuel specification. With over 20 years of documented results, we can confidently predict the performance you can expect at your plant.
Take full control of fuel combustion
The variable speed drive provides the ability to have a fuel retention time of 3 to 45 minutes inside the HOTDISC. This reduces the adverse effects of unburned fuel in the kiln inlet and provides complete control of the process. Consequently, the HOTDISC eliminates operational disturbances such as cyclone blockages, the need for extra cleaning in the riser duct and emissions of unburned components. These disturbances typically occur if combustion and sulphur circulations from unburned fuels cannot be controlled.
Proven technology for new builds or retrofits
Since the introduction of the HOTDISC in 2002, we’ve continuously improved the design of the system. The latest generation provides maximum fuel flexibility, process control, capacity and durability. The HOTDISC is available for new kilns and for retrofit into existing kiln systems.
What do you want to burn?
• Refuse-derived fuel - for example, MSW (municipal solid waste) and SRF (solid recovered fuels) • Old tyres – whole, shredded or cut into pieces • Biomass • Paper sludge • Sewage sludge • Lime-stabilised oil sludge (from tanker cleansing) • Old car fragments (upholstery, dashboards, etc.) • Impregnated wood waste • Hazardous waste
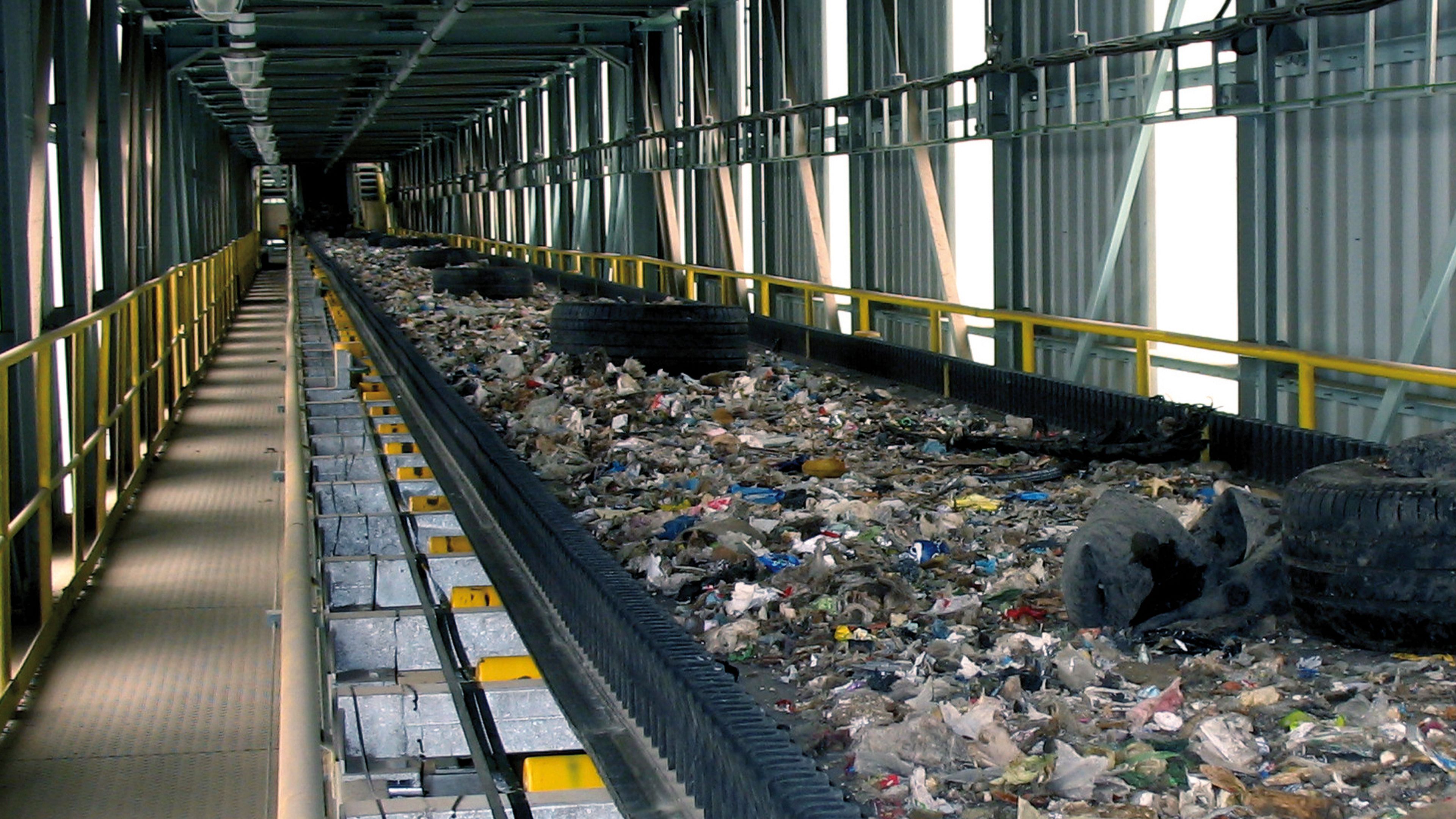
Economically replace your calciner fossil fuels with alternative fuels
Replace fossil fuels with coarse alternative fuels for lower costs
Some alternative fuels are less expensive than others and the HOTDISC Reactor gives you the ability to pick and choose the best available options on the market – delivering full cost efficiency. And thanks to its high energy efficiency, the HOTDISC ensures your pyro system can run at full capacity while consuming less fuel and power. The result? Better performance and lower operating costs.
Flexibility to use a wide range of alternative fuels qualities
Able to burn almost anything – from sludge to truck tyres – our HOTDISC Reactor means you are not tied to one fuel type or supplier. Waste to energy frees up your cement plant to burn your preferred fuel – without compromising function.
Impressive substitution rates with difficult alternative fuels
The HOTDISC Reactor is designed to achieve a calciner fuel substitution rate of up to 80%, although results vary significantly depending on specific plant conditions. Our specialists accurately estimate the exact performance results you can expect at your facility – and we guarantee that it will deliver.
High kiln availability
A fuel retention time of up to 45 minutes reduces the adverse effects of unburned fuel in the kiln inlet. This means no extra cleaning of the riser duct, avoids operational disturbances such as cyclone blockages and eliminates emissions from unburned components – giving you exceptionally high kiln availability.
All the maintenance access you need
The HOTDISC Reactor is designed for long-term uninterrupted performance, with regular maintenance done during planned shutdowns for the whole plant. It requires similar maintenance to other kiln system components and features various platforms, manholes, doors and clean-out holes – giving your personnel easy access.
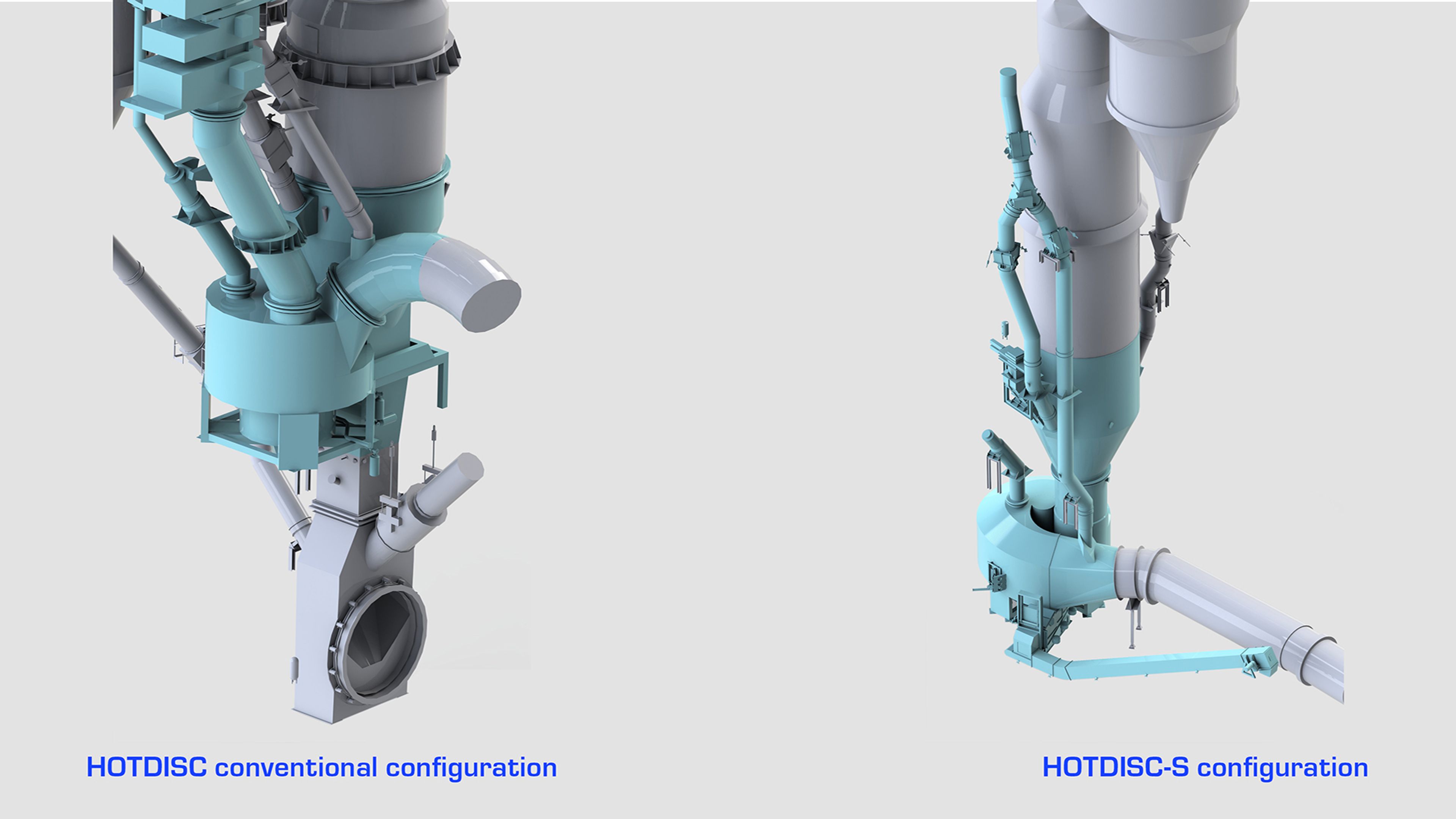
HOTDISC®-S
The HOTDISC®-S for separate line calciners
The standard HOTDISC® is designed for installation at plants with In-Line Calciners (ILCs). But what if you have a separate line calciner (SLC)? Conversion from an SLC to an ILC is unlikely to be a feasible option due to the high expense involved. The HOTDISC-S provides an alternative. Unlike the standard HOTDISC, the HOTDISC-S is positioned under the existing calciner. Most of the alternate fuel is fed first into the calciner with any unburnt fuel falling into the HOTDISC-S, where it completes burnout. Any drop-out from the HOTDISC-S is recovered via an ABC inlet for cooling and can be transported back into the system.
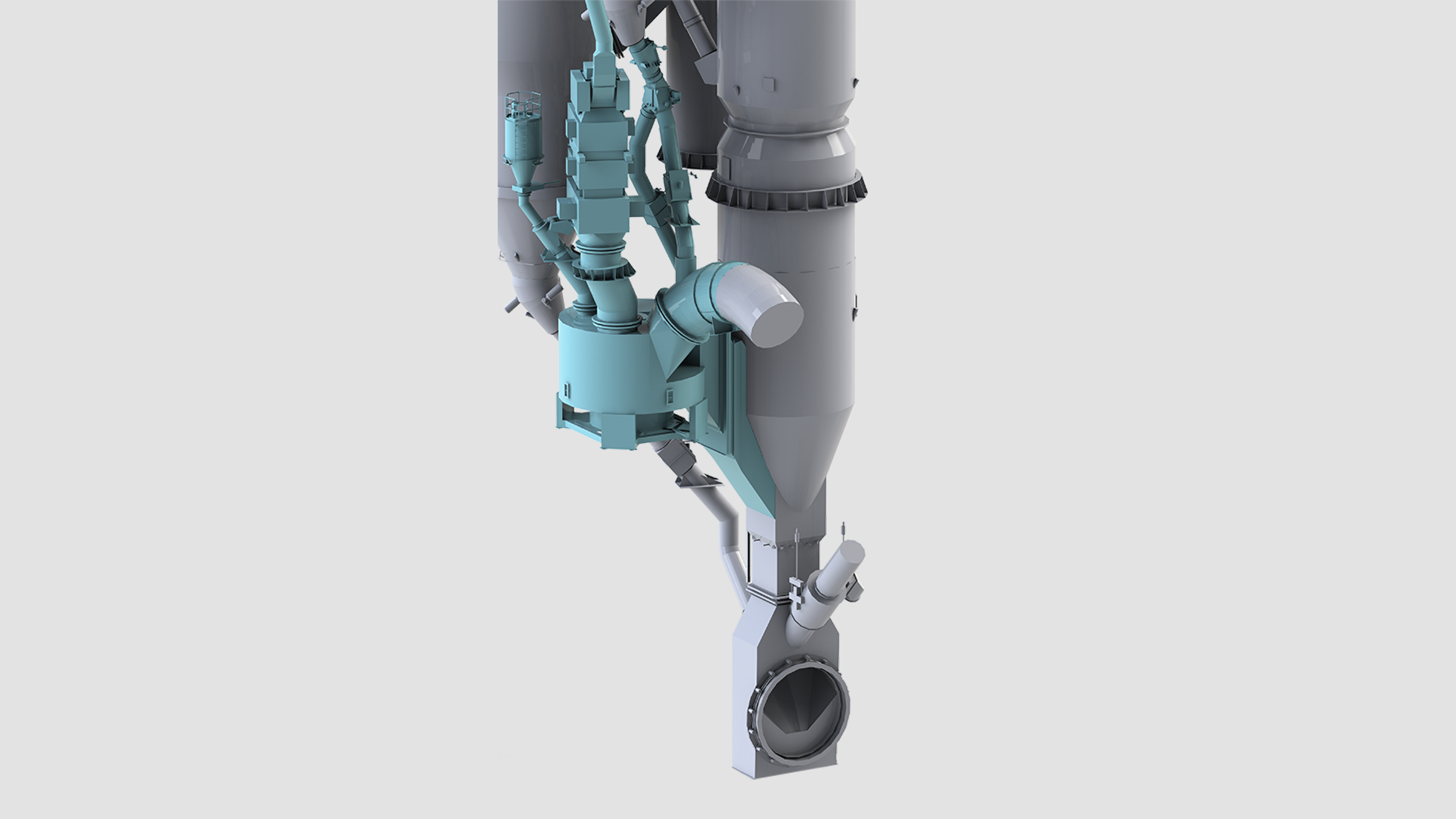
HOTDISC® with HMT
HOTDISC® with HMT (Hot Material Transport)
Introduced in 2021, the HOTDISC w/HMT offers the same functionality and benefits as the traditional HOTDISC, just quicker and easier to install for existing plants. Instead of directly integrating the exit of the HOTDISC reactor to the calciner and riser duct, the new approach to layout allows the HOTDISC reactor to be mounted 2 to 5 meters away. Then, it is connected to the calciner and riser duct via a hot material transport chute for gas flow and combustion ashes.