Out and about in Lisbon: EnviroTech 2024
World Cement’s inaugural in-person conference, EnviroTech 2024: Gateway to Green, took place in Lisbon, Portugal in March, and was an “excellent event with many encouraging initiatives highlighted for the decarbonisation of cement,” Christopher reported. “Energy efficiency, alternative fuels, and calcined clay appear to be gaining particular traction within the industry, while there is much preparation around carbon capture, storage, and utilization.”
A highlight of our experience at EnviroTech was Lars Skaarup Jensen ‘s presentation regardingthe very first FUELFLEX® pyrolyzer, at Mannok Cement in Ireland. The technology supports 100% fuel substitution in the calciner. Enabling the use of high-volatile fuels with high moisture content, large particle sizes, and varying calorific value – without impacting process stability – it also eliminates NOX in the calciner. Now, with a positive experience at the start-up of the second installation at Continental Cement’s Davenport plant in Buffalo, Iowa, USA, we will soon announce the full commercial release.
Staying with some of the topics picked up at EnviroTech, our first calcined clay plant is on-track at Vicat’s Xeuilley site in France. A second installation is currently in progress at CBI Ghana, with more orders expected. The first quarter also saw us sign a new contract for a HOTDISC® reactor at a Turkish cement plant, a cooler upgrade in the middle east and a new OK™ Cement Mill in the US.
Last but by no means least, the conference provided a great opportunity to meet with customers. “There was tangible interest in our vision for the future and what we are doing to help cement plants on their net zero journey,” said Christopher. “I was also extremely pleased to receive positive feedback from customers on the upcoming divestment of FLSmidth Cement.”
“Having come into the business only recently, I immediately saw the tremendous potential for growth divestment would bring and am only excited by the prospect,” Christopher continued. “But I always knew the real test would be how our customers viewed the decision. Now that the initial surprise has passed, I’m excited to hear many welcoming the news and recognising the benefits and opportunities that pureplay, under new ownership, will bring.”
In Italy and Germany: visiting Ventomatic and Pfister
Christopher’s European tour also took him to Italy and to Germany to visit our Ventomatic and Pfister locations.
In Italy, he visited our Valbrembo site on the outskirts of Bergamo, which has been the home of Ventomatic since 1974. Today, it houses Ventomatic’s administrative, technical, and sales teams, as well as a materials testing laboratory and R&D workshops. Christopher also visited nearby Presazzo, where we assemble, test, and dispatch Ventomatic packing and dispatch and Pfister feeding and dosing product lines at two neighbouring sites with a combined 8800m2 of workshop space.
The Presazzo workshops employ 80 skilled workers, who are cross trained across both product lines to deliver high-quality manufacturing capacity that can quickly respond to customer needs. Meanwhile, onsite spare part warehouses – including procedures for express shipping via airfreight for urgent orders – position us to deliver the high-quality, proactive service our customers expect and rely on to keep their production flowing.
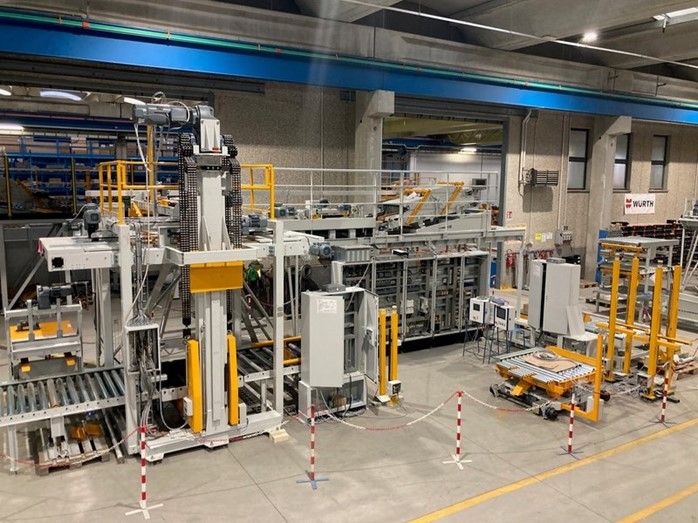
Christopher also dropped in to our Pfister headquarters in Augsburg, Germany, where he met with Pfister management and took part in the annual sales meeting.
“Pfister rotor weighfeeders have been a successful product for decades, and consequently we see an installed base of over 4000 feeders worldwide,” noted Christopher. “Of course, we want to grow sales and keep the total number of installations rising. But we don’t stop there. I was privileged to observe the pride the Pfister team take in their products. They want our customers to love their feeders and work hard to ensure every customer has the best possible journey throughout their feeder’s lifecycle, with top notch services and support, as well as a portfolio of upgrades that ensure their efficiency and operational flexibility support the way to reduced CO2 emissions.”
On the other side of the pond
In addition to his European tour, Christopher headed across the Atlantic to Pennsylvania, USA, where he visited the site where we produce blades for our Ful-Vane™ rotary vane compressors, as well as our pneumatic conveying test facilities.
“I was surprised by the number and range of materials we have tested over many decades – from petfood and pharmaceuticals to finished cement, and many other cementitious materials, such as pozzolan and fly ash,” Christopher said after visiting the test centre. “Most recently, we’ve also been testing calcined clay as part of the industry’s move to lower-carbon materials. These test capabilities are a key benefit for customers, who gain both confidence in the feasibility of moving their materials pneumatically, as well as the insight needed to optimise the design of their system, including component selection, layout, and power requirements.”
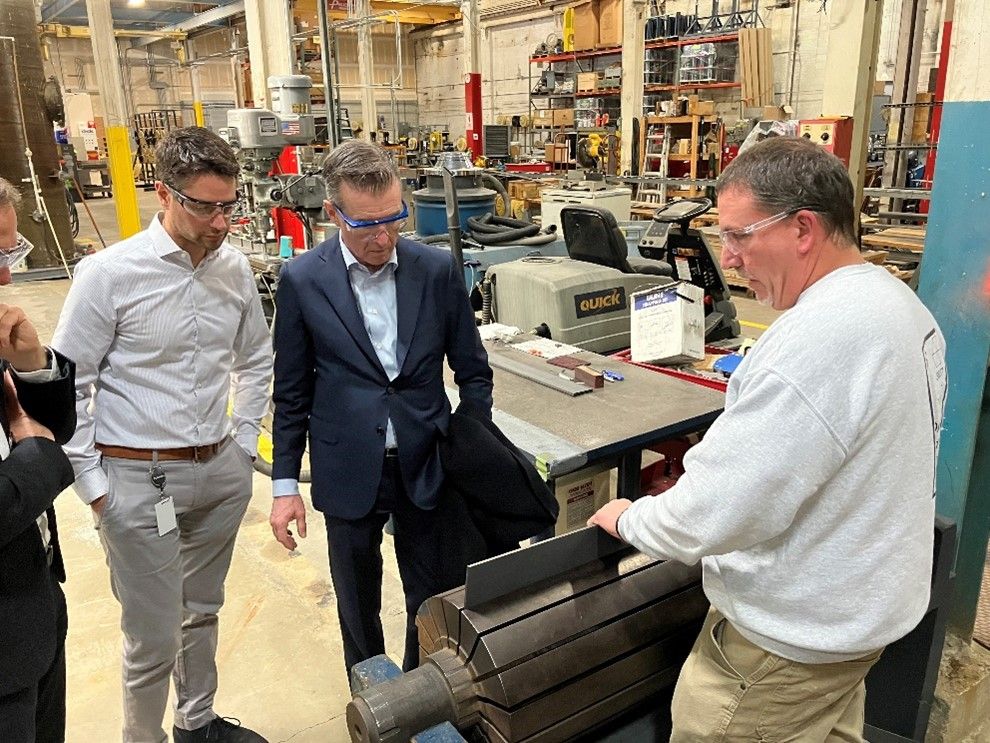
While in Pennsylvania, Christopher – who only joined FLSmidth Cement last October – was given a tour of Keystone Cement by plant manager, Stuart Guinther. Located just a 15-minute car ride from our Allentown offices, the Keystone plant is part of Giant Cement Holdings Inc. and has been producing cement for almost a century. “I’ve been around many industrial sites before, but this was my first cement plant. It was a thoroughly enjoyable and educational experience. My thanks to Stuart and his team for hosting us and showing me around. I look forward to visiting many more!”
Service-centricity in action
Working with existing clients to improve their operating and maintenance practices and get ‘more from less’ is core to our service-centric approach. This quarter saw us sign or extend several service contracts including:
- A new global service agreement with leading cement maker, TITAN Group, covering 14 cement plants, three grinding plants, and a cement terminal at various locations around the world. Under the agreement, we will provide a range of onsite and remote services, covering a wide spectrum of equipment and systems – from material handling, to grinding, pyroprocessing, and digital control systems – as well as sustainability audits on key process areas.
- A new five-year service agreement with SSB International Ltd (SSBIL) to provide expertise and supervisory support in connection with SSBIL’s O&M contract with Abayak Cament’s Akoga cement plant in Equatorial Guinea. We originally supplied and installed the main equipment at Akoga in 2016, but issues with the main power supply have seen the plant idled since then. These have now been resolved and commissioning is expected to be complete by mid-2024.
- Renewal of our PlantLine™ service agreement with Ash Grove Cement for the 21st year running. Over the years, the scope has grown from a modest beginning to now cover each of its plants in the USA and Canada. Covering a plant’s automation and digital systems, our PlantLine service agreements ensure that these systems operate reliably, 24/7, through a range of flexible service offerings that keep the software and hardware protected and performing well.
- An extension to our existing maintenance service agreement with Argos Cement to include its Newberry plant in Florida. Covering the complete production process – from quarry to packing plant – this agreement will involve us working with Argos to improve overall equipment efficiency and thus plant productivity.
After more than a century, this relationship is still going strong
The first quarter also saw us welcome a delegation from Siam Cement Group (SCG) to our Copenhagen headquarters and Dania laboratory to discuss how our solutions and services can best enable their sustainability journey. Incredibly, our relationship with SCG has spanned generations. We installed their first kiln 103 years ago and, today, we continue to support the company, as it looks to establish itself as a green pioneer in southeast Asia.
Christopher offered, “The length of this relationship may be unusual, but its spirit imbues everything we still aim for in the 21st Century. As an increasing number of cement plants ask how we can enable their green ambitions, we are proud to work with customers, new and old, to support their journey to reduce emissions and improve operational performance.”
As the pureplay transition continues, we thank you for your patience!
For over a year, we have been transforming our organization to be fully separate from mining. Some of it is super easy, such as our sales teams and product specialists who were always independent. But, it goes without saying that there have been some challenges in both our own business systems and work processes. Similarly, many of our customers and partners have been tasked in updating business systems with our new legal names, banking details and so forth. Thank you!We appreciate all of our customers and suppliers for their patience through what was at times a bumpy ride.
We are happy to report that with very small exceptions, the process is now almost complete with only our Denmark office remaining. We will make the change here at the end of Q2.