Extend maintenance intervals with our flow control and shut-off valves
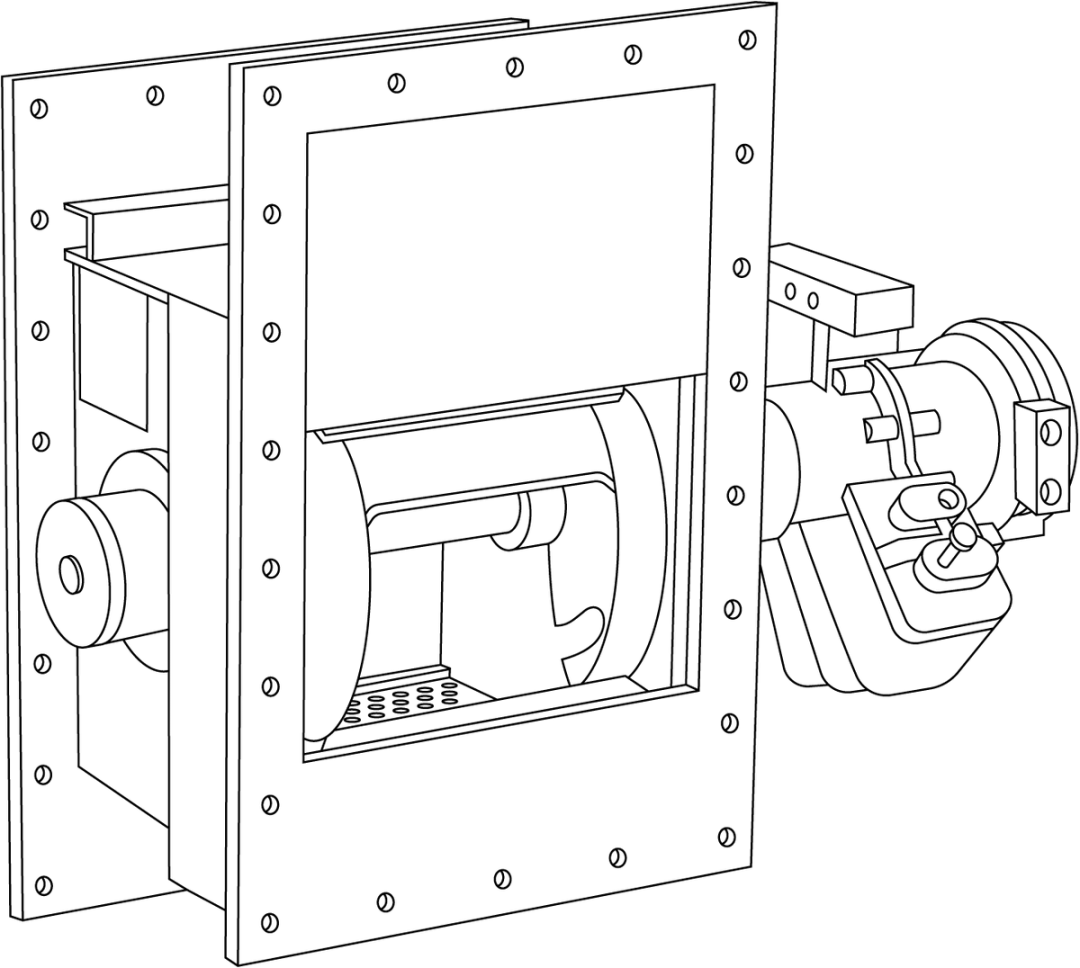
What we offer
Flow Control and Shut-off Valves for pneumatic conveying applications
Valves are critical components for optimum performance of your material transport system. But they’re also subject to significant wear, giving you a maintenance headache and a high repair bill. Our Rotary Flow Control Valve and Rotary Shut-off Valve are designed to deliver high performance bulk material control in pneumatic conveying applications, with a superior service life. The difference compared to conventional valves is the attention to detail. By adjusting the frame to the surface of the rotary valve casing, we can ensure optimum sealing and low friction. This helps to extend maintenance intervals and reduce repair costs. When it does come time to service the valve, wear parts can be easily replaced without removing the valve housing. The Rotary Flow Control Valve delivers precise and continuous adjustment of the bulk material flow from bins and silos. The Rotary Shut-off Valve is used where quick and reliable shut-off is necessary. The two valves are suitable for material flows from 10 to 1000 m³/h and temperature resistant up to 200˚C. High-quality materials and drive systems from renowned manufacturers ensure high operational reliability and thus an efficient production process.
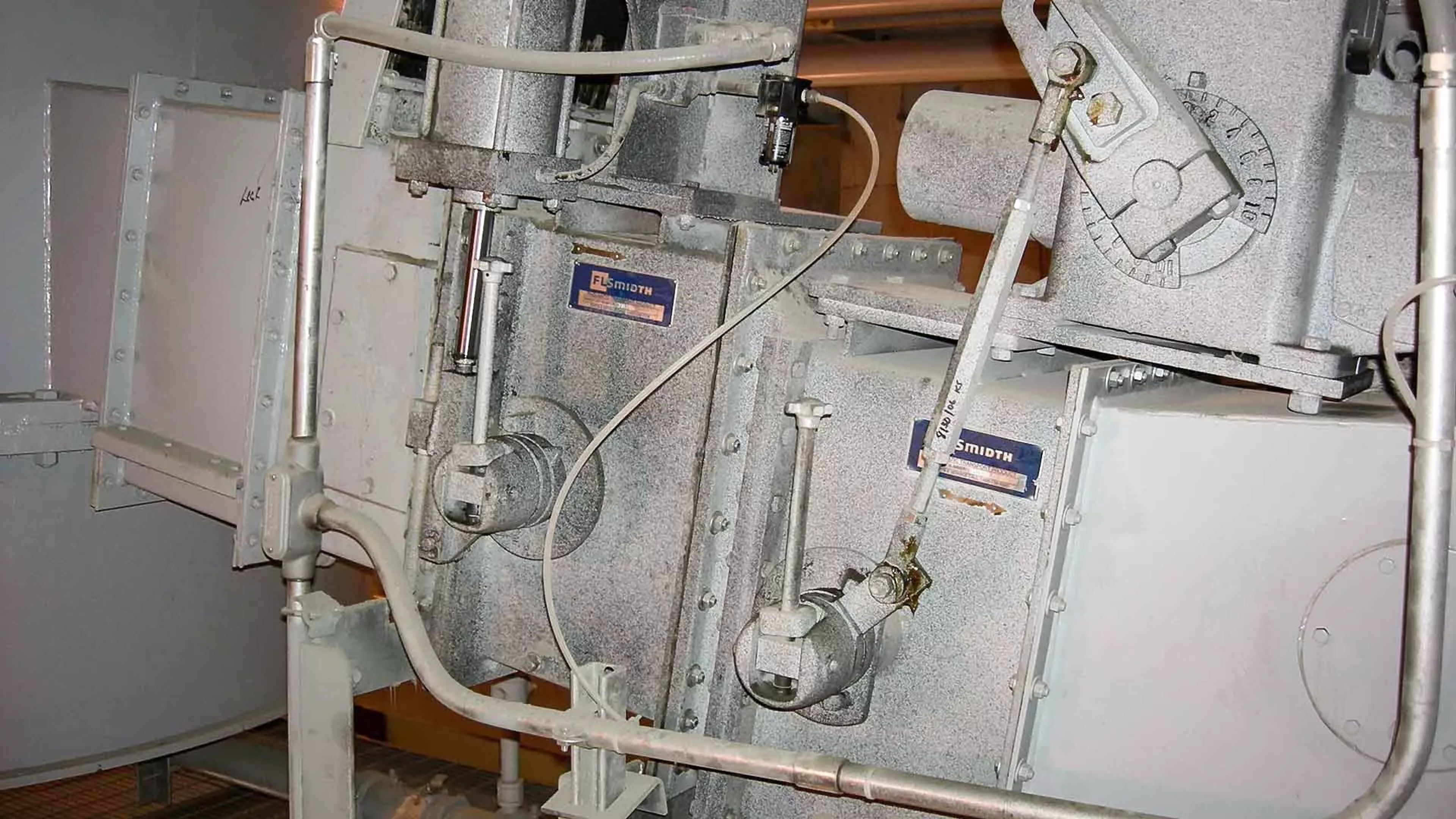
Reliable, easy maintenance rotary valves for a range of materials
Proven technology
Our Rotary Flow Control Valve and Rotary Shut-Off Valves use proven technology to deliver continuous control of material throughput in Airslide® pneumatic conveying systems with throughputs from 10 – 1000 m3/h. They are equipped with fluidisation fabric in the housing bottom to ensure free and continuous flow of materials when the valves are open.
Wear resistant
Thanks to the self-readjusting metal gasket, these valves are extremely wear resistant, giving you extended operating life with high operational reliability. They are also temperature resistant up to 200˚C, ensuring flexibility of operation across your facility.
Low maintenance
Maintenance is simple, as every valve is equipped with a large maintenance hole through which wear parts can be replaced. Service is safer, quicker and less expensive than some conventional systems. On request, the valves can additionally be equipped with a contaminant clearing hole or stroke limiter.
Quick shut-off
The Rotary Shut-Off Valve works with a pneumatic drive to actuate very quick shut-off, though you can also opt to equip the valve with an intermediate position if required. The Rotary Flow Control Valve can be controlled by either a pneumatic or motor drive, for optimum flexibility and control of material flow.
Optimum control, maximum service life – rotary valves from FLSmidth
Rotary Flow Control Valve
Our Rotary Flow Control Valve provides an accurate means of flow control and positive shut-off of pulverised material from storage silos and feed bins. Four different sizes provide a range of control from complete shut-off up to 1000 m3/hour. The rotary metering flow valve can control pulverised materials passing 35 mesh. The rotary flow control valve can shut off and adjust any desired bulk material flow between 10 and 100% using a specially shaped metering section. Further turning of the rotary valve will provide a cleaning hole through which contaminant can easily flow out.
Rotary Shut-Off Valve
Due to its technical design the rotary shut-off valve is suitable for quick and reliable shut-off. However, we can also adapt the valve to open to any desired intermediate position using a special valve control system. In addition, the maximum opening cross-section can be limited by a stroke limiter. The housing bottom of each valve is equipped with a fluidisation fabric to prevent tearing off or deceleration of the material flow. This ensures the valve doesn’t impair the performance of your pneumatic conveying system. The cast iron sealing frame is flexibly attached to the housing and is continuously pressed against the rotary valve casing by self-readjusting spiral springs to avoid blockage.
Typical applications handle materials such as:
- Cement raw meal
- Finish cement
- Fly ash
- Limestone
- Gypsum
- Soda ash
- Talc
- Resins
- Ground ores
- Phosphates
- Clay
- Bentonite
- Hydrated lime
- Alumina oxide