When we look at the future of cement manufacturing, we see huge potential to increase efficiency and reduce environmental impact through digitalisation. From an operational perspective, it enables us to streamline processes by automating controls that would previously have been manual, removing the potential for human error and making calculations much more quickly than people ever could. And when it comes to maintenance, those quick calculations, combined with expert insight, enable us to identify the early warning signs of potential failure. Armed with that information, plant operators can act at the right time, eliminating the occurrence of unplanned downtime.
Digitalisation, then, holds the power to both increase operational efficiencies and enable a predictive maintenance schedule that extends equipment life and reduces costs. But how do we harness that power in a real plant setting?
Monitoring kiln health
Let’s say, for example, that you suddenly notice cracks in the kiln tyres. Everyone panics – this is a problem that needs to be dealt with urgently. But your next maintenance shutdown is not due for another 9 months. Can you afford to take the risk, and wait and see how far you can push it? Or should you be thinking about a more immediate shutdown, with all the associated costs?
Without all the data, you can’t calculate the risk. But with the right data, you could have avoided the problem altogether. And that’s where digital solutions like online condition monitoring services come in.
FLSmidth Cement offers online condition monitoring services across the plant. For the kiln, these services enable plant operators to continuously gather data that was not previously available and use it – in combination with the continuing support provided by our kiln specialists – to keep a close eye on kiln health, including kiln components that would typically only be inspected every 2 – 3 years. This means, for example, that unusual kiln overload would be detected long before the tyre cracks. The problem could be resolved before it becomes urgent, saving you both the cost of unscheduled downtime and all the stress that goes along with it.
Data that informs
The act of gathering data is not new, of course. Your kiln is already equipped with certain sensors, monitoring the bearings, hydraulic thrust device and kiln drive, and you are probably already using a control platform to operate the kiln. The issue is how the data is used. In all likelihood, most of it is looked at in isolation, and some of it is not looked at very often at all. This presents a risk that key indicators of wear will be missed, along with the root causes that could go on to become major kiln failures.
By adding new sensors, you can also monitor kiln crank, kiln shell ovality, kiln drive vibration and axial balance – all on a 24/7/365 basis. This gives you most of the measurements you would get with a Hot Kiln Alignment (HKA), meaning you have all the data you need to schedule the HKA and maintenance activities when they are needed most.
Expertise that empowers
Data without insight is no good to anyone. The data needs to be collected, analysed and reported back in a way that is meaningful and actionable – which is why our online condition monitoring services are digitally-enabled, but also people-powered. All of the sensors are collecting data all the time, and feeding it to FLSmidth Cement’s cloud application, which is designed to detect any abnormal events or ‘behaviour’. If anything out of the ordinary shows up, an alarm is sent to the FLSmidth Cement 24/7 Global Remote Service Centre where the data is analysed by our kiln experts. These are people with plant and process experience, who can decide the context of an alarm and recommend what action the plant might need to take to solve whatever problem has arisen. These recommendations are put into a report for the plant to act on, and these case reports are in addition to the regular condition reports that come as part of the online condition monitoring services package.
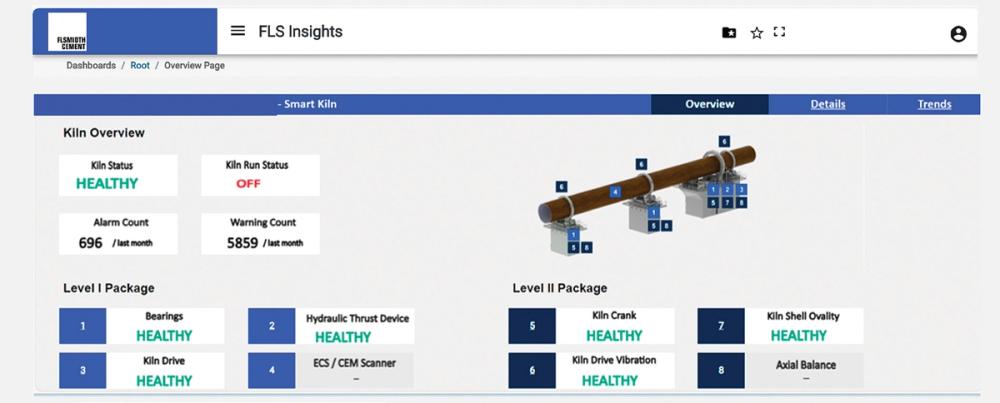
Decisions that drive efficiency
The major benefit of all this information is the ability to be more strategic about maintenance. No more running to failure (unless it makes sense to do so). No more nasty surprises. Instead, maintenance can be planned in such a way that best suits your production schedule, your budget, and the urgency of the repair work. This not only reduces the cost of downtime, but also the duration – enabling you to optimise productivity and remain competitive. It also reduces the pressure of downtime because you know exactly what you are dealing with, and you are able to prepare properly.
At its core, managing your maintenance schedule based on data about your current kiln condition enables you to:
- Extend the life of rotating parts
- Improve the life of lining and kiln shell
- Avoid kiln shell constriction and reduce stress
- Avoid girth gear breakdown
- Identify alignment issues
- Stabilise bearing temperatures
- Reduce power consumption
The more efficiently your kiln runs, the more sustainable your operation. That’s the potential of digitally-enabled, people-powered services.
What is being monitored?
The list below comprises all the kiln components that can be monitored with the online condition monitoring services, though it should be noted that the actual provision depends on the service package you choose and the specific equipment to be monitored.
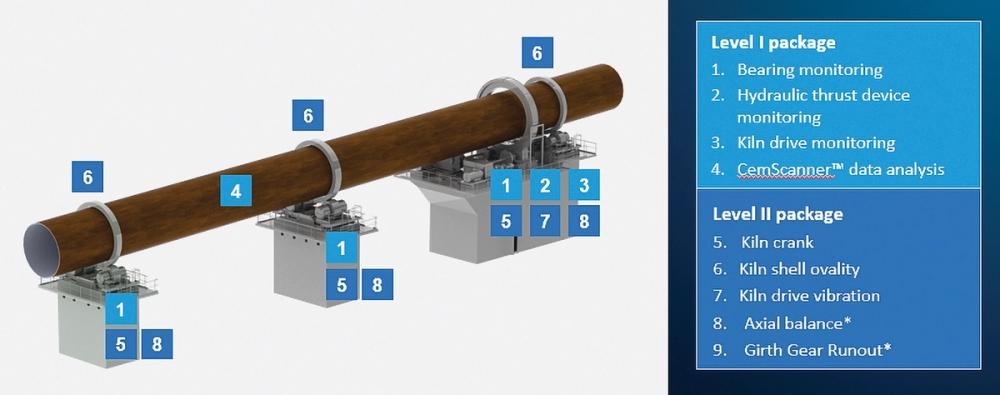
Bearing monitoring
- Identify overload
- Identify improper lubrication
- Analysis of bearing temperature trend
- Root cause analysis on hot bearings
Hydraulic thrust device monitoring
- Kiln axial floating and cycles
- Kiln axial load
- Health of hydraulic system
Kiln drive monitoring
- Kiln drive power consumption
Kiln drive vibration
- Detection of gear issues
- Detection of facet formation
- Protection of planetary gear
Axial balance
- Monitor thrust bearings temperatures
- Monitor thrust direction of individual supporting roller
- Full overview of axial balance
Kiln crank
- Kiln shell ovality
Plus, with ECS/CemScanner™ integration (if applicable), we can also detect refractory failure and the early signs of hot spots.
How condition monitoring saved a kiln in Egypt
A customer in Egypt had been having some issues with their kiln for a while. With the condition monitoring system, we were able to identify that the kiln axial floating was unstable, and this was causing pump cycles as low as 5 minutes. Using this data, our experts worked with the plant on a root cause analysis, which suggested a hydraulic leak was to blame for the instability – the result of a defective valve. This kind of defect would have been virtually impossible to identify without the condition monitoring system and would ultimately have resulted in downtime, and potentially even failure. In this instance online condition monitoring services saved substantial costs and allowed the plant to replace the valve in a stress-free, timely and cost-efficient manner.
No matter where you are
While on-site services remain an important and necessary provision, the benefits of remote services can’t be denied.

Remote services guarantee a quick response, since our service centre is manned 24/7 and we can monitor continuously – which means you can also take action more quickly, resulting in a faster resolution to your problem. In between planned on-site services, which will always be needed to maintain a kiln correctly, we will be able to solve many problems without sending anyone to your site. This reduces the cost of services, not to mention the environmental impact of all those airmiles. Plus, by coupling on-site tools – such as these condition monitoring sensors or when we use helmet-mounted cameras to – together with our remote capabilities via the FLSmidth Cement 24/7 Global Remote Service Centre, we are able to support you wherever you are, share our expertise and help with everything from commissioning new kilns to repairing older machines.