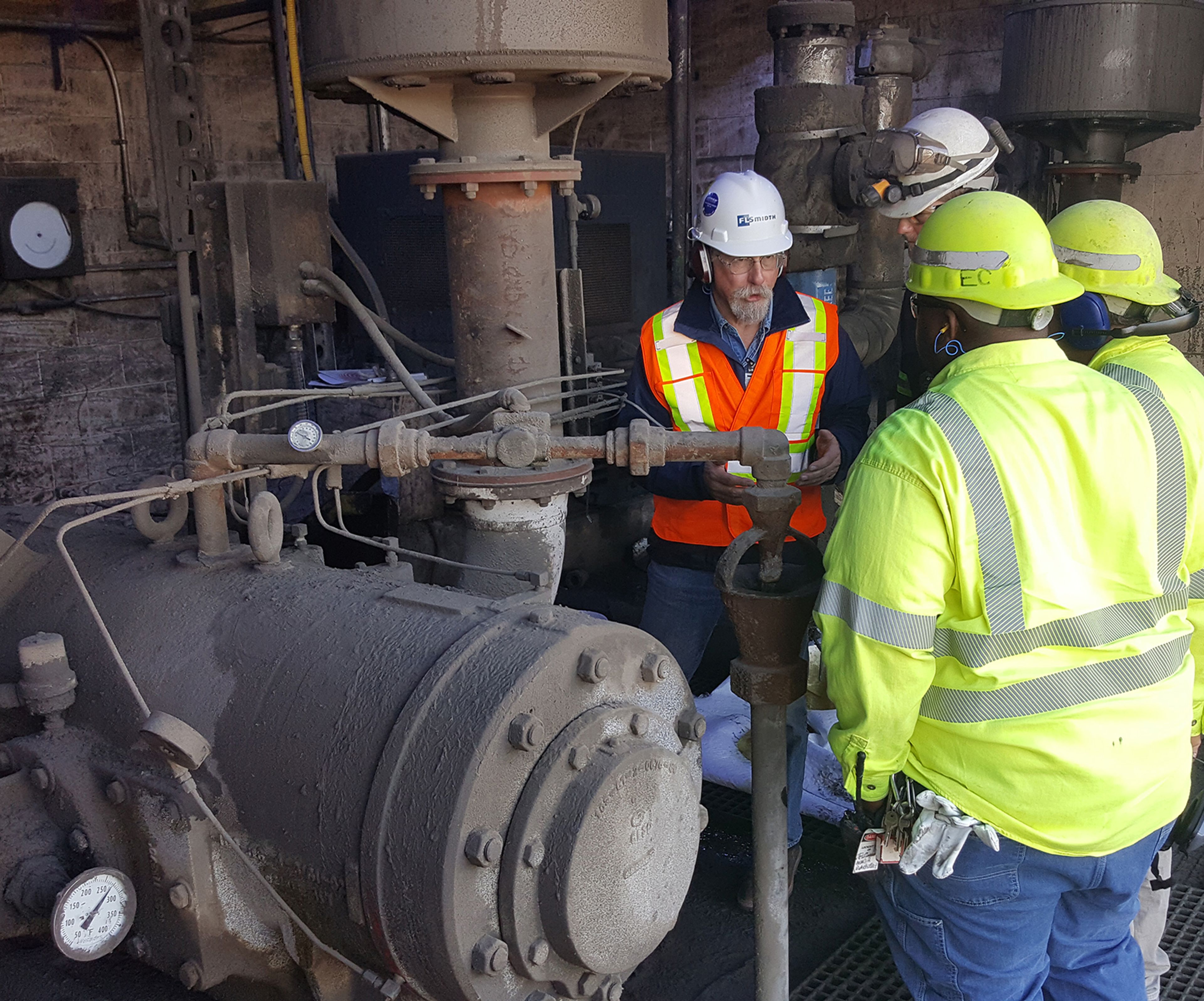
Better service means higher productivity
What we offer
Improve your plant’s productivity and boost your bottom line
The technology exists to improve plant efficiency, and we want to help get you there. Our world-class services and equipment programs are designed to bring you solutions that enhance your efficiency, whether that is new technology or new ideas. Above all, we want to share our experience so that you can improve your plant’s productivity and boost your bottom line.
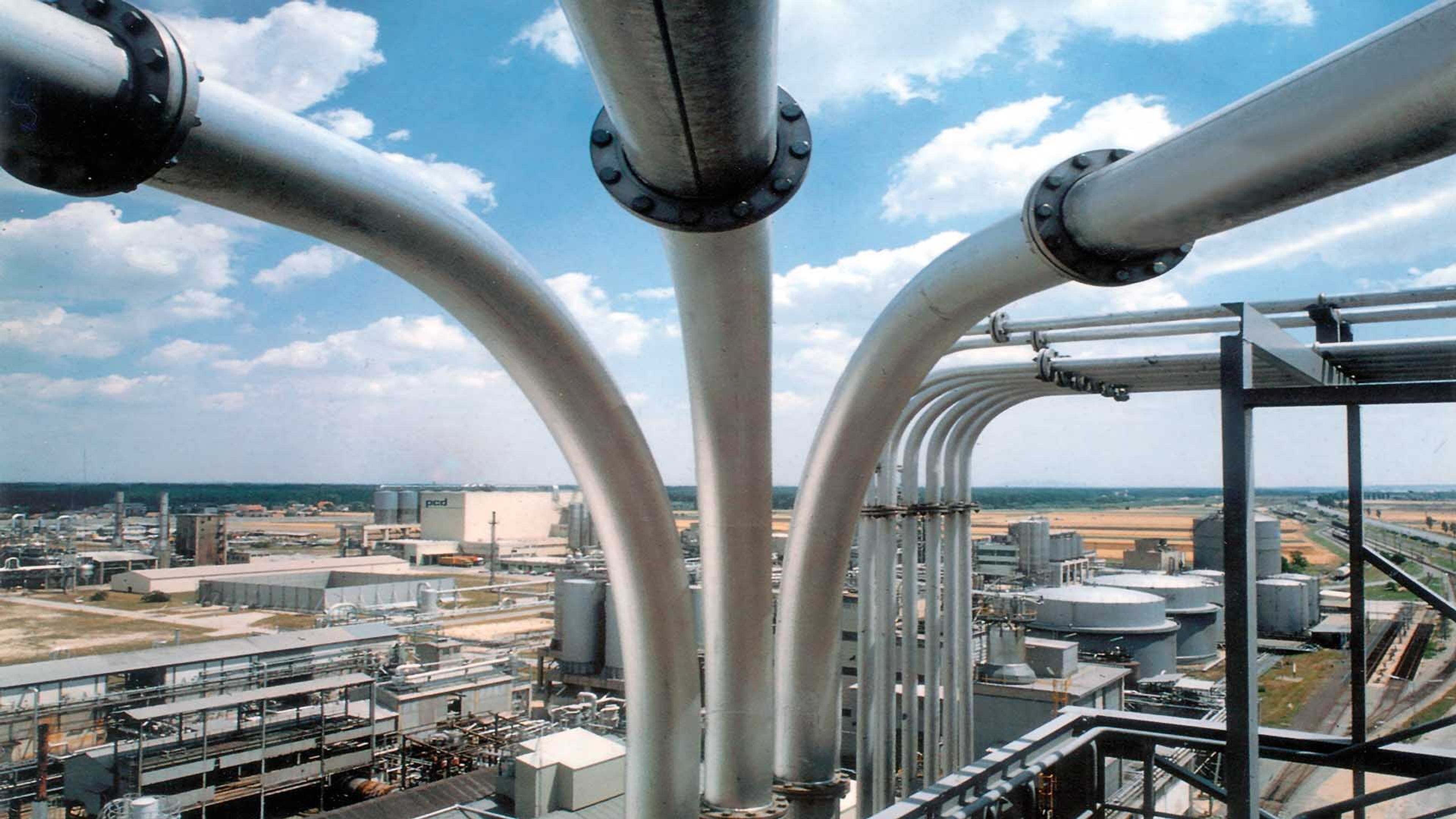
Maximize pneumatic conveying performance
Better service means higher productivity
Ful-Vane™ compressor exchange program
Our compressor exchange program enables you get back to business as usual – and fast, and to offers significant cost-savings over other replacement options.
Hot swap bearing assembly for FK Pumps
Keep Hot Swap bearing assemblies on your shelf. Having complete bearing assemblies readily available cuts downtime by more than half.
3-Piece screw upgrade for Fuller-Kinyon® pumps
Our convenient and cost-effective pump screw upgrade reduces downtime, lowers maintenance costs and minimizes the impact on the rest of your equipment.
A spare parts program that works for you
A ready supply of spare parts is essential for the continued, efficient operation of your plant. But the cost of carrying all the necessary spare parts can be prohibitive. We’ve developed a Spare Parts Stocking Program (SPSP) that enables you to keep up safe inventory levels in your storeroom while minimizing costs.
FK Pump and Compressor Roadshow training
How well do you know your Fuller-Kinyon® Pump and Ful-Vane Compressor? The better you understand how these industry workhorses operate, the better the performance you’ll get from them. That’s why we’ve developed the Pump and Compressor Roadshow – so that we can bring our expertise to your site,
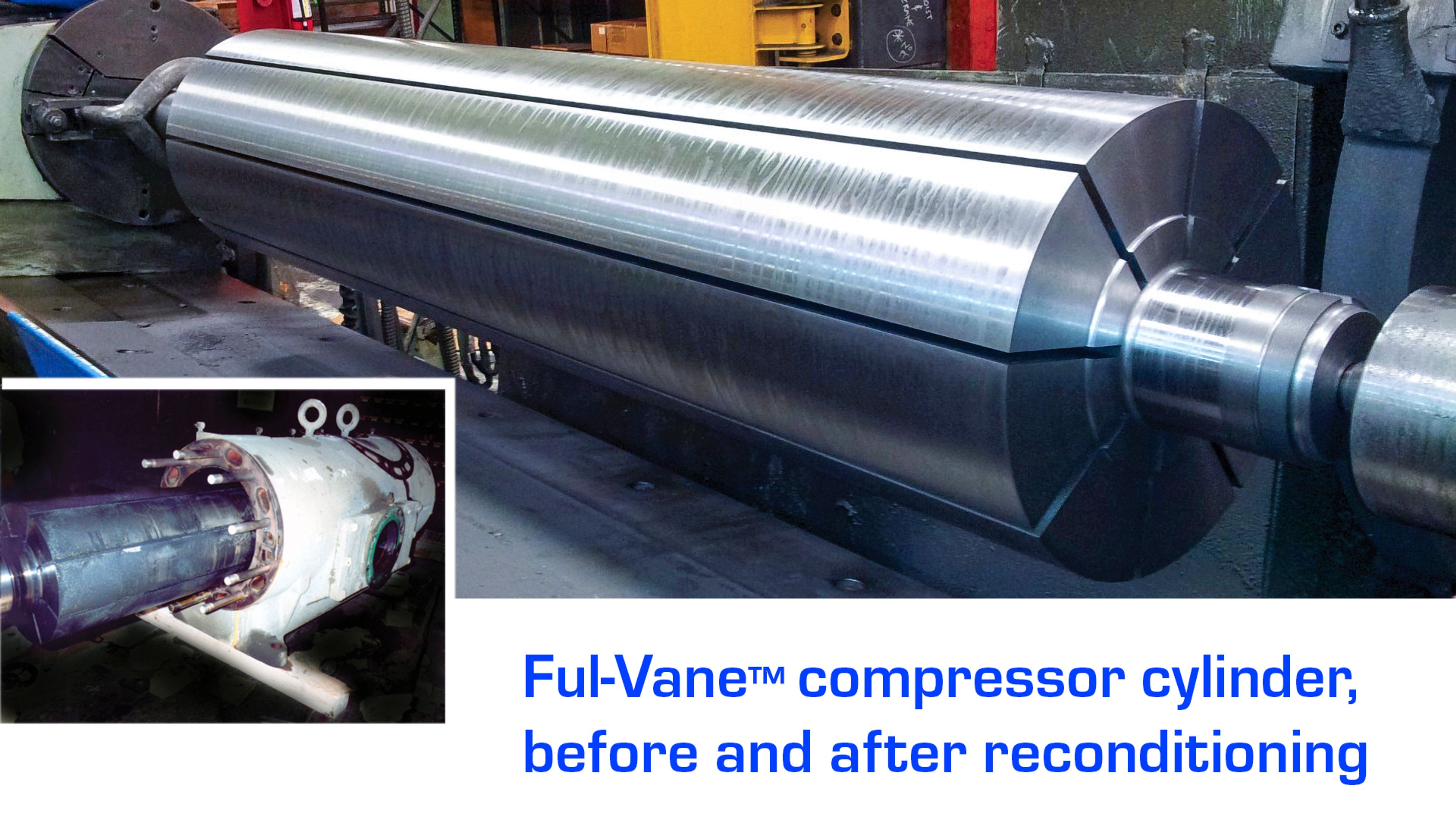
Compressor exchange
Ful-Vane™ compressor exchange program
When your compressor breaks down, you can’t afford to wait months for a replacement. You need to get back to business as usual – and fast. Our compressor exchange program enables you to do just that and also offers significant cost-savings over other replacement options. How does it work? We take in your worn Ful-Vane™ compressors and replace them with OEM factory reconditioned and warranted replacements, available from the huge stock kept at our plant in Northampton, Pennsylvania plant and in Certified Service Centers situated across the US and Canada. All you have to do is call us to confirm availability. We’ll ship a replacement compressor right out to you.
Hot Swap bearing assembly
Hot-Swap bearing assembly for 3-piece pump screws
Even with a high-quality machine like a Fuller-Kinyon® pump, it’s not a question of if a bearing assembly will wear out, it’s a matter of when. The typical removal, rebuild, and reassembly of a worn bearing unit can take up to 7 to 10 hours, depending on the extent of wear to the original parts. Instead of taking the time – and time is money – to rebuild a worn bearing unit from scratch, you can maximize the benefits of the 3-piece screw in your Type M Fuller-Kinyon Pumps by keeping Hot Swap bearing assemblies on your shelf. Having complete bearing assemblies readily available cuts downtime by more than half. In fact, you can be back up and running in approximately 3 hours.
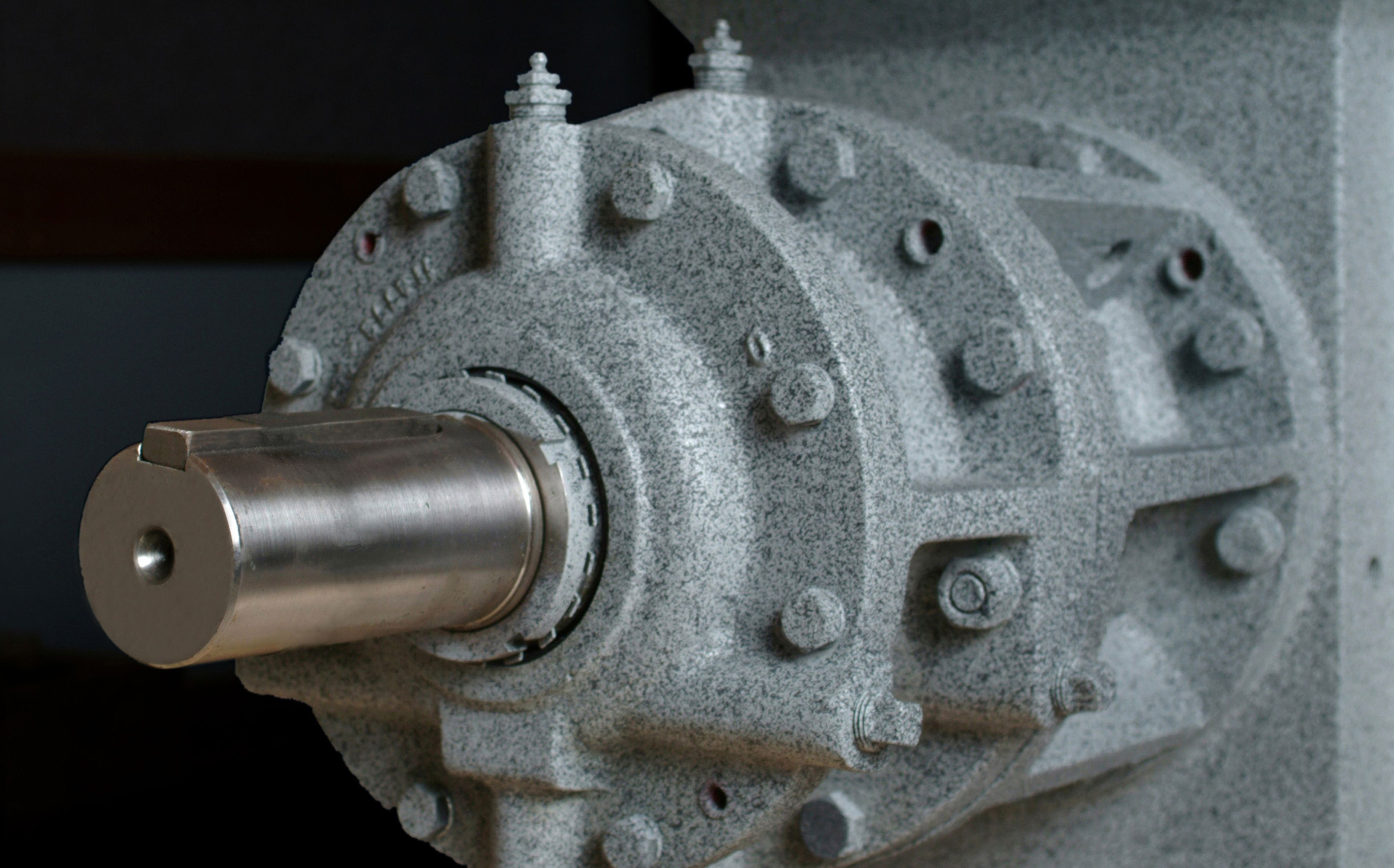
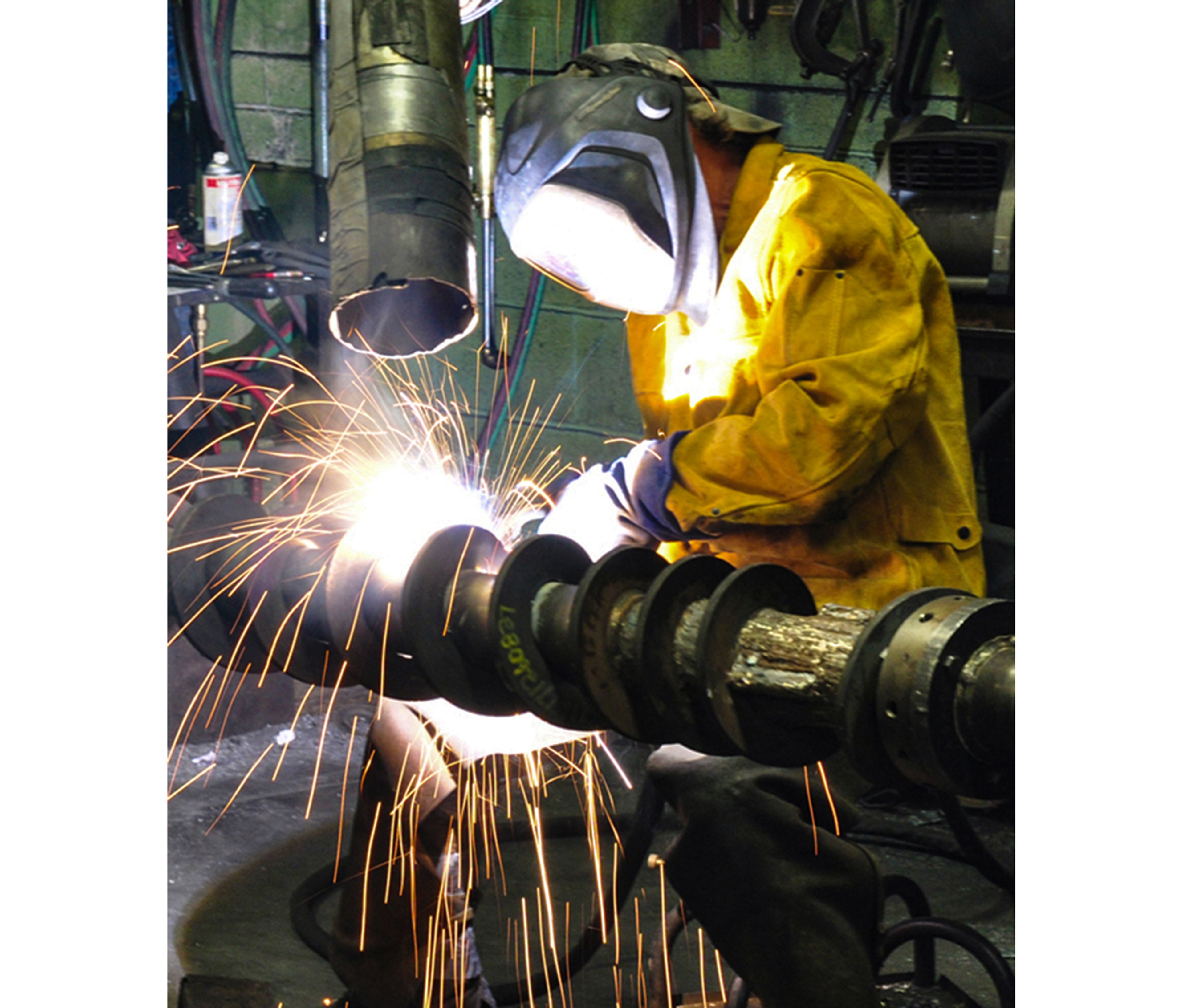
3-piece screw upgrade
3-piece screw upgrade for FK Pumps
If you have an older Type M Fuller-Kinyon pump manufactured prior to the year 2000 in your plant, then it probably uses the single-piece screw design. The screw is a wear part and will need replacing from time to time. This is a fairly difficult procedure with a one-piece screw – disconnect the coupling, expose the bearings and seals to a dusty and dirty plant environment, and then pry the screw out of the drive side bearings. It could take three technicians 10 to16 hours to complete a screw change-out with this design. That’s a significant cost, both in man-hours and downtime. To eliminate these issues, we introduced the 3-piece screw design. This design splits the pump screw into three sections that are bolted together at the balance wheels of the screw. On each end there is a stub shaft that is contained inside the bearing housing assembly. To change out the center screw, you simply remove it from these ends. The man hours and downtime required to carry out the task are dramatically reduced – down to two technicians and 3 to 4 hours.
Spare parts
Spare parts stocking program
When you join the 12-month program, we decide together on the optimal inventory mix for your facility ($100,000 minimum), whether that’s parts required for normal preventive maintenance or for an emergency. We will then ship that inventory out to you – but until those parts are put to use in your plant, ownership of the stock stays with FLSmidth Cement. The benefits are clear - you have the reassurance of knowing that the spares you need for the year are on site, ready to go when you need them. No lengthy waits for spare parts, or high costs for emergency deliveries. At the same time, your capital isn’t tied up in that spare parts stock – you only pay for what you use until the end of the contract, when we’ll invoice for any remaining inventory. Spare parts – and spare funds The SPSP is both convenient and practical. You have the parts you need, when you need them. Once a part is put to use, just let us know and we will send you the invoice. But if a part stays on the shelf, you don’t have to pay for it until the end of the contract. Joining the SPSP is simple. Just contact us to set it up and together we’ll decide what you need. Once you’re enrolled and you’ve signed the SPSP agreement, we will ship the inventory to your facility.
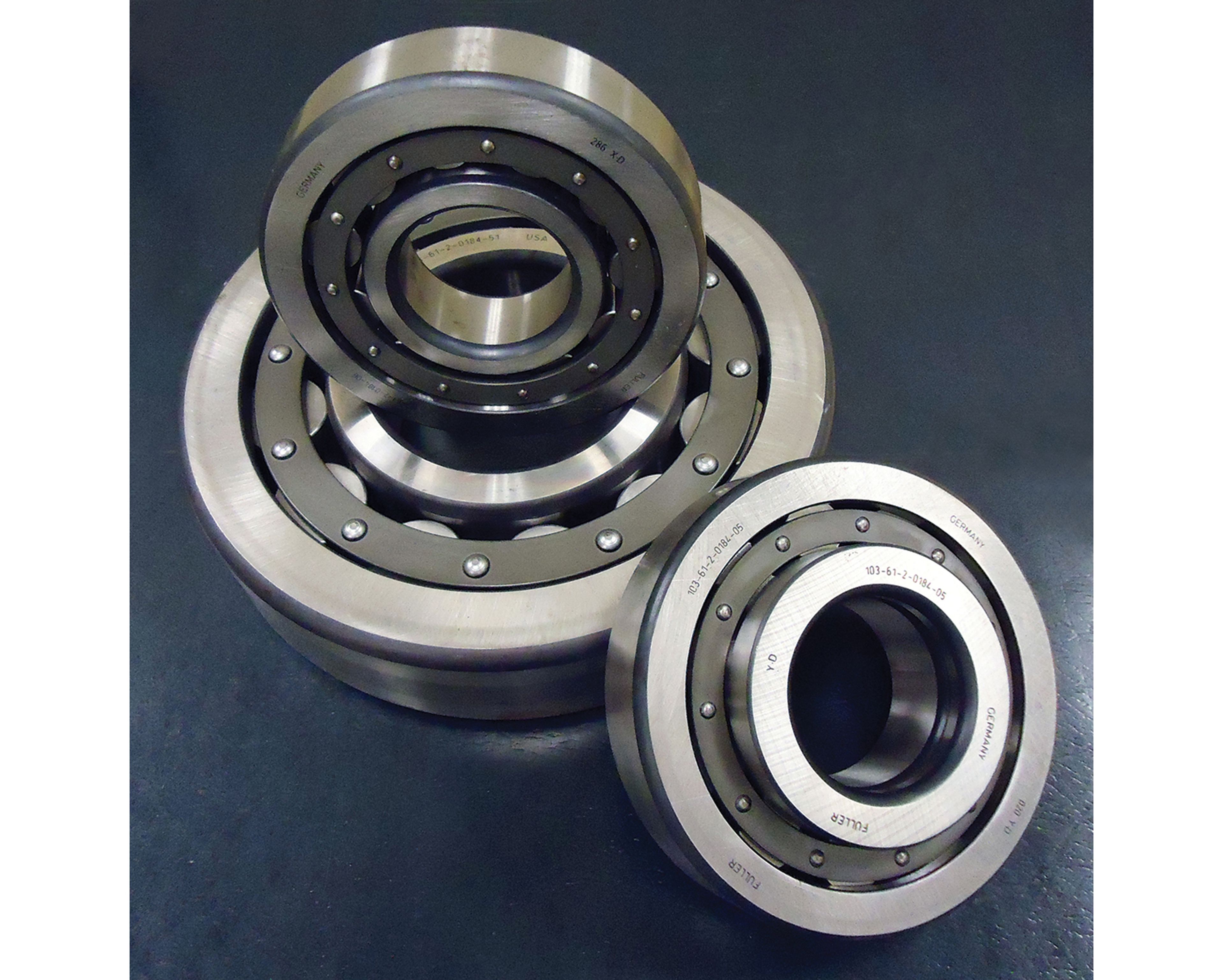
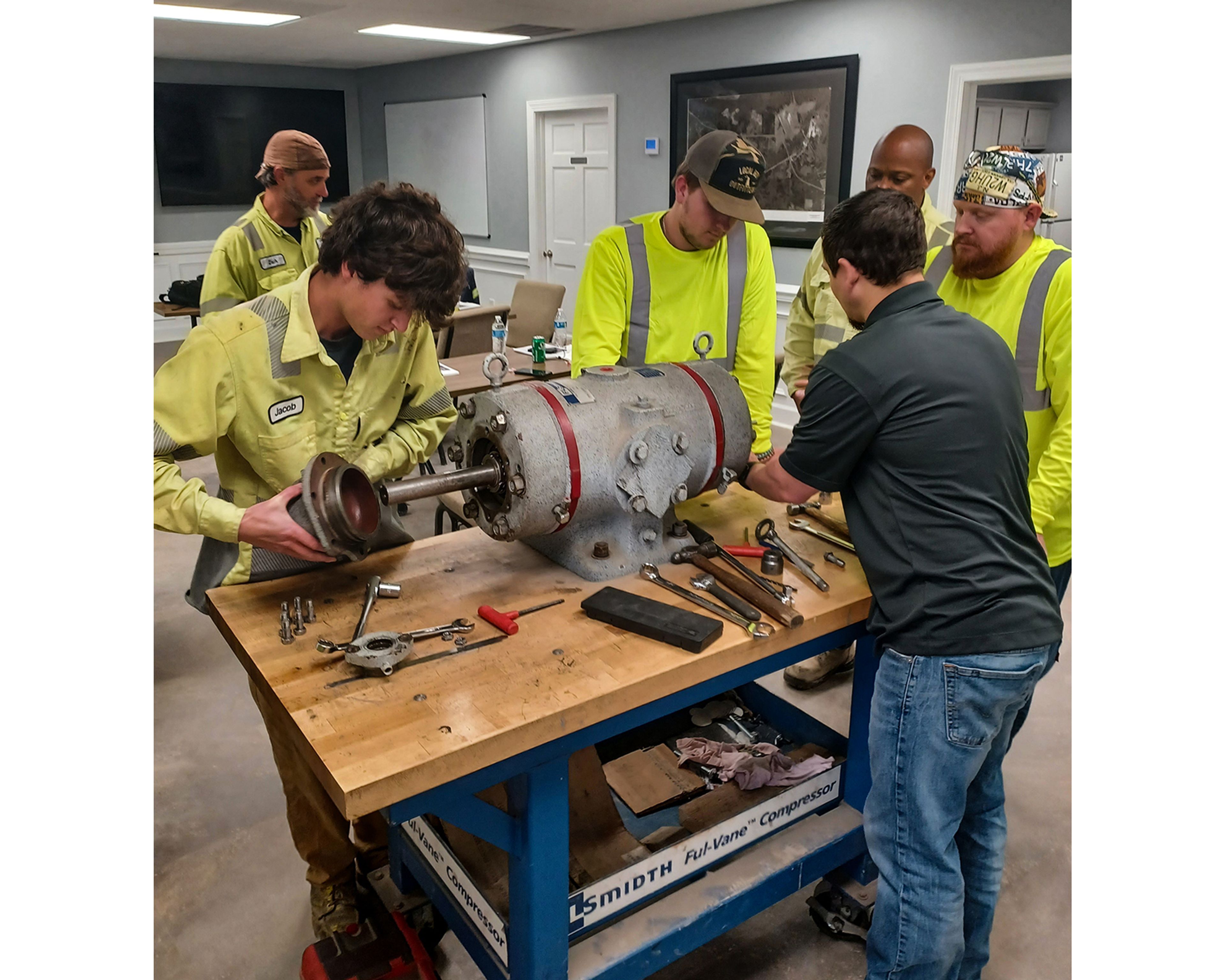
Training
FK Pump and Compressor training at your plant
We think that wherever possible, training on plant equipment ought to involve getting your hands on the actual equipment. But that’s not always possible on a working plant. So for this two-day roadshow training, we’ll ship an equipment container to your facility ahead of the seminar. Each participant will be provided with manuals highlighting the material covered for both the pump and compressor training sessions. Do you have a specific training need? Ask us about customized Pneumatic Transport training. Part of the training will take place in a classroom, but for the rest of the time you’ll have the opportunity to learn with full-size equipment, including: - Fuller-Kinyon® (FK) M Pump - Ful-Vane™ Compressor - Fuller-Kinyon® H pump - SK™ Diverter Valves - FK Pump AutoLube System If you have pneumatic conveying concerns, we’ve got you covered. From an on-site advisory service to a 24/7 helpline, an FLSmidth Cement service engineer can help you get the most from your equipment. Call us 24/7 at 800-795-6825.
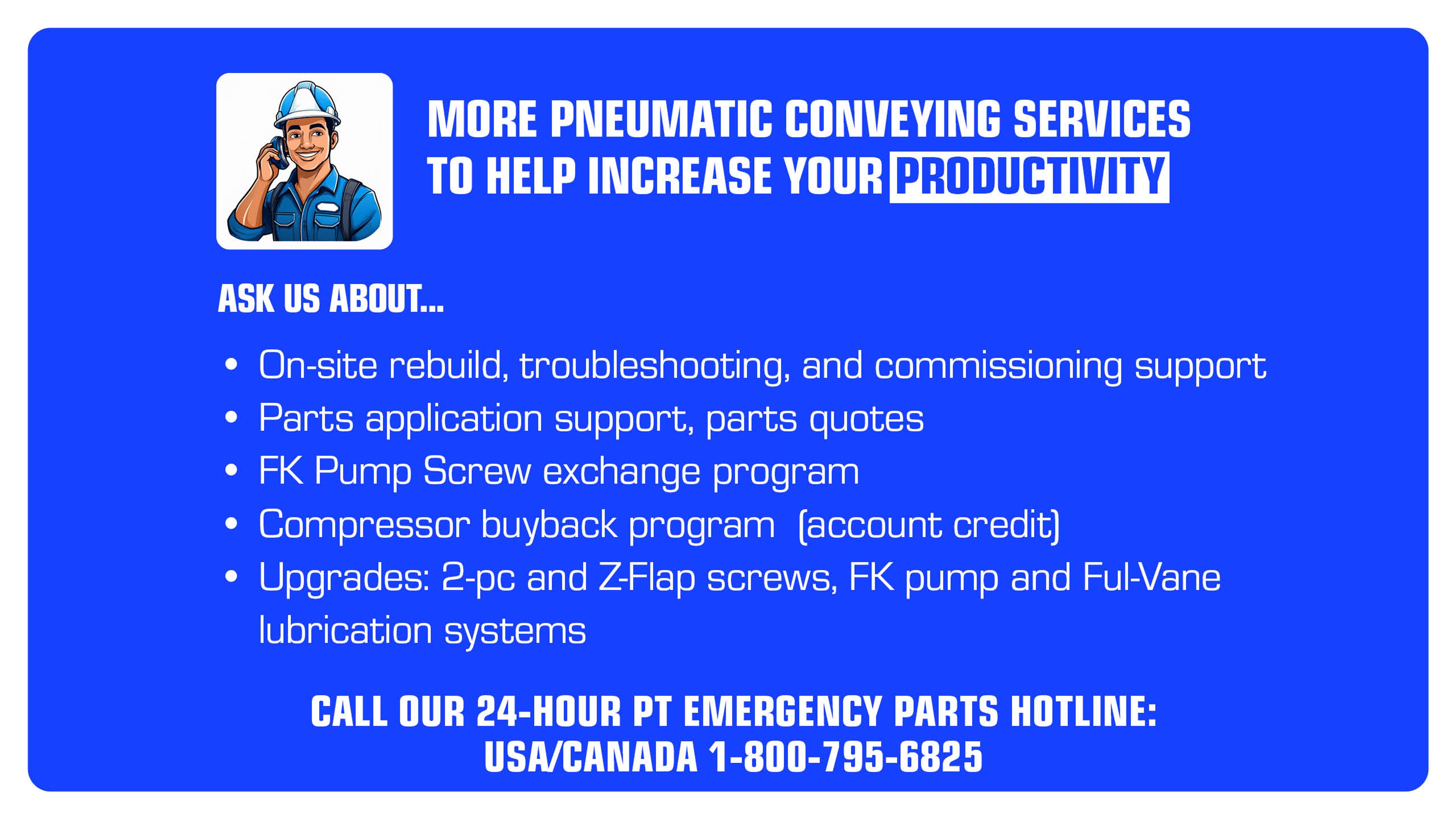