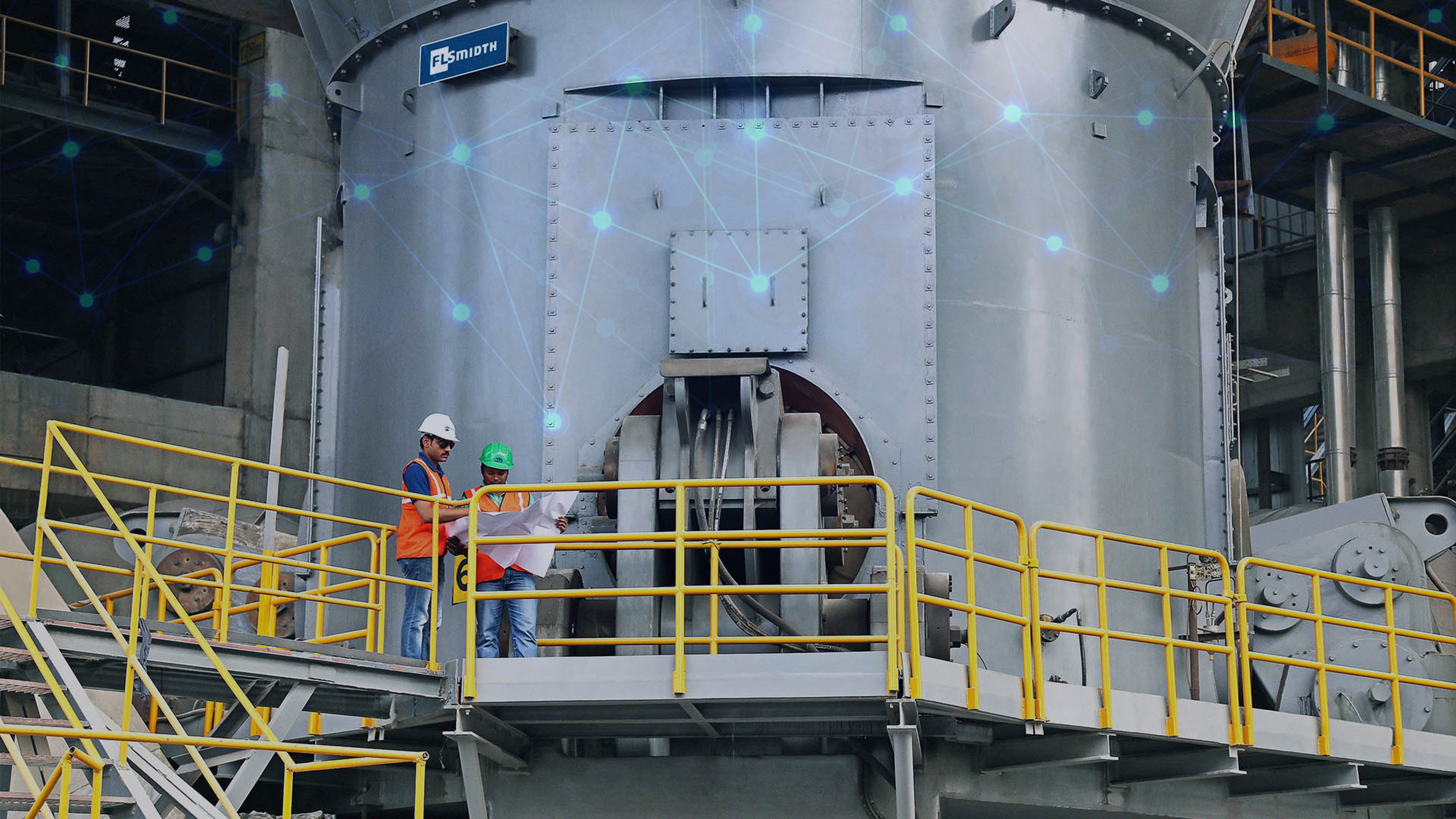
Proactive maintenance strategy to eliminate unexpected downtime
Key benefits
- Minimise unplanned stoppages
- Minimise secondary damage to equipment
- Increase equipment lifetime, reliability and performance
- Lower OPEX and more productivity
- Achieve more sustainable operations
Sustain maximum mill performance
This service helps detect early symptoms that can’t be detected by regular on-site
maintenance alone. Standard sensors on the mill monitor, for example, gas flow pressure and temperature, and hydraulic grinding pressure. With continuous monitoring, you can ensure these parameters are all consistently maintained, giving you plenty of time to take planned action before problems become severe.
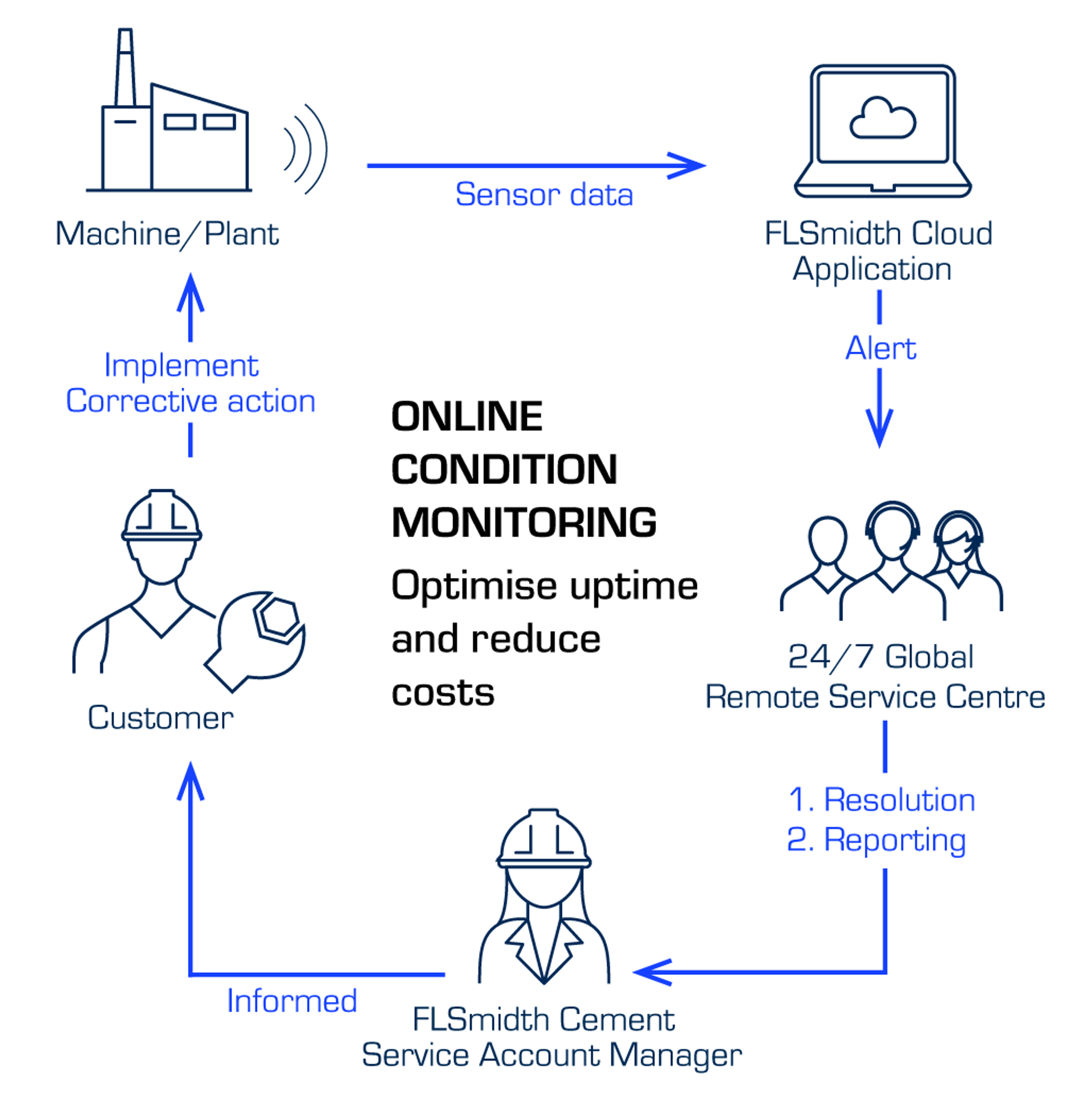
Optimise uptime and reduce costs
Signals from the monitors are sent to the cloud for analysis. Experts at our Global Remote Service Centre are notified of all alarms/events, enabling them to further analyse the data and generate a report detailing our recommendations for corrective actions. Your Service Account Manager will keep you informed at all times, ensuring you have plenty of time to carry out our recommendations and avoid further problems. All our service packages can be tailored to your needs.
Optimise uptime and reduce costs
Our specialists interpret the data and give you qualified analysis and expert recommendations for a healthy, optimised mill system.
What?
Continuous OK mill health monitoring and incident support; regular reports summarizing alarms and recommendations; clear, actionable insights that you can implement to reduce operating costs and optimise performance.
Outcome
This means you can predict potential problems in critical components or subsystems in the mill circuit and prevent them from negatively impacting overall mill operation.
Case
The early onset of instability in grinding pressure caused by cylinder seal leaks was detected by this service before the more severe symptoms of lost production or product quality were seen. Replacing a piston seal during a planned maintenance schedule ensured regular production was maintained.
With Level 1 service, we monitor:
- Operating conditions
- Mill air circuit
- Mill fan efficiency
- Grinding hydraulic system
- Roller and table wear liner life
- Separator top seal
With Level II service, we monitor all of Level 1 plus
- Roller position and speed
- Mechanical stopper impact
- Bearing temperatures
- High resolution gear and bearing vibrations
- Lubrication oil pressure and flow
- Input torque on mill gears
- Table wobbling and tilting on mill gears