Energy efficient gas compression technology
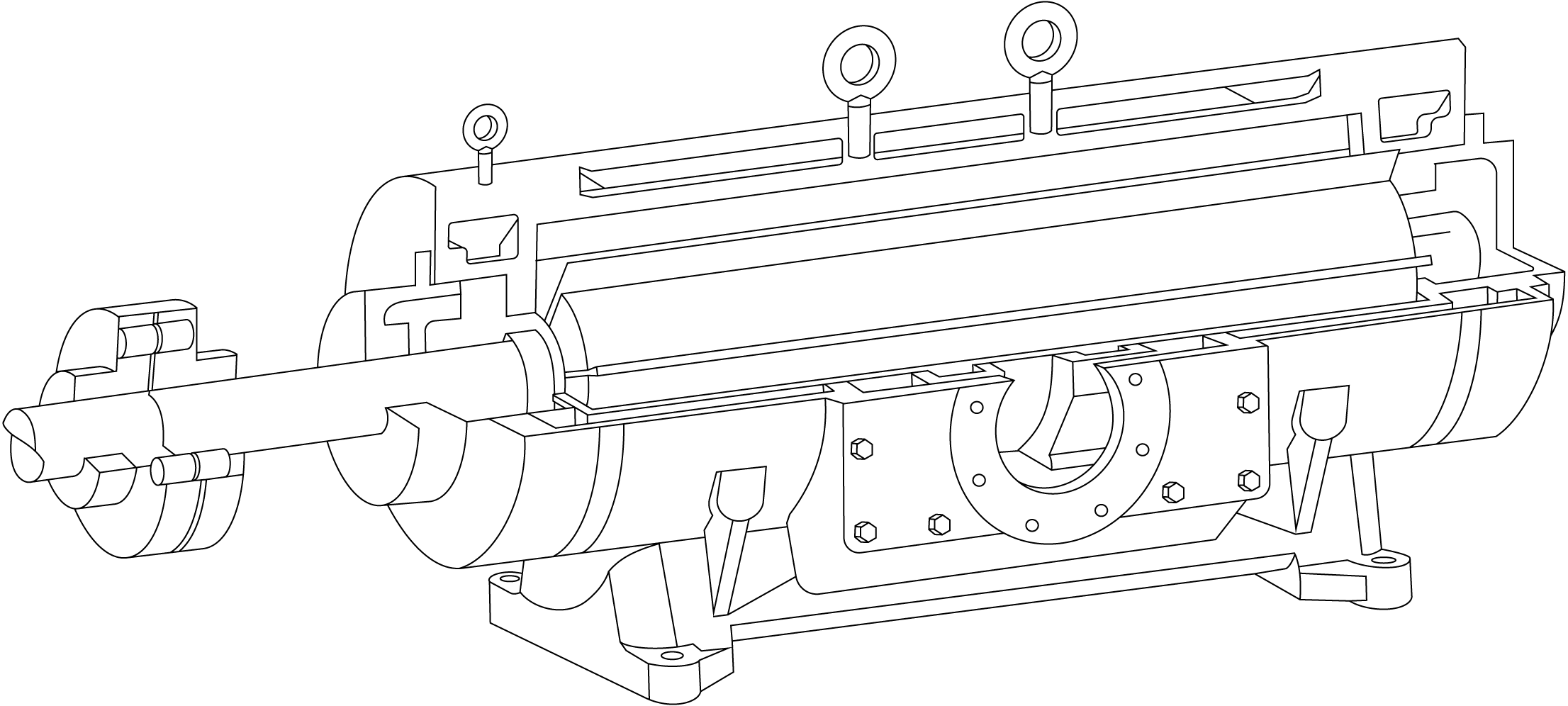_Rotary_Vane_Gas_Compressor.png?w=1080&q=80&auto=format)
What we offer
Rotary vane gas compressors and vapour recovery for the oil and gas industry
Your energy bill is a major component of your operational costs. That’s why we’ve focused on minimising energy consumption and maximising compressed gas in the design of Ful-Vane™ Gas Compressors. By minimising the number of moving parts, we have reduced the potential for mechanical losses, while the shaft and bearing design minimises drive losses. Constant blade-to-cylinder contact maintains compression efficiency, while the large inlet area efficiently captures large gas flows. And it’s a flexible system. You can operate it with a variable frequency drive, and we can customise a complete solution to your project specifications or offer a standard range of single-stage and two-stage sizes.
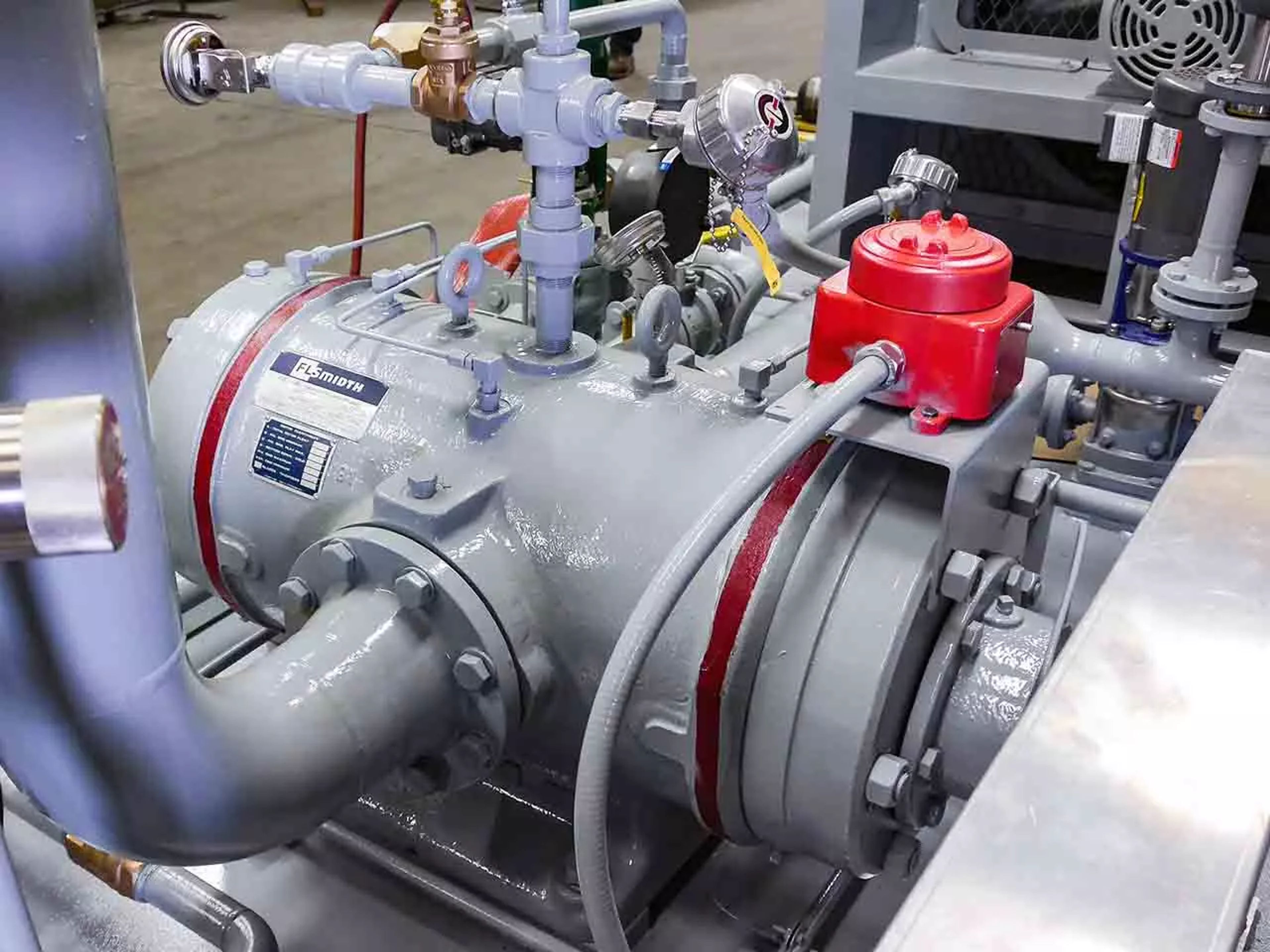
More compressed gas, less energy consumption
Developed from Fuller® design and technology, our Ful-Vane™ Gas Compressors provide more compression using less energy. The success of these systems comes down to the logical engineering, which focuses on areas where energy is typically lost and minimises those losses:
minimal losses
Only three moving parts for minimal mechanical losses. Shaft and bearing design minimises drive losses.
Efficiency
Constant blade-to-cylinder contact maintains compression efficiency
Easy maintenance
We’ve also made sure these compressors are built to last. The minimal, easy maintenance can be carried out in the field, saving time and money.
Ful-Vane™ Gas Compressors, customised to your application
Wear-resistant
Internally, carbon fiber vanes ride on a thin layer of lubricant to provide positive sealing for each compression chamber. Since the vanes compensate for wear, the compressor maintains its design efficiency over time.
Low-maintenance
The Ful-Vane Ammonia Gas compressor boasts a simple design that is easily field repairable. Ful-Vane compressors also feature rebuildable housings and rotors. Rather than being replaced, the inner cylinder can be re-bored numerous times, and the rotor can be reslotted up to three times. This means the compressor can be easily rebuilt to factory specs several times over its lifespan. This greatly reduces the long-term cost of ownership.