article
The Evolution of Fuller-Kinyon® Pumps – workhorses of industry
Originally designed in 1919 as a solution for the safe transportation of pulverised fuels, the Fuller-Kinyon® screw pump has proven itself to be a must-have component in materials handling systems worldwide. Over more than a century, the pump has evolved to handle greater throughputs, longer conveying distances, and the increasing complexities of today’s dry bulk materials processes. In that time, it has been widely applied across the cement and other dry bulk materials handling industries, developing reputation as a real workhorse – as is testified by the continuing operation of some of the original FK Pumps.
When handling of pulverized coal caused explosions and threatened lives, engineer Alonzo G. Kinyon of the Fuller-Lehigh Company invented what later became one of the greatest contributions to cement manufacture. That was more than one hundred years ago. Over the years, the award-winning Fuller-Kinyon® Pump has profoundly changed the layouts of cement plants. Today, ongoing developments and improvements to pump performance, operating life and maintenance requirements ensure our customers maximum efficiency, flexibility and reliability in the conveying of pulverised material.

Today's FK pump is the result of decades of continuous improvements
The pump has evolved to be capable of handling greater throughputs, longer conveying distances, and the increasing complexities of today’s dry bulk materials processes.
Maintenance innovations
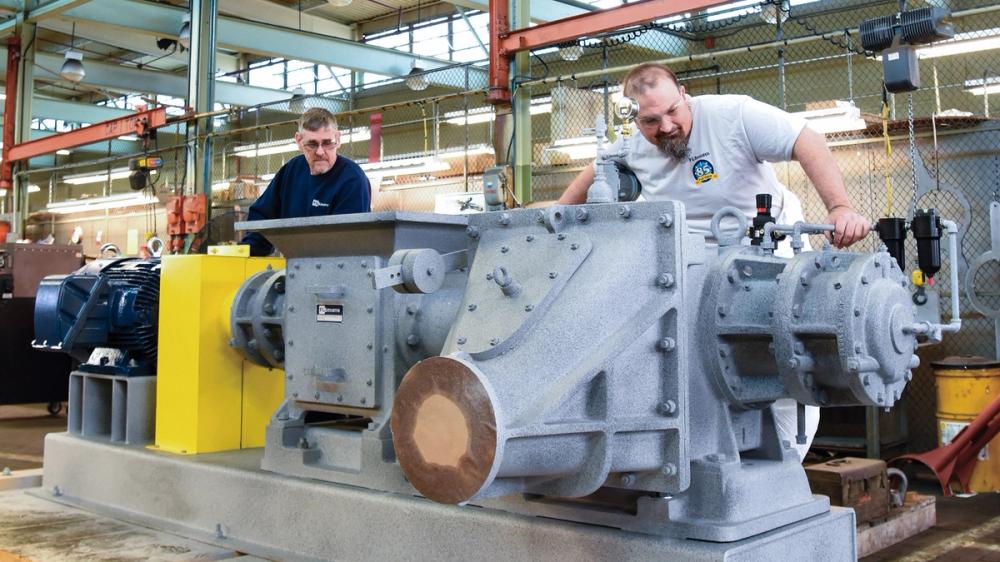
Even with a high-quality machine like a Fuller-Kinyon® pump, it’s not a question of if a bearing assembly will wear out, it’s a matter of when. The typical removal, rebuild, and reassembly of a worn bearing unit can take up to 7 – 10 hours, depending on the extent of wear to the original parts. We’ve worked to reduce downtime by developing two key solutions:
Three-piece screw
FLSmidth Cement introduced the 3-piece screw design as a conversion kit for existing pumps and as the standard for all new Type M pumps sold. The 3-piece screw makes maintenance both quicker and easier, cutting screw change-out time by up to a third.
The 3-piece screw splits the pump screw into three sections – the centre section being the replaceable wear part. This eliminates the need to disconnect the coupling to perform maintenance, saving the bearings and seals from being exposed to a dusty, dirty plant environment.
Hot Swap bearing assemblies
The 3-piece screw is a crucial component of the Type M Fuller-Kinyon® pump. However, its bearing assembly requires occasional replacement. Keeping Hot Swap bearing assemblies in stock cuts downtime by more than half. In fact, you can be back up and running in approximately 3 hours. Each Hot Swap is a fully-assembled unit complete with seals, bushings, bearings, and drive or stub shaft. The cost of each assembly is significantly less than buying the individual parts. The savings get even better when you factor in the reduced overall system downtime.
Every Hot Swap exchange bearing assembly is backed by an FLSmidth Cement one-year material and workmanship warranty.
Hot Swap bearing exchange programme
Once the new assembly is “swapped” onto the pump, you can rebuild the worn assembly when time allows. Or, for additional savings, send us the old unit. If an inspection reveals that its shaft, bearing housing, bearing support and cover plate can be used again (many can be) for a future rebuild, we’ll give you credit for the reusable parts.
Spare Parts Stocking Programme
A ready supply of spare parts is essential for the continued, efficient operation of your plant. But the cost of carrying all the necessary spare parts can be prohibitive. We’ve developed a Spare Parts Stocking Program (SPSP) that enables you to keep up safe inventory levels in your storeroom while minimising costs.
Conclusion
The Fuller-Kinyon® screw pump's evolution over the past century exemplifies the power of innovation in the materials handling industry. From its inception in in the early 20th century, the FK Pump has continually adapted to meet the demands of modern dry bulk material processes. Each design advancement, from the introduction of the game-changing Type 'M' pump to the latest innovations in maintenance solutions that keep downtime to an absolute minimum, has enhanced the performance and reliability of this industry workhorse. We’re committed to the continual development of this critical handling solution to ensure it can help our customers meet their materials and process challenges for the next 100 years and more.
Related Offerings