article
How Mangalam Cement removed downtime and personal dependencies
Troubleshooting is now so easy for operators at Mangalam Cement’s plant in Rajasthan, India, that downtime is a thing of the past. Upgrading the control system to FLSmidth Cement’s ECS/ControlCenter™ V8 has made the system simple to use and Mangalam no longer depend on specialised individuals to perform maintenance or bypass interlocks.

Uptime was a challenge at Mangalam Cement’s plant in Rajasthan, mainly due to frequent plant tripping that affected the productivity. Worst of all, the operators on site could barely do anything about it, considering the limitation of the old control system.
“Our old system was obsolete, and with the existing programming standard our operators couldn’t identify the causes of the tripping. Also, the SCADA system was not user friendly, so the operators depended on specific instrumentation engineers for simple maintenance like bypassing of interlocks and managing alarm timers,” says Mr. Sunil Sanadhya – Sr. G.M. - Instrumentation & Projects, Mangalam Cement.
The system was based on Siemens WinCC and was engineered without use of any standards. As a result, only specific engineers knew how to trouble shoot and maintain the system.
When Mangalam reached out to FLSmidth Cement to talk about an upgrade, easing the use of operation was an important aspect. And now with version 8 of FLSmidth Cement’s own ECS/ControlCenter™ system in place, Mangalam got what they bargained for.

“For instance, all interlocks can be seen and bypassed by every authorized user directly from the faceplate, most often done from the engineering station. Before it was very difficult to know the interlocks and impossible to bypass them from the faceplate, as each bypass required reprogramming of the PLC system. This means that the system is very easy to operate – and most important, we avoid the plant tripping, as operators can take action fast,” says Mr. Sunil Sanadhya.
Independent of specialised users
A great advantage of the new system is that it is independent of individual, specialised engineers. Because everything is based on a standard system, learning to operate the system and extract knowledge from it is easy and intuitive. This applies to everything from troubleshooting, configuring, process analytics using trend and reporting tools and even back-up and restore.
“Our old system was very complex and did not have a set pattern to take backup and restore. It required a specialised person. With the built-in capacity in ECS, backup and restore is basically just the push of a button,” says Mr. R. Giri - VP-E&I.
Library built for cement plants
ECS/ControlCenter is so easy to use for cement plant operators because it is tailored specifically to this industry. Even the programming of the PLCs is based on the ACESYS component library developed by FLSmidth Cement for the cement industry.
Engineering Excellence
In the case of Mangalam, decoding the existing PLC program and converting it to the ACESYS standard was the most challenging part. Also, the PLC backup had no reference of standard tag names and descriptions, so the database had to be cleaned up and standardized.
“In coordination with the customer and with the domain experience of our specialist, we did a complete clean-up of the database, made sure all tag names were corrected and all the non-standard existing programs were reprogrammed to the state of art ACESYS standard.
We retained the existing hardware to the maximum extent and upgraded all six PLC sections. Complete I/O panels of the sections related to the kiln and the cooler were also upgraded and the I/Os in the remaining four sections are a mix of Siemens S5 and S7 and were retained – so we also had to make interfaces to the analogue I/Os of the S5s. Altogether, this made it an extended and challenging upgrade,” says Senthil Raj Krishnan, Engineering Manager in FLSmidth Cement.

Mr. Sunil Sanadhya – Senior G.M. - Instrumentation & Projects, Mangalam Cement
Improved productivity
The project was executed in three phases that all went smoothly, and productivity at the plant has already increased. This is in contrast to the previous upgrade of the plant where Mangalam hired a system integrator to upgrade the line. Here, the result was a technical focus on converting the S5 logic to S7 logic but that didn’t solve neither the problems with plant tripping nor the dependency of specific individuals for operation and maintenance.
“No matter which vendor supplied the PLC hardware, we have the skills to suggest the optimum upgrade strategy and integrate our ECS/ControlCenter on top. What matters to us is the output for the customer rather than the supplier of the PLC hardware. We are cement people, and our engineering is centred around making cement production simple and effective for our customers,” says Rizwan Sabjan, Head – Global sales and proposals, Process Control and Optimization, FLSmidth Cement.
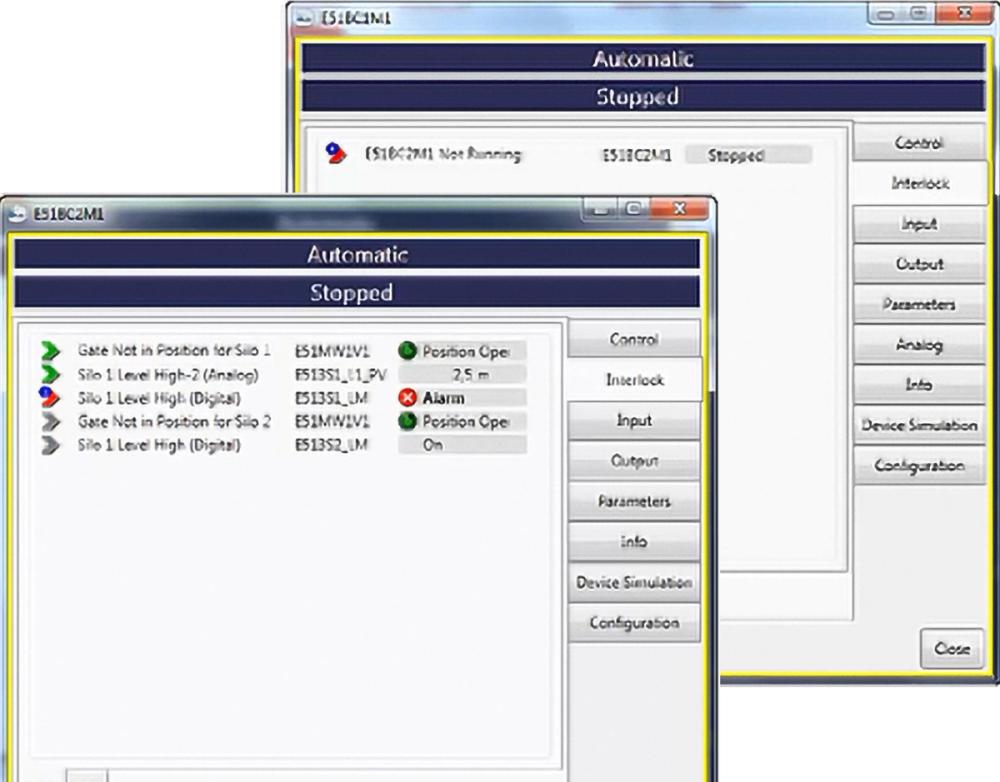
That task of making it simple and effective has indeed been completed at Mangalam Cement.
“Productivity has improved as the spurious tripping due to program related issues is now eliminated. The interlocks root cause analysis and advanced trending and reporting features of ECS/ControlCenter V8 benefits operators for much easier fault tracing and stable operation, as the operators can easily understand the cause of tripping of sections. FLSmidth Cement can access remotely for monitoring, and we have easy access to support when needed,” says Mr. Sunil Sanadhya.
Ready for further digitalization
With FLSmidth Cement's ECS/ControlCenter V8, Mangalam Cement has taken a big step towards utilizing the benefits of digitalization and Industry 4.0.
ECS/ControlCenter paves the way for process insight supported by data to further optimise production. Data can easily and effectively be connected to FLSmidth’s cyber protected cloud solution for further analysis and benchmarking, even cross plants where applicable.