alternative fuels
FUELING CEMENT’S
GREEN TRANSITION
From Waste
to Wow
The use of Alternative fuels are an effective first step towards a more sustainable cement production process. Not only can they significantly lower your environmental footprint, but they also offer the potential to cut fuel costs. However, transitioning to alternative fuels comes with its own set of challenges, such as variability in fuel characteristics and size, storage and dosing and operational risks. The good news is that these obstacles can be overcome with the right expertise and technology. That’s where FLSmidth Cement comes in. With over 140 years of experience in the cement industry and decades of expertise in alternative fuel solutions, we ensure your transition is seamless, impactful, and tailored to your plant’s unique needs.
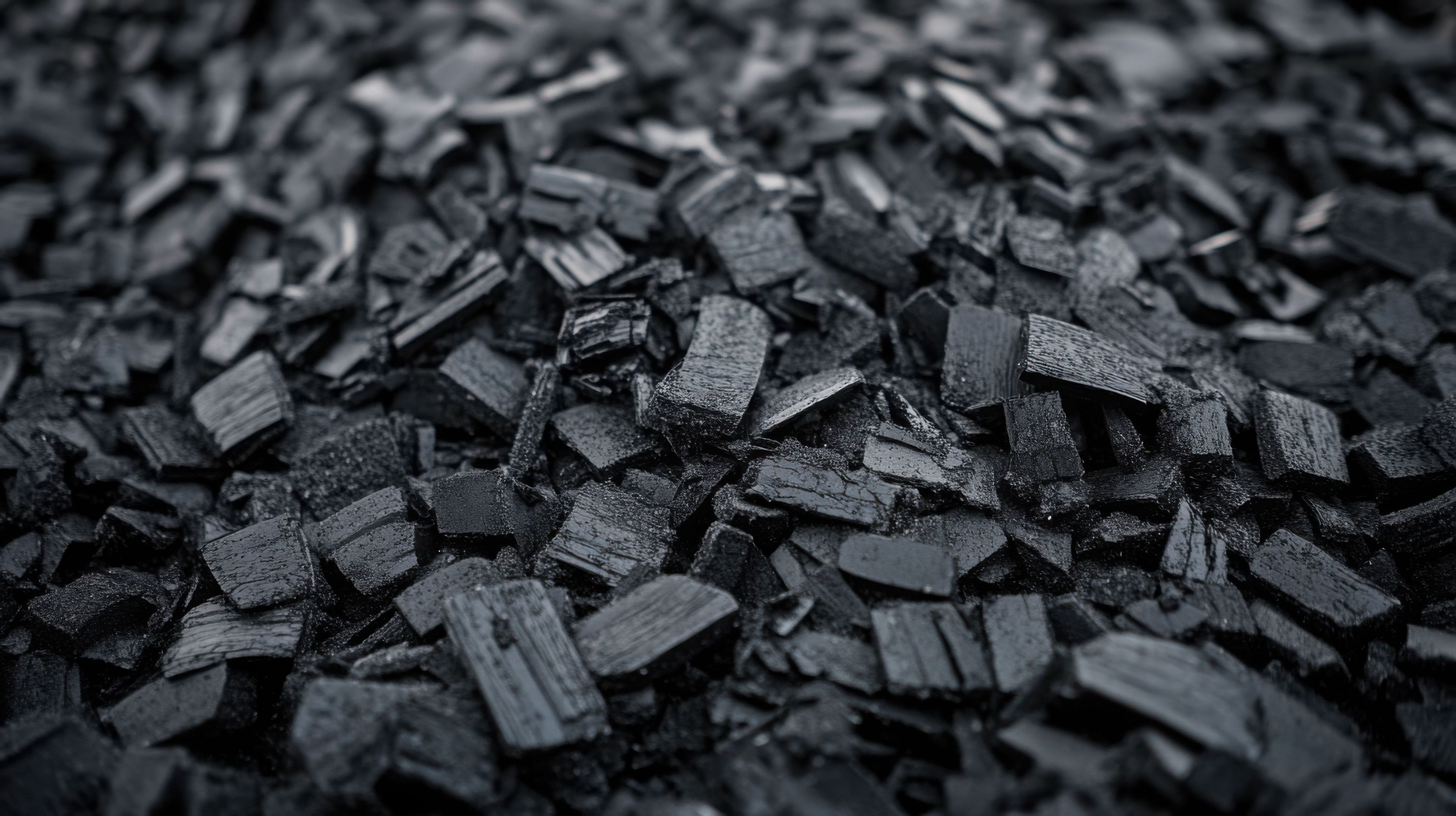
Looks like coal? Good news: it isn't! Shredded tyres.
Most alternative fuels have a larger particle size, higher volatility and moisture contents, and a lower heating value than conventional fossil fuels. These differences pose challenges for efficient use, which is why flexibility is essential from the outset.
Flexibility for FLSmidth Cement means providing the ability to use fuels with varying sizes, characteristics and combustion properties, ensuring your plant operates efficiently no matter the fuel source.
It also means offering tailored solutions that meet your specific needs—whether you’re just starting your journey into alternative fuels or striving to maximize your total substitution rate.
Whatever your ambitions or maturity in alternative fuels, we’re committed to supporting you, ensuring that from fuel delivery to the final clinker, every phase of your process runs smoothly and efficiently.
your needs
Full flowsheet solutions for
proven results.
Our alternative fuels solution portfolio has been developed to work together throughout the cement plant flowsheet in an optimized and harmonious way. While each solution is a performance leader in its own right, the maximized value comes by using the portfolio of solutions in combination. That’s why we work closely with customers to understand how and in what combination our solutions can deliver the best results for them.
1 | Waste sourcing
A variety of different waste is collected and transported to one or more locations for pre-treatment.
2 | Waste preparation
A complex process of shredding, sorting, drying and sizing, converting the waste to different fuel qualities.
3 | Material handling and storage
The fuels are transported, stored and if necessary, dried to become part of the fuel mix.
4 | Dosing
The extracted fuel is accurately dosed to meet the pyro process requirements.
5 | Pyro processing
The alternative fuel enters the calciner or main burner where it substitutes coal or other fossil fuels.
6 | Clinker cooler
Designed to give you reliable long-term performance, our range of clinker coolers deliver efficient heat recuperation and high uptime.
7 | Process and quality control
Ensuring clinker quality, enabling the control system to compensate and optimise the fuel mix.
1 | Waste sourcing
A variety of different waste is collected and transported to one or more locations for pre-treatment.
2 | Waste preparation
A complex process of shredding, sorting, drying and sizing, converting the waste to different fuel qualities.
3 | Material handling and storage
The fuels are transported, stored and if necessary, dried to become part of the fuel mix.
4 | Dosing
The extracted fuel is accurately dosed to meet the pyro process requirements.
5 | Pyro processing
The alternative fuel enters the calciner or main burner where it substitutes coal or other fossil fuels.
6 | Clinker cooler
Designed to give you reliable long-term performance, our range of clinker coolers deliver efficient heat recuperation and high uptime.
7 | Process and quality control
Ensuring clinker quality, enabling the control system to compensate and optimise the fuel mix.
SUPPORTING YOUR PATH TO GREENER CEMENT.
EVERY STEP OF THE WAY.
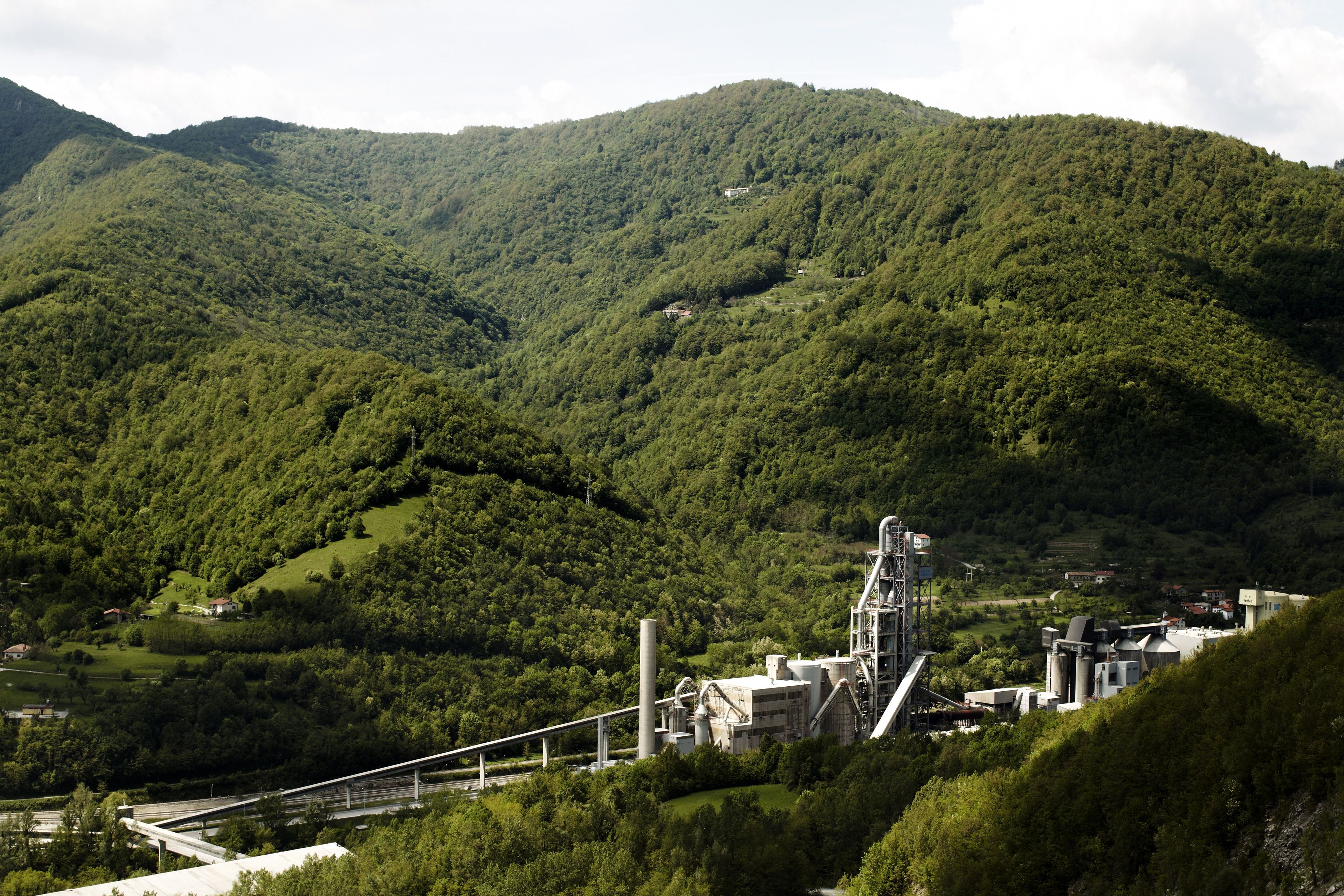
Comprehensive planning meets ongoing service
We’re here to make your transition as seamless and stress-free as possible. From detailed planning and tailored strategies to installation and commissioning, we optimize your system for peak efficiency and performance. Once installed, our expert service team/support team is here to provide ongoing maintenance, monitoring, and process optimization, ensuring your equipment runs smoothly and delivers lasting value.
With FLSmidth Cement, you're not just investing in innovative technology—you're gaining a trusted partner for every step of the way.