article
Calcined clay: test before you invest
Testing, testing – how material and pilot scale testing helps confirm clay suitability for eco cement: FLSmidth experts describe the material testing necessary to determine if a particular clay is suitable to process into eco-friendly cement.
Testing, testing
How material and pilot scale testing helps confirm clay suitability for eco cement
Clay is a naturally occurring material found almost everywhere around the world. Already, current standards allow for 50-55% clinker substitution, reducing process emissions by more than 40% - a staggering achievement for an industry that is currently responsible for producing around 7% of global CO2 emissions. Looking ahead, though, the potential is far greater. As practices evolve even further, performance-based approaches will likely gain wider acceptance such that 70% substitution can become more commonplace. This, paired with other CO2 reduction methods, will put the cement industry within sight of its net zero goals.
No wonder, then, that cement producers are increasingly interested in this eco alternative. But how do you know if your clay is the ‘right’ clay for the job? What guarantees should you get before you proceed with an investment? We called on Mette Moesgaard, Lab Engineer, and Rasmus Franklin Momme, Global Chief Process Engineer, to tell us all about FLSmidth’s clay testing laboratory and pilot plant, which is used by companies from around the world to determine the chances for a project’s success, based on the materials available and their properties.
Why clay matters
Cement manufacture is an emissions-intensive process. We can replace fossil fuels, we can increase energy efficiency, we can optimise every part of the process, and we still won’t get close to a zero-carbon process because of the embedded emissions that arise during the calcination of limestone. Carbon capture promises hope for the future, but that technology is not ready to take on this level of emissions just yet. Replacing clinker has therefore become key to the cement industry’s net zero vision. The less clinker we make, the less carbon emissions are released. “Cement producers have long been replacing clinker in some quantities with things like limestone, fly ash and other pozzolans,” explains Rasmus. “But clay offers a global opportunity for greater emissions reduction – first because it’s so widely available, and second because of its pozzolanic properties after activation. However, not all clay is suitable to use as a clinker replacement. Which is where our laboratory and pilot plant come in.”
Step 1: Testing the raw clay
The first step is to evaluate if the clay raw material of interest (most often clays or shales) has the potential to be a suitable precursor for SCM production. In order to do this, the customer sends us a 15 kg sample of the material, which should be a representative sample from across the deposit. They typically send several different 15 kg samples, enabling us to determine which ones have the most potential.
We use XRF, XRD and thermal analysis to determine the chemical and mineralogical composition of the sample and ask:
- Does it contain the desired minerals and at sufficient quantities?
- Are there any red flags in terms of emissions?
- What about the physical properties of the clay?

The physical properties are important because they will have an influence on wear and handling.
When we run these tests, we’re looking at it from the perspective of ‘is this feasible?’ as well as ‘is this financially viable?’ If the results were to show that emissions would be so high that the cost of air pollution control measures would outweigh the cost benefits of using calcined clay, for example, then we would make the customer aware of that so they could decide whether or not to proceed.
“At this point, we can rule out any materials where the content of reactive clay minerals is too low,” says Mette. “When that’s the case, there’s no benefit in continuing with the testing, and we’d recommend the sender look for alternative sources.”
The testing is not just a simple “pass” or “fail”, but also provides insights to guide the project design. For example, information about the physical properties of the material feeds into project planning, so that equipment is designed to withstand highly abrasive or extremely sticky materials. Not only does this avoid costly pitfalls during commissioning, but it also makes the initial business case far more accurate.
What kind of analysis?
X-ray diffraction (XRD) is an analytical technique used for phase identification and quantification of crystalline materials. Qualitative analysis of clay minerals is challenging due to the various chemical compositions, preferred orientation, structural disorder and great structural diversity of clay minerals. Thus, the XRD results are combined with other methods of analysis.
Thermal analyses, including thermogravimetric analysis and differential scanning calorimetry, are used to study how the properties of the clay raw material change upon heating. The results are used in combination with the results of XRD.
X-ray fluorescence (XRF) is a technique used to determine the oxide composition of the raw material without providing any information on the mineralogy.
Step 2: SCM characterization
"Provided the results from step one indicate that the clay may be a good match, we move on to step two. At this stage, we calcine the clay in our laboratory (usually a sample size of about 2 kg of material) and then evaluate the results. The calcination temperature will depend partly on the results of step one, but we may undertake calcination at up to three different temperatures to analyse the results." Mette
Step two also includes an emissions analysis, an initial assessment of grinding behaviour, a characterisation of the calcined material, and what the material looks like after calcination. In addition, it includes an assessment of the potential to control the colour of the calcined clay, rheology, and strength testing of a blended cement containing the calcined clay. In the case of rheology issues, we evaluate optimisation by usage of superplastizers.
“The majority of the clays we have looked at so far have moderate or high potential to be used as SCMs,” says Mette. “In the few samples we’ve seen where we’ve suggested not to proceed, one of them contained excessive Pyrite, which would increase the sulphur emissions significantly, and necessitate a much higher capital investment. That’s where the testing is so valuable. Pre-screening enables cement manufacturers to disqualify the worst materials – whether that’s because the emissions are too high or the strength doesn’t meet requirements.”
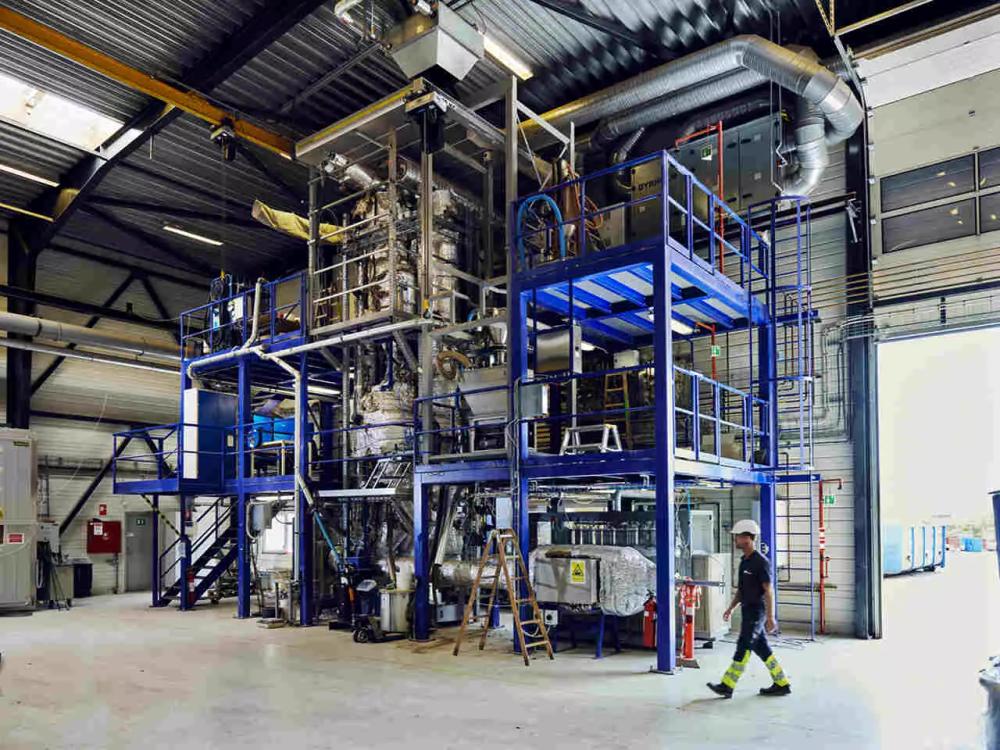
Our emissions assessment package includes:
- Chloride (wet chemical method)
- Fluoride
- Sulfide
- TOC / Org. C
- Crystal water
- CO2
- Offgas test
- Heavy metals screening, incl. Hg
The characterisation of the calcined material includes:
- Calcination degree based on thermal analyses.
- Distribution of minerals after calcination.
- Strength testing and calculation of strength activity index.
- Determination of water demand of blended cement mortar
- Assessment of the potential to control the colour of the calcined clay, including colour measurement of calcined clay with and without colour control
Colour control
“The characteristics of the clay affect the colour, which is why colour measurements are important during our tests,” explains Rasmus. “End users typically prefer grey cement, but adding calcined clay usually means the cement turns a shade of red, pink or brown. We measure the colour at the second stage of our process and undertake a laboratory scale colour reduction to understand what is needed to achieve the typical cement grey colour that customers prefer. We then apply our patent-pending colour manipulation process, to determine the colour gradients achievable for the specific clay or cement mixtures applied to. This process will become even more important as cement manufacturers increase the quantity of calcined clay in the end product – the more clay in the mix, the more colour control is

Step 3: Pilot scale calcination and product evaluation
“We have a state-of-the-art pilot scale pyro processing facility at our R&D Centre in Dania, Denmark,” says Mette. “If the material has successfully passed the first two steps of the process, we will undertake a pilot scale calcination.”
The installation includes:
- Flash calciner string with temperature up to 1000°C and feed rate up to 100 kg/h
- Fluidised bed principle reduction vessel for colour control
- Flash cooler string where temperature profiles are controlled – to ensure colour is preserved and heat recuperation will be applied in industrial configuration.
- Measure the full portfolio of gaseous emissions
“In order to undertake the pilot calcination, we usually have the customer send us at least 3 tonnes of raw material,” Mette explains. “We’re aiming to produce as much of the finished product to send back to the customer as possible – usually at least a few hundred kilograms, sometimes more – so that they can perform their own large-scale tests on mortar and concrete mixes.”
Having established the conditions for calcination in step two, in step three it is typically only necessary to produce the calcined material at one set of process conditions.
After dry crushing or grinding, the clay meal is calcined and then further tests are carried out to determine the degree of calcination, mineralogy after calcination, and the colour. It is then ground to a standard fineness and tested for performance in a blended cement mix.
The mortar test of the final product includes one standard degree of substitution and the following tests:
- Strength testing at 1, 2, 7 and 28 days according to EN norm, or 1, 3, 7 and 28 days according to ASTM norm
- Calculation of strength activity index
- Water requirement to reach normal consistency of fresh mortar
Gypsum is added to the blended cement to obtain an SO3 content that matches the SO3 content of the cement. During standard evaluation the lab uses a CEM I 52.5 cement as reference, but it’s also possible to include other cements or a clinker as part of the test.
“Step 3 is the time to experiment with process design, to define the optimum parameters for calcination, colour control and emissions,” says Rasmus. “This work is so important to ensure our customers get the most from their investment. We usually invite customers to come to the plant at this stage, so they can see the results for themselves. It’s really rare for a clay to ‘fail out’ of the process at this point, but it can happen.”
Reasons to use calcined clay to reduce your clinker factor
With LC3-50 (CEMII C/M) cement where the raw clay contained 15% moisture, 10% LOI (dihydroxylation), you can achieve:
- Up to 40% CO2 emissions reduction per tonne of cement
- 30% reduction in power consumption per tonne of cement
- 40% reduction in fuel consumption per tonne of cement
- Increase productivity without increasing emissions
- Worldwide availability
- Maintain cement quality with much-reduced environmental impact
- Technology is proven and available now, with low ROI and low OPEX
Step 4: Extra testing
In step 3, we either use our own reference cement to mix up the blended cement for testing, or the customer can send us some of their cement products for us to test. This testing is usually to produce a binary (cement/calcined clay) cement, but sometimes customers also want to test other options, like a ternary cement comprising cement, calcined clay and limestone. We offer both, so this fourth step is really just to carry out any further experimentation the customer would like to try.
Whether or not cement manufacturers proceed with the extra tests, they will receive all the information needed to decide whether to proceed with the investment. First, they will receive a complete summary and analysis of all testing performed, even guidance on the process design that would optimize their future operations. In addition, they will receive finished product (material), which they can use to carry out any further tests on their own.
A decade of pilot scale testing, more than 150 years of history
Dania is one of the world's most advanced laboratories for the analysis of raw materials in cement production, receiving and testing tonnes of raw materials from all over the world. The Dania pilot plant was commissioned in 2010 and reconfigured for SCM activation and colour control in 2020, but the site has been processing materials in one form or another since it was originally built as a cement plant in 1872.

Conclusion
Calcined clay represents the best opportunity the cement industry has right now for large-scale emissions reduction, as well as reducing OPEX or even enabling a low-cost capacity increase. As standards evolve to enable greater use of SCMs, cement producers would be wise to seize that opportunity and position themselves for future changes to the cement mix. However, while the market continues to demand grey cement, cement manufacturers should also be aware that the more clay they add, the more colour control will be needed. In order to ensure the right quality and the correct colour, careful planning is required. Pilot scale testing enables cement producers to get the information they need to determine if their clay is suitable, and to design the process for the best results.
This article originally appeared in the August 2023 issue of ICR (International Cement Review)