article
Fuel flexibility reaches new heights (and new carbon lows) at Mannok Cement
The Pfister® FEEDflex is an upgrade to the proven and widely used Pfister® DRW Rotor Weighfeeder, with the advantage of a much lower minimum feed rate – down to as little as 60 kg/h – with no change to the maximum feed rate.
During the final commissioning of the FUELFLEX® Pyrolyzer at the Mannok Cement plant in Ireland in 2022, the ambitious cement manufacturer was keen to embark on the next steps of its Vision 2030 project to reduce its carbon footprint.
”The FUELFLEX enables us to burn up to 100% alternative fuels in the calciner while also bringing NOx emissions right down. It’s been a game-changer for our plant,” explains Damian Reilly, Mannok Cement. “The next obvious step for us was to upgrade our coal dosing system so that we can reduce the amount of coal going into the preheater to an absolute minimum without sacrificing flexibility. We were happy to continue working with FLSmidth on these projects, knowing we share similar goals.”
Traditionally, coal feeders have operated with a minimum quantity of 1 tph of coal. This is low relative to the quantity of alternative fuels being fired, but still higher than many plants would like at a time where every carbon saving counts. However, eliminating coal from cement production entirely is not on the cards right now.
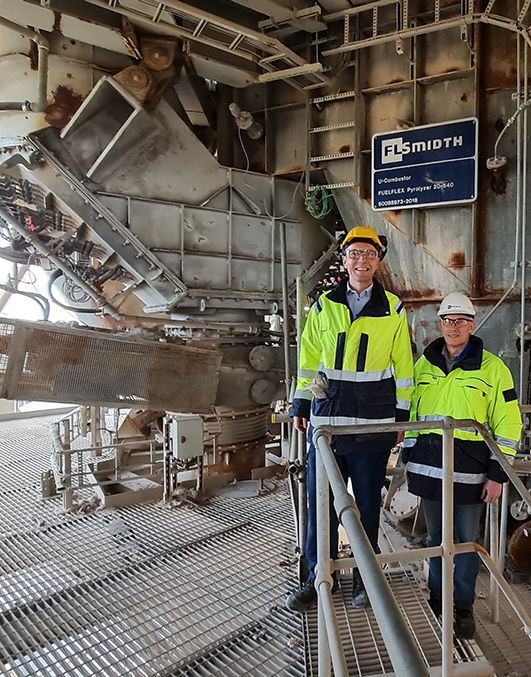
“The ambition to remove coal from the pyroprocess was what drove us to develop a more flexible coal feeder,” says Peter Norek, Global Product Manager Feeding and Dosing Technologies, FLSmidth. “Even with the ability to fire 100% alternative fuels, most plants still require the ‘fallback’ of coal for when SRF supplies are low, or at start-up. The Pfister® FEEDflex is basically an upgrade to the proven and widely used Pfister® DRW Rotor Weighfeeder, with the advantage of a much lower minimum feed rate – down to as little as 60 kg/h – with no change to the maximum feed rate. The achievable feed range of 1:100 means that plants can significantly reduce their coal usage, without hamstringing their operation if greater quantities of fuel are required.”
The FEEDflex has been available for 5 years and was part of Mannok Cement’s plans for the plant since the early stages of the FUELFLEX development in 2019. The plant was already operating two SRF lines to the calciner using Pfister TRW-S feeders, but the minimum coal feed quantity was not yet a limitation, as it became when the FUELFLEX came into operation. Now one SRF line feeds via the FUELFLEX and one directly into the calciner. Before the FEEDflex upgrade, their existing coal feeders were fixed at a minimum feed rate of 1 tph. However, with the new SRF capacity in the calciner, the plant wanted to reduce this to 0.16 tph.
“This has been a multi-way project,” explains Damian. “On the one hand, we’re bringing in a new feeder upgrade to reduce the quantity of coal. On the other, we’ve optimised our TRW-S feeders to increase their SRF capacity and make the most of the FUELFLEX. And then the third part of the project is the ECS/ProcessExpert® advanced process control software, which has been remarkable.”
Reducing coal feed
The FEEDflex technology consists of newly designed air distribution in the DRW Rotor Weighfeeder by replacing and adding parts, which allows significantly lower rotor rpm without leading in pulsations. The upgrade can be easily carried out in just one day during regular maintenance shutdown.
SRF Optimization
With the optimised TRW-S SRF feeders and the new Pfister FEEDflex, the plant is saving more than 1 tph of coal.
“We’ve been using Pfister feeders since the 1980s and they have always served us well,” says Damian. “The TRW-S SRF feeders were commissioned in 2014 and we’ve steadily increased their use over the last few years and especially since the FUELFLEX went into operation. They are easy to maintain and haven’t given us any trouble.”
As the plant was operating at close to 100% capacity on both SRF feeders, Mannok came to FLSmidth for advice on how to increase their capacity. In June 2021, during a Pfister service, the FLSmidth site team investigated the options. It proved possible to update a few control system parameters to achieve the necessary results; the pneumatic and mechanical transport were already capable of handling the additional SRF feed.
“As a result of this work, we’re now operating at a steady 10 tph through one of the SRF feeders and the feed rate of the second feeder is controlled by the ECS/ProcessExpert® system according to the temperature in the calciner,” explains Damian. “We’re averaging 17 or 18 tph of SRF, and if there’s a blockage in the line, the coal feeder kicks in, and we don’t need to stop the plant. It’s seamless.”
With the optimised TRW-S SRF feeders and the new Pfister FEEDflex, the plant is saving more than 1 tph of coal in addition to what was achievable by implementation of the FUELFLEX alone – a considerable achievement.
“It may not seem like a large sum, but the road to net zero is going to be full of these incremental improvements,” says Damian. “Every little helps. The FEEDflex has been in operation since the winter shutdown in early 2023 and you’d hardly know it was there – it’s so easy.”
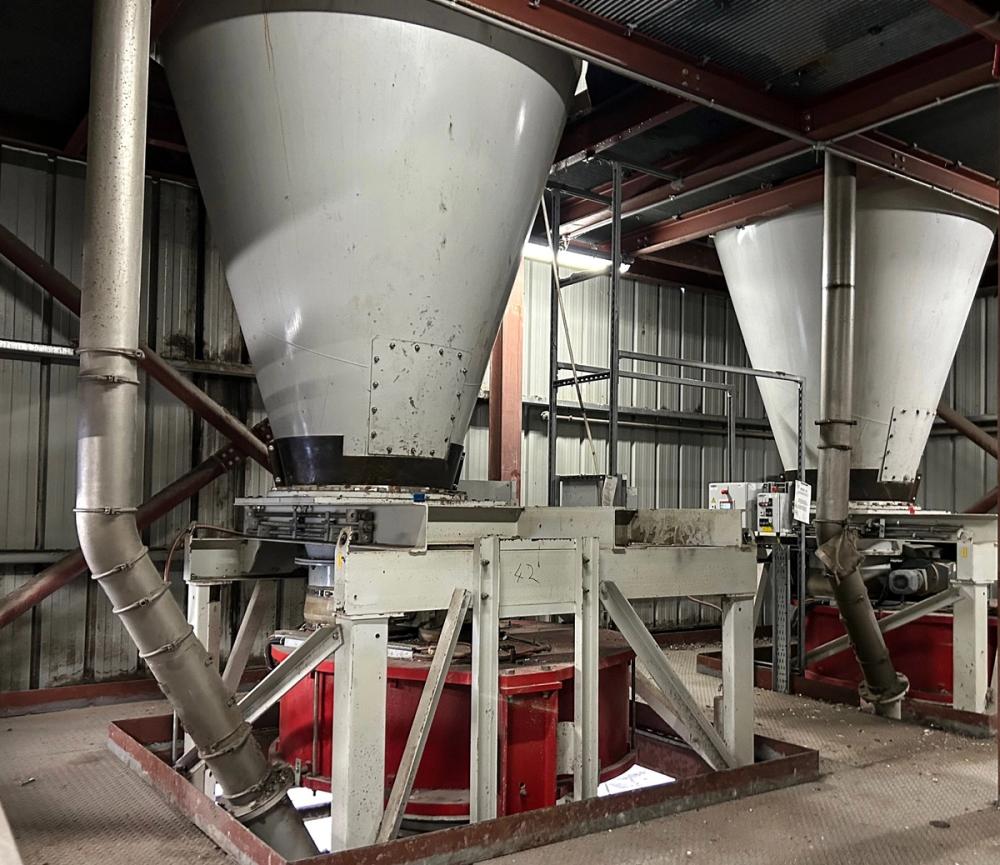
Damian Reilly, Mannok Cement
Advanced process control
Mannok was already operating an older version of ECS/ProcessExpert system on its kiln line and seeing the benefits there, particularly in optimising fuel consumption. After the FUELFLEX project was complete, the FEEDflex upgrade and ECS/ProcessExpert upgrade were rolled out to calciner operations at the same time, effectively minimising coal consumption. The fired fuels are prioritised so that SRF is automatically used as control fuel, but coal seamlessly supplements SRF if there are limitations in the available feed for any reason. More recently, Mannok introduced ECS/ProcessExpert software to the raw mill and cement mill to increase efficiency in those processes.
“ECS/ProcessExpert advanced control software is the one big thing that’s going to make a difference long-term to cement production,” says Damian. “It’s the first time I’ve witnessed AI outperforming humans. Even your best operators couldn’t be so quick to increase or reduce the SRF feed depending on calciner conditions. We’re seeing true optimisation and I think the potential of this tool is only going to increase. We’re expanding our use of it across the plant, including on the kiln and mills. The cement mill has seen an increase in tonnage across all cement types.”
Vision 2030
Mannok is committed to reducing carbon emissions by 33% compared to 2020 levels by 2030.
Alongside their alternative fuel investments for the calciner, they have also been making plans to reduce fossil fuel use in the kiln.
“In early 2024 we will be adding a satellite burner to the kiln so we can feed in SRF and reduce fossil fuel use,” says Damian. “This will be fed by a new Pfister TRW-S feeder and will also involve putting in a new docking station for receiving SRF. The following winter we hope to replace the existing kiln burner with a JETFLEX® burner, which will further increase our fuel flexibility. In the long term, we’ll also be looking at the potential for waste heat recovery and additional energy efficiency projects. These investments are made purely on the basis of their ability to help us reduce our carbon footprint and meet our Vision 2030 goals, though we can’t deny they often also bring a cost benefit. We’re very committed to being a pioneer in low-carbon cement production and we couldn’t do it without FLSmidth.”
“It is great to look back at how Mannok and FLSmidth have essentially eliminated the use of calciner coal and ammonia water for de-NOx by a close collaborative team effort combining several new technologies and process optimizations. We look forward to the next steps in 2024 and the years ahead.” says Lars Skaarup Jensen, R&D Specialist and project manager Green Innovation, FLSmidth.
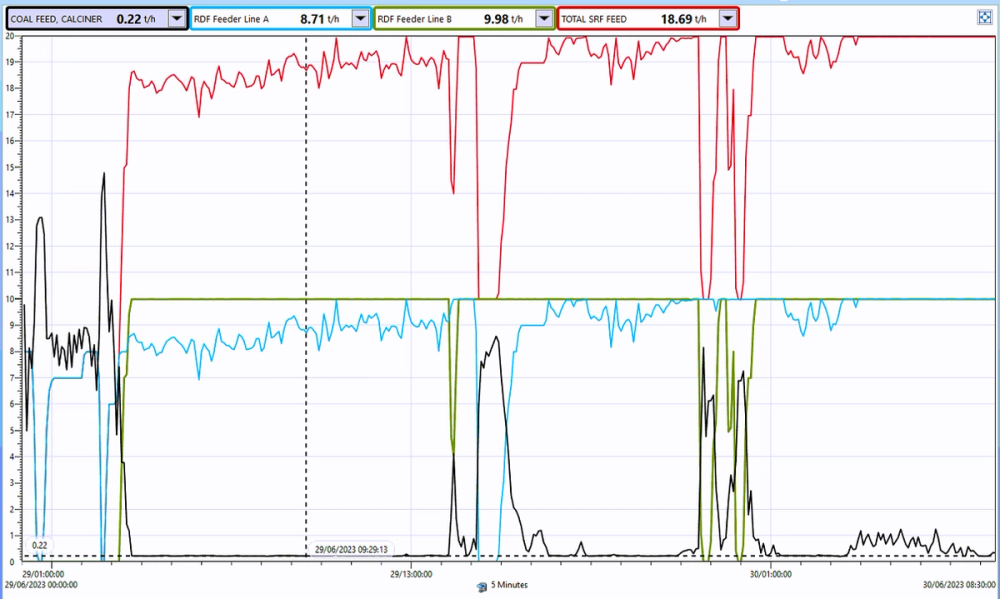
Figure 1. The chart illustrates how the three Pfister feeders act in conjunction with PXP control. The coal is minimised but kicks in when the SRF feeders reach their maximum – and when a SRF feed line blocks. Initially the FUELFLEX is not operated. Then SRF feed to it is ramped up to 10 tph with SRF line A to the calciner controlling the bottom stage temperature. Each time an SRF line blocks the coal replaces it – and when SRF feed reaches the 20 tph limit coal feed supplements to control the calciner temperature. Otherwise, the coal is maintained at the 0.2 tph minimum.
This article was initially published in International Cement Review's March 2024 issue.