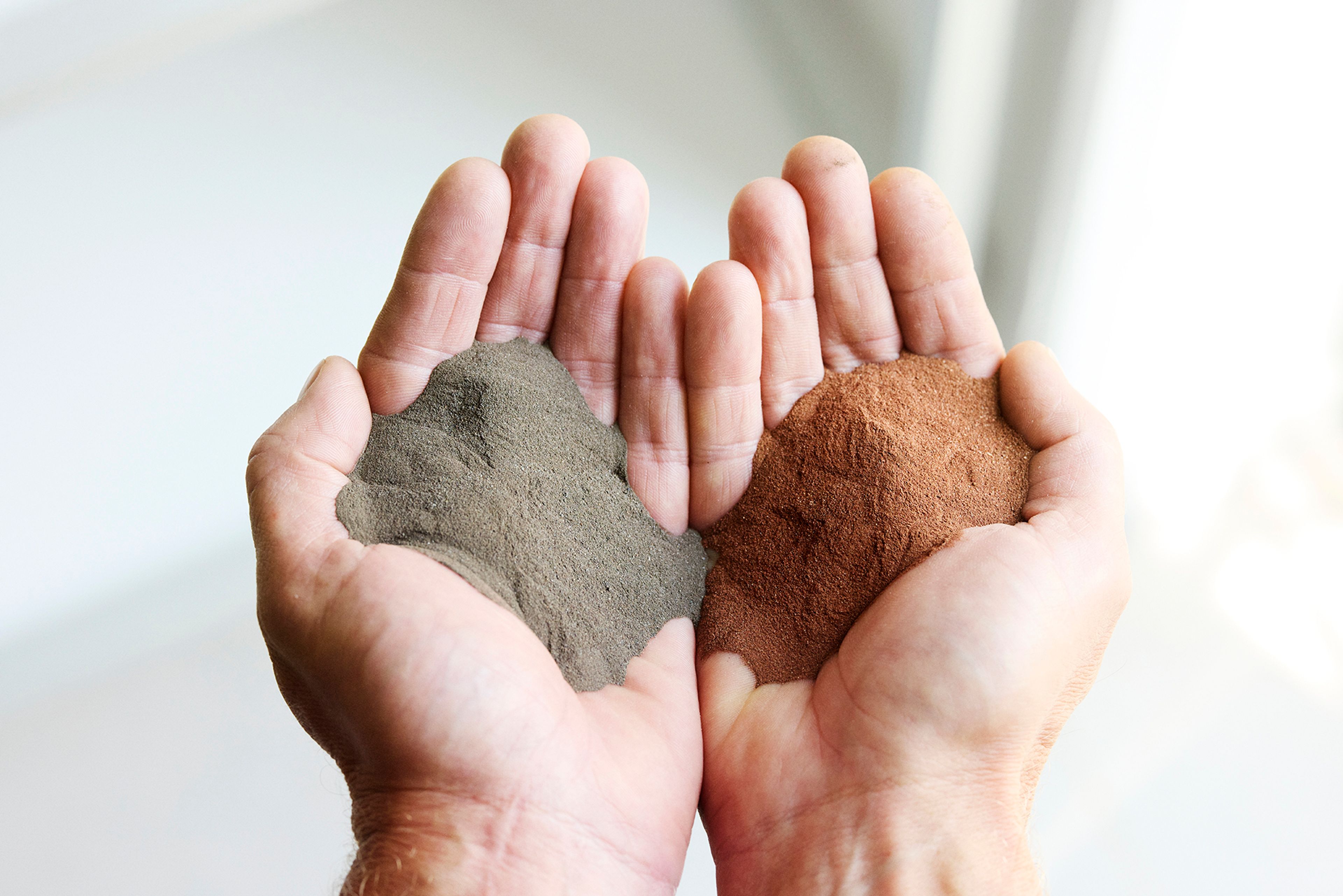
A partnership to decarbonize the cement industry.
Current clay calcination processes have gained momentum in recent years. With FLSmidth’s existing flash calciner system, cement producers are able to produce highly reactive clays that replace 30% - 40% of the limestone-based clinker, resulting in a huge reduction in CO₂ emission. By electrifying the clay calcination process preferably using renewable sources and thereby eliminating the use of fossil fuels, the ECoClay partnership expects to further reduce emissions up to a total of 50% reduction per ton of cement produced. Furthermore, electrification enables better temperature control, and thus more uniformed material activation and higher end-product quality.
Leading industry experts partnering to target 50% CO2 reduction in cement production
To further decarbonise the cement industry, FLSmidth and a series of leading industry experts have formed a partnership called ECoClay™. To reduce CO2 emissions from cement production by up to 50%, the ECoClay partners will develop and commercialise the technology needed to replace fossil fuels in clay calcination by fully electrifying the process.
The use of calcined clay as a Supplementary Cementitious Material (SCM) is essential in drastically reducing the massive environmental footprint from conventional cement production, which today accounts for approximately 7-8% of the world’s CO2 emission.
Based on the shared research and testing on clay activation, electric heat generation and storage, and grid integration, the ECoClay partnership will build a pilot plant at one of FLSmidth’s R&D Centers located in Denmark. The consortium seeks to demonstrate how the ECoClay solution is competitive in terms of better process control, greater efficiency, lower capital investment and higher end-product quality.
Based on the shared research and testing on clay activation, electric heat generation and storage, and grid integration, the ECoClay partnership will build a pilot plant at one of FLSmidth’s R&D Centers located in Denmark. The consortium seeks to demonstrate how the ECoClay solution is competitive in terms of better process control, greater efficiency, lower capital investment and higher end-product quality.
According to the project plan, the ECoClay partners expect to commence construction of the first full-scale electric clay calcination installation by mid 2026.
Unlocking value with ECoClay™
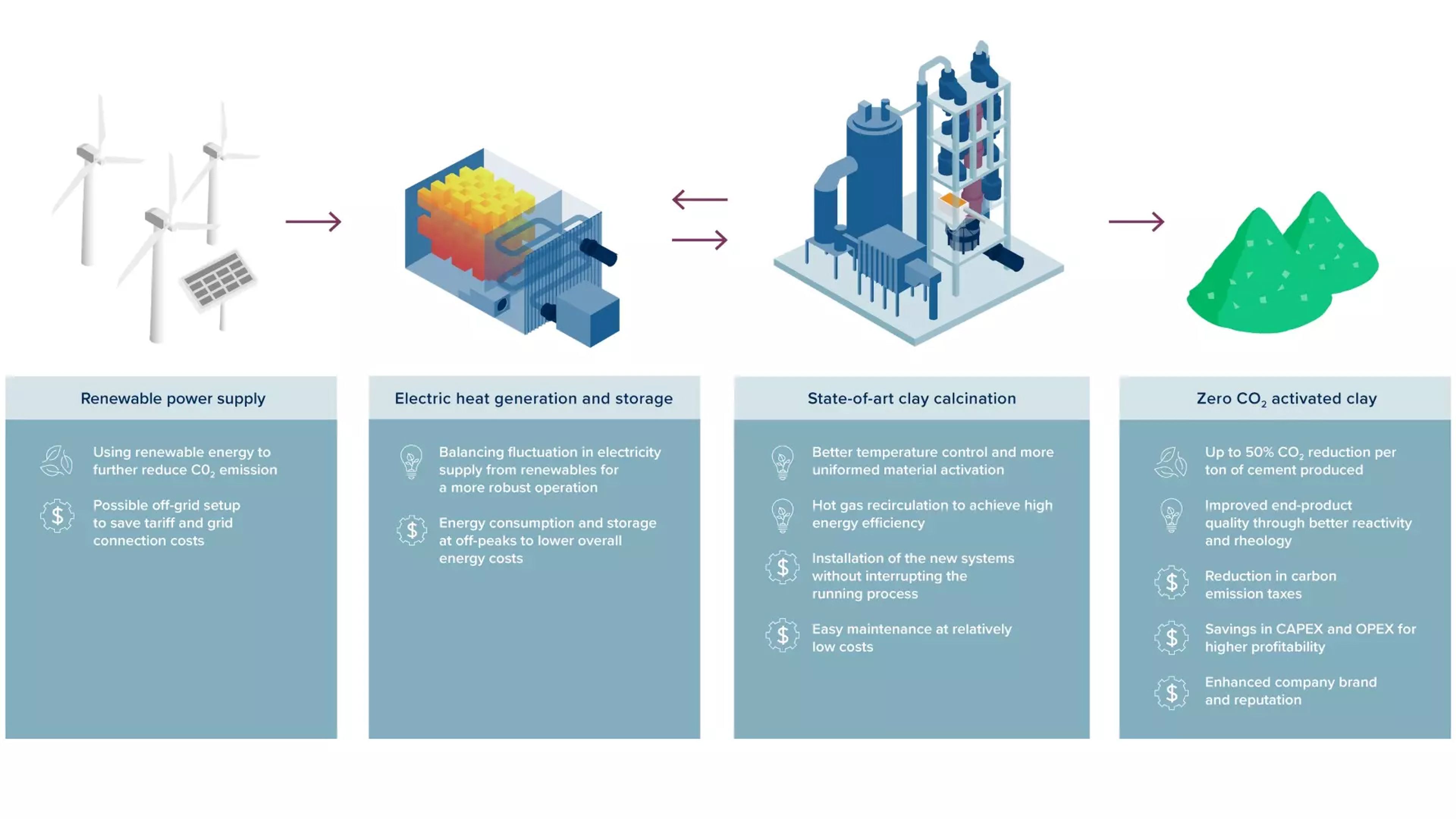
TIMELINE
START
01.Jan.2022
END
30.Jun.2026
Funding remark:
This project is partially funded by the Danish Energy Technology Development and Demonstration Program (EUDP) under the Danish Energy Agency, Project Agreement No. 64021-7009.
Pilot plant
ECoClay will pilot a new-to-the-world energy and process technology that enables the direct use of electrical energy for the clay activation process, at temperatures range from 700 to 900 °C depending on the clay properties. This demonstration comprises the development and operation of a pilot plant with a clay throughput of 50 to 100 kilograms per hour as the first step towards commercialization. The pilot plant will be used to validate feasibility and viability of the ECoClayTM solution through study of different process configurations and simulation of grid integration with renewables.
It is expected to obtain a fully integrated process, new knowledge, reliable design tools, a complete technical layout, and a full techno-economic report. This information will pave the way for the first large-scale industrial unit and accelerate the decarbonization in the cement sector.
More information is coming soon.
PHD PROJECTS
Academic research
Project 1
Process calculation, CFD model based on measurements on pilot
This PhD project is running in close related to research activities conducted at the Danish Technological Institute (DTI). There are three main research objectives in this PhD project:
To understand the calciner system layout and recycling influence on energy efficiency and provide recommendations for an efficient system layout.
To develop a model that provide an understanding of the interaction of flow, clay kinetics and calciner layout on the obtained conversion and thereby also provide a tool that can be used for scaling up the calciner reactor.
To improve the understanding of the calcination reactor and evaluate the CFD model calculations, detailed local reactor measurements will be done.
Project 2
Integration of clay calciner with renewable energy resources
Innovative electrification of the clay calcination process holds promises of a huge unexploited pool of flexible electricity consumption as well as emission reduction. The main objective of the ECoClay™ PhD project is to demonstrate how data-driven modelling, grid integration simulations, and optimal dispatch strategies can enhance demand-side flexibility using an industrial process hybridized with energy storage. The following PhD activities and outcomes are anticipated:
Electricity consumption profiling of ECoClay pilot plant to validate the electric metric of mass and energy balances.
Grid integration-oriented modelling, optimal sizing, and optimal placing of distributed energy resources (e.g. wind and solar power) and key components including heat storage according to the load profile of the electric clay calcination, its geographic location and its key equipment operation characteristics based on the wealth of data that can be collected at all levels (e.g. sensors/SCADA) of ECoClay system.
Simulation of grid integration for the selected use cases for example, geographic locations with high penetration of wind power and solar PV; heat storage hybridization with battery electric storage systems, etc.
Developing smart grid-oriented optimal dispatch and control strategies to support wind/solar power integration and stable & reliable operation of the ECoClay system to maximize its demand-side flexibility considering among others machine-learning based multi-objective optimization with cost-effective, CO2 reduction and value-added grid services.
Exploring and facilitating the replicability and scalability of power-to-heat solutions in the ECoClay system to harvest demand-side flexibility, economic and environmental benefit.
Project 3
Digital Twin modelling for operations and model predictive control
The objective of this research is to establish methods for advanced and robust model predictive control. The models must be able to assimilate information from sensors related to the process in near real-time. We will aim at constructing models which are able to take advantage of combining information from first principles with information in data. This research will focus on identifying digital twin models for process control and decision making under uncertainty. The digital twin models will be formulated as continuous- discrete time stochastic state space models. This family of models allow for a real-time estimation of important process parameters that are not directly measured or measurable.
The dynamics of the models are described by a set of stochastic differential equations, and this formulation enables a possibility for combining information from chemistry and physics with information embedded in measured data and signals. This type of digital twin models will be formulated in a way which allows for auto-tuning of the most important model parameters. It is well-know that this type of models is superior for advanced model predictive control. The formulation also allows for embedded forecasting of the relevant disturbances, and recent applications of this methodology has led to significant improvements of the performance of the controllers. The result on the response will be used by the grid integration project.
PARTNERS
PARTNERS
FLSmidth A/S
140 years’ experience in the cement industry. FLSmidth A/S is global company, who strives to provide sustainable productivity to the cement and mining industries. FLSmidth was founded in 1882 and has 140 years’ experience in the cement industry. The FLSmidth history is a classic narration of entrepreneurial success, starting out as a local one-man consultancy firm with humble beginnings and, through hard work and a sound strategy, growing into a major international company, specialised in serving the cement and mining industry, worldwide. Today, FLSmidth consists of 12,000+ employees, is present in 60+ countries, had a revenue of 17.6 DKKm in 2021, and is the market-leading supplier of engineering, equipment and service solutions to customers in the global mining and cement industries.
VICAT, France
Vicat is a French group that develops materials, products and services for construction players. VICAT is a global cement producer from France, who is committed to limiting his environmental impact with several innovative ideas for reducing its carbon emissions. To decarbonise its cement production processes, the company has recently purchased its first clay activation process line from FLSmidth. The invention of the electrical clay activation can become the first significant and commercially viable process in the electrification of the cement industry. Electrification allows the use of renewable energy (solar, wind) and supports independence from fossil fuels which are both great drivers of technology. Additionally, the ECoClay technology might allow for processing a much broader range of clays (composition and impurities) due to the better mixing and temperature control, making it commercially very attractive compared to the state-of-the-art. Being in the project gives VICAT the first-mover advantage and new market opportunities. Further opportunities come from potential new product formulations due to the unique material properties of electrically activated clay, e.g. higher reactivity.
Argos, Colombia
Focus on client and sustainable development. Argos is a multinational company that produces and markets cement and ready-mix concrete through its operations in Colombia, the United States, Central America, and the Caribbean. In the cement industry, Argos is the leader in Colombia, the fifth largest producer in Latin America, and the second largest in the southeast of the United States. In the Ready-Mix business, Argos is the market leader in Colombia and the second largest producer on the southeast coast of the United States. Its business model focuses on client and sustainable development, which means it is economically viable, respects people, and is environmentally friendly and responsible. Argos was the first player in the world to operate a calcination clay line to produce a SCM that is combined with clinker, limestone, and gypsum to produce blended cement successfully. With this project, Argos will still in the cutting edge of implementation and use of calcined clay as a cementitious material. With the operational experience, access to a broad range of clays (not available in Europe), and product properties (for comparison), the ECoClay process brings relevant value to the project, and it is fully in line with the EUDP goals to commercialize such a process as fast as possible and to act as a role model for the green transition of the cement industry.
Rondo Energy Inc, United States
Eliminating CO2 emissions from the world's most energy-intensive industries Rondo designs and delivers creates concepts, technologies and complete solutions to store and continuously release industrial heat that is generated from intermittent electricity through resistive heating. Rondo’s Heat Battery captures intermittent electricity, whether from new dedicated renewable generation or from overcapacity at times of excess electricity production (a lot of wind or solar energy). The Rondo Heat Battery technology releases the stored energy (heat) continuously or on demand, so as to power continuous high-temperature industrial processes from low-cost green electricity without increasing peak demands on the grid. The overall goal is to establish economic viability and make a green transition in the cement and process industry possible at reasonable costs.
DTU Chemical Engineering
Meet today’s industrial challenges and create value through education, innovation and research. DTU KT deals with research for the development of sustainable technologies that can lead to reduced climate footprint and support the competitiveness of the Danish industry. The department research includes studies on high temperature processes, process plant optimisation, cement processes and modelling of reactors and particle conversion. The DTU KT project work will include process modelling, reactor CFD modelling, and pilot reactor measurements, and will fit in very well with the present DTU KT strategy.
DTU Wind and Energy Systems
Creating an impact for people and society through research and innovation. The DTU Department of Wind and Energy Systems is one of the world’s largest centers providing sustainable solutions for integrated energy systems powered by wind energy. The Power and Energy Systems (PES) division, part of DTU Wind and Energy Systems strives for excellence within grid modelling and simulation in the ECoClay project. PES Division has large experience with the application, operation and integration of energy storage systems such as Lithium-ion based battery systems (0.01-1MWh system), flow battery systems and heat storages. A battery electric energy storage system can act as a proxy for or be hybridised with a heat storage system in an industrial pilot plant. In achieving our goals DTU Wind and Energy Systems sees an advantage in expanding its collaboration with DTU Compute regarding advanced industrial process control. In addressing the energy intensive cement industry, DTU Wind and Energy Systems sees FLSmidth is a preferred strategic industrial partner in demonstrating the potential of a major reduction in carbon emissions. The reduction may be achieved by adding significant but controlled electric power consumption to the demand side management portfolio, thus supporting integration of more renewable production methods.
DTU Compute
Create knowledge and innovation to develop the society of the future DTU Compute strives to be a leading player related to demand side management and use of flexibility in general, and consequently the ECOClay project is within the core of our interests. DTU Compute hosts the researcher, which according to Google Scolar, is No. 1 worldwide on citations related to demand response. Similarly, both DTU Electro and DTU Compute are winners of the Energy Cluster Denmark Innovation Price 2021, which was given to the EUROGRID project. DTU Compute provides technology for the software used for wind, solar, load and price forecasting for all major stakeholders in Denmark and Europe, and approx. 25 % of today’s global wind power is operated with our tools. DTU Compute has established widely used methods for identifying digital twin models which are optimised for utilising real-time information from sensors. DTU Compute has established some of the leading software packages for model predictive control. FLSmidth is a strategic partner for DTU Compute, and we have a historical track record in providing optimal solutions for the cement industry. With the ECOClay project, it will become possible to understand how the flexibility of an important indus- trial plant can better facilitate integration of fluctuating green electricity. DTU Compute is also interested in expanding the collaborations with DTU Electro on smart grids, forecasting, modelling, and control using data-driven methods.
Chimneylab
More than 20 years experience in type testing chimneys and related products for CE-certification ChimneyLab Europe ApS is one of the largest accredited chimney testing centres in Northern Europe, with more than 18 years’ experience testing chimneys, liners and flues. With the participation in the current project, ChimneyLab will expand its pilot plant-competencies and emission testing business to include operation of cement pilot plants.
Danish Technological Institute
Ensure durable buildings, with a healthy indoor climate. Danish Technological Institute is among the strongest partners when it comes to developing and implementing high-tech solutions in Danish companies. We are a key partner in ensuring that the green transition takes place in companies in terms of energy, materials and foods. The green transition requires technological knowledge, test facilities that are ready for industrial use and partnerships in order to achieve its goals. Energy is one of the three areas where the Institute has strengthened its position as an important business partner for the green transition of companies in 2021/22. The two other areas are materials and foods. In all three areas, we offer Danish companies a shortcut in the form of competences and equipment for developing and testing green technological solutions.
GET IN TOUCH WITH US
For more information about the project, you can get in touch with us via the contact methods on the right.
FLSmidth Cement
Vigerslev Allé 77, 2500, Valby, Copenhagen, Denmark
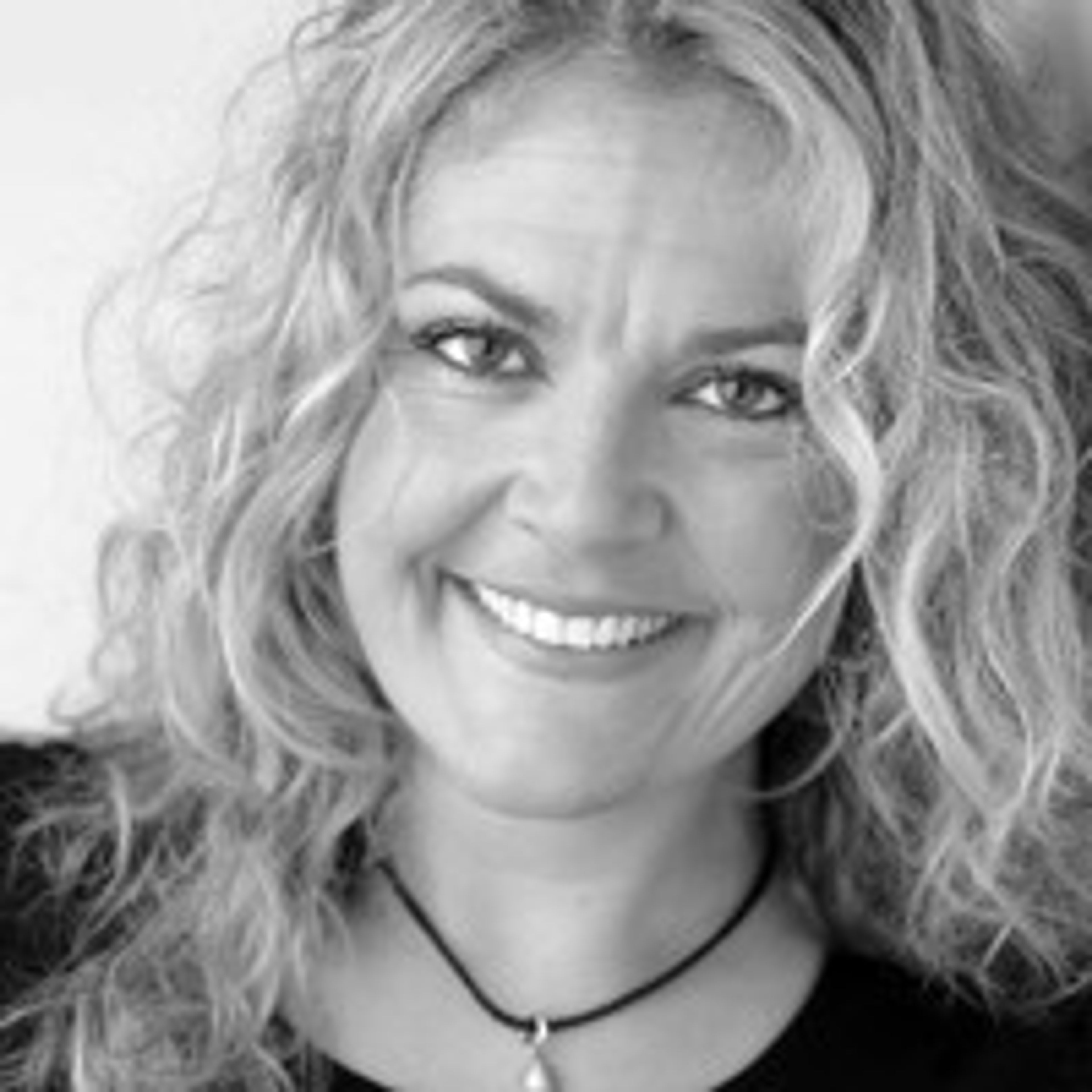
Lone Wittenkamp
Project Manager, Green Innovation
Phone: +45 4137 1621
ECoClay publications in the press
Read about ECoClay in the news and stay updated on our SoMe channels
Featured posts