article
Partial upgrade – complete new burner
A Jetflex® burner upgrade at Salt River Materials Group’s (SRMG) Clarkdale plant in Arizona, USA, delivers the benefits of a new kiln burner. This ‘out-of-the-box’ solution results in a stronger, better flame, and a more consistent kiln operation and clinker quality. Previously published in ICR, May 2019.
Salt River Materials Group (SRMG) had a problem. Its 15-year-old Duoflex® kiln burner at its cement plant in Arizona, USA, was costing thousands of dollars a year in excess maintenance and causing issues with clinker quality. After several years of good operation, the air annulus was struggling to hold its perfectly symmetrical shape over an annual campaign, causing inconsistencies in the flame shape and clinker quality. The annulus needed annual reconditioning to achieve a good flame, and the plant was maintaining two spare burners as it tried to keep operational consistency. Though the maintenance costs were high, the cost of a brand-new burner was even higher. The plant was stuck in a damage control cycle that was costing much more than it wanted to spend and resulting in lower-than-desired clinker quality over time.
A design challenge – accepted!
When FLSmidth Cement introduced the Jetflex® burner to the market in 2016, the Danish equipment manufacturer presented it to SRMG as a potential replacement option. The Jetflex burner design includes two methods of introducing primary air – an axial ring comprising rectangular jet air nozzles for fast ignition and stable flame formation, and a ‘swirler’ ring that controls flame shape. FLSmidth Cement knew that these improvements alone would spell the end of SRMG’s ongoing flame consistency and quality issues, as well as save the cement producer considerable sums in maintenance costs.
SRMG was excited about the new technology but hesitated over the cost of a completely new burner. However, with two spare burners in excellent condition, the question arose: would it be possible to carry out a partial upgrade on one of the spares? The project would mean less of an investment but with the operational benefits of the new Jetflex burner design – an intriguing prospect. FLSmidth Cement immediately set to work trying to establish if this could be achieved
Gregg St Clair, Vice President, Cement Operations at SRMG
A motivational partnership
With FLSmidth Cement having been entrusted with the contract for an additional production line at SRMG’s plant in 2001, the two companies had already established a very good relationship. As a single owner-operated cement plant, SRMG has the flexibility to be a bit more adventurous. This presents an opportunity to develop and nurture a close technical and personal relationship that betters both companies. All were keen to make this burner upgrade happen. After reviewing the design of the existing kiln burner, it was evident that a partial retrofit was not only possible but could actually work really well.
A minor upgrade with major implications
Most burner retrofits would necessitate the complete replacement of the burner pipe, but this project was simpler. The existing external kiln burner pipe, together with the inner sections of the burner for coal and natural gas firing, could all stay. No changes were necessary. The troublesome air annulus would be replaced with two separate air rings for radial and axial air, to match the new Jetflex burner design.
Figure 1 below shows the new air rings as well as how the burner tip would look after modification.
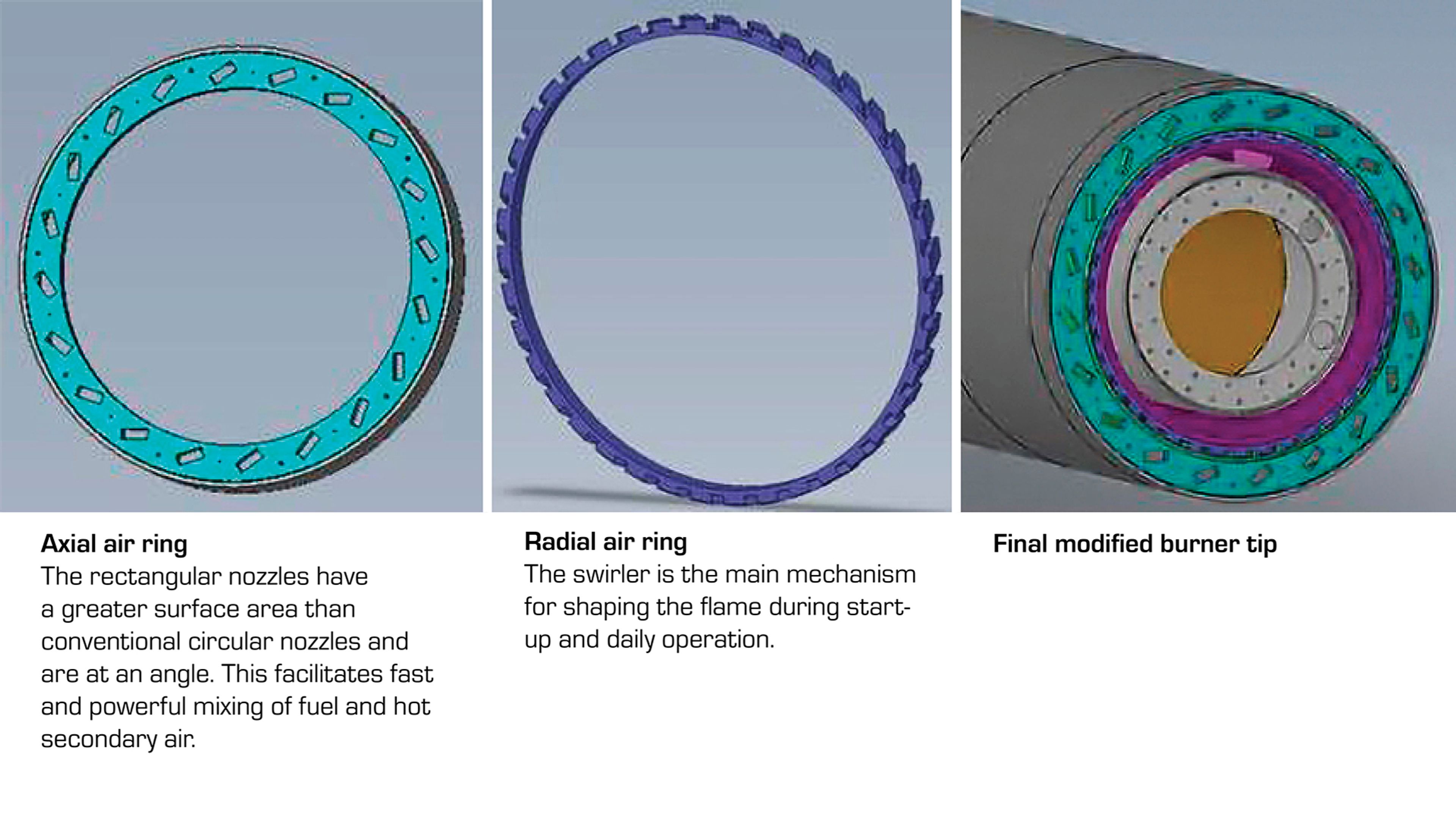
With the air annulus gone and the new air rings in place, the updated burner would have the identical primary air system to the latest Jetflex burner design, giving SRMG all the benefits of better flame shaping as well as significantly lower maintenance costs. No other replacement parts were needed – the existing burner trolley, primary air fan and fuel connections to the burner were all retained. Therefore, the upgrade could be achieved at approximately half the cost of a brand-new burner. SRMG was thrilled at the concept and quickly placed the order.
Figure 2 below: The new parts for the upgraded burner were supplied by FLSmidth Cement. The installation and physical upgrade of the burner were completed at a local shop near the plant, which had been handling the annual reconditioning of the existing Duoflex® burner.

Better flame, more consistent kiln operation
The upgraded burner was installed and commissioned in June 2018. As well as a stronger, better flame, SRMG also reports flame shaping is now much easier, and adjustments show in the flame right away. The flame has also been much more consistent, which maintains clinker quality.
Additional benefits include:
- A reduction in primary air pressure from 263mbar to 188mbar, despite there being no change in the primary air volume
- Approximately 10 per cent reduction in NOx emissions at the main stack and approximately 400ppm reduction in kiln backend NOx
- A small reduction in the CO emissions in the main stack.
“We have been very satisfied with the performance of the Jetflex burner upgrade,” said Gregg St Clair, vice president, Cement Operations at SRMG. “We see an improved flame and a more consistent kiln operation and clinker quality with this new burner. This partial upgrade is the kind of out-of-the-box solution that is only possible when two organisations work really well together and I’m thankful that we have FLSmidth Cement in our corner, willing to try something new.” SRMG is so pleased with the impact of this cost-effective upgrade that it has requested that FLSmidth Cement repeats the project with the cement producer’s other spare Duoflex burner.
Related Offerings