A cement plant's job is to produce cement as productively and profitably as possible. FLSmidth Cement’s model of operational excellence and principles of lifecycle support is how we help producers achieve these objectives:
- Diagnose: understand the gaps and identify improvement opportunities
- Improve: implement corrective actions identified during the initial assessment
- Stabilise: maintain plant performance
This approach relies on several pillars (Figure 1), including product-based upgrades, digital solutions, and services. A comprehensive overview is beyond the scope of this article. Instead, we will focus on how the convergence of digital solutions and services facilitates operational excellence. In short, the purpose of this paper is to discuss how digitally enabled services have matured to become a powerful tool to help diagnose and correct process inefficiencies—if not entirely avoid them.
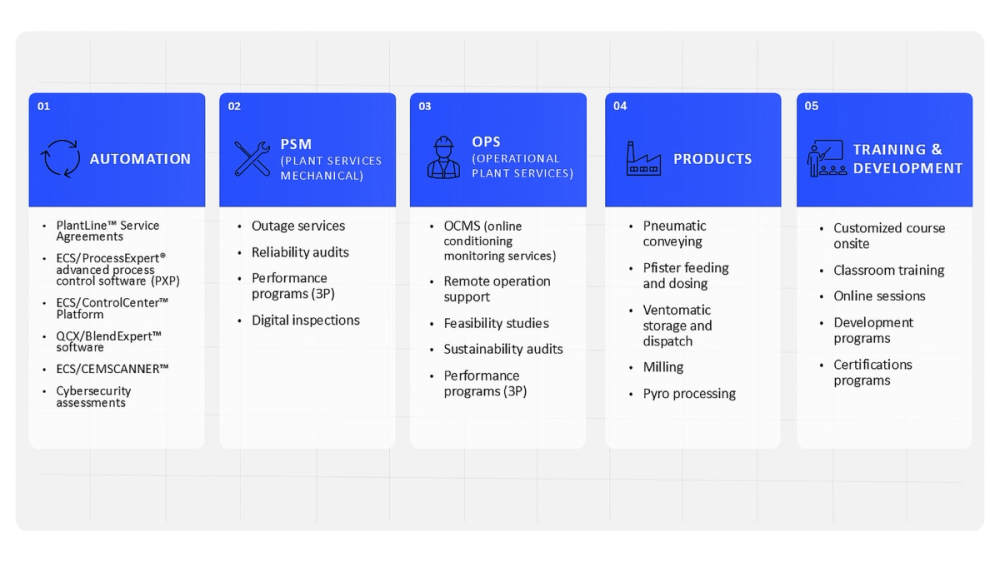
Figure 1. Digital solutions are entwined with all facets of operational excellence, enabling equipment to run better and reducing equipment downtime.
Services in the cement industry: 1887 – today
For most of the cement industry’s history, receiving expert advice and service support was complicated. When FLSmidth Cement built its first cement plant in 1887, the only options were telegraph and arduous travel to remote sites by service engineers. This eased through the 20th century as global telephone networks developed; however, these remained patchy, especially in the remote locations of many cement plants.
Automation and digital solutions have slowly eased service delivery. In 1969, FLSmidth’s Henrik Bang-Pederson and his colleagues launched the QCX® (quality control by computer and X-ray) system. This was followed in 1975 by the first forerunner of the company’s ECS™ plant control system – which now has more than 2000 installations globally. And the technology continues to advance. For example, the latest version of the ECS/ProcessExpert® (PXP) advanced process control solution now includes self-adaptive control – a feature likely beyond anything imagined by the first developers.
The focus of this paper is about services and using digital as an enabler.So, why the discussion about automation solutions? It may seem a bit off topic, but the fundamentals of digital capabilities underpin the advances of both. Morever, engineers with backgrounds in automation systems were the natural pioneers in pushing the limits of connectivity, remote monitoring, and support. This began in the late 1990s and slowly grew over the first decades of the 21st Century to cover not just automation systems, but also critical mechanical and process equipment. Fast forwarding to today, the widespread adoption of Industrial Internet of Things (IIoT) and Industry 4.0 technologies through the 2010s has provided the next step-change in the service landscape, accelerated by the outbreak of COVID-19.
We are now in an era with less need for service engineers to crisscross the globe in an endless quest to fix problems. Instead, they can access and monitor plant and equipment data remotely to deliver expert support to cement plants 24/7 for faster advice, troubleshooting, and corrective action. To make this support easily accessible for cement plants, FLSmidth Cement has designed specific offerings for online condition monitoring services (OCMS) for key equipment including ATOX® and OK® mills, kilns, Cross-Bar® coolers Ventomatic® equipment and Pfister® weighfeeders.
Online condition monitoring services
The concept is simple: to spot problems before they become problems. To do so, equipment performance data are collected from the plant and connected to FLSmidth Cement’s Global Remote Service Centre. Here, they are run through specially developed algorithms that flag any irregularities for review by the centre’s team of experts, who will contact the plant if there are any immediate concerns. The data are also readily available to the plant in real-time and curated into a regular report, which advises the plant on upcoming maintenance needs and opportunities for optimisation. The following examples illustrate how these digitally enabled services are powerful tools for diagnosing and correcting process inefficiencies.
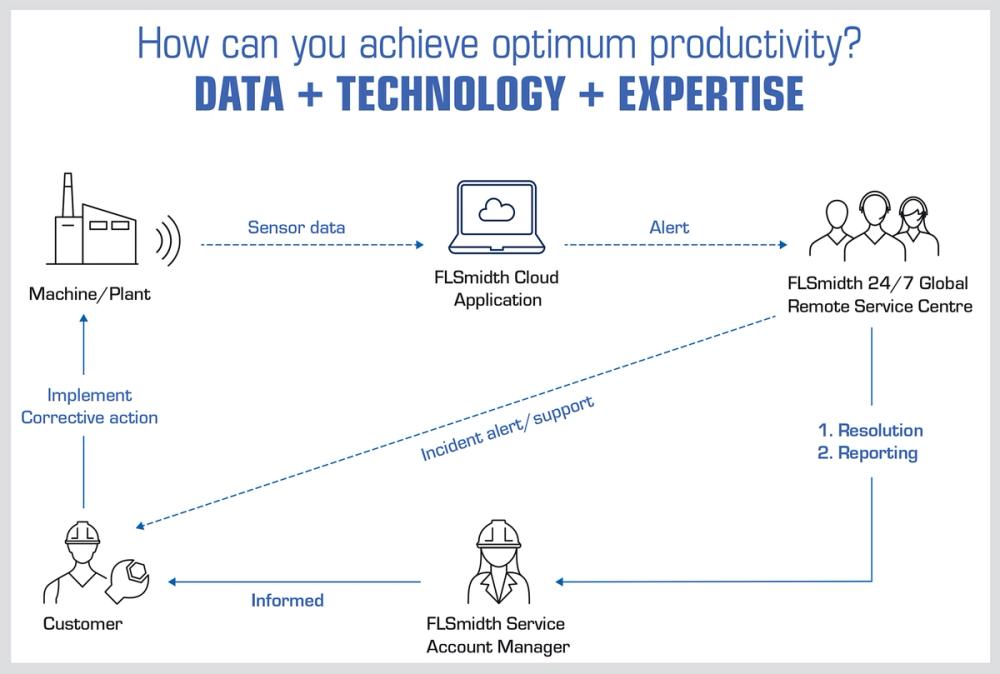
Figure 2. Process of OCMS delivering insights
Case study 1: kiln crank monitoring
Consider the kiln. An upset here will impact productivity, product quality, and environmental performance. Yet many kilns operate with just a few isolated sensors and inspections every 2-3 years. This does not provide enough information to optimise kiln performance or maintenance.
For example, problems with the kiln crank can cause bearings to run hot, increase lining loss, cracking of the kiln shell and supporting roller shafts, and wear of the supporting rollers and kiln tyres. Therefore, promptly reacting to any issue with the crank can reduce maintenance time and costs. Yet crank issues may not be picked up by plant operators – whose focus will rightly be production and other KPIs – until it is too late. However, by measuring the deflection from the crank on the roller, OCMS for kilns detect if the crank value deviates from the allowable limit, allowing quick correction.
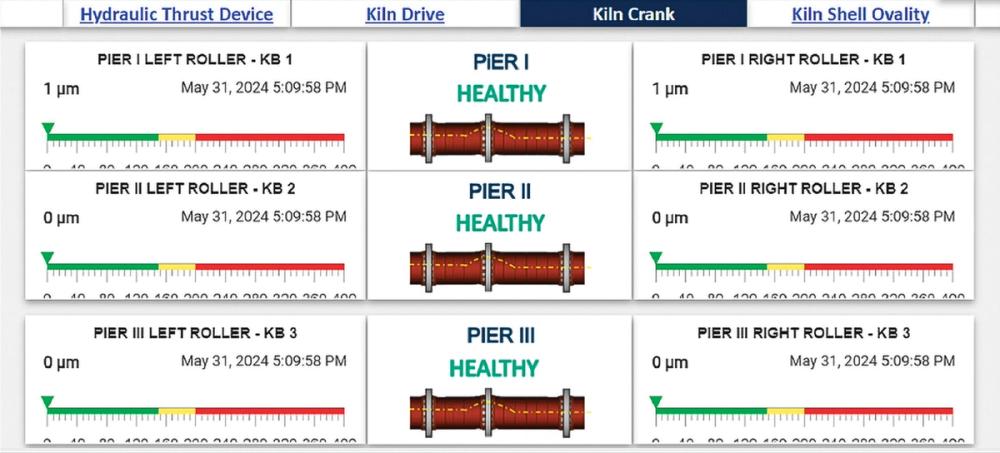
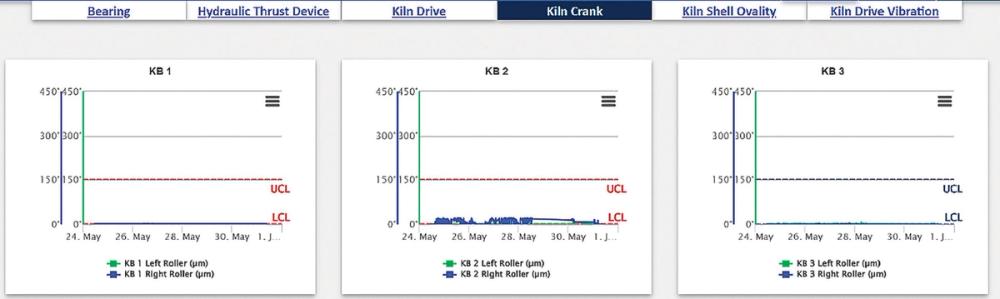
Figure 3. Dashboards from OCMS for kilns
Case study 2: kiln cycle time monitoring
Short kiln cycling times are another unwanted condition that is hard for plant operators to detect. Typically, a kiln cycles every 24 hours. More frequent cycling increases the thermal stress on kiln linings and components, leading to cracks and other negative implications, including reduced energy efficiency and even impacting cement quality, as inconsistent temperatures lead to incomplete reactions and variations in clinker chemical composition.
OCMS makes it much easier to identify when a kiln is experiencing short cycling times. FLSmidth Cement experts may be able to troubleshoot and identify the issue remotely or provide a list of possible options for further investigation by the plant. Either way, the problem is identified and corrected earlier than it would have otherwise been.
Case study 3: mill grinding pressure monitoring
A very simple issue, such as a small leak in a hydraulic cylinder, can have far-ranging consequences. Consider how unstable grinding pressure leads to uneven grinding and thus lower product quality, increased mill vibration, higher energy consumption, and challenges to maintaining stable operating conditions. This, in turn, can lead to more frequent adjustments, higher wear on equipment, and potential downtime.
Using OCMS for mills has been proven to help plants avoid this unwanted situation by detecting the early onset of grinding pressure instability before more severe symptoms are seen. How? A pressure transducer on the cylinder identified a slight decrease in hydraulic pressure, alerting FLSmidth Cement engineers of the leak before it was detected visually and allowing them to warn the plant a new seal was needed. Replacing the seal during a planned maintenance schedule solved the issue and maintained regular production.
Digital in support of digital
As digitalization advances, we have all come to depend on plant automation systems more than ever. Here, we package our support as a PlantLine™ service agreement. It offers a customisable mix of remote services that ensure a plant’s automation equipment and software remain protected and perform well. At the heart of all PlantLine agreements is the mandatory Essential module, which provides rapid access to a global team of automation experts for user support, advanced troubleshooting, hotfixes, re-establishment, and managed antivirus. Four optional service packages can be built onto Essential: Proactive, Lifecycle, Cyber Security, and Remote Technologies. Interest from plants has been on the rise in the last year, and to date, we have nearly 300 active contracts worldwide.

Figure 4. The components of a PlantLine service agreement.
Staying secure in a dangerous digital world
Of course, remote services depend on reliable and secure connectivity. It is something that FLSmidth Cement has been developing since 2007 when it introduced Bomgar, its first remote customer portal. Today, the company’s remote services rely on secure remote access to a plant’s control network via the Go2FLS LiveConnect™ system, which provides real-time access to plant and equipment data, such as process mimics, trends, diagnostic faceplates, and all alarms/events.
Finally, no discussion of digital would be complete without a short word about cybersecurity. FLSmidth Cement’s offering here is another story of organic development. As the company’s remote services advanced, so (by necessity) did its cybersecurity expertise and experience until some customers began approaching us to support their own cybersecurity needs. This inspired FLSmidth Cement to launch its cybersecurity services package. We now offer a comprehensive range of services in this area that assist cement plants in maintaining digital system performance, protecting critical assets from cyber threats, and ensuring quick reestablishment should the worst happen.
Toward the full potential of digitalisation
With each passing year, the world becomes exponentially more complex. Cement plants (and most other businesses) are expected to do more with less, have increasingly complicated equipment and systems, and are often challenged to retain talent and keep sufficient knowledge in-house. This may sound bleak, but ironically, the same forces driving these changes have also made accessing expert services and support much simpler.
Not only has digitalisation transformed the mechanism for delivering services, but it has also greatly extended the scope of what can be addressed. With the vast array of sensors now prevalent at plants, there is more opportunity to identify potential issues and improvement opportunities. Furthermore, the advances in sharing data and connectivity can give cement plants access to an army of experts worldwide who can be brought in to help resolve issues as needed. With digital, no plant needs to be alone.
This article was originally published in the November 2024 issue of World Cement Magazine.