Burn more alternative fuels, more efficiently
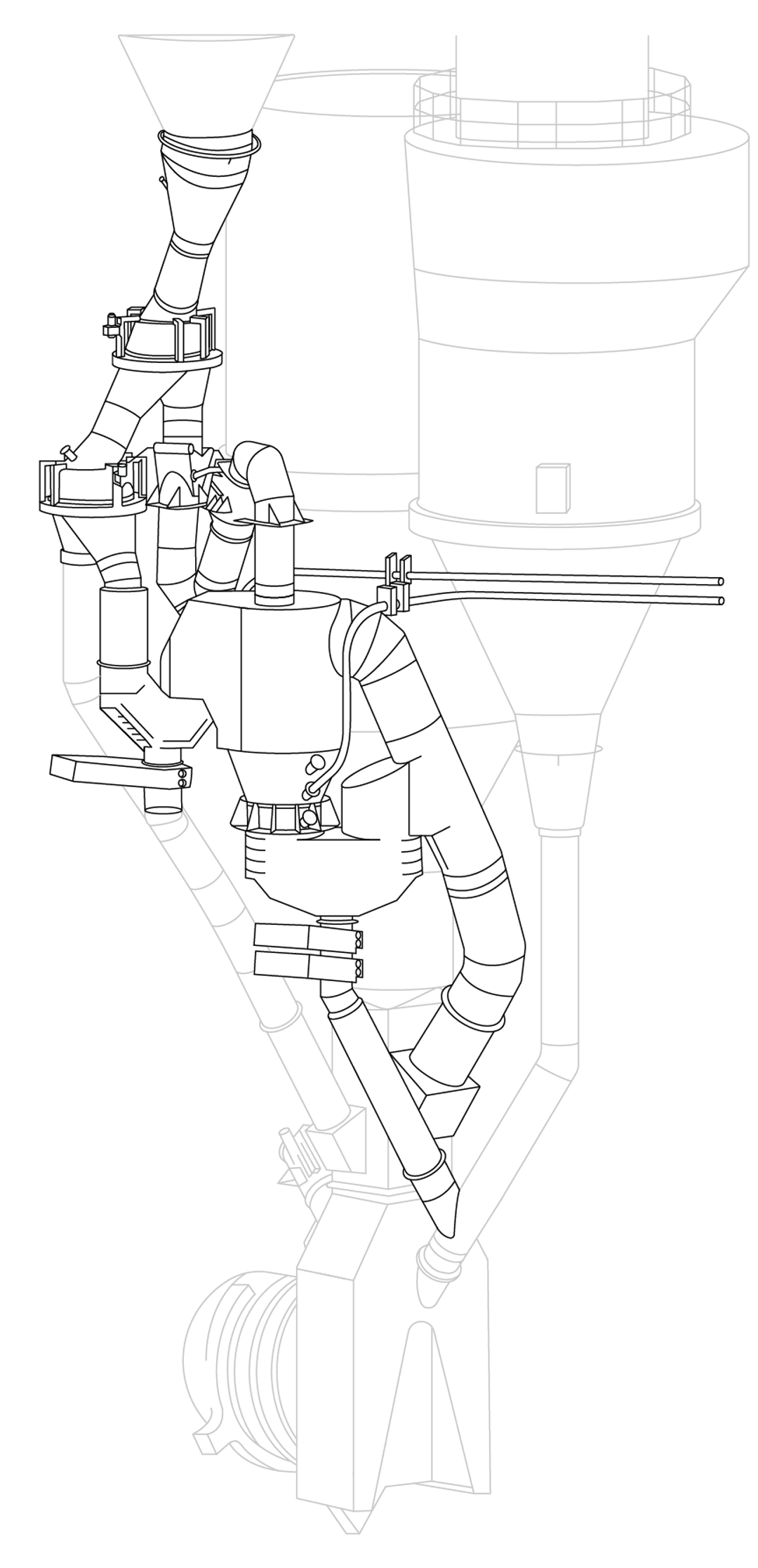
What we offer
A unique combustion solution for alternative fuels
The FUELFLEX® Pyrolyzer is a new technology specifically developed for the cement industry to replace all calciner fuel with alternative fuels, ensuring efficient, complete combustion, NOx control and process stability. The FUELFLEX® Pyrolyzer eliminates the need for a costly calciner extension to be able to reach high degrees of fossil fuel replacement by high-volatile solid fuels, which may have significant moisture content, large particles and varying calorific value. It also improves NOx emission control to the extent that the need for ammonia injection for NOx limit compliance is dramatically reduced.
Up to 100% alternative fuels with minimum NOx
Reduce CO2 emissions, as net CO2 emissions from alternative fuels generally are lower than from coal. Increase utilisation of local waste streams, avoiding the need to dispose of or store this waste in other ways. Reduce fuel costs, especially in times of fluctuating energy prices. Reduce fossil fuel use to save the associated environmental impact of natural resource extraction and transport.
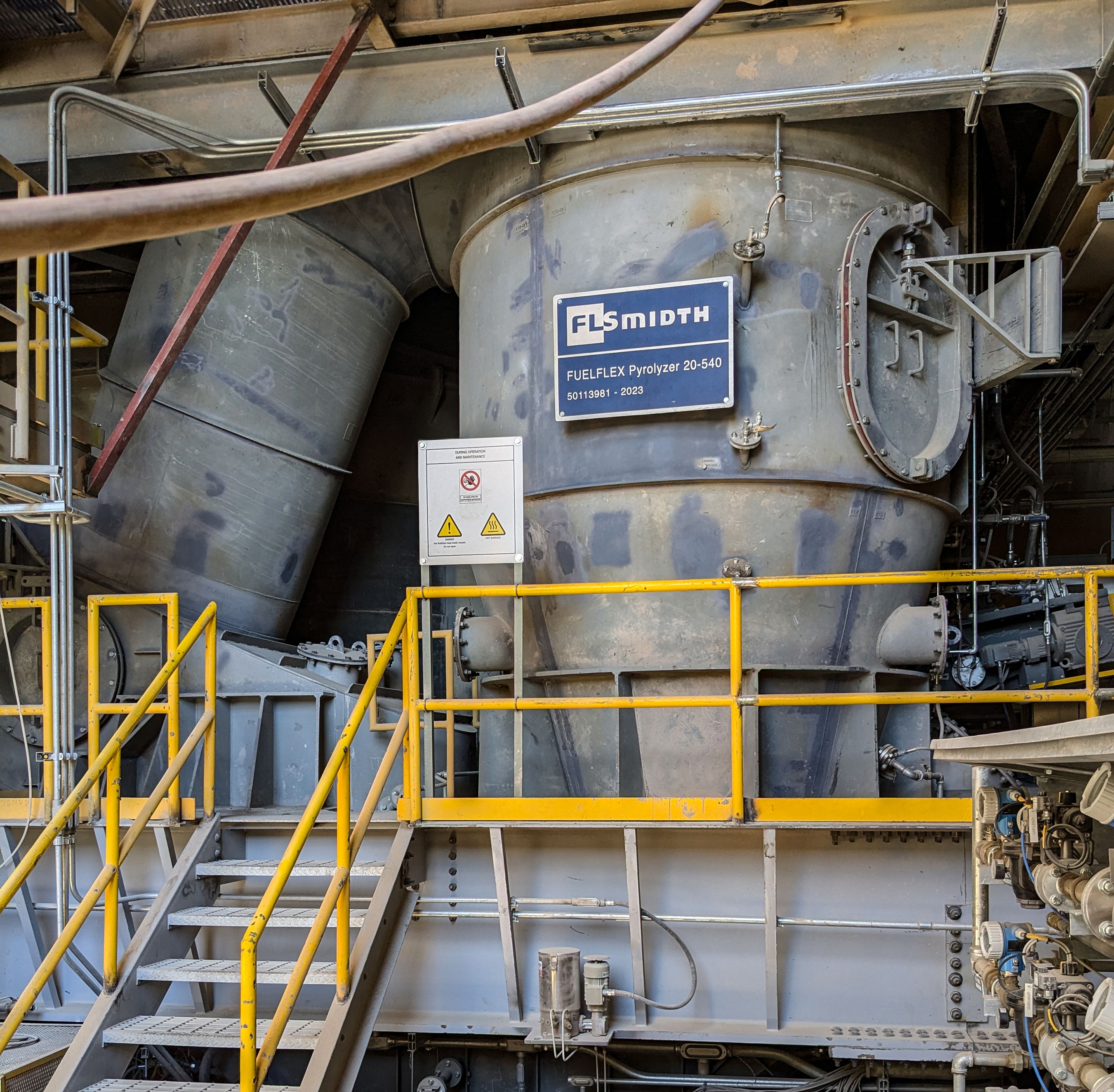
Suitable for most high-volatile fuels
Thanks to the unique design of the U-shaped reactor, even low calorific value and high moisture fuels are successful in this process, which dries as it pyrolyzes.
Increase stability in the kiln
The combustion of alternative fuels through pyrolysis ensures a stable and highly reactive stream entering the calciner, which has an ongoing positive effect on the rest of the pyroprocess.
Eliminate NOx from the calciner
The expense of controlling NOx emissions can add up to hundreds of thousands of euros per year. By successfully limiting NOx emissions, the FUELFLEX Pyrolyzer enables cement producers to dramatically reduce ammonia water consumption, and the cost, environmental and health and safety impacts associated with its use. It’s also much easier to meet NOx compliance limits, due to the lower baseline NOx in the process.
Get more value from your alternative fuels
Use a wider range and greater quantity of alternative fuels to power your calciner. The FUELFLEX Pyrolyzer maximises the reactivity of your fuel before it enters the calciner. So you can use your existing calciner for new fuels while effectively controlling NOx.
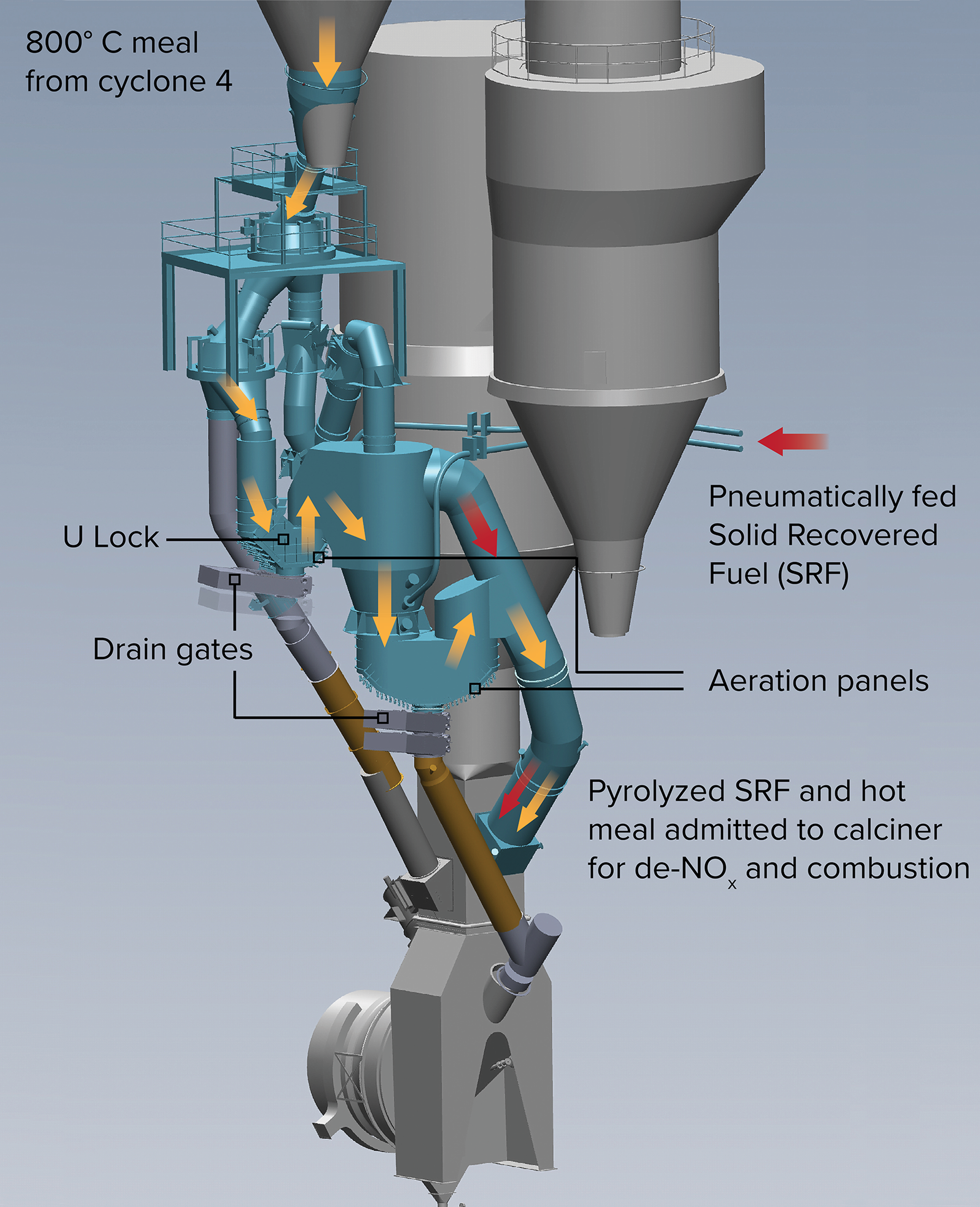
Features
How does the FUELFLEX® Pyrolyzer work?
The FUELFLEX Pyrolyzer converts Refuse Derived Fuel (RDF) or biomass to a very effective fuel stream, which enables cement plants to replace fossil fuels and control emissions without a costly calciner extension – and avoiding or limiting costs associated with NOx emission control. The FUELFLEX Pyrolyzer® utilizes hot meal from lower preheater cyclones to dry and pyrolyze SRF. The U-Lock fluidizes the hot meal, forming a U-shaped gas lock that prevents pyrolysis gases from flowing backwards through the process. Subsequently the hot meal stream flows into the Pyrolyzer vessel, which also has a U-shaped lower aerated section to contain the hot fluidized meal. RDF is pneumatically fed to the pyrolyzer vessel where, through contact with the hot meal, it is dried, heated and pyrolyzed to form reactive gases and char. The gases push upwards into the main pyrolyzer vessels while the char falls down into the fluidized meal bed, before being reunited and fed as a very reactive stream into the calciner. Aeration panels are used to fluidize the hot meal and slide gates are used to drain out debris and meal from the pyrolyzer to the kiln system in a controlled manner when required. The reactive stream of pyrolysis products react with rotary kiln NO by so-called “re-burning” reactions, utilizing pyrolysis gases to convert NO into free N2 in the reduction zone prior to mixing with preheated combustion air in the calciner. In addition, the full fuel pyrolysis preceding the calciner contributes to limiting calciner NOx formation by limiting access to oxygen when burning.
New energy efficient fluidization
We developed a patented aeration technique that uses little pulses of air to enable cohesive meal to flow smoothly without blockages.
The pulsed aeration technology is quite different from conventional fluidization in that the fluidization air consumption is dramatically lower and the meal bed is made up of fine cohesive powder (raw meal). This detail makes the FUELFLEX Pyrolyzer very energy efficient – and avoids unnecessary production capacity loss of the kiln system.
Kevin Lunney, Chief Operations Officer for Mannok