article
Carbon capture – we’re not there yet, but where are we?
Kiranmai Sanagavarapu, Program Manager - Clinker Decarbonisation, and David Jayanth, Project Manager, Carbon Capture, FLSmidth Cement, share highlights from a cross-industry panel discussion on carbon capture in the cement industry, with a focus on the US.
Carbon capture is integral to the cement industry’s plans to achieve Net Zero cement by 2050. Yet, the technology is still in the relatively early stages of development, with very few cement plants even close to achieving carbon capture at an industrial scale.
With the clock ticking on the cement industry’s environmental targets, we gathered a select panel of experts from both the cement production and supplier side of this story to discuss progress so far, challenges they’re currently facing and on the horizon, and what needs to happen to make significant progress on carbon reduction. We were fortunate to be joined by:
- Gina Lotito – Chief Sustainability and Innovation Officer, GCC
- Dave Carichner – VP Engineering, CalPortland
- Hamed Maraghechi – VP R&D and Decarbonization, CalPortland
- Prabhjot Bal - Director, Environment, Social & Governance (ESG), Summit Materials
- Sathish Krishnamoorthy – Director Project Engineering CCUS, Heidelberg Materials North America
- Andrew Baxter – President of Sustainable Energy Solutions, Chart Industries, Inc.
- Duncan McSorland – Business Development Manager - Carbon Capture & Hydrogen, Honeywell UOP
The discussion was lively and insightful. We’re grateful for the contribution of all the panelists, and for their permission to reproduce some of the findings from that discussion here.
Finding 1 – Cement companies can’t afford to wait
The discussion began with some plain talking. Carbon capture technology isn’t at the desired Technology Readiness Level (TRL) yet, but some cement companies will have to make the leap anyway to try to meet their 2030 targets. This requires sizeable investment with little to no return.
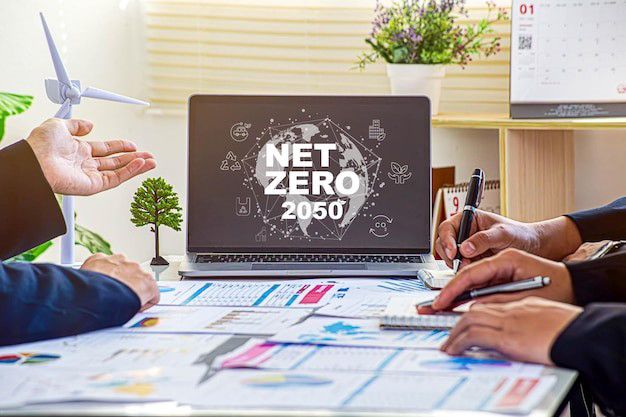
“Given Heidelberg Materials’ 2030 targets, we are working primarily with Amine-based technology for Carbon Capture,” said Sathish Krishnamoorthy, who put the TRL of carbon capture within the cement industry at about 7, but outside of the cement industry as high as 9. “Right now, we’re focusing on how to achieve the 2030 targets with the technology that is available to us. Additionally, we continue to monitor other maturing technologies that are promising, but also have a lower technology readiness level”.
Gina Lotito agreed. “We built a technology matrix to help with the decision-making process because it’s obvious that there isn’t going to be a ‘one size fits all’ solution – there will be different technologies that suit different plants. Based on our research, we’ve focused our decision-making on the long-term operational costs – effectively, the energy input required, because these systems are energy intensive. That’s been the deciding factor for us. The technology we’re looking at is only at a TRL 6, but we’re expecting the efficiency to improve as the technology matures.”
We asked if the cement plants anticipated having to change technologies as it evolves, and it was clear that the future of carbon capture for cement is still deeply uncertain.
“That’s why no one wants to be the first,” said Dave. “Because that’s the model that will likely have to be replaced.”
“Cement manufacturing has evolved a lot in the last 60 years with significant advances in energy and operational efficiency, and continues to develop,” said Sathish. “Similarly, we believe the capture technology will continue maturing and hopefully will become more cost-effective as it does so, so that we can meet our 2050 goals.”
“We’re not waiting,” said Gina. “We're working towards a solution. And in the meantime, we’re also pursuing other routes to reduce carbon, like increased energy efficiency, blended cements, and alternative fuels.”
Finding 2 – Storage is a major issue
The term ‘carbon capture utilisation and storage’ is often thrown around as a single solution, but the reality is very different. Carbon capture is one thing; storage and utilisation are almost like separate projects.
“Right now, we are focusing on the storage itself,” said Sathish. “This is the foundation. Without storage, we can’t proceed with any of the available capture technologies. We have some plants that have potentially good storage options, but overall storage across USA is going to be a challenge– and without the support infrastructure in place our hands are tied.”

Gina and Dave both agreed that there aren’t sufficient answers yet on sequestration. Dave made the point that the requirement in California is for 100 years of storage, whereas in other states it’s half that, putting Californian producers at a disadvantage compared to their peers.
“I think, after 2030, the carbon capture technology will be there. But will the infrastructure be in place? I think that's the limiting factor for us in the US,” said Gina. “I have a feeling they’re further ahead on this in Europe.”
Finding 3 – Utilisation is not always a valid option
None of the producers were especially optimistic about the scalability of utilisation projects in the near term, from both a practical and regulatory standpoint. CalPortland is currently working on a project to mineralize CO2 into recycled concrete materials, but cast doubt on its widespread application.
“Globally speaking, I think that the availability of the sorts of minerals or calcium that can bind CO2 is not sufficient, so utilisation is limited – but it’s not impossible,” said Hamed. CalPortland is building a very small-scale demonstration plant to explore how they can recycle concrete. “We think it has the potential to be used back in the cement mix. And of course, CO2 can be used to make other products, so we are exploring ideas at the moment.”
Cement producers are also navigating a regulatory framework that sometimes struggles to distinguish between sequestration and utilisation. In California, for example, there is no accepted route for utilisation other than aviation fuel. “We’re stuck trying to work with rules that aren’t well defined,” said Dave.
Gina made the point that Science Based Targets also have clearly defined rules on utilising carbon. “It’s another one of those things where we’re having to balance the economics, but at the moment it’s looking like the long-term option will be sequestration,” she said.
From the suppliers’ perspective, it was reassuring to hear that in some cases suppliers can help coordinate between the carbon-emitting industry and the CO2 end user.
“At Chart, we have a pretty broad presence in a few different areas,” Andrew said. “We participate in hydrogen liquefaction and hydrogen transport and storage through different parts of our business. We also have most of the traditional industrial gas companies as customers of ours – people who are already moving CO2 for use in food and beverage or industrial sources. So we often find ourselves coordinating and asking, ‘what can we do?’ Plus, our technology enables us to achieve very high purities and the purer the CO2 is, the more options you have for utilisation – for example in alternative fuels or food and beverage markets.” Andrew also noted that in recent years the traditional CO2 market has experienced severe shortages, pushing the price of traditional CO2 up – a situation that makes achieving the right specifications for F&B application especially appealing.
Duncan noted that Honeywell is supporting early-stage studies for a few projects where some of the CO2 will go to sequestration and some to utilisation, noting that “we have both CO2 capture technologies and Methanol to SAF (Sustainable Aviation Fuel) technology. In the U.S., we have a publicly announced methanol to SAF project. With CO2 to eMethanol to SAF (versus Fischer-Tropsch process to create SAF for example) we get an intermediate tradable product in eMethanol which is advantageous. Both eMethanol production from CO2 and eSAF production from eMethanol requires large amounts of green hydrogen, which is reliant on renewable energy – what do you do if the renewable energy input supply goes down, but your carbon emissions are still coming?” Additional sequestration capacity provides some flexibility here.
It’s an uncertainty the cement producers would like to resolve.
“Honestly, it would be awesome if we could go into green hydrogen,” said Gina. “If we could make it more available and get it to the point where we could use it in the calciner, that would be over half the thermal emissions gone. Of course, it’s very expensive. But we’re going to have to look at the books and figure out what makes sense. How much is it going to cost to sequester CO2 in the ground versus how much is it going to cost to produce green hydrogen?” Gina also asked how the alternative fuels market might evolve to help cover the cost of carbon capture. “At the moment, there’s a big focus on alternative fuels and the circular economy. It’s better than fossil fuels, but there are still emissions coming out of the stack. At some point, someone’s going to have to pay to capture those. I think the market will have to evolve to accommodate that. It’s going to be interesting.”
Finding 4 – State-to-state inconsistencies are going to be an issue
As noted by the differences between California and other states on sequestration, the regulatory framework doesn’t currently support cement producers. First, because it’s ill-defined, and second because the financial support isn’t sufficient for the level of investment required.
“We’re currently conducting two FEED (front end engineering and design) studies with grant funding from U.S. Department of Energy, which leverages a substantial contribution with our financial commitment” said Sathish. “The Section 45Q carbon sequestration tax credits provide a significant benefit as well, but they’re not fully sufficient at this time to support the capital and ongoing investment for full scale capture and storage. We must seek and develop additional, and creative, enablers to support these operating cost increases associated with carbon capture.”
Gina expressed concern that the lack of consistency across the states may cause a problem with carbon leakage from one state to another, and with permitting. “It would be really nice if there were more guidelines and more consistency. We also need a carbon market that works across the country. Personally, I think the industry should also be lobbying for a different type of 45Q tax credit. The government recognises we are a ‘hard to abate’ industry, but we’re not getting the support we need.”
Finding 5 – The cement industry requires tailor-made solutions
Carbon capture didn’t start in the cement industry, and it has arguably been slower to take off there than in other industries. We asked the suppliers what makes the cement industry more challenging than other industries.
“The cement industry is different than other applications in a few important ways,” said Andrew. “The concentrations of CO2 are different. The process is less homogeneous than a lot of other industries. You can't really predict what's coming out of the stack at one plant versus another plant without going and talking to the producers. So that's a core challenge: we have to design every application fresh each time. Also, there are challenges with contaminants, some regions face water scarcity, and the availability of utilities is not universal. We are anxious to scale up quickly and preparing to meet these many needs at a larger scale within the timeframes we're talking about here.”
Duncan points out the bottleneck in the process is often engineering resources and skills – as it is across many industries. “A lot of operators come to us thinking that you can get an off-the-shelf kind of answer, but you've kind of got to re-engineer the solution each time, which is a lot of effort. This is the bottleneck in our business. We need more people to look at every cement plant and every power plant and every steel plant and every CO2 emitter and they’re all going to be at least slightly different. I'm sure it’s possible to have a reasonably standardised concept by industry, but it's not going to be optimised.”
“This is something that FLSmidth Cement has brought to the table in some of the projects we've worked on together,” said Andrew. “They can provide that process expertise, audit the plant, and provide a full picture for optimisation, looking at cement production and carbon capture together and what can we do to bring the cost down, bring the energy down for that whole process as much as possible.”
"The options for the cement industry is to either employ an end-of-pipe capture technology or to implement integrated capture solutions which require adjustments to the cement manufacturing process." said David from FLSmidth Cement. "The choice will be plant specific and is driven mainly by cost, energy penalty, technical maturity, and abatement potential. To reduce costs associated with end-of-pipe solutions we look to make low-risks adaptations to the cement process to enhance compatibility with the capture plant. Simultaneously, integrated solutions like oxyfuel, indirect calcination and electrification to enrich the CO2 concentration in the cement flue gas are being developed.Across all of this, there is one universal truth: there must be a pull from market to justify the development cost. Our first large-scale pilot on oxyfuel was successfully tested nearly a decade back, but the project was shelved as the market was not ready back then.”
Finding 6 – Public outreach and information sharing are required to keep pushing forwards
We asked everyone on the panel to tell us what they would like the public to know about carbon capture for the cement industry, and got a range of answers.
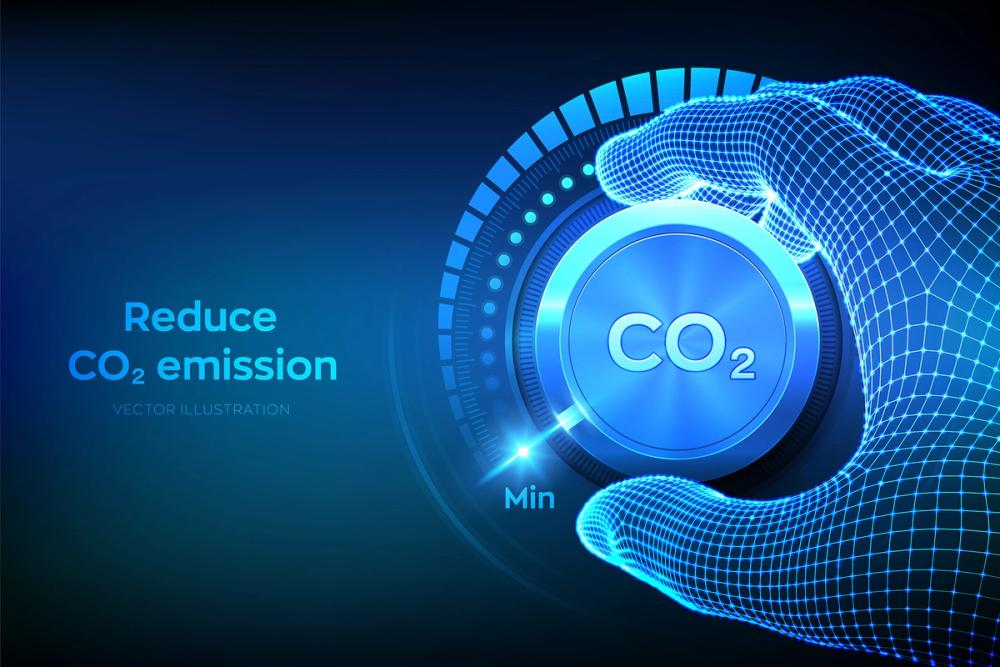
“Most plants invested significantly over the years in developing supportive and close relationships with their local communities, but when we’re talking about carbon capture and storage the impact is potentially wider – the carbon dioxide will need to be transported and sequestered probably outside of that community,” said Sathish. “It’s critical that we engage with the communities that will be affected and work together in a harmonious, transparent way. Within our own industry, I’d say the same actually – if we could share knowledge, especially around the work in our community and stakeholder engagement, we can make substantial progress.A rising tide lifts all boats.”
Gina agreed and added, “I also want everyone to know that carbon capture is not a one-size-fits-all technology. There won’t be one ‘best available technology’ to fit every kiln system. We need site-specific solutions and we need regulations that accommodate that.”
“Let’s also remember that concrete absorbs CO2 and is an important part of the green transition,” said Dave Carichner, earning a smile from all participants.
Andrew offered up an inspiring quote for us to all take home: the future can’t be predicted, but it can be invented. “My takeaway is there is a long road ahead of us, and some challenges there, but we’ve never had more going the right way than we have right now. We’ve got people stepping up to pave that road. I’m optimistic that we’ll see all the parts and pieces come together over the next 3 – 5 years. I’m excited to be working with those on this panel and others out there to help make that happen.”
A fitting way to end an excellent discussion. Our thanks to all who participated.
This article first appeared in the April 2024 issue of Word Cement.