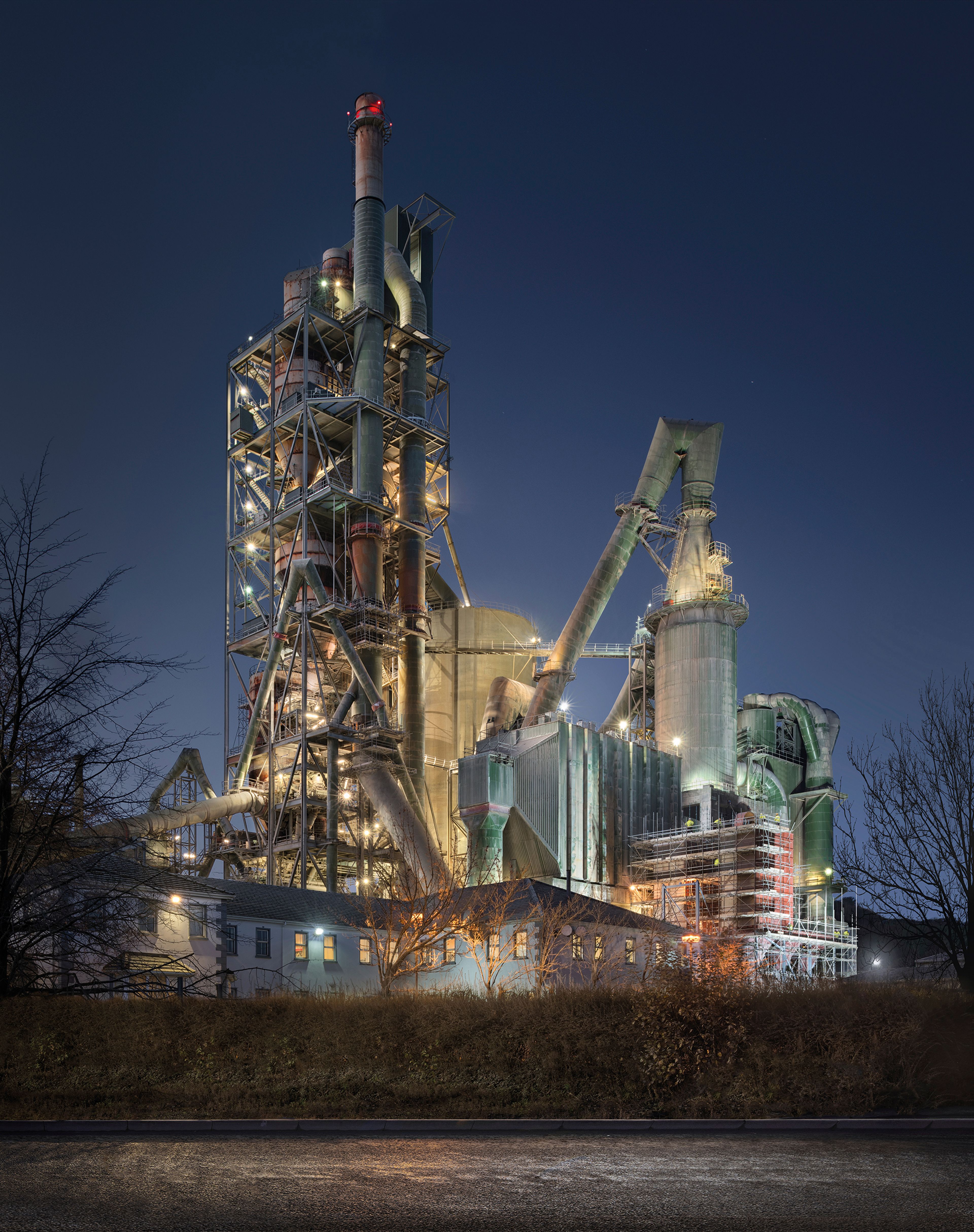
3rd May 2024
Decarbonizing Cement: The FUELFLEX® Pyrolyzer Innovation Journey
The cement industry faces mounting pressure to reduce CO₂ emissions while maintaining production efficiency. With 30-40% of emissions coming from fuel combustion and another 60-70% from the process itself, traditional technologies alone cannot meet decarbonization targets.
Practical innovation delivers measurable results in cement's green transition
FLSmidth Cement's FUELFLEX® Pyrolyzer transforms cement production by enabling up to 99% alternative fuel substitution while simultaneously reducing NOx emissions without needing expensive calciner extensions or ammonia injection—delivering both environmental and economic benefits.
Explore how this technology was developed, implemented, and optimized through collaborative industry partnership.
Featuring:
Lars Skaarup Jensen PhD Chem. Eng., R&D Specialist and Project Manager at FLSmidth Cement, in partnership with Mannok Cement.
Explore with Lars Skaarup Jensen:
- Three-pronged decarbonization framework – clinker substitution, clinker decarbonization, and efficiency improvements provide comprehensive pathways to reduce emissions
- Innovative pyrolysis implementation – converting solid alternative fuels into highly reactive gas and char for improved combustion and NOx reduction
- Documented performance gains – elimination of ammonia water usage while reducing emissions below regulatory limits
- Optimization beyond implementation – continuous refinement enabled 99% coal substitution through integrated process control and feeder upgrades
Discover how real-world implementation of the FUELFLEX® Pyrolyzer at Mannok Cement demonstrates a practical path toward decarbonization for cement producers worldwide.
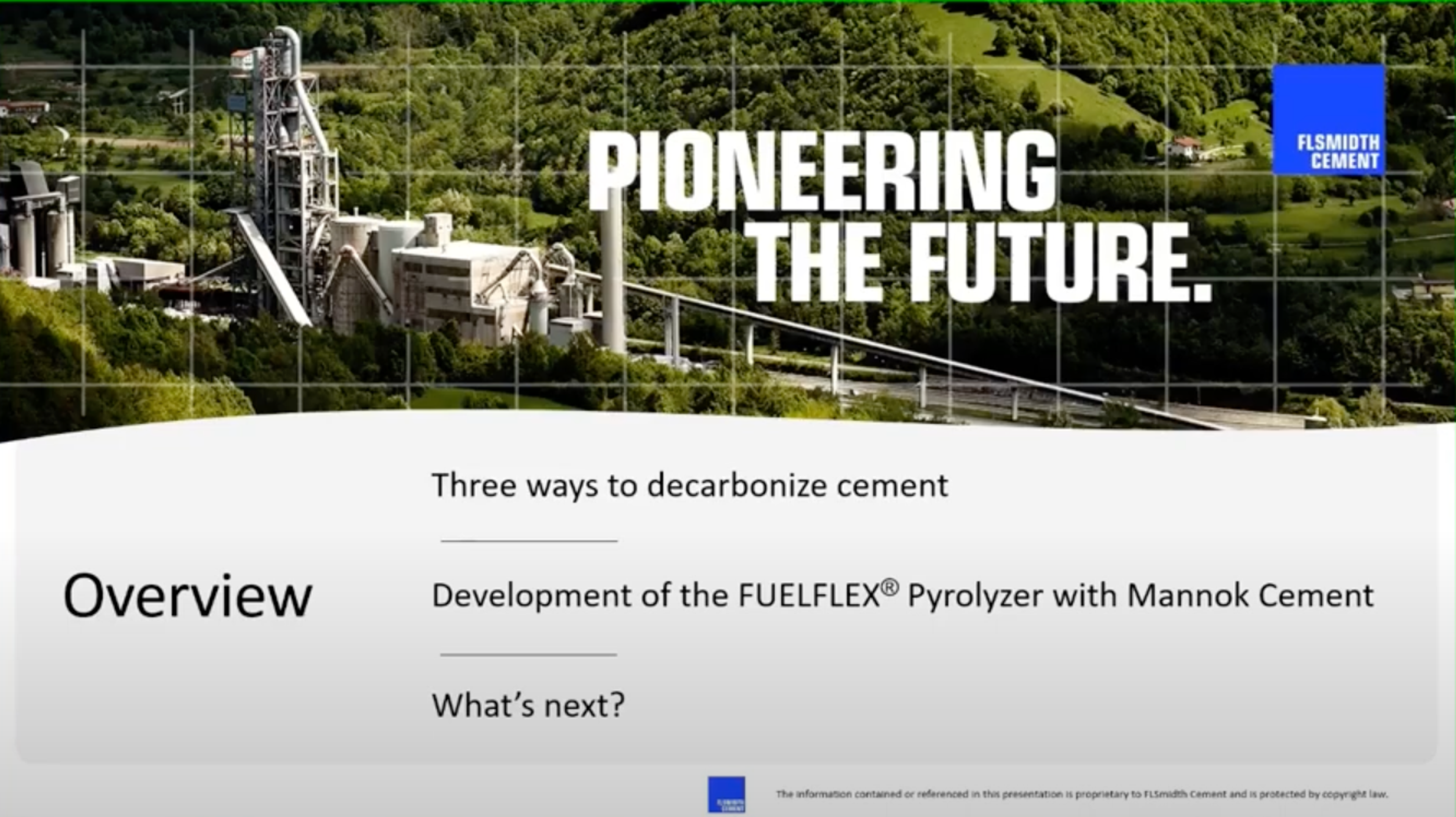
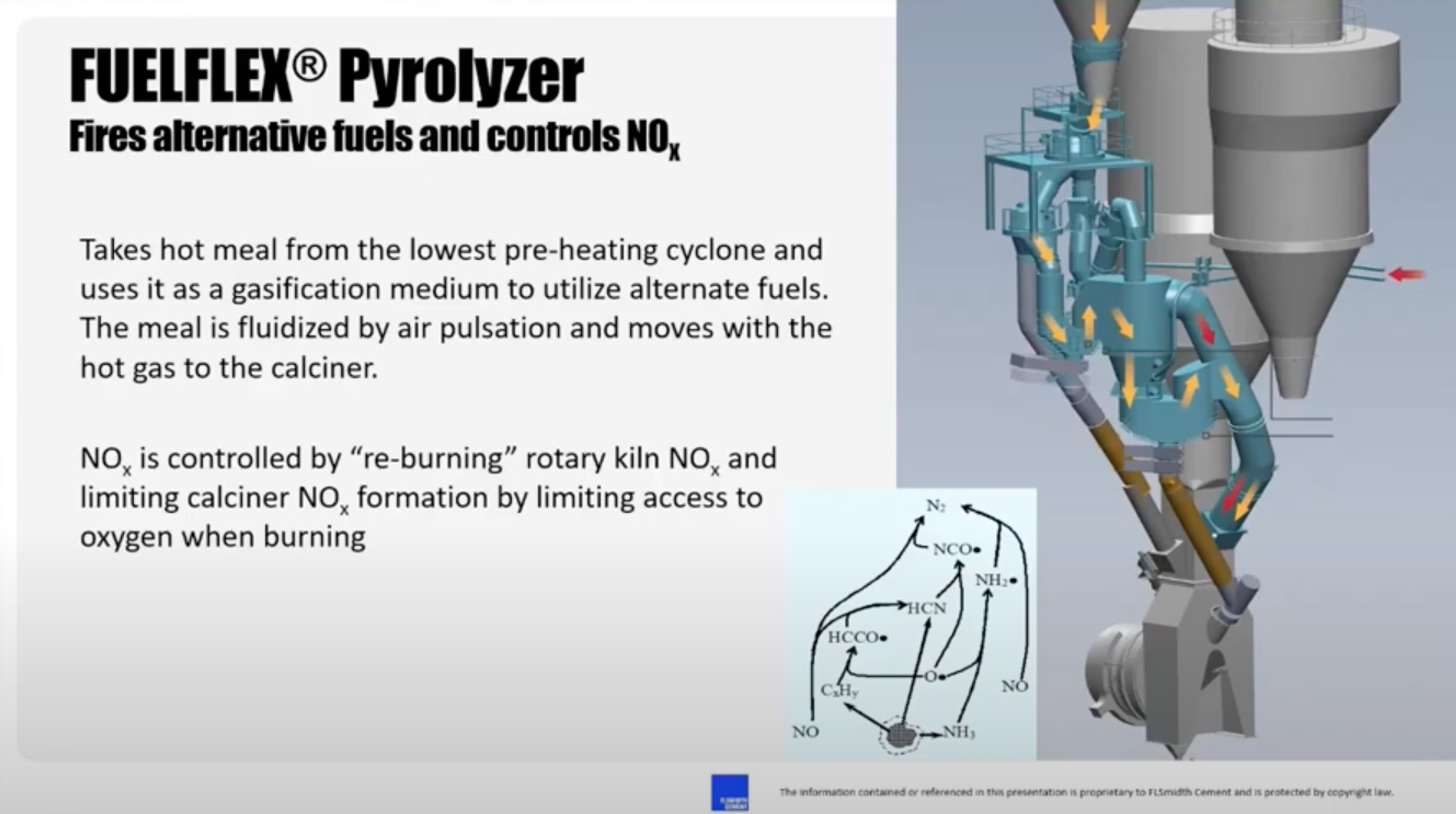
Lars Skaarup Jensen, R&D Specialist & Project Manager - PhD Chem. Eng., FLSmidth Cement
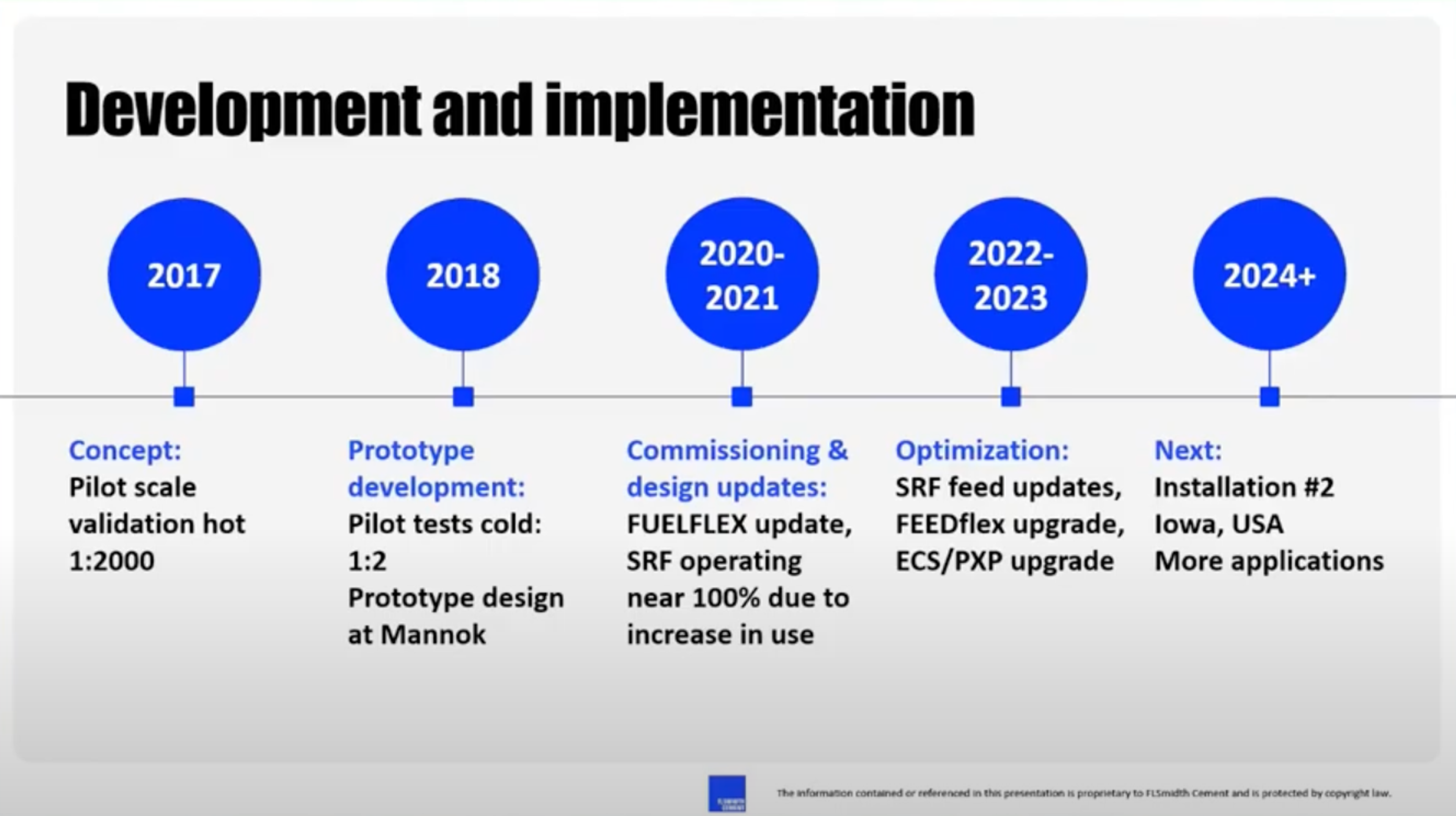
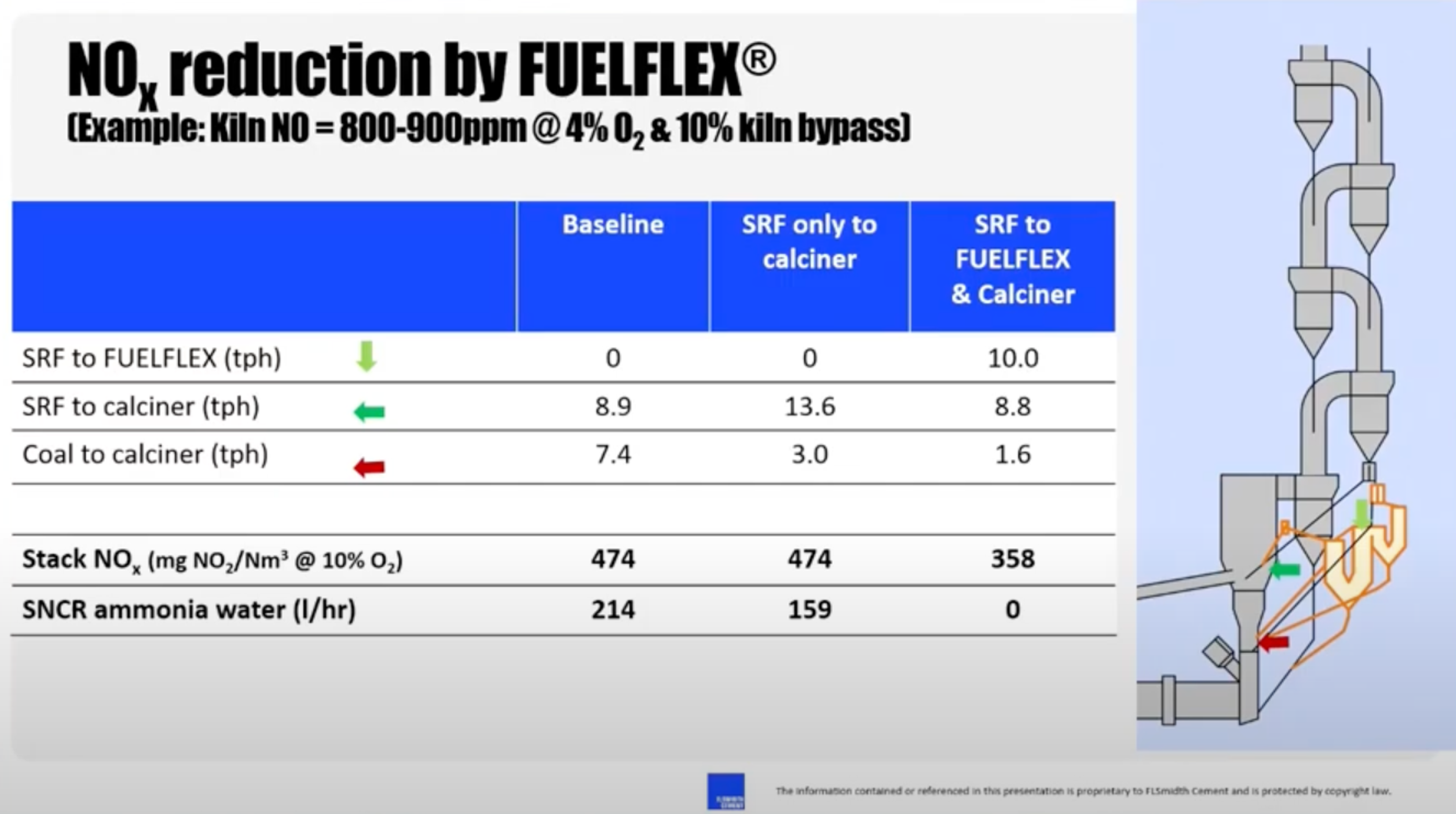
FUELFLEX® Pyrolyzer: Alternative Fuel Technology for Cement
Decarbonization Pathways Quantified
- Clinker substitution can reduce emissions by 30-40%
- Fuel substitution contributes 10-15% emissions reduction
- New technologies like CCUS offer 30-40% additional reduction potential
The cement industry's pathway to net-zero requires a combination of approaches, with clinker substitution and new technologies offering the greatest impact potential.
FUELFLEX® Pyrolyzer Mechanism
- Uses hot meal (800°C) from the lowest preheater cyclone as gasification medium
- Converts alternative fuels into reactive gas and char for improved combustion
- Features continuous debris removal through twin drain gates
The pyrolyzer's innovative design allows for extended fuel residence time without requiring costly calciner extensions, making it a practical retrofit solution.
Demonstrated NOx Reduction Performance
- Eliminated need for ammonia water injection (previously 214 l/hr)
- Reduced stack NOx from 474 to 358 mg NO₂/Nm³
- Enabled 90% alternative fuel substitution rate
At Mannok Cement, the FUELFLEX® Pyrolyzer demonstrated both environmental and economic benefits through significant NOx reduction and fuel cost savings.
Integrated Process Optimization
- FEEDflex® Upgrade enabled 1:100 coal feeder turndown ratio
- ECS/ProcessExpert® solution minimized coal usage to 0.2 tons/hour
- Three Pfister feeders coordinated through advanced control system
By optimizing the complete system rather than just the pyrolyzer alone, Mannok achieved stable operation with minimal fossil fuel use.
Industry Implementation Timeline
- 2017-2018: Concept development and pilot testing
- 2020-2021: First installation and design refinements at Mannok
- 2024: Second installation at Continental Cement, Iowa
- Future: Expanded applications worldwide
With initial implementation challenges overcome, the technology is now being deployed more widely with predictable installation timelines.
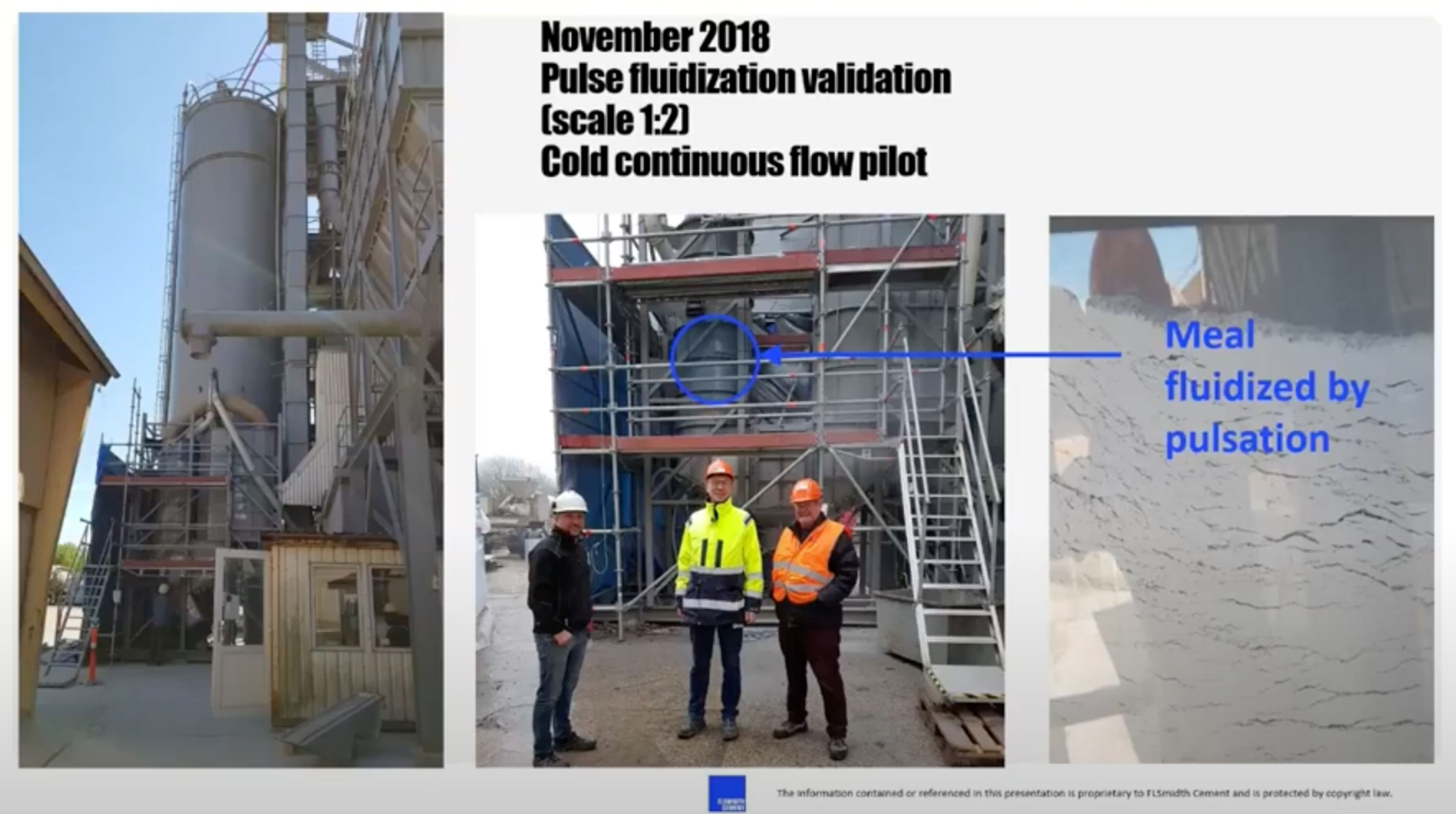
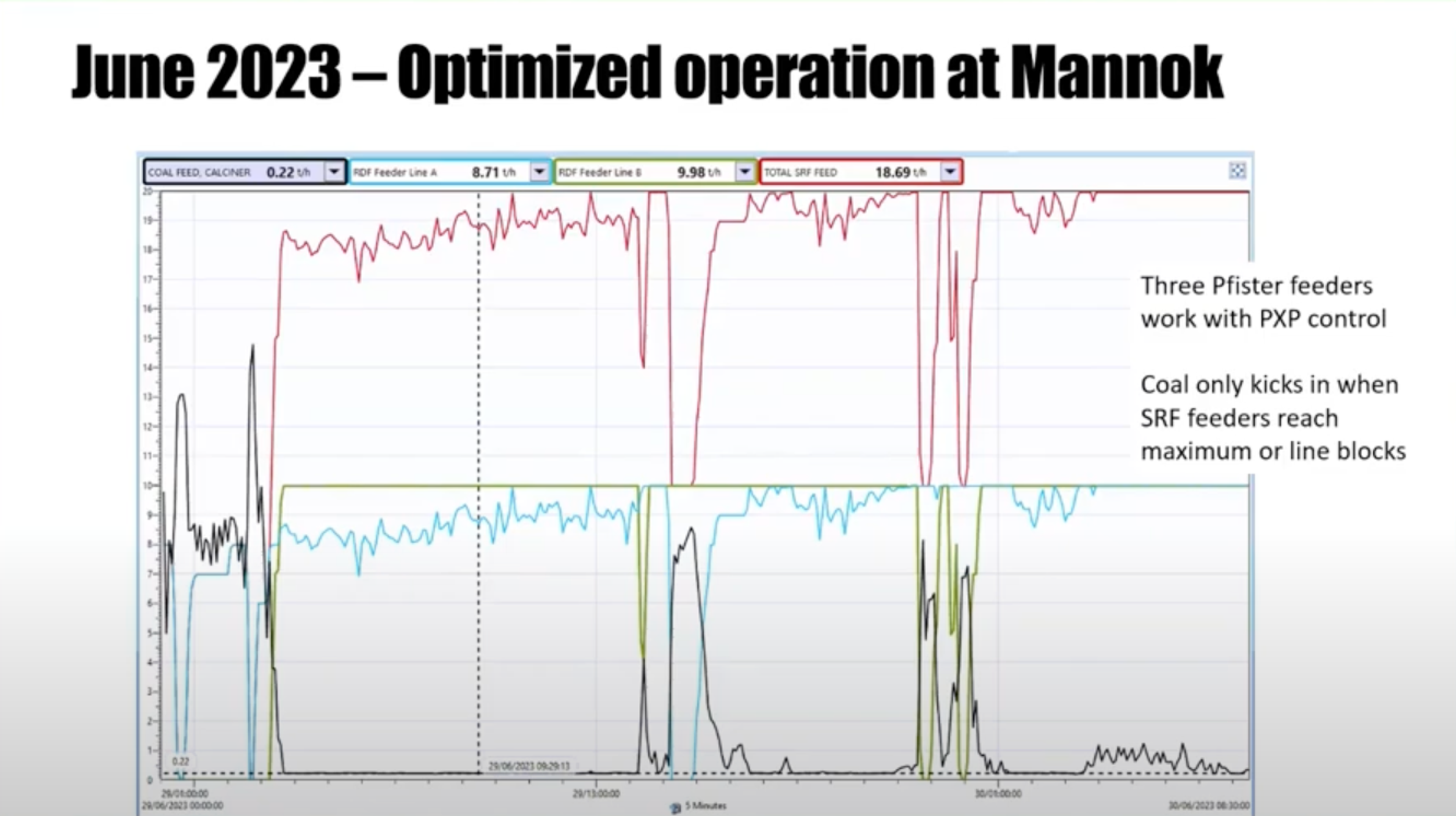
Technology Implementation Journey
Addressing cement's decarbonization challenge requires practical innovations that deliver measurable results. The FUELFLEX® Pyrolyzer development demonstrates how industry collaboration creates implementable solutions for real-world production facilities. From initial concept testing at 1:2000 scale to full industrial implementation, the technology evolved through systematic problem-solving and refinement.
Key innovations include the pulse fluidization technology that enables hot meal to flow like water, the two-stage gate system preventing backward gas flow, and the continuous debris removal system critical for long-term reliability. The integration with advanced process control systems ultimately enabled Mannok Cement to achieve up to 99% alternative fuel substitution while eliminating NOx reduction chemicals, demonstrating both environmental and economic benefits that make decarbonization commercially viable.
Implement Proven Alternative Fuel Technology in Your Cement Plant
Discover how FLSmidth's FUELFLEX® Pyrolyzer can integrate with your existing preheater tower to increase alternative fuel usage while reducing NOx emissions and operational costs. See actual implementation data from Mannok Cement and learn about the development process that ensures reliable operation in demanding production environments.
Related Offerings
Products (4)
Expert Insights Q&A
Frequently Asked Questions: Green Innovation and FUELFLEX® Pyrolyzer