article
Collaboration leads to success at Ozinga’s new terminal
Ozinga is a fifth-generation family business that has been supplying the construction industry throughout Illinois, Indiana, Wisconsin, Michigan and South Florida for almost a century. What started as a small coal yard has grown into a premier supplier of concrete and materials solutions. As business has grown, the company needed a terminal in the Port of Palm Beach to support their concrete business. This was a challenging location. The site is in a tourist area subject to high interest from local government with considerable desire to maintain a pleasing aesthetic. It was also a complex project because Ozinga wanted to utilize a mechanical ship unloader with a pneumatic conveying system – the first time, to the team’s knowledge, a solution quite like this had been attempted worldwide. Thankfully, Ozinga had already assembled the perfect team to pull it off following a successful first project in Chicago with Dome Technology and FLSmidth Cement.
The Port of Palm Beach project
“This project was similar to the Chicago project in terms of capacity, but the challenges were new,” explains Mark Jackson of Ozinga. “The dome was going to be the same size, with the same Ful-Floor™ reclaim system, but the terminal position was very different. It’s a much more public setting, for one thing, so we had to go through a long design process to ensure we could get the permit for the build from the city, but we also wanted to connect a pneumatic transport system to the Siwertell mechanical ship unloader, which was a challenge. To our knowledge, this had never been done before. Having worked so well with Dome Technology and FLSmidth Cement on the Chicago South Side project, we were confident we could make a success of this project too.”
The desire for a pleasing aesthetic meant that Ozinga and Dome Technology had to work closely with the Port of Palm Beach and city officials to achieve an approved silo design. That meant hiding the mechanical fixtures behind a parapet wall on top of the dome, giving the silo a cylindrical appearance.
“We’ve never done anything quite this architecturally sophisticated for an industrial project,” says Bradley. “It’s a one-of-a-kind project. In order to attach a parapet wall on top of the dome to hide the mechanical equipment, we needed a vertical edge to attach it to. We developed a low-profile dome concept, which includes a structural steel ring at the top of the dome to constrain the geometry between the top of the dome and the parapet wall – effectively a screen to improve the appearance of the dome. We’ve used this design on smaller applications in the past but never on an industrial scale. It took several design iterations to get the profile just right to obtain the needed tonnage of storage while ensuring the height of the parapet wall was sufficient to prevent anyone seeing the mechanical equipment on top. We created a 3D model of the project and checked the line of sight from several different points on the ground to be sure we’d got it right. In the end we settled on an 18 ft high aluminum parapet wall. The roof of the DomeSilo is constructed from a second piece of fabric – the same airform material the vertical DomeSilo wall is made from – that attaches to the steel ring at the top of the first section of the dome.”
The parapet wall gives the dome the appearance of a cylinder and hides the mechanical equipment from view.
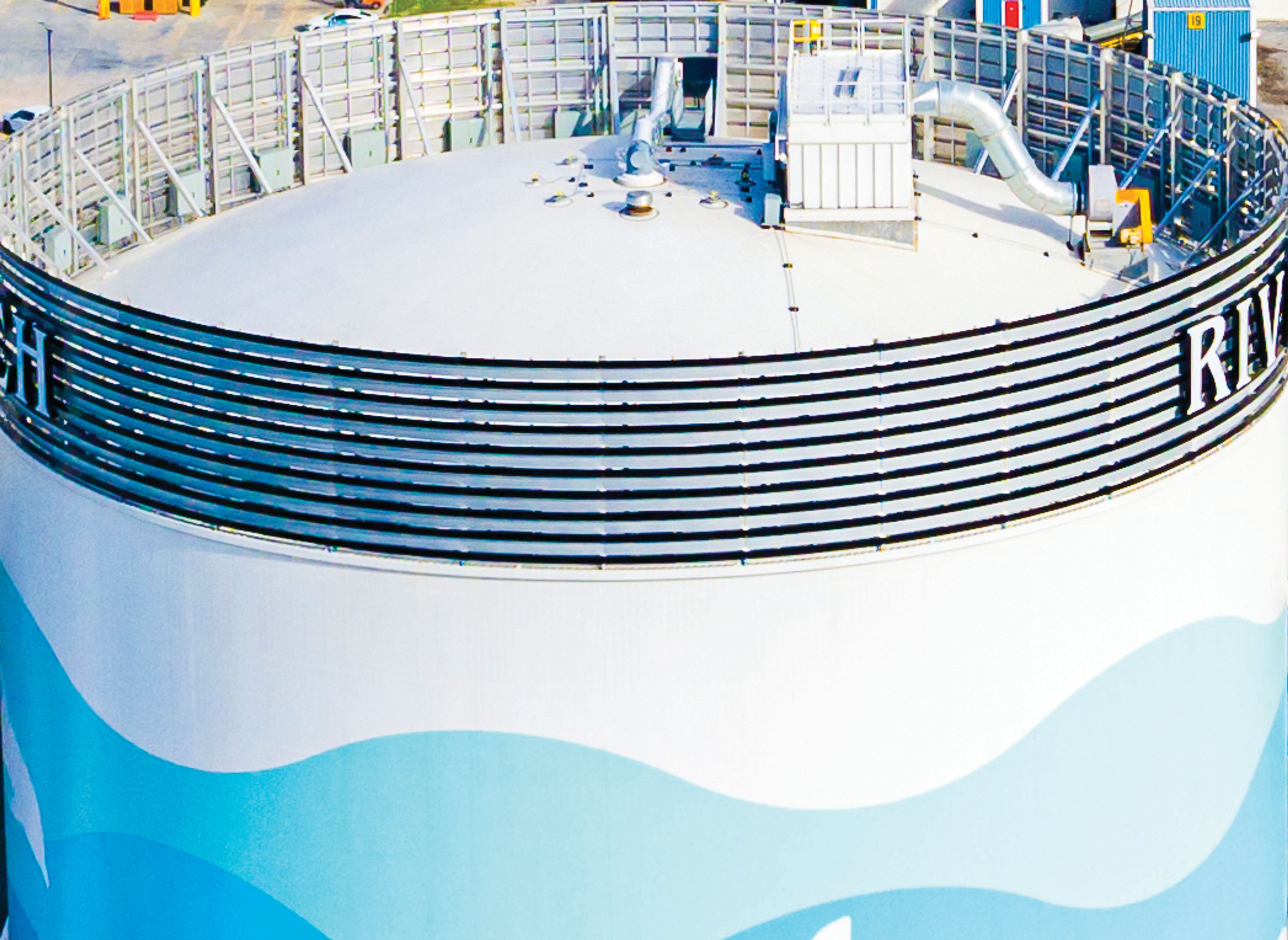
Making the dome
Having received the permit in December 2021, work began on site. The deep foundation contractor installed 500 auger cast piles 48’ deep to support the weight of the 50 000 MT dome.
The air control valves for the Ful-Floor™ reclaim system are contained in a single tunnel beneath the dome.
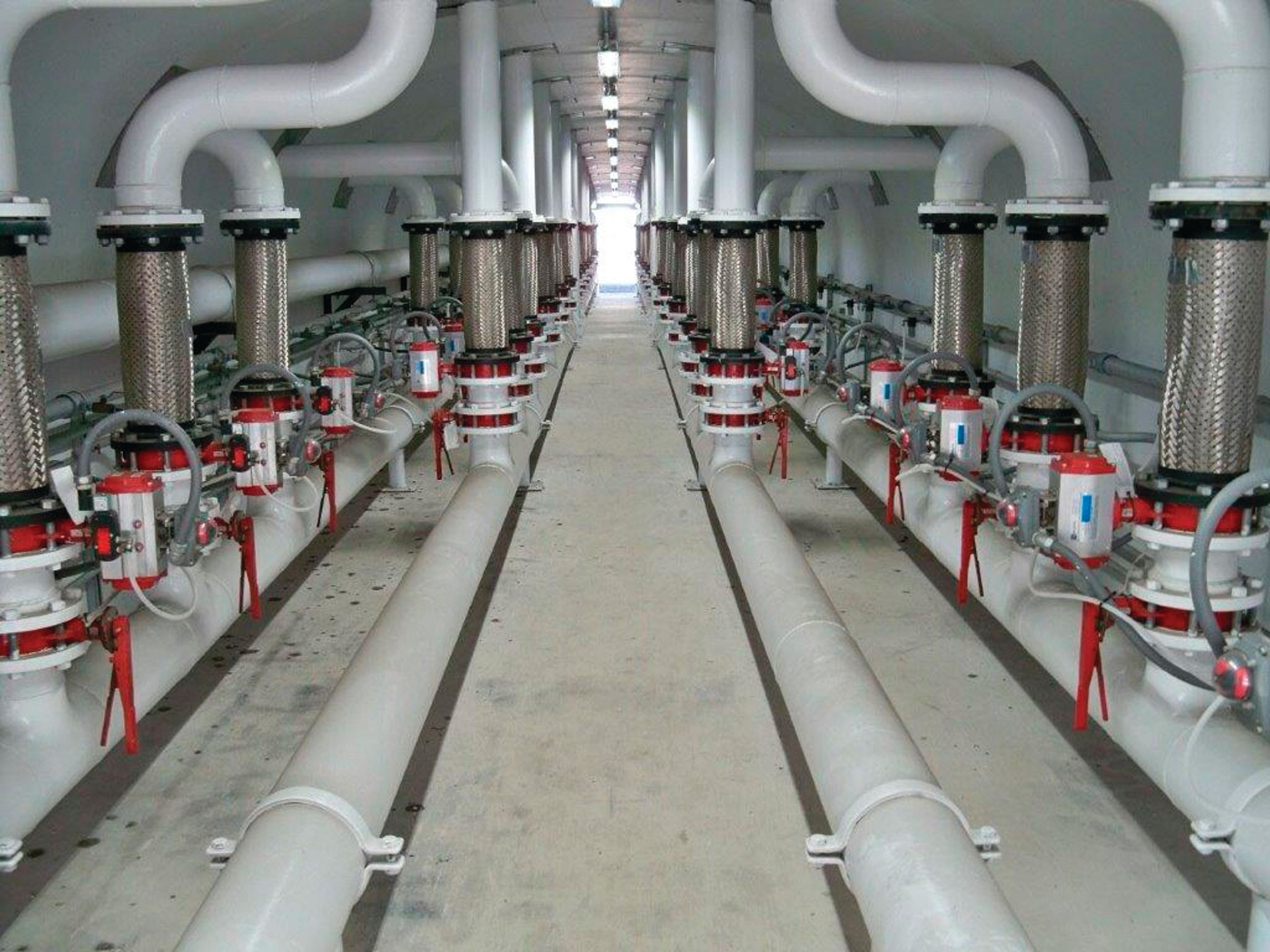
In traditional Dome Silos, the PVC airform is bolted to the ring beam before being inflated with large fans. With this project, because of the pre-attached additional steel ring at the top of the silo wall, cranes were required to stabilise the dome as it inflated. Once inflation was complete – which took about 3 – 4 hours – work could begin inside the dome, with concrete and reinforcing steel rebar applied to the inside of the fabric until the required thickness was reached. The PVC airform remains in place, becoming the outer waterproofing membrane – and for this project, the surface on which the decorative finish was placed.
“The dome took about a year and a half to build, from permitting to commissioning. We’re very proud of the end result, and of the teamwork that got us there,” says Mark.
Concrete and steel rebar are layered inside the airform to achieve the required strength.
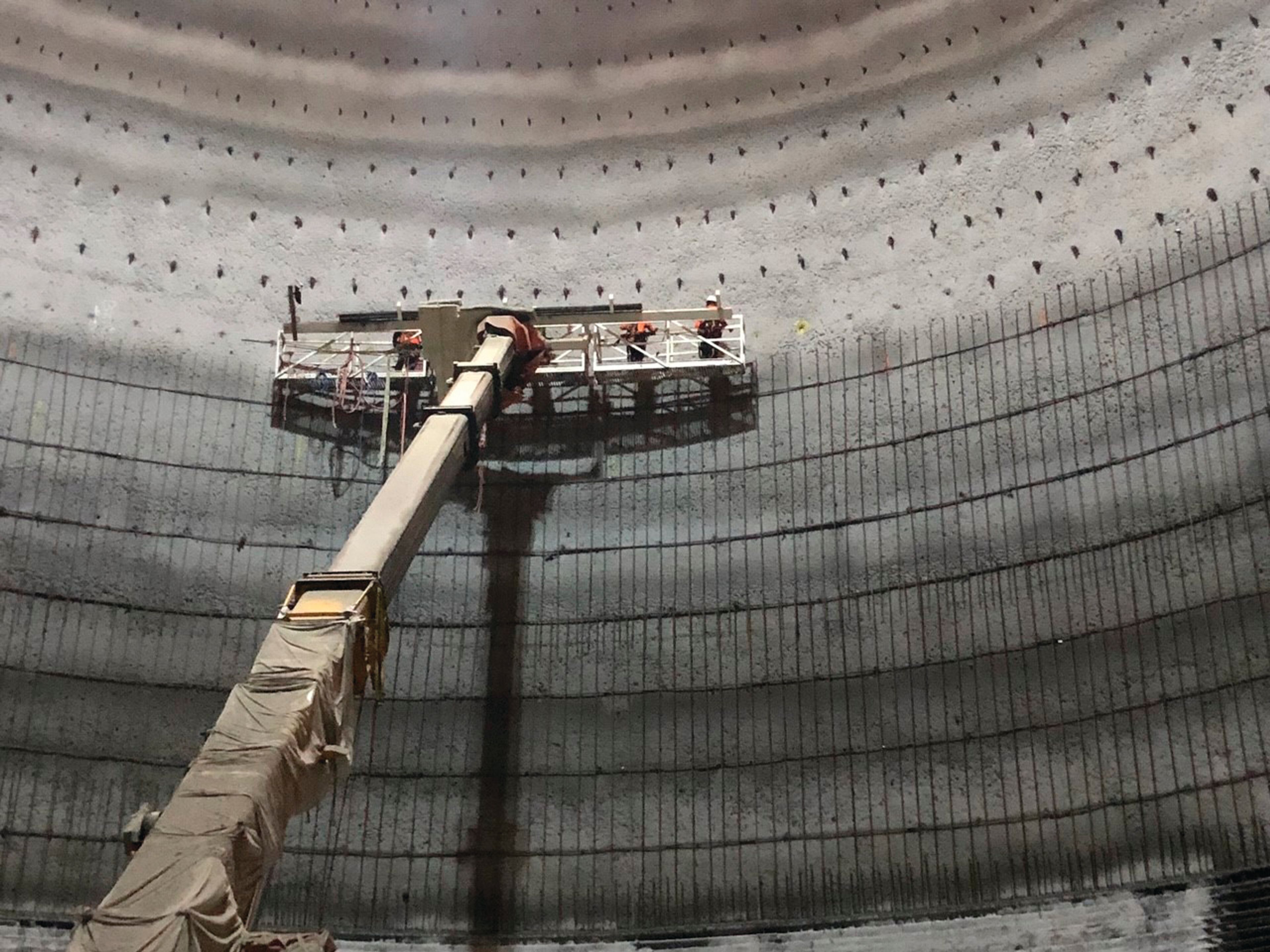
Connecting with the Siwertell
One of the most challenging parts of the project was integrating a new pneumatic transport system with the Siwertell ship unloader. With cleanliness a priority, Ozinga wanted to convey product from the ship to the dome fully pneumatically, which meant figuring out a way to connect the FLSmidth Cement 'N' Pump with the Siwertell ship unloader.
“The Siwertell ship unloader is a mechanical conveying system,” explains Jason Heiser, head of sales and support for FLSmidth Cement’s Pneumatic Transport Line. “But Ozinga wanted to use a pneumatic conveying system to reduce dust and keep a cleaner environment. It was a real collaboration between our team, Siwertell, Ozinga and Dome Technology, to create a solution that worked for everyone.”
That solution was a Fuller-Kinyon® (FK) 350 ‘N’ Pump with three 500 hp Ful-Vane™ Compressors, the Ful-Lube™ lubrication systems and cooling systems. This was all designed to fit into a purpose-built building that was designed, then constructed under the highway bridge on site before it was moved into place under the Siwertell.
“This is a big building,” said Mark. “It’s about 40 ft by 100 ft and it weighs over 100 tons. We used heavy hydraulic moving equipment to lift it up and drive it to the port where the Siwertell was positioned to receive the building. The building is connected to the Siwertell in four locations, and everything fit perfectly.”
House moving equipment had to be brought in to move the compressor room.
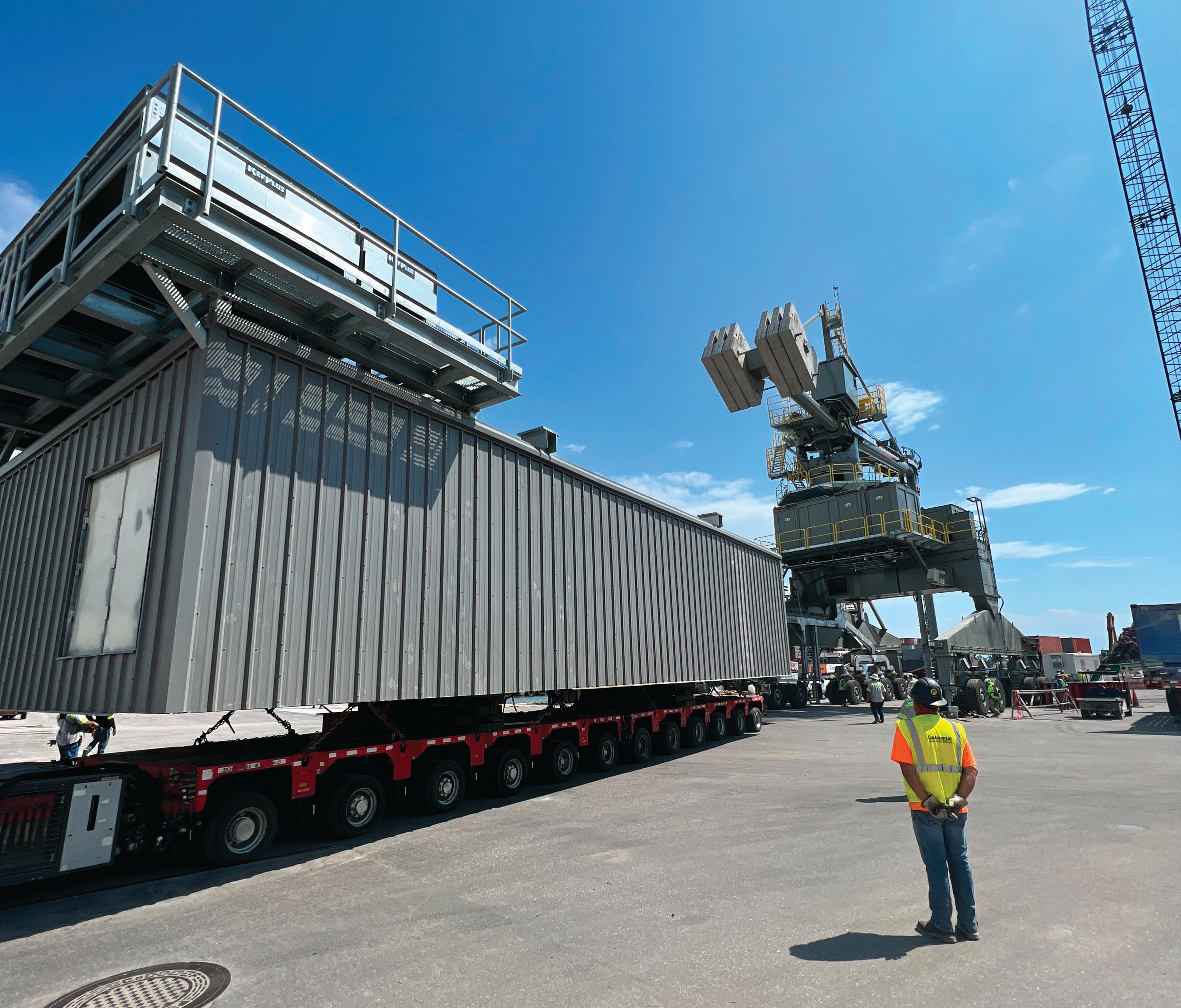
Electric power is distributed via the Siwertell into the pump and compressors, generating sufficient energy to achieve discharge rate of 600 MTPH. The convey pipe then travels 1700 feet underground before entering the DomeSilo.
“This was a real feat of engineering,” says Bradley. “We needed to unload the ship at a certain rate but there was no existing way to connect the mechanical system with the pneumatic transport. So all of us – Ozinga, FLSmidth Cement, Siwertell and Dome Technology – worked together to bring the technology into a solution that worked for this project. It unloads mechanically; it transports pneumatically. We think it’s the only one of its kind in the world.”
99% reclaim and full redundancy
“This is our third dome across the company. In our first project we used a different reclaim system, which has turned out to be very maintenance heavy. So when we were building the dome in Chicago – and again in the Port of Palm Beach – we knew we wanted something with more redundancy built in,” says Mark. “The Ful-Floor fits the bill. The double dihedral crown in the middle, aeration system and twin outlets enable us to keep mechanical moving parts and people out of the dome.”
The Ful-Floor aerates different segments of the floor at controlled intervals, facilitating a balanced, even flow at the discharge points on the side of the DomeSilo. The importance of the twin outlets is really felt if one of the FK Pump transport systems outside of the DomeSilo is off-line. Discharge can continue from the other outlet while repair work is carried out, with no lost time.
The Ful-Floor™ reclaim system uses advanced fluidization technology to move materials smoothly and efficiently. Air is pushed through the Airslide® fabric, enabling material to flow like water, and the gentle slope directs the flow of material to the dual exits.
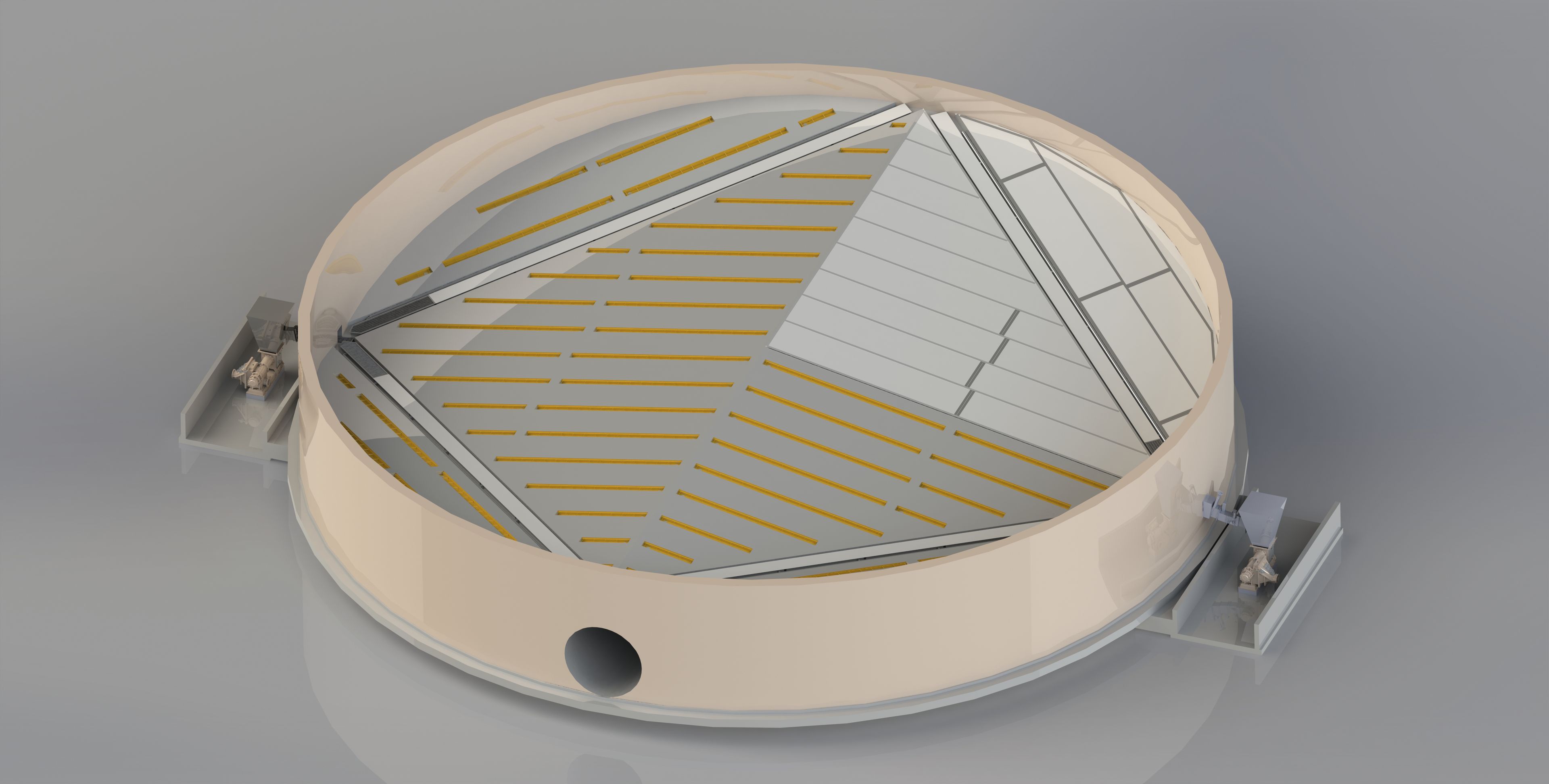
Aesthetics and weather-proofing
“This terminal had to be all things to all people,” said Mark. “A good amount of storage for us, with maximum reclaim for minimal effort. Clean, so we didn’t upset the local community or the environment with dust emissions. But it also had to stand up to the elements – of which coastal Florida has plenty – and to the discerning eye of the city officials. I’m happy to say we knocked it out of the park on all counts.”
- The dome is rated for 175 mph winds, and during the construction phase stood up to a couple of severe weather events with no difficulties.
- The finished appearance of the dome has won the approval of the city officials and the local community alike, with plenty of positive press for the beautiful ocean-themed design.
- The fluidised floor continues to work well at both the Chicago and Palm Beach terminals. The Port of Palm Beach dome is now in daily operation.
“The Florida coast is not an easy place to build,” says Mark, “but we worked hard and we worked well with our partners and with the city officials and the Port of Palm Beach to make this a success. We’re all really proud of the results.”
“Ozinga is a very sophisticated group. They drove this project and were instrumental in developing the overall technical solution,” says Bradley. “We all like to solve a problem, and this project presented plenty of challenges. It’s a testament to Ozinga’s innovative spirit that they were happy to take on so many firsts at the Port of Palm Beach, and we were proud to work alongside them for that.”.
“Let’s be honest, the challenging projects are often the most interesting ones,” said Jason. “I’d go so far as to say they’re the fun ones; particularly when you’ve got a great team of people working to solve those challenges together. It’s a real thrill to look at that terminal now and know we played a key part in bringing it to fruition.”
Note: A version of this article originally appeared in the August 2024 edition of International Cement Review.
Related Offerings