Reliable rotary valves for pneumatic conveying
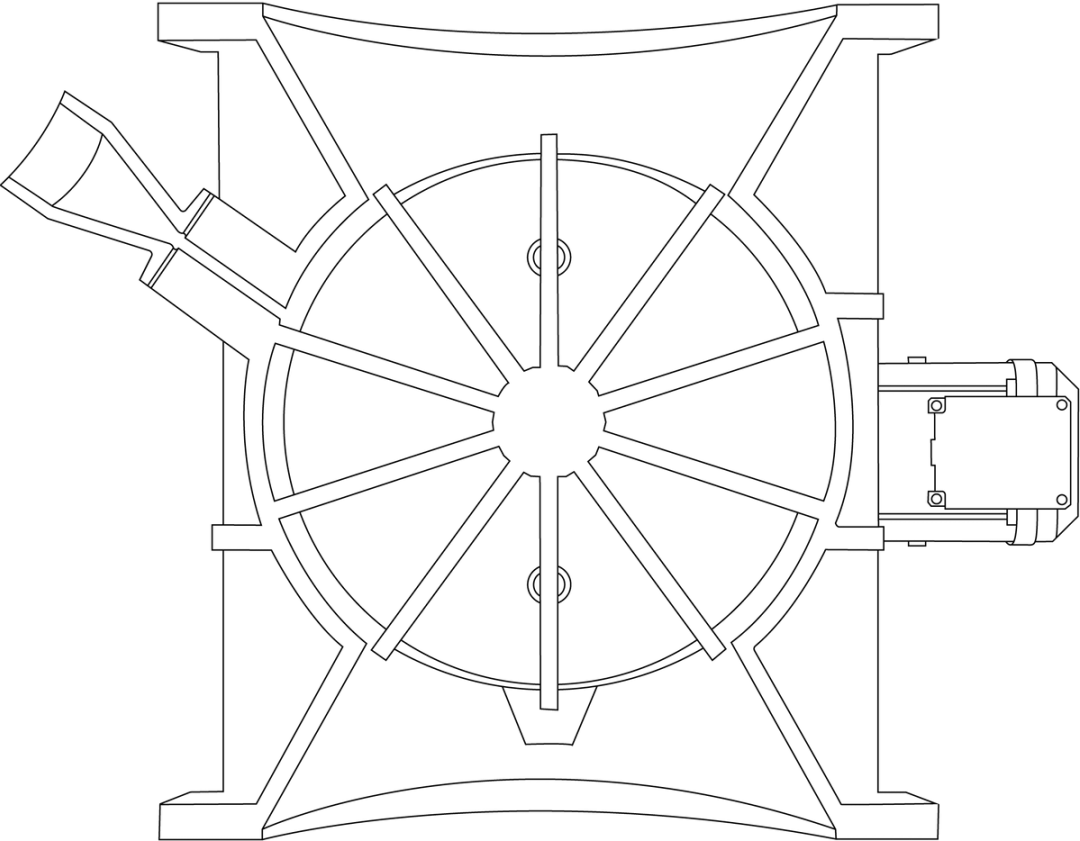
What we offer
Rotary valves for pneumatic conveying
Our range of rotary valves is designed for use in all industrial areas in which powdery bulk materials are processed, conveyed, stored, distributed, weighed or metered. Our metric series feeders / rotary airlocks combine many essential features in a single unit, helping to maximise the performance and dependability of a pneumatic conveying system. The metric series will handle materials in either vacuum or pressure conveying systems. If you need to feed pneumatic conveying systems efficiently and at high-pressure differentials up to 29 psig (2 bar), choose FLSmidth’s V-Series rotary airlock. The V-Series feeder handles dry, fine powder or granular product in vacuum or pressure conveying systems. FLSmidth "TE" (Totally Enclosed) feeders / rotary airlocks are designed to meter dry, pulverized or granular materials, or to serve as airlocks for pressure and vacuum pneumatic conveying systems. These feeders are available in capacity ranges to meet most plant requirements for vacuum, pressure and general-purpose applications.
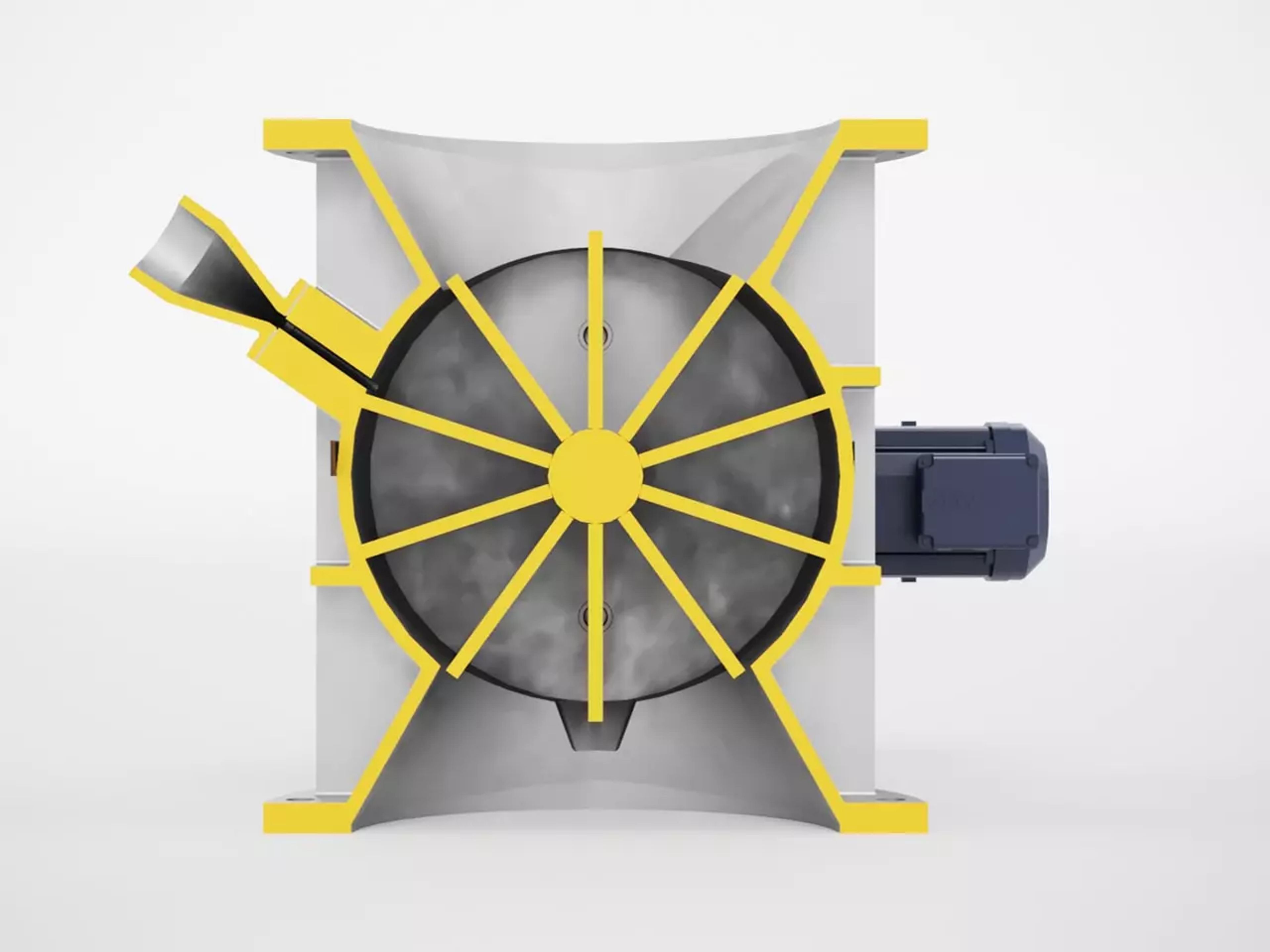
All our rotary valves are designed for long service life and high reliability.
Metric Series Feeder / rotary airlock
Rugged construction and ribbed for dimensional stability; Can be furnished with either closed- or open-end rotor; Smooth operation; Length can be extended if required; Efficient sealing
V-Series Feeder
Designed to minimise slip leakage; Pressurised air is vented out, ensuring even material flow; Mechanical lip-type bronze labyrinth seals minimise air leakage; Severe duty drive system with VFD; NFPA and ATEX rated
TE Feeder/Rotary Airlock
More than 70 years history; Suitable for vacuum, pressure and general-purpose applications; Range of capacities to meet most plant requirements; Heavy-duty cast iron construction, ribbed for stability; Compact, low-wear design
Cutting-edge rotary valve design backed by decades of experience
Metric Series Feeder / rotary airlock
The metric feeder is built to last and designed to adapt to your application. You can choose either a closed or open-ended rotor, an optional port to extend the length of the body, and a range of sizes to suit your needs. All standard feeders are designed to handle material in conveying systems that operate up to a maximum pressure differential of 5 psig (1.05 Kg/cm2). The throat inlet is angled to induce a shearing action, which gives you a smoother operation. The inlet flange easily adapts to a square or a standard 125 Ib ASA flange on Models 150, 300, 700. All rotors have eight vanes with a minimum of four vanes sealing at all times to minimise leakage. Rotors can be furnished with bevelled blades and hard-coated tips as required, giving you optimum wear protection. Efficient sealing is a priority, and to that end we’ve equipped the metric feeder with two lip seals and two lantern rings, or three rows of packing and one lantern ring per end plate. Pipe taps are provided for the air purge and lubrication of the lip seals. Lantern rings, lip seals and outboard sealed bearings are fitted as standard. In order to keep this solution compact, motor support lugs are cast as an integral part of the feeder body to permit the mounting of a gear motor directly on the unit. All integral horsepower gear motors are TEFC, 1.15 Service Factor, Class “F” insulation and corrosion-resistant. All standard gear motors are 230/460 volt, 3-phase, 60 Hz. Standard drives are roller chain with OSHA approved guards. Oil bath guards are also available.
V-Series Feeder
This 10-vane open or closed end rotor minimises slip leakage while efficiently feeding through large inlet and outlet openings. The inlet flange has an inverted integrally cast plow for deflecting granular material. Pressurised air from the pockets is vented through a vent connection, keeping the air out of the inlet flange and maintaining even material flow. The rotor shaft seals minimise air leakage with mechanical lip-type bronze labyrinth seals. The bearings are sealed deep ball bearings that provide very tight peripheral and end clearances. Connections for air purge seal protection are provided with single solenoid and pressure regulator. The drive system includes a direct mounted right-angle bevel gear motor, TEFC, severe duty with integral variable speed drive (VFD) for modulating speeds of 30 rpm to 6 rpm. The V-Series feeder is both NFPA and ATEX rated and is available in six sizes: V200 to V600.
TE Feeder/Rotary Airlock
The TE (Totally Enclosed) line of rotary feeders is a legacy product, having been in the industries we serve for over 70 years. This robust product line features an open-ended rotor for handling most dry bulk powders and granular product. It is available with circular or rectangular flanges and volumes from .26 cu.ft /rev to 5.2 cu.ft/rev. This line is applicable for cement, minerals and power industries. The body and end plates are heavily ribbed and constructed of #50 cast iron, as are the rotors. Motor support lugs are cast as an integral part of the body and permit the mounting of the gear motor directly on the unit, resulting in a compact package. The end plates have integral cast outboard bearing supports and male-female joints between end plates and feeder body ensuring concentricity. All rotors have six or eight vanes with four vanes in seal between inlet and outlet, except for the 2 in. totally enclosed feeder, which has four vanes. The rotor shaft has a tapered hub to reduce friction from trapped material between rotor and end plates. Anti-friction bearings are shielded and mounted on the rotor shaft outboard of the packing gland.