article
Lowest CO2 footprint for clean air? Use an ESP!
Did you know that an Electrostatic Precipitator (ESP) could be a more cost-effective long-term option than Fabric Filters (FF) for clinker cooler applications with a significantly lower CO2 footprint? If the answer is no, you’re not alone.
Many people in the cement industry have dismissed ESPs as outdated technology that has been surpassed by the superior performance of fabric filters – but this is no longer true. And with energy costs rising, ESPs developed with the latest state of the art technology actually present a more affordable option, with lower energy consumption, lower maintenance, and a lot less work.


Evolving technology
Over the years, we have continuously improved the design and technology of our ESPs to enable them to meet increasingly stringent emission requirements and also keep the physical layout as small as possible. Computational Fluid Dynamics (CFD) modelling help us design optimal gas and dust distribution, enabling 100% utilisation of the installed collection area. This, combined with our extensive process know-how and specifically developed equipment technology, reduces the equipment footprint and thereby results in a more compact plant layout - which in turn minimizes installatipon costs.
Despite the more compact design, we still ensure sufficient safety in design to be able to handle increased loads and still operate under the original guarantee values. As a result of these efforts, our ESPs can now achieve dust emissions well below 5 mg/Nm3.
The technology has been proven in more than 4000 installations for applications within cement, pulp and paper, iron and steel, and metallurgical production. These customers have benefited from:
- Reduced dust emissions
- Compact footprint
- Reliable dust emissions control
- Low, simple maintenance
In some cases these are new installations and in others they are upgrades, which we can perform on any ESP, regardless of the original make. In every instance, the ESP is configured to meet the specific needs of the application.
Energy consumption
It’s easy to assume that equipment with ‘electro’ in its name is going to be power-hungry. But while it’s true that ESPs do require energy for charging and capturing the dust particles, it’s also true that they require less than fabric filters.
The ID fan must overcome the pressure drop through the filters. Pressure drop over a baghouse is around 1500 Pa, whereas with an ESP it is more like 150 Pa, resulting in a significantly lower energy consumption for the ID fan. Cleaning filter bags is an essential but wearing and energy-dense process requiring compressed air. The ESP requires no compressed air at all.
Our ESP can operate continuously at up to 400 ˚C which eliminates the need for a heat exchanger (HEX) and the associated power consumption for cooling. All things considered, the energy consumption is typically 33-44% lower for an ESP solution depending on the emission limit. In times of high energy prices, there are big savings to be made with an ESP compared to fabric filters.
The numbers are based on a recent project in Spain and presented in relative terms
Effective emissions control
At the time that more stringent particulate emissions regulations were being brought in, fabric filters represented the best available technology to reach the low numbers required. However, today, technology developed by FLSmidth has improved and our ESPs are equally capable of meeting low emissions limits, to as low as 5 mg/Nm3.
From the European Environment Agency indicator Emissions and energy use in large combustion plants in Europe (europa.eu ) the Industrial Emission Directive (IED) has effectively required plants to reduce emission in order to sustain operational permits as shown in the diagram.

( Reference: EEA, 2022 " Emissions and energy use in large combustion plants in Europe ")
At the time that more stringent particulate emissions regulations were being brought in, fabric filters represented the best available technology to reach the low numbers required. However, today, technology developed by FLSmidth has improved and our ESPs are equally capable of meeting low emissions limits, to as low as 5 mg/Nm3.
Generally speaking, the ESP is the preferred technology in India, where OPEX is considered more of a priority than CAPEX. ESPs are also widely used in other industries, such as pulp and paper, iron and steel, copper and zinc, and other metallurgical applications.
Long-life equipment
Fabric filter bags last typically 3 years (range 2-5 yrs.), at which point the bags will need to be replaced. After 6 years (range 5-7) the cages supporting the bags also need replacement.
Similar replacement of the wear inserts on the heat exchanger is required. That’s tons of material that become waste. The ESP, on the other hand, is more of a ‘set and forget’ asset. It requires very little maintenance over an expected 20 – 30-year life, and the wear parts limited to hammers (replaced every 5-7 years), and collecting plates & electrodes every 10-15 years. Both the ESP and the FF & HEX would require dust transport wear parts changed every 5-7 years.
The ESP is also less vulnerable to unexpected downtime. For example, if your heat exchanger fails and your baghouse receives a blast of hot air, you risk burning the bags and a period of downtime to remedy the damage. An ESP is more robust. It doesn’t require a heat exchanger because it can handle peak temperatures up to 450˚C, and so the risk of downtime is lower.
FLSmidth ESPs also benefit from a state-of-the-art control system with PIACS® , our proprietary smart microprocessor controller that enables the ESP to automatically react to process variations to ensure outlet emissions remain low even under challenging conditions. We also cover the ESP with our remote service offering, providing 24/7 support wherever you are.
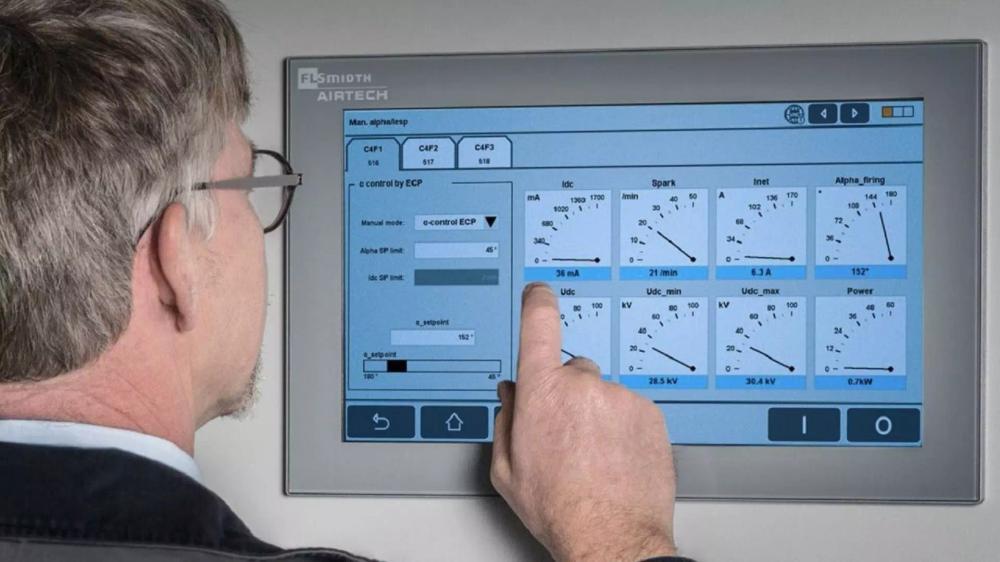

Minimise the equipment footprint
Baghouses are smaller than ESPs, and this is often a consideration when cement manufacturers are planning expansions or new lines. However, it is also important to consider the space taken up by the heat exchanger and interconnecting ducting, which, as mentioned, is not required with ESPs. The combined footprint of a heat exchanger and baghouse is typically equivalent to the space required for an ESP, and the layout of an ESP is simpler.
We have worked hard to reduce the size and footprint of our ESPs by optimising gas and dust distribution to enable 100% utilisation of the installed collection area. This has been a deciding factor for many of our customers in selecting FLSmidth to upgrade or install new ESPs.

Process flow-sheet for de-dusting the clinker cooler gas using a fabric filter and heat exchanger

Process flow-sheet for de-dusting the clinker cooler gas using an ESP
ESPs are clearly the best choice for some applications
While we believe the ESP is underappreciated, given its strengths, it is not the best option for every application. For example, an ESP might not be suitable for your raw mill or kiln applications, or for very unstable process. However, it is ideally suited to clinker cooler applications, where its robustness and trouble-free performance is especially valuable. You could even incorporate a waste heat recovery unit after the ESP to make use of the hot gases – you couldn’t do that with a fabric filter!
Lowest total cost of ownership, lowest carbon footprint
With its relatively low power consumption, low maintenance and simple layout, the ESP represents the best value for money for emissions reduction. The low energy use compared with fabric filters not only reduces operating costs but also carbon emissions, helping you lower your carbon footprint. And there’s no sacrifice on performance, with emissions levels as low as 5 mg/Nm3 a possibility. All in all, it’s time the wider cement industry started giving the ESP the consideration it deserves.