
Green innovation to drive cement’s green transition.
The transition to carbon neutrality in the cement industry is a multi-stranded mission involving numerous measures and innovative new solutions. It will take time. And effort. But we’re committed to getting the job done. Backed by our dedicated Green Innovation R&D team, we’re here to support your green ambitions.
Paving the way for the green transition
Traditional cement production emits about 850kg of CO2/tonn of cement produced. Getting from there to zero is not straightforward: there are multiple options and routes to travel to reach the destination. We group these various solutions into the following three broad pathways:
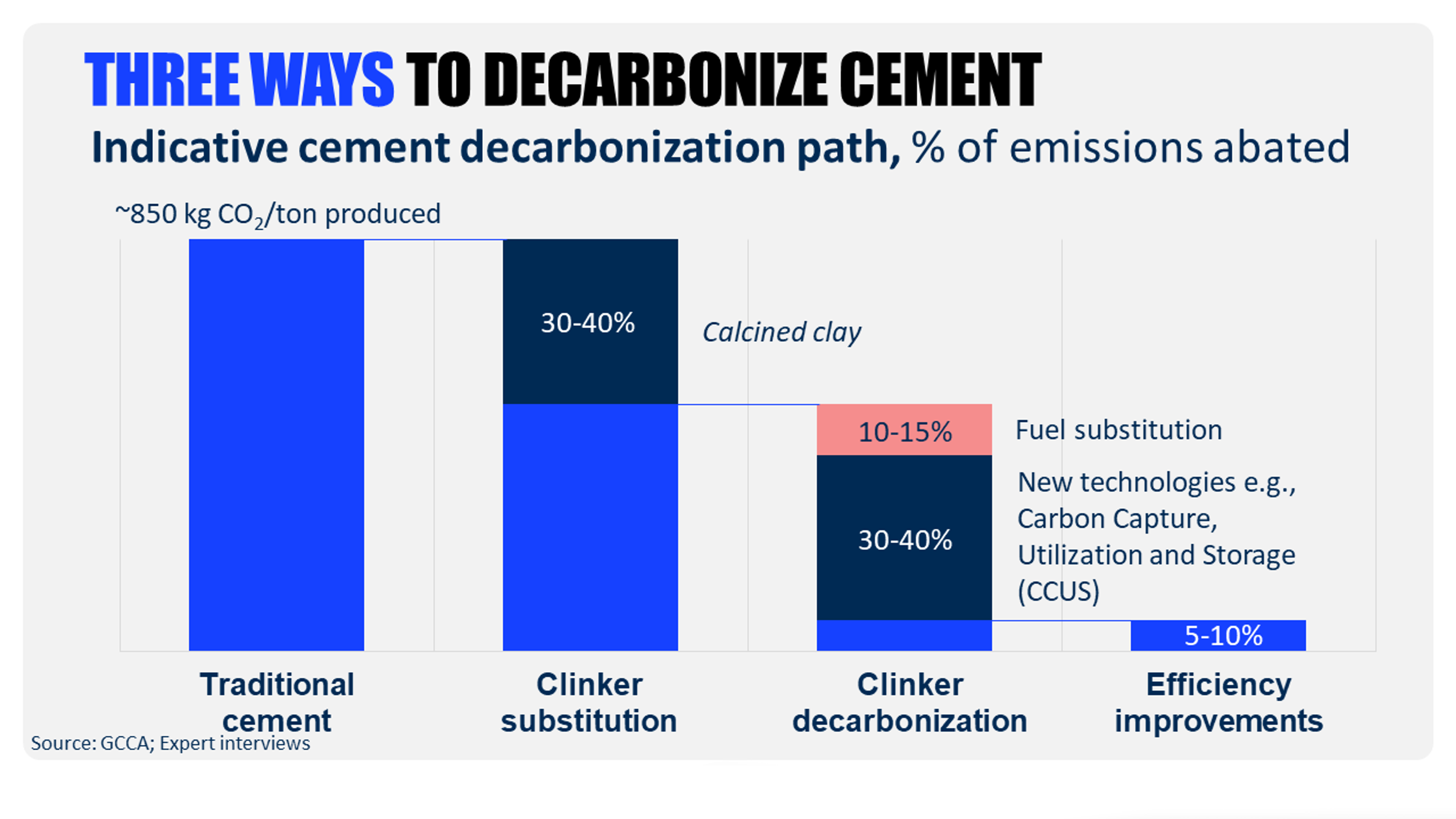
How do we get there?
Innovation has been at the heart of FLSmidth Cement from the very beginning. Since we delivered our first cement plant back in 1887, we have worked to make cement production cleaner, safer, and more efficient. Now, as we face the urgent need to lower manmade carbon emissions, our focus is on developing solutions within these three pathways to support cement producers decarbonize cement production. We already have an extensive portfolio of proven solutions to improve the efficiency and reduce the carbon footprint of cement production.
But we also know there’s still a long way to go. And that’s where our Green Innovation R&D team takes the field. Comprising researchers, engineers, and program/project managers, we collaborate with colleagues throughout the FLSmidth Cement organization to apply their knowledge and experience to the green transition. We also work with external partners to innovate product, technologies and solutions needed to reach zero.
A key part of this is our dedicated partnerships team, which aims to identify external partners that we can collaborate with to generate and incubate ideas and innovations that will help deliver our decarbonization
goals.
What are we doing?
Our Dania test center is one of world’s most advanced laboratories for the analysis of raw materials in cement production, receiving and testing tons of raw materials from all of the world. In 2020, it was reconfigured to support SCM activation and color control testing. State-of-the-art equipment and processes, including R3 tests, XRF/XRD, and thermal analysis, empower leading materials science data collection and analysis. Dania is also the home of our ECoClay™ demonstration plant.
ECoClay
Traditional clay calcination already has a far lower carbon footprint than clinker production: it’s why calcined clay is such an promising SCM. But electrify the process and that benefit is increased significantly. In fact: the ECoClay partnership expects to reduce emissions up to a total of 50% per ton of cement produced.

CO2Valorize
The chemical breakdown of limestone during clinkerization accounts for much of the carbon emissions association with cement production. The CO2Valorize project focuses on this process challenge, investigating the potential for carbonating recycled concrete and mine tailings to produce an alternative to limestone in cement production.
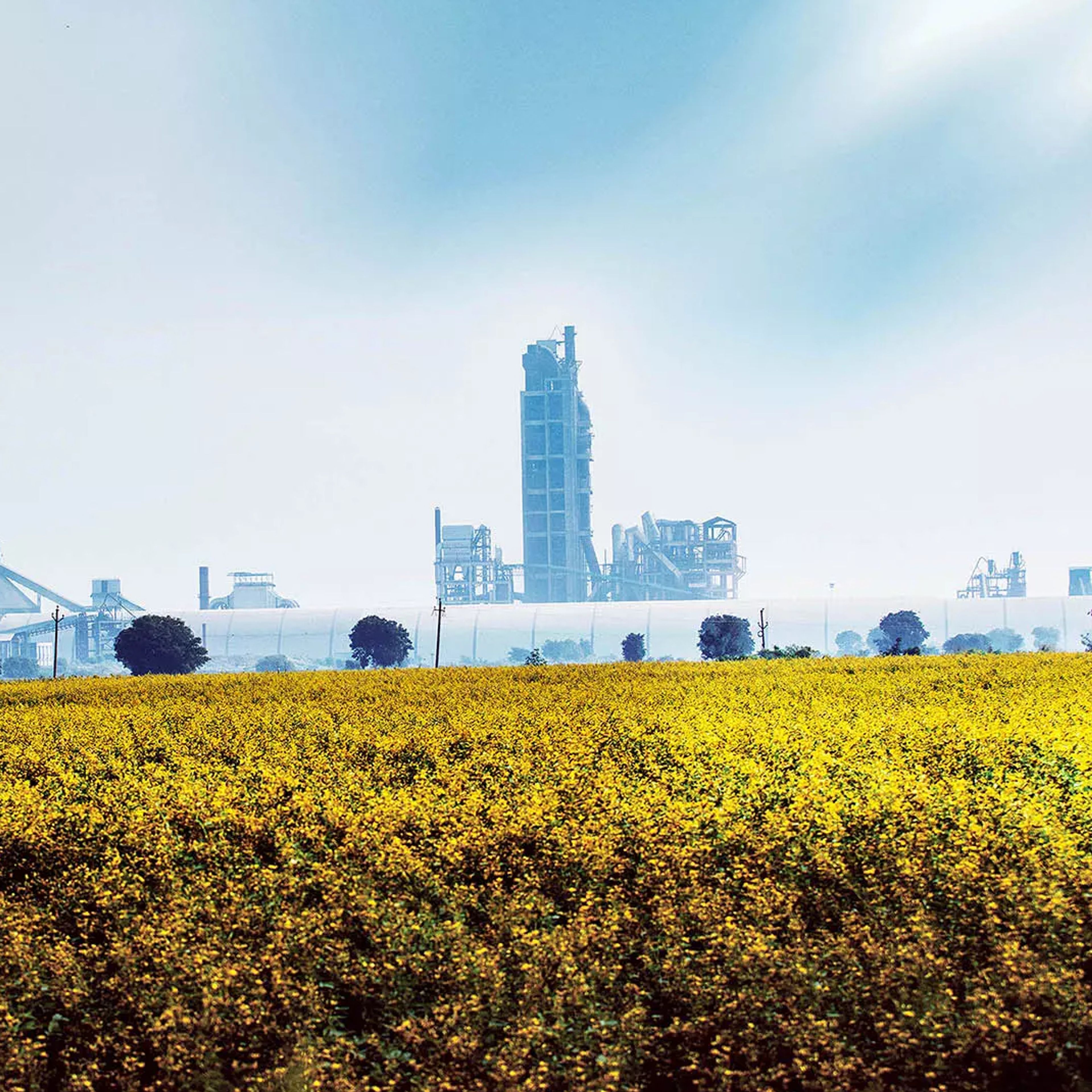
Dania Test Center
Advanced materials testing and analysis - there’s been a test center at Dania in Denmark since 1976. Today, it’s home to one of the world’s most advanced laboratories for the analysis of materials. Dania supports our green innovation work through state-of-the-art testing of supplementary cementitious materials (SCMs) and clays, as well as hosting the ECoClay™ pilot plant.
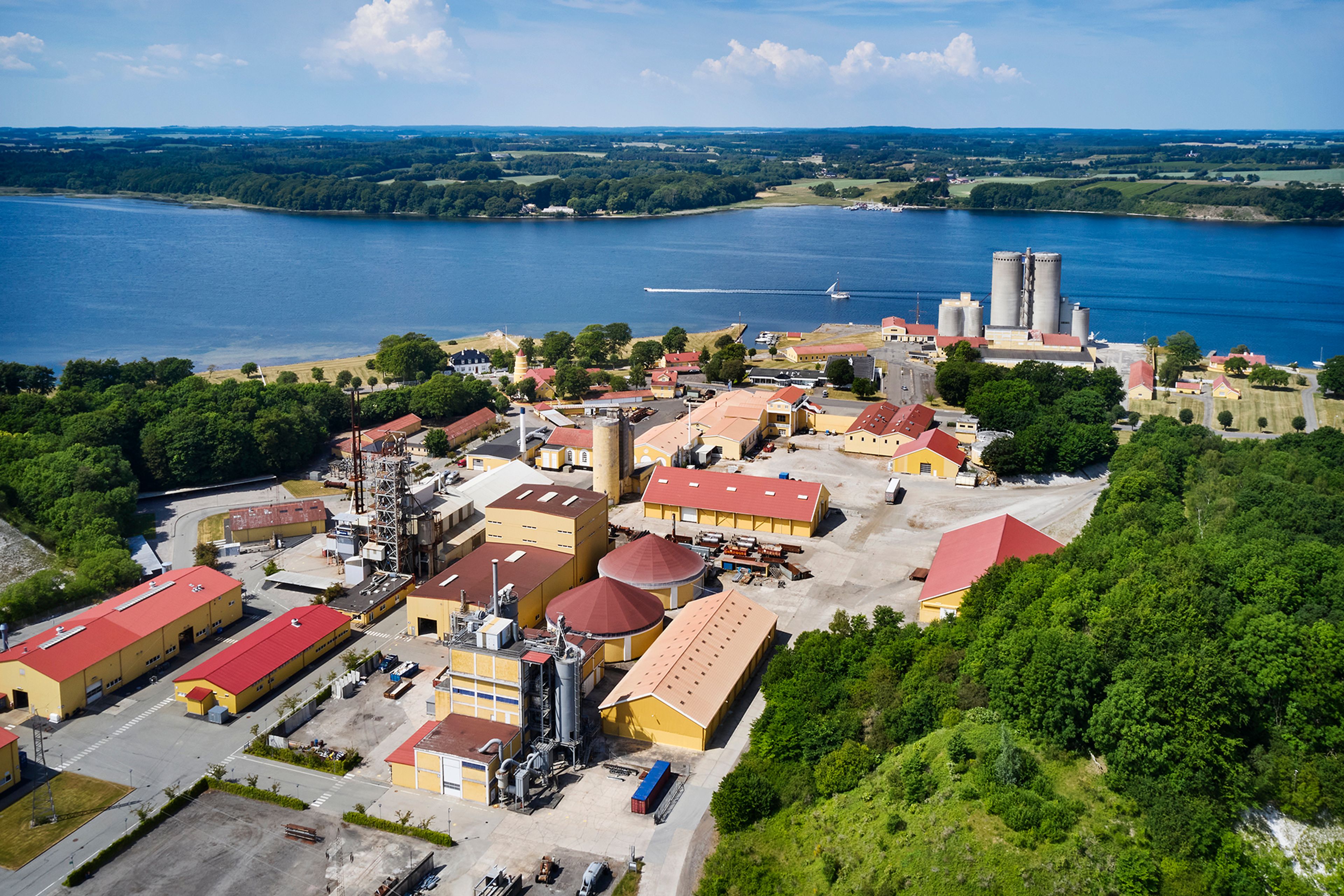