Reliable and efficient kiln sealing
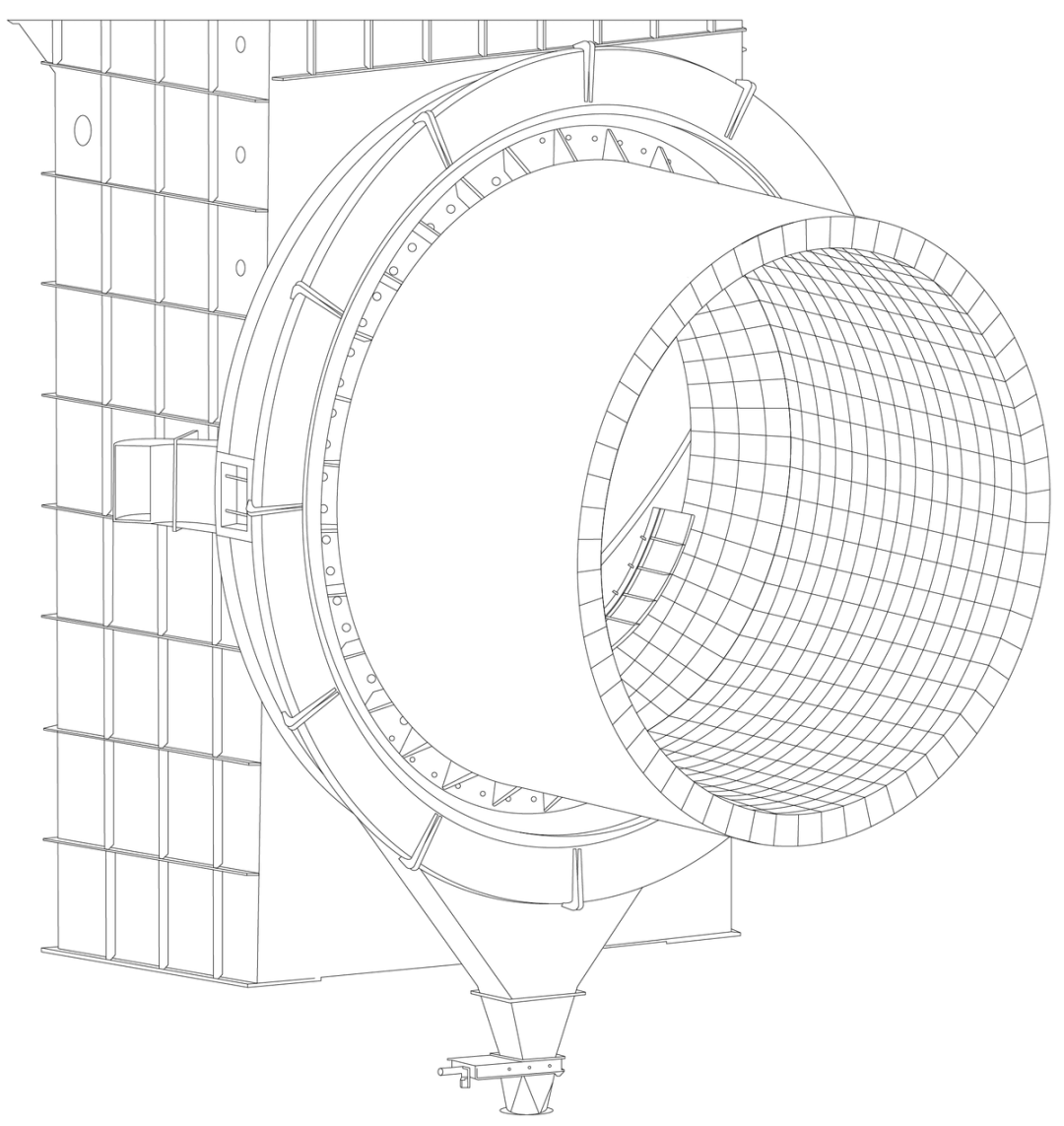
What we offer
What’s new with the Spring Tensioned Graphite Seal
The inline row of graphite blocks that make up the FLSmidth Cement Spring-tensioned Graphite Seal are actuated by individual thrust modules, which ensure efficient sealing towards the rotating parts – i.e. the sealing ring or the cooling mantle – at inlet and outlet, respectively. This arrangement allows the graphite blocks to move individually with the movement of the kiln without any risk of getting stuck or damaged. We’ve also added a linear guide system to the tensioning module to prevent lateral movement and stop false air entering the kiln system.
The thrust module – how it works
The compact thrust module generates the individual thrust to each graphite block by a spring suspended/tensioned in the module. Four bearings operate with low friction on two hardened stainless-steel shafts to secure a controlled and fast response to the kiln runout. The module easily takes up any movements of up to ±50mm caused by kiln runout, ovality or expansion. With an individual tensioning arrangement for each block, we eliminate the risk of failure across numerous blocks compared to other tensioning systems, such as wire ropes. The spring force can be adjusted as the graphite blocks wear.
Three key features contribute to the success of the Spring Tensioned Graphite Seal:
Unique mechanism to thrust the graphite block against rotating parts
Linear guide for each graphite block to control lateral movement
A design that can handle a runout of up to ±50mm
Flexible solution for kilns of all sizes
The Spring Tensioned Graphite Seal is highly flexible and easily adaptable to any size of kiln – both of FLSmidth Cement and third-party design.
Fast and easy installation
Modules can be easily pre-assembled, so the typical installation of a new Spring Tensioned Graphite Seal requires just 7 to 10 days.
Built to last
The wear parts are made to run for a period of 3-5 years without any need to replace the parts during normal operations conditions.
Kiln inlet spring tensioned graphite seal dust handling system
Depending on the kiln design and the ability for integration of the existing dust handling system, the graphite seal can be delivered with a heat-resistant steel shovel arrangement, which effectively collects any back spillage and returns it to the kiln.
Kiln outlet spring-tensioned graphite seal dust handling system
Depending on customer requests, the dust handling system can be designed to ensure that escaping dust from the kiln outlet is collected in a concentric dust chamber and returned directly to the cooler either to the first grate or to the external drag chain system via a chute.
Heat shield
A heat shield is installed in the casing to protect the graphite blocks from the radiant heat and from coming into direct contact with the clinker dust via a chute.
Air cooling system - Inlet
The inlet cooling system consists of a fan and a closed isolated ducting system to cool vital sealing components. The cooling air is distributed to the rear flange and the air-cooling chamber attached to the kiln riser. The air will escape into the atmosphere.
Air cooling system - Outlet
The outlet cooling system is separated into two independent systems – one for the kiln shell and nose ring cooling and one for the graphite cooling. The graphite cooling is designed to maintain the temperature of the graphite blocks below oxidization temperature and secures the flatness of the flange module.