JETFLEX 2.0 – a burner to solve the alternative fuels challenge

What we offer
The latest evolution in cement kiln burner technology
Our JETFLEX 2.0 cement kiln burners offer a high degree of fuel flexibility. Use pulverised coal or petcoke, anthracite, oil, natural gas – or any mixture of these – as well as alternative fuels (such as plastic and wood chips, sewage sludge). The results are the same. Switching from fossil fuels to more environmentally-friendly alternative fuels is one of the easiest ways to reduce carbon emissions associated with cement production. Yet high thermal substation rates can pose a challenge to process stability and impact plant productivity. No longer. Our JETFLEX 2.0 burners deliver optimum flame shaping and lowest NOx emissions, whatever your fuel mix. And with capacities available up to 250MW, we can cater to even the largest of rotary kilns. The latest JETFLEX 2.0 design offers an upgrade to our original JETFLEX burners with features including:
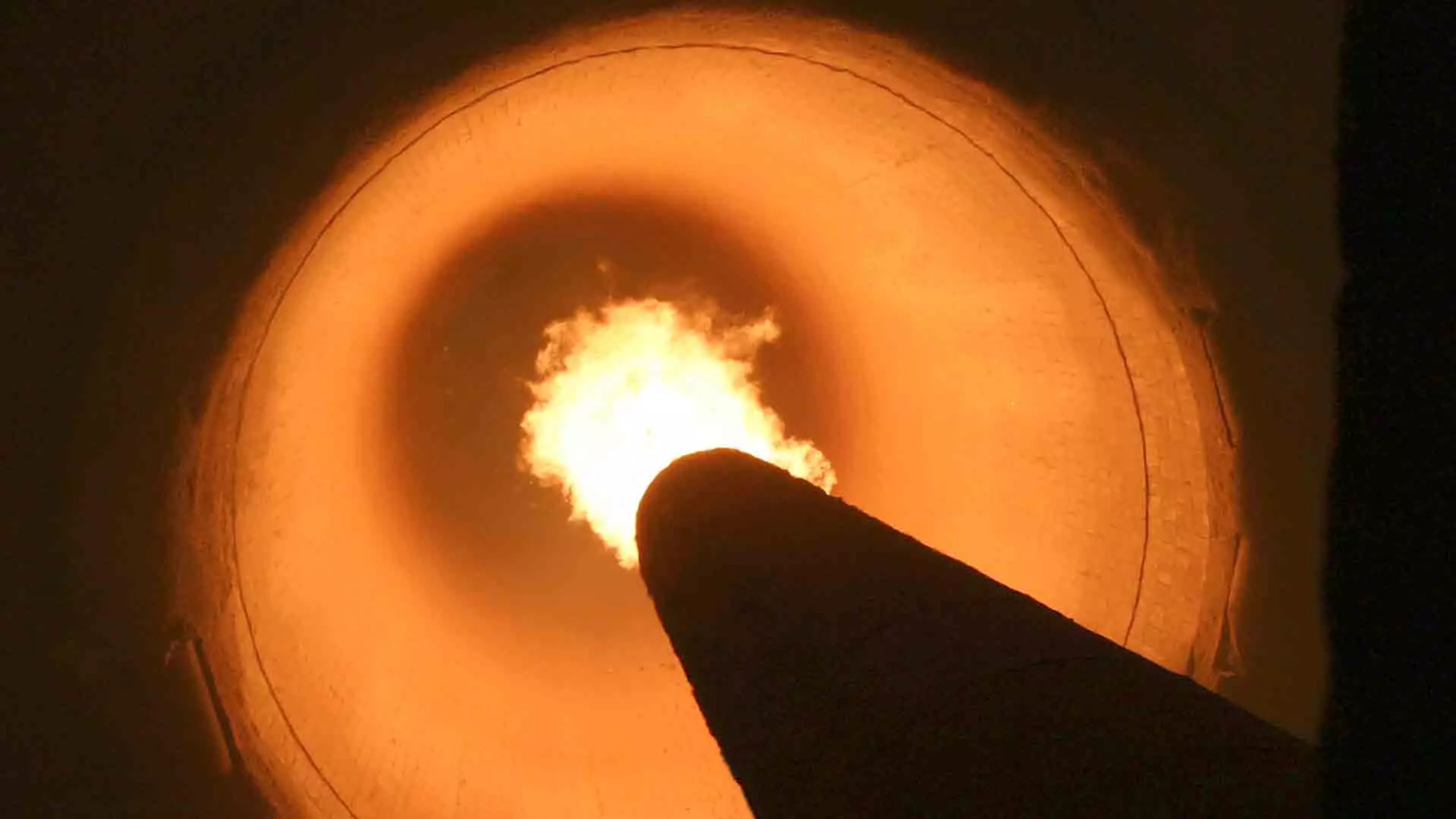
Improved expansion joint
The improved expansion joint for guiding fuel injection pipes ensures accurate control of thermal elongation during operation.
Stronger front plate as a single unit
The front plate has been strengthened to extend operating life and comes as a single unit to facilitate swift replacement.
Optimal ignition and flame formation
Flame formation is controlled by separate systems for axial and swirl air, ensuring fast ignition and stable flame formation with a shorter and more-intense flame.
Greater fuel efficiency
The JETFLEX 2.0 enables solid fuels to be injected via a common fuel injection pipe, reducing cold airflow and so improving heat and power consumption.
Stable firing process
The JETFLEX 2.0 is available in the same two models as the original JETFLEX burners: a standard JETFLEX 2.0 burner and the JETFLEX 2.0 PLUS burner. Both designs are optimised for reduced container shipment cost and time, as the design incorporates a simplified structure with a detachable beam and reduced overall length.
Firing alternative fuels – without the compromise
Developments in kiln burner design are an essential part of global efforts to raise the use of alternative fuels within the cement industry. JETFLEX 2.0 burners are at the cutting edge of this movement, helping make high alternative fuel substitution rates a practical reality.
Increase fuel substation rates
Alternative fuels replace carbon-intensive fossil fuels, and are thus integral to achieving carbon emissions reduction in the cement industry. Increasing the use of alternative fuels can also help improve fuel security and cost stability, as it reduces dependency on globalised fossil fuel supply chains.
Efficient operation reduces energy consumption
An improved nozzle design makes it possible to reduce primary air percentage, while lower pressure drop across the solid fuel injection pipe saves conveying airflow compared to traditional burner design. Both reduce the burner’s energy requirements, improving OPEX and reducing power-related emissions.
High clinker quality, reliable and low-maintenance operation
The benefit of a good flame cannot be underestimated: it is felt along the complete pyroprocess. By minimising volatility in the kiln, it ensures reliable and consistent production of high quality clinker, with reduced maintenance, increased productivity, and lower OPEX. It’s just better – and means can worry about other things.
Low NOx emissions
We utilise a well-established principle of flame formation whereby a fuel-rich flame core is then surrounded by the flame-shaping primary air. Combined with a short ignition distance and a compact flame, this minimizes thermal NOx generation, reducing NOX emissions from the pyroprocess.