Reliable and trusted plant sampling and sample transport
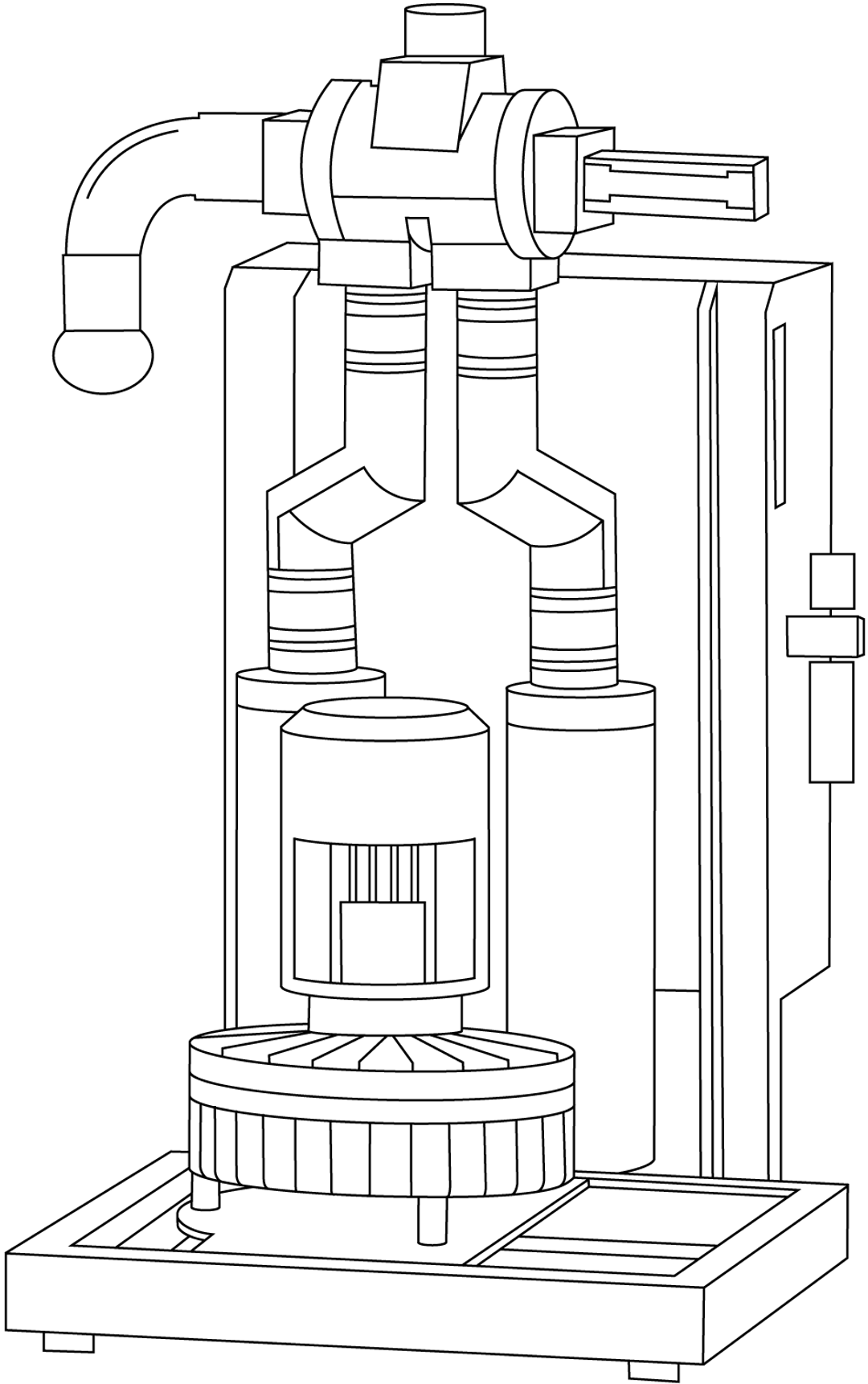
What we offer
A fully integrated automated system from process sampling point to laboratory
Our automated sample transport network links our reliable sampling equipment to our robotic laboratory cells. We have been actively involved in developing tube transport systems, which have been employed for fast sample transportation in harsh industrial environments, since the 1960s. Our market-leading position is solid within this technology through the execution of hundreds of projects with automated sampling and sample transportation to customers worldwide. The QCX/AutoSampling™ software is very user-friendly – the solution is highly flexible with well-designed user interfaces that provide an unmatched overview of the complete automated sampler-to-laboratory system.
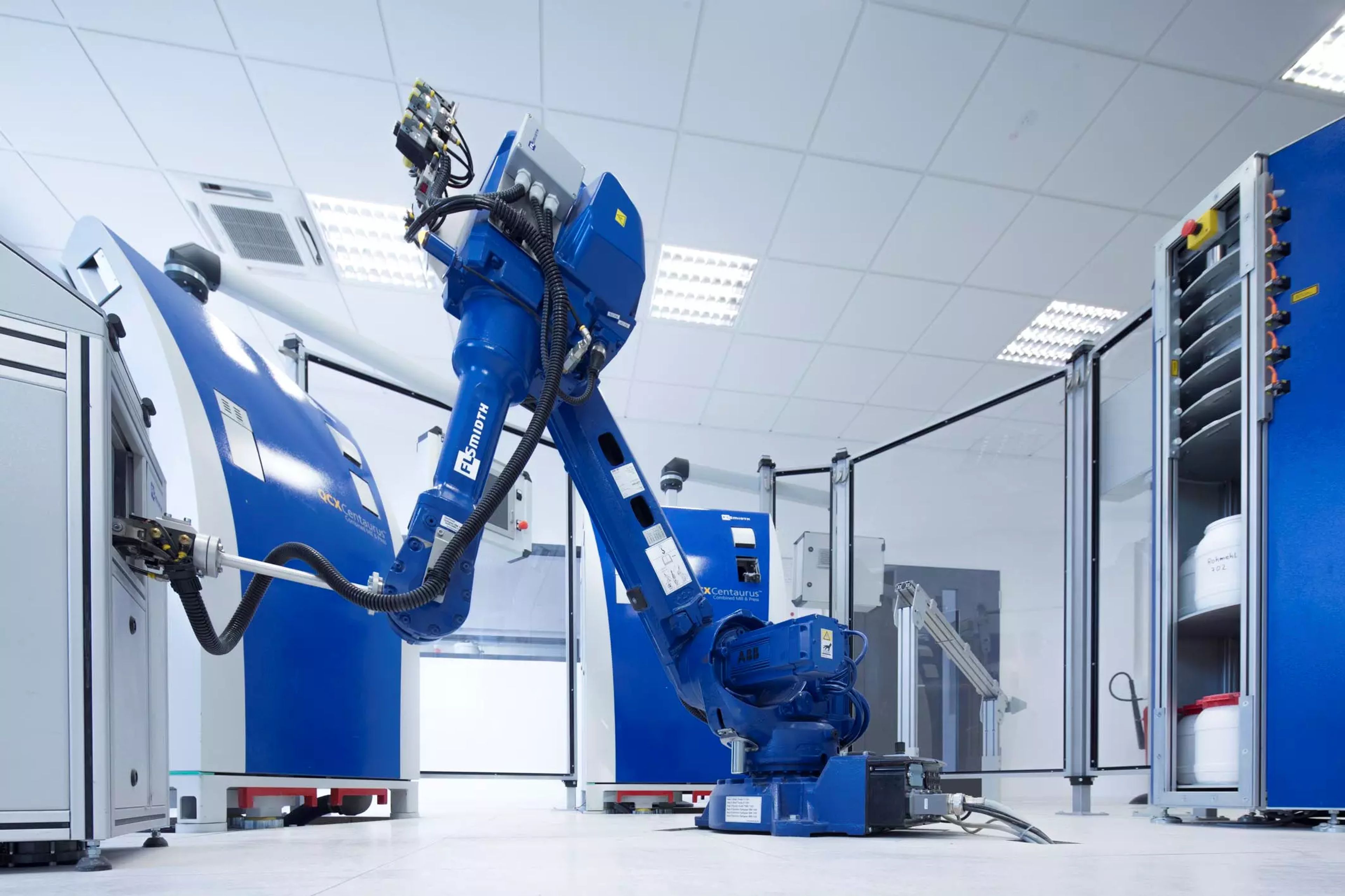
Get the right sample to the laboratory faster and keep your quality under tight leash
Balancing your cement plant’s chemistry can be challenging. Sampling inconsistency and inaccurate analysis results contribute to laboratory errors. These errors create process fluctuations and disrupt productivity, reducing equipment life while jeopardising product quality.
Automated sampling results in samples being taken at the right time, at the right place and consistently. It’s a safe choice. Fast turnaround time from sampling to analysis: the fast, fully integrated system is cost-efficient and reliable, giving you maximum return on investment.
Improved product quality and related operational savings
Sample traceability and improved quality control: samples are sent from the process stations to receive/send stations in the laboratory in accordance with individual sample priorities and waitlist status. Sample entities such as sampling location, product type, sampling time etc. are automatically passed on to the next handling stage, whether manual or automatic.
Less labour requirements: the systems require minimal human intervention, leaving your workers free to take on other tasks.
Improved worker safety: sampling is often done in hot and dusty environments. Sampling for hot meal often happens every 2 to 4 hours in the cyclone where the material temperature exceeds 800 degrees C. Manual clinker sampling and hot meal sampling can also expose workers to hazardous environments. Does the frequency and quality of your sample taking diminish due to these difficult work conditions? This may have a negative impact on the quality of the final product and the productivity of your plant.
Sampling made easy
QCX® AutoSampling controls the sampling and pneumatic transport – via a tube transport system – of sampled material from the process areas to a central production laboratory or to designated “satellite” laboratories.
Manual, semi-automatic or fully automated send/receive stations are available both at the process end and the laboratory end of a pneumatic sample transport system. Automated sampling equipment for powder, granulate and/or lumpy materials can be connected to the process send/receive stations, thereby ensuring fully automated systems.
A typical project scope may comprise of:
Automated sampling equipment
Process send/receive stations
Laboratory send/receive stations
Transport tube and tube diverters
Transport air blowers
Project-specific control hardware and software
Optional sample ID entry terminals
QCX/AutoSampling™ supervisory software
Project engineering services
Factory acceptance testing Installation supervision and commission services
Samples are transported in sample cartridges (or carriers or shuttles). For dry powder/granulates, typically 250 or 500 cc material is sent to the laboratory. Send/receive stations – in the process area or in the laboratory – may be manually serviced or fully automated, which, at the process end, means full automation of the entire sampling and sample transport process.
The sampling and transport system is controlled from built-in control components undertaking the equipment device control and a central QCX/AutoSampling PC/PLC system which handles the coordinated traffic control, sample identification, sampling schedules, transport priorities, visualisation, alarms etc.
You can be sure that our automated sample transport equipment and associated QCX/AutoSampling software system will result in quality optimisation through the complete sampling process in the cement plant. It can be seamlessly configured to suit your work processes, and most importantly, delivers reliable data.